The Future of Digital Twin Technology in Smart Manufacturing
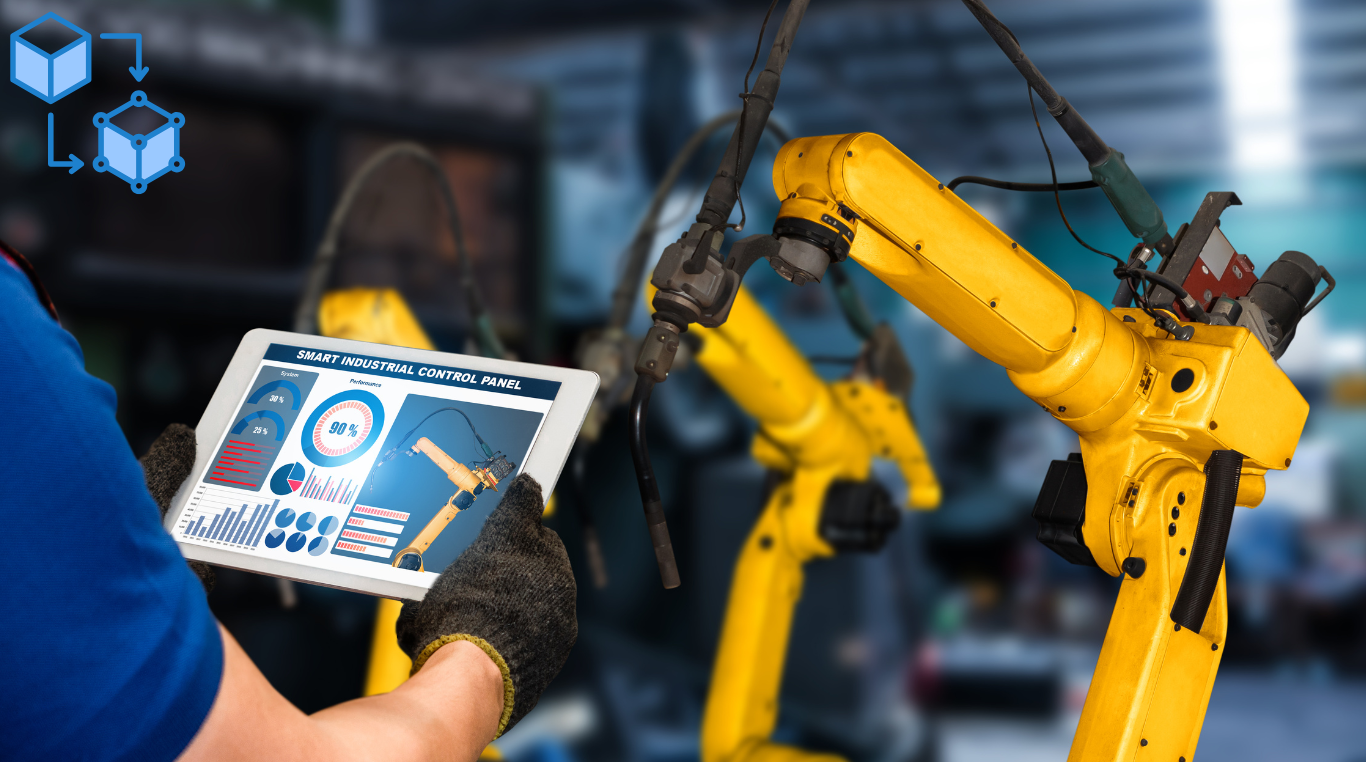
The manufacturing sector is constantly evolving to meet the demands of an increasingly complex market. Creating virtual replicas of physical assets allows businesses to simulate and optimize real-world processes. Automated solutions improve production efficiency, reduce human error, and increase throughput. However, predictive maintenance helps companies prevent unplanned downtime by identifying issues before they affect production.
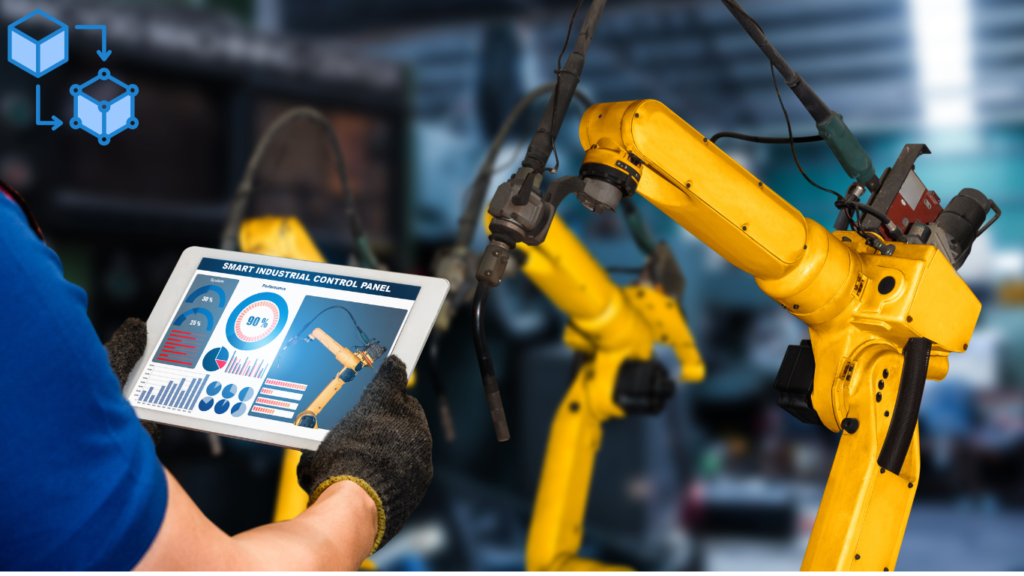
Digital Twin Technology offers real-time, data-driven insights into physical assets and their performance. Smart manufacturing leverages technology to enhance production processes and improve operational efficiency. Here, we outline the role of digital replicas in transforming smart manufacturing for the future. Keep reading to learn how digital twins can optimize efficiency, reduce costs, and boost innovation.
1. Revolutionizing Operational Efficiency
Creating virtual models rapidly changes how suppliers approach operational efficiency through predictive maintenance and process optimization. Real-time data gathered from machines can be used to identify potential failures before they occur. Manufacturers can avoid costly downtime and improve operational efficiency by predicting maintenance needs. Innovative AI-driven manufacturing solutions from top industry experts will continue refining and optimizing suppliers’ production schedules.
Here are the essential factors associated with operational efficiency:
- Real-time data collection enhances decision-making by identifying inefficiencies.
- Predictive maintenance prevents costly downtime, reducing unplanned disruptions.
- Automation streamlines operations, reducing human error.
- Continuous process optimization through data analytics improves throughput while minimizing waste.
2. Enhancing Product Design and Development
Manufacturers can create virtual prototypes and simulate different design possibilities with high-end virtual twin systems. Using real-time data, designers can refine and test products virtually before committing to physical production. This speeds up the product development cycle and ensures higher-quality products by identifying potential flaws early. Advanced competent manufacturing service providers will be essential in helping suppliers realize faster design iterations.
3. Improving Supply Chain Management
Digital twins are invaluable for managing and optimizing supply chains by creating real-time models. These models allow manufacturers to track goods throughout the supply chain and predict disruptions. These high-end solutions ensure the efficient flow of materials and timely deliveries by optimizing logistic management. Leaders in industrial AI solutions are critical in integrating digital twins with existing supply chain systems.
4. Enabling Predictive Analytics for Maintenance
Digital replicas of assets enable predictive analytics by gathering and analyzing data from embedded machine sensors. This allows suppliers to forecast when equipment will require maintenance or repairs, reducing unexpected downtime. They can extend asset life cycles and reduce operational costs by implementing predictive maintenance strategies. Digital transformation specialists for manufacturing will continue to refine these predictive models, ensuring accurate forecasting.
5. Accelerating Sustainability and Energy Efficiency
Digital twins help manufacturers monitor and optimize energy consumption, enabling more sustainable manufacturing practices. Suppliers can test their effectiveness by simulating different energy-saving strategies before implementing them in production. This reduces waste, lowers carbon footprints, and improves resource use across operations. Smart factory optimization consultants help implement sustainable energy solutions by using this technology for optimization.
Read: Improving Emergency Fire Response by using Technology(Opens in a new browser tab)
6. Advancing Workforce Training and Safety
In the future, virtual asset models will change workforce training by providing realistic virtual environments. Employees will interact with digital replicas of machinery and systems without the risk of injury. This simulation enables hands-on training in a safe, controlled environment, ensuring workers are prepared for their tasks. Industrial AI and digital transformation experts will help create immersive training programs using digital twins.
Embracing Digital Twin Technology can propel your business toward a future of unmatched operational excellence. Collaborating with smart factory optimization consultants ensures seamless integration of innovative solutions. Experts provide invaluable guidance, optimizing your systems for greater productivity, efficiency, and sustainability. Do not miss the opportunity to revolutionize your operations by partnering with the right experts today.
Read: The Role of Business Directories in India’s Digital Economy
Read more safety topics at safety bag