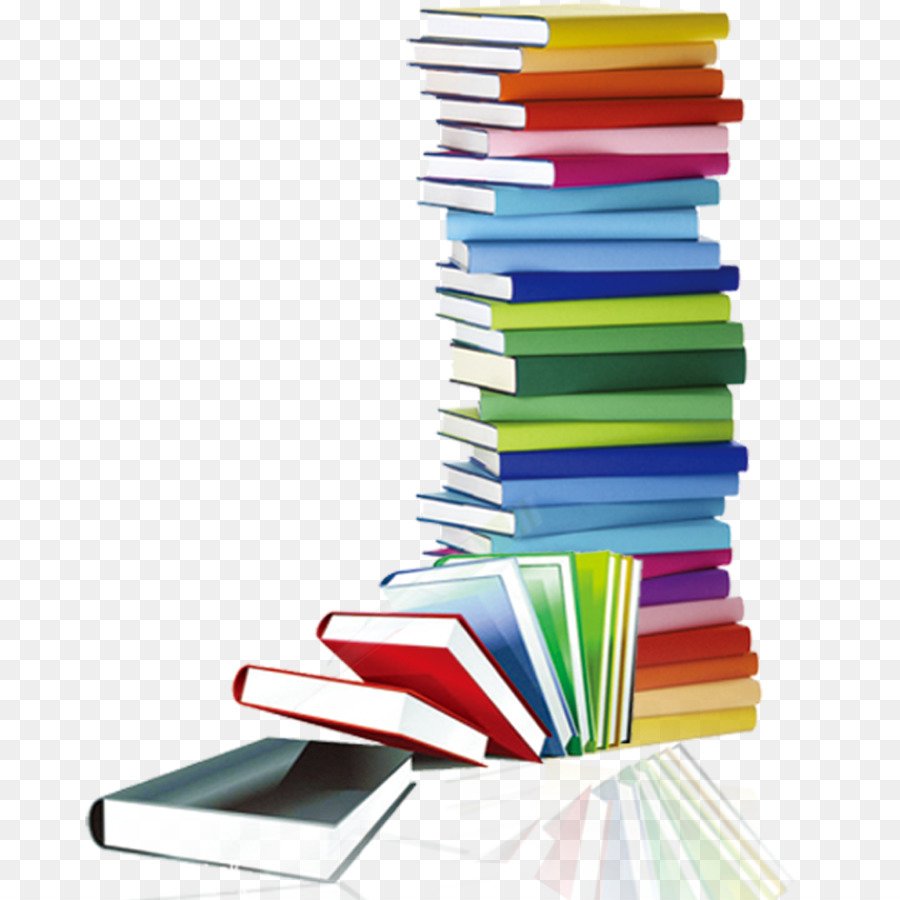
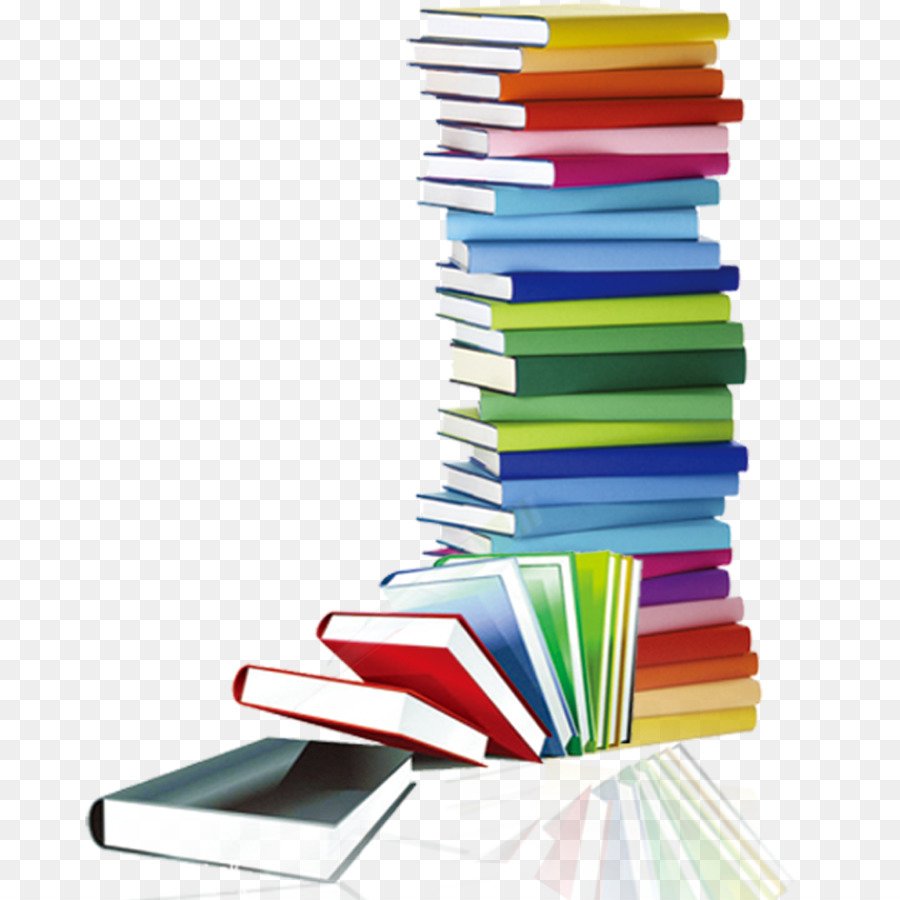
I am text block. Click edit button to change this text. Lorem ipsum dolor sit amet, consectetur adipiscing elit. Ut elit tellus, luctus nec ullamcorper mattis, pulvinar dapibus leo.
HSSE Store
PDF’s Posts & E-Books
COVID-19 Healthcare Planning Checklist
Checklist for COVID-19
1- Planning Checklist
2- Office Self assessment Checklist
SAFETY INTERVIEW QUESTIONS AND EXAMS
some examples of real safety exams and interview questions
Aim of the book
The last five years of the twentieth century witnessed significant changes in the way firms operate and in the fundamental structure of business units as globalization became more prominent. British industry has changed from primarily manufacturing based to predominantly service provision and, after the mergers and takeovers of the 1970s, came the trend for down-sizing to much smaller business units in the 1980s and 1990s. Total number of businesses has grown to around four million, the vast majority being sole traders or partners without employees, accompanied by the rapid growth in the use of telecommunications, the internet, part-time and temporary employment contracts and the use of home-working.Membership of the European Union has brought with it a stream of legislation and, more recently, a desire to bring all member states into closer alignment on employment and worker protection, social issues, taxation and other fiscal measures. This has been closely followed by many directives which seem to be blurring the edges between different disciplines
Work-related stress is one of the most important issues in many countries and in different kinds of workplaces. Stress has many negative impacts, including circulatory and gastrointestinal diseases, other physical problems, psychosomatic and psychosocial problems, and low productivity. Increasing emphasis is being placed on improving working conditions and work organization with respect to stress at work, and on practical measures to cope with stressful work situations. Recent surveys by the ILO indicate that there are commonly applicable checkpoints for studying and reducing stress at work. It is useful to review recent international experience in this regard and develop easy-to-apply checkpoints applicable in varying situations. It is especially important to optimize workplace conditions and work organization to prevent stress-related problems in the workplace. There are a number of practical countermeasures to such problems, which include optimizing the outer loads (stressors) at work, at home and in the community; increasing the coping ability of workers; and reinforcing support systems for workers.
Environmental Chemistry is a relatively young science. Interest in this subject, however, is growing very rapidly and, although no agreement has been reached as yet about the exact content and limits of this interdisciplinary discipline, there appears to be increasing interest in seeing environmental topics which are based on chemistry embodied in this subject. One of the first objectives of Environmental Chemistry must be the study of the environment and of natural chemical processes which occur in the environment.A major purpose of this series on Environmental Chemistry, therefore, is to present a reasonably uniform view of various aspects of the chemistry of the environment and chemical reactions occurring in the environment.The industrial activities of man have given a new dimension to Environmental Chemistry.We have now synthesized and described over five million chemical compounds and chemical industry produces about hundred and fifty million tons of synthetic chemicals annually.
Safety science is a twenty-first-century term for everything that goes into the prevention of accidents, illnesses, fires, explosions, and other events that harm people, property, or the environment (ASSE and BCSP 2000,3). Of these events, fire losses can be one of the greatest threats to an industrial organization in terms of financial losses, loss of life, loss of property, and property damage. Therefore, industrial fire protection and prevention are crucial components of any safety professional’s job, be it serving as a loss-control consultant or a safety manager.
These guidelines cover compressed and liquefiable gas cylinders as shown on the ‘Gas cylinder colour identification‘on pages 8-9. Please note that the identification of the gas contents of any cylinder is given by the label on the cylinder and is qualified by the colour(s) of the cylinder, and the cylinder valve outlet.These guidelines touch on toxic gases (e.g. Ammonia which is used as a refrigerant) but do not cover these gases in detail as these are considered generally the domain of special gases.
Job Hazard Analysis a Guide for Voluntary Compliance and Beyond From Hazard to Risk:
Transforming the JHA
from a Tool to a Process
This Small Entity Compliance Guide (SECG) is intended to help small businesses comply with the Occupational Safety and Health Administration’s (OSHA) Respiratory Protection standard (63 FR 1152; January 8, 1998). While the guide is for small entities, the guide itself is not small. OSHA’s goal for this document is to provide small entities with a comprehensive step-by-step guide complete with checklists and commonly asked questions that will aid both employees and employers in small businesses with a better understanding of OSHA’s respiratory protection standard. The reader should be advised that OSHA also has other shorter documents and visual aids that may be used to better understand respiratory protection and the OSHA standard itself.
The intent of this WELDING GUIDELINE is to serve as a resource for employers and workers to safely perform welding activities. The guideline will provide information on:
• the types of welding processes
• the hazards (noise, smoke characteristics, metal contents, ultraviolet light, ozone, carbon monoxide & other gases)
• health effects of exposure
• current allowable guidelines
• ventilation guidelines
• PPE requirements
• special welding situations
• checklist
• references
Written by Laurence Britton, who has over 20 years’ experience in the fields of static ignition and process fire and explosion hazards research, this resource addresses an area not extensively covered in process safety standards or literature: understanding and reducing potential hazards associated with static electricity. The book covers the nature of static electricity, characteristics and effective energies of different static resources, techniques for evaluating static electricity hazards, general bonding, grounding, and other techniques used to control static or prevent ignition, gases and liquids, powders and hybrid mixtures.
A workplace safety and health program is a legislative requirement in workplaces with 20 or more workers. Well-designed programs reduce injuries and occupational illnesses. This guide will help you to develop an effective safety and health program. Each chapter matches one of the eleven elements required in The Workplace Safety and Health Act
Rethinking the Way We Think About Safety by Select International. This short, 8-page publication “is designed to provoke readers to question assumptions regarding safety management”.
The work place guide to Arc Flash safety Get answers to your arc flash and NFPA 70E questions
Forklift Safety Guide:Learning the safe way to operate a forklift and other powered industrial trucks may save your life
Engineering Safety Assessment
by Jim Thomson PhD is a 219-page book on how to assess the safety of highly hazardous operations and facilities.
A Health Hazard Evaluation (HHE) is an evaluation of possible health hazards at a workplace. Employees, employee representatives, or employers can request an HHE if they have concerns about health hazards at work. During an evaluation, NIOSH investigators evaluate whether a health hazard to employees caused by exposure to hazardous materials or conditions exists. Workplace agents NIOSH has studied include chemicals such as lead, bromopropane, and chloramines; biological agents such as anthrax and mold; and physical agents such as heat stress, noise, radiation, and ergonomic stressors.
Managing contractors
A guide for employers has been written as a guide for small to medium-sized companies in the chemical industry, but it will also be of use to other industries and larger companies.Safe working with contractors presents a challenge, but being a smaller company has its advantages. You can be more flexible in your approach and decisions can be made more quickly. Lines of communication are shorter, usually there are not too many people involved and it is easier to know who is around.
A workbook for employers, unions, safety representatives and safety professionals.Every year people are killed or injured at work. Over 40 million working days are lost annually through work-related accidents and illnesses. This workbook gives organisations an opportunity to find out what went wrong. Learning the lessons and taking action may reduce, or even prevent, accidents in the future. As a step-by-step guide, it will help all organisations, particularly smaller businesses, to carry out their own health and safety investigations. Investigating accidents and incidents explains why you need to carry out investigations and takes you through each step of the process:
This user guide provides an overview of what leading indicators are, and how and why they might be applied to strengthen your organization’s health and safety culture and performance. Some leading indicators may be more effective than others, depending on an organisation’s current level of OHS performance. For that reason, the user guide considers three categories of OHS performance: those that are focused on maintaining
Workplace exposure limits Containing the list of workplace exposure limits for use with the Control of Substances Hazardous to Health Regulations.It is 74-pages and was published in 2005. Common workplace health hazards such as chemicals, dusts, and fumes are reviewed. The latest updated European exposure limits are discussed (some of which are more stringent than U.S. limits). Monitoring methods are covered as well as proven solutions/controls. This book should be of special value to to those companies with international operations.
Easy Ergonomics, A Practical Approach for Improving the Workplace was developed by the Education and Training Unit, Cal/OSHA Consultation Service, California Department of Industrial Relations. The document was prepared for publication by the staff of the Publications Division/CDE Press, California Department of Education. It was distributed under the provisions of the Library Distribution Act and Government Code Section 11096. Published 1999 by the California Department of Industrial Relations
Managing shiftwork– Health and Safety Guidance is 45-pages in length and was published in 2006. Understand shift work and its’ effect and impact on worker safety and health. It offers numerous strategies for improving the safety records on all shifts at any organization.
Successful health and safety management is a Book was prepared by HSE as a practical guide for directors, managers, health and safety professionals and employee representatives who want to improve health and safety in their organisation.
DOWNLOAD
Successful health and safety management was prepared by HSE as a practical guide for directors, managers, health and safety professionals and employee representatives who want to improve health and safety in their organisation. Its simple message is that organisations need to manage health and safety with the same degree of expertise and to the same standards as other core business activities, if they are to effectively control risks and prevent harm to people. This book describes the principles and management practices which provide the basis of effective health and safety management. It sets out the issues which need to be addressed, and can be used for developing improvement programmes,
This guide is mainly aimed at medium to large employers. It will help them in their legal duty to consult and involve their employees on health and safety matters. Small businesses may find the guidance helpful, particularly the case studies. Employees, their health and safety representatives and trade unions may also find the guide useful. The guide concentrates on examples of how to comply with the Safety Representatives and Safety Committees Regulations 1977 (as amended), and the Health and Safety (Consultation with Employees) Regulations 1996 (as amended). A complementary guide, containing both sets of regulations, and a leaflet are also available. The guide is designed to clearly distinguish different types of information so you can find the parts that are relevant for you. References to the regulations are colour coded
Saudi Aramco HAZOP Guidelines and it’s techniques
Preliminary Hazard Analysis (PHA) 5 th Edition September 1993
HSE Procedures
Preliminary Hazard Analysis (PHA) 5 th Edition September 1993
HSE Manuals
Safety , health and welfare on construction sites a training manual
HSE Forms
Prior to initial use, all new and altered cranes should be inspected to determine if any safety hazards exist. Thereafter, inspections should be performed at intervals according to the following list. Some components require daily inspection, while others need only be checked on a monthly basis. A complete inspection should also include observation during operation to detect any defects that might appear between regular inspections.
This checklist is intended to be used as a self-inspection checklist for portable ladders. It is based on NIOSH’s “Portable Ladders for Construction Self-Inspection Checklist,” According to NIOSH, the checklist “covers regulations issued by the U.S. Department of Labor, Occupational Safety and Health Administration (OSHA) under the construction standards 29 CFR 1926.1050 to 1926.1060. It applies to portable ladders used at temporary worksites associated with construction, alteration, demolition, or repair work including painting and decorating.
Process safety management (PSM) is a systematic analytical tool for preventing the release of highly hazardous chemicals (as defined by OSHA). Hazardous chemicals include toxic, reactive, explosive and highly flammable liquids and gases. It is a comprehensive management that aims to decrease the number and severity of incidents relating to highly hazardous chemical releases.
The Epstein Becker & Green law office has prepared an 8-page OSHA Inspection Checklist. It’s a resource you can use to help prepare for an OSHA inspection. It has six sections that cover:
- Preparation before an OSHA inspection
- Preliminary inspection issues and opening
- Document production
- Walkaround inspection
- Employee interviews
- Closing citations & post citation considerations
Job Hazard Analysis form used to identify the work hazards and it’s related control measures
Incident Report Form used to report any type of incident as Near-Miss , injuries , property damage , fire and more
Safety Inspection Form used for site Facility , equipment and Activity inspection
Contractor Weekly HSE Report Form used for record the weekly statistics of contractors
Competent Person Designation form used to approve and qualify the competent person
Lift Plan Form used for making critical and simple lift plan
After Completion of the Emergency Test drill as per adopted plan a review for the drill shall be done to evaluate the Drill and ensure that the planned objectives of the drill have been done efficiently by using Emergency Drill After Action Review form you will be able to record drill timing and find out the positive and area of improvement with final recommendations to be followed for the next Drill.
Before starting Emergency Exercise drill a preparation meeting shall be held by all participant of the drill including Emergency Command post , Evacuation team , medial team , Rescue team, fire fighting team and HSE Team. through that meeting the drill scenario will be discussed and minuted on the Emergency Table to meeting form
Compressed Gas Cylinders Access Control Inspection Checklist used for inspection before using and site access
Heavy Equipment Inspection Checklist used for Heavy equipment inspection prior using and site entry
Cranes Inspection Checklist used for crane and lifting equipment inspection before using at work site
Vehicle Inspection checklist used for Vehicle inspection before site Entry
Camp Inspection Form used during Camp inspection and audit
Power points and Presentations
The grantee offered 6-hour training to workers and employers engaged in the construction, deconstruction, and maintenance of telecommunication towers and wind turbines in Iowa, Nebraska, and North Dakota. Training topics included accident investigation, site inspection, and hand and power tool safety. Materials included PowerPoint presentations and student tests. Training is in English.
The grantee provided 2-hour confined space in construction training to workers in the construction industry. Training topics will included confined spaces hazard, air monitoring, and personal protective equipment. Training was offered in English.
The grantee developed safety training materials regarding the recognition and abatement of excavation and trenching hazards. Training materials include an excavation safety manual and PowerPoint presentations.
The Materials Provide safety training about electrical hazards for General Industry Including Arc Flash. Training materials include PowerPoint presentations, handouts, quizzes, and a manual.
The Materials provided presented a bloodborne pathogens program targeting small businesses and fire/emergency service workers and employers. Training topics include routes of infection, prevention, and the OSHA Bloodborne Pathogens Standard. Training materials include PowerPoint presentations, handouts, and quizzes. Training materials are available in English.
The grantee conducted a training course concerning process safety in the biofuels industry. The training course included an introduction to key process safety (PS) concepts in the biofuels sector, how to perform a hazard evaluation analysis, and how to write safe operating procedures. Training materials include PowerPoint presentations and handouts in English
Chemical Hazards/Hazard Communication
The Materials provided training on the Globally Harmonized System (GHS) under the Hazard Communication Standard (HCS) to workers and employers located in rural Pennsylvania. The learning objectives of this training include understanding the GHS hazard classification and labeling system and applying the hazard classification and labeling system within the HCS. An instructional kit was prepared for this training in both English and Spanish.
Aerial Lift
The Material presented aerial lift safety training to workers and employers in the landscaping and tree care industries. Training topics included work practices near utility lines, aerial lift inspection, and driving. Training materials will include workbooks and quizzes.
Cranes
OSHA- 10 Hour Construction outreach
DOWNLOAD
Excavations
OSHA 10-Hour Construction outreach
DOWNLOAD
Health hazards in construction
OSHA 10-Hour Construction outreach
DOWNLOAD
Materials Handling, Storage, Use, and Disposal
OSHA 10-Hour Construction outreach
DOWNLOAD
Personal Protective Equipment
OSHA 10-Hour Construction outreach
DOWNLOAD
Scaffolds
OSHA 10-Hour Construction outreach
DOWNLOAD
Stairways and Ladders
OSHA 10-Hour Construction outreach
DOWNLOAD
Tools – Hand and Power
OSHA 10-Hour Construction outreach
DOWNLOAD
Bloodborn pathogens
OSHA- 10 Hour outreach Training General industry
DOWNLOAD
Electrical
OSHA- 10 Hour outreach Training General industry
DOWNLOAD
Introduction to Ergonomics
OSHA- 10 Hour outreach Training General industry
DOWNLOAD
Exit Routes, Emergency Action Plans, Fire Prevention Plans, and Fire Protection
OSHA- 10 Hour outreach Training General industry
DOWNLOAD
Fall Protection
OSHA- 10 Hour outreach Training General industry
DOWNLOAD
Hazard Communications
OSHA- 10 Hour outreach Training General industry
DOWNLOAD
Hazard Materials
OSHA- 10 Hour outreach Training General industry
DOWNLOAD
Introduction to Industrial Hygiene
OSHA- 10 Hour outreach Training General industry
DOWNLOAD
Machine Guarding
OSHA- 10 Hour outreach Training General industry
DOWNLOAD
Personal Protective Equipment
OSHA- 10 Hour outreach Training General industry
DOWNLOAD
Safety and Health Programs
OSHA- 10 Hour outreach Training General industry
DOWNLOAD
Walking and working Surfaces, Including Fall protection
OSHA- 10 Hour outreach Training General industry
DOWNLOAD
Signs and Slogans
free “danger” safety signs. More free danger safety signs will be added in the future so check back often. Click the thumbnail to bring up the 11″ x 8.5″ inch version of the sign to print or save. The signs were created in landscape mode so they print better that way than if you choose portrait. If your printer prints the date or website name you can click on settings in print preview and choose “empty” on all of the header and footer options to
Free “caution” safety signs for alerting employees to hazardous conditions. More free caution signs will be added in the future so check back often. Click the thumbnail to bring up the 11″ x 8.5″ inch version of the sign to print or save. The signs were created in landscape mode so they print better that way than if you choose portrait. If your printer prints the date or website name you can click on settings in print preview and choose “empty” on all of the header and footer options to remove them.
Free warning safety signs used at work place
Free Emergency safety signs used at work place
Free danger signs used at work place
Safety Flash
A landscaper died after entering the hopper of a bark blower truck and becoming entangled in its rotating auger system. The bark blower truck’s pressure sensors, designed to shut down the conveyor belt when the auger system experienced too much pressure, were broken. Because of the broken sensors, the hopper’s bulk material would bridge over the conveyor belt, forming a tunnel. When tunneling occurred, material would not flow into the feeder and workers were unable to blow the material through the hopper. It had become accepted to have workers inside the hopper standing on bulk material, using a pitchfork to move material into the blower system. The supervisor and another laborer heard a clunking noise coming from the truck and bark stopped flowing through the hose. The victim was found dead, entangled in the stir rod of the auger system.
Construction Siding Subcontractor Installer Killed when Oversized Scaffolding Platform Destabilized and Telescopic Forklift Overturned
A 48-year-old foreman was killed while repairing a water line break. The victim was inside an excavated hole in a roadway.
In April of 2013, an orchard worker died when he was run over by a rotary mower after he fell from the tractor it was attached to. The victim was using the tractor and mower attachment to cut the grass between rows of pear trees. The incident was not witnessed, but investigators believe that it is most probable that he fell when he attempted to dismount the tractor to retrieve his hat that may have been knocked off by a low hanging branch. He likely either failed to put the tractor in neutral when he stopped, causing the tractor to lurch forward when he removed his foot from the clutch pedal, or inadvertently moved the gear selector lever out of neutral as he stood up to dismount the tractor. In either scenario, it is assumed that the sudden or unexpected movement of the tractor caused him to fall to the ground between the tractor and the mower. As the tractor continued to move forward, the victim’s upper body was run over by the 1740 lb. mower. He was pronounced dead at the scene.