Secure Your Lifts:Guidelines for Safe Lifting Operations Free Planning Tool

Any activity that involves the lifting or lowering of a load using equipment such as a crane, hoist, or forklift is considered a lifting operation. Lifting activities are critical in businesses that require big or bulky things to be moved, such as buildings, manufacturing, and transportation. Lifting operations, on the other hand, might be dangerous if sufficient safety procedures are not done. Accidents can cause serious injuries or fatalities, as well as damage to property and equipment.
Several aspects must be addressed to ensure the safe and efficient completion of a lifting operation, including the equipment to be utilized, the load to be lifted, the site circumstances, and the individuals involved. A lifting plan should be created that details the particular steps needed to complete the lifting operation. By following these guidelines, lifting operations can be safely and efficiently completed, reducing the risk of accidents and injuries. It is essential for all personnel involved in lifting operations to be aware of the potential hazards and to take the necessary precautions to ensure the safety of everyone involved.
Also Read: Crane Suspended Personnel Platform Manbsket Permit
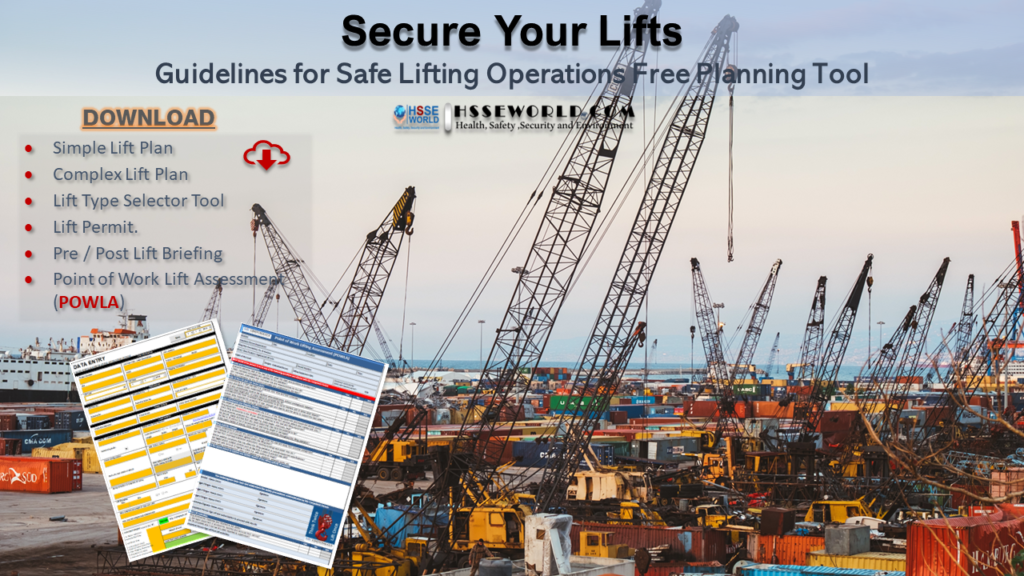
Important Abbreviations and Definitions
Competent Person (CP): An authorized person who has the required level of competency to plan and supervise specific types of lifting operation
Custom-made: Job, shop, or self-made
Engineered Lift: A lift where the load exceeds the rated capacity of the overhead crane
Exclusion Zone: The area around the load where the only personnel present is the Operator and/or Lift Team members
Fall Zone: Area where the load can fall in an unplanned event. This area can vary according to the phase of the lifting operation, the height of the load, how the load is attached, the shape of the load, etc.
Lifting Equipment: Equipment for lifting and lowering loads e.g. cranes, hoists. It also includes attachments used to anchor, fix or support the equipment (e.g. the runway of an overhead crane)
New / Modified Product Lift: A lift that involves either a new product or a modified product, where the modification would impact the existing Lift Plan and /or risk assessment
Normal Lift:
Any lift that does not meet the requirements of:
- Critical Lift
- Engineered Lift
- New / Modified Product Lift
Operator: The person who operates the lifting equipment and has ultimate responsibility for the lifting operation
POWLA: Point of Work Lifting Assessment
Qualified Person: Independent expert with competence and authority to approve exceedance of a crane’s SWL (e.g. representative of Crane Manufacturer, Insurance Company, 3rd Party inspection Authority, Customer)
Rigging(Lifting Accessories):
A component or device used to attach loads to the hoisting mechanism of equipment used for lifting, including but not limited to:
- Slings – synthetic / wire rope/chain
- Lifting attachments – Magnetic / Vacuum
- Shackles / Eye bolts / Hooks / Swivel Hoist Rings
- Pull lifts/Chain falls/ Chain blocks
- Spreader beams
- Lift Clamps
- Custom-designed lifting attachments
Rated Capacity (or SWL or WLL): The maximum load the lifting equipment is certified to withstand under normal use. (also, Safe Working Load or Working Load Limit)
Technical Lifting Advisor (TLA): Someone who is technically competent and can make an informed and impartial judgment concerning lifting operations and equipment, typically a structural or mechanical engineer (or similar professional qualification) with specific knowledge of cranes/lifting.
Requirements
There are mandatory requirements for lifting operations that must be followed to ensure the safety of personnel and equipment besides Compliance with relevant regulations and standards. Regulatory bodies such as OSHA (Occupational Safety and Health Administration) in the United States and the Health and Safety Executive (HSE) in the United Kingdom have established guidelines for lifting operations to ensure that they are performed safely.
The following sections describe the minimum mandatory requirements for lifting operations.
Lifting Teams
All persons involved in lifting operations must be subject to recorded competence checks to ensure necessary training experience and qualification prior to commencing work. See the Section below for further details on training requirements.
All operational sites must maintain a list of personnel authorized to fulfill the following roles*:
- Competent Person (CP)
- Operator
- Qualified Persons
- Slingers / Riggers
- Signallers / Banksman
- Technical Lifting Advisor (TLA)
*Note: Based on the qualifications and experience of specific personnel, it is possible that one person may fulfill multiple roles
Types of Lift
Lifting Operations are categorized as follows:
- Normal
- Critical
- New / Modified Product
- Engineered
Lift Type Selector Tool ( DOWNLOAD ), should be used in conjunction with Figure 1: Lifting Operations Preparation and Execution, to identify the type of lift to be undertaken and the associated control measures, as part of all pre-lift planning (fixed facility and project site).

Prior to commencing any Critical, New / Modified Product, or Engineered lift, an on-site recorded pre-lift meeting, including toolbox talks, must be performed. See Pre-Lift Briefing ( DOWNLOAD ). On completion of the Lift, a post-lift de-brief must also be documented.
Prior to commencing any lifting operation, the Competent Person responsible for supervising that operation must ensure that roles and responsibilities are clearly allocated and communicated to each lifting team member, as defined by the lifting plan.
A POWLA must be performed prior to performing any lifting operation (See Point of Work Lift Assessment DOWNLOAD ).
Lifting Equipment and Rigging (Lifting Accessories)
Minimum formal Lifting Equipment and Rigging inspection requirements are specified in Control of Lifting Equipment and Accessories.
Pre-use inspections prior to any lifting operation must verify that all lifting equipment and accessories are free from damage or defects and marked with:
- Rated Capacity (SWL)
- The inspection status
- An individual unique identification code
Custom-made lifting accessories must only be used if they have been designed by a Competent Person and formally certified as safe for the purpose intended by a TA or Qualified Person and marked .
Any defective or non-compliant rigging or lifting equipment must mark and taken out of service for repair, disposal, or replacement.
Under no circumstances must the load exceed the SWL of the lifting equipment, except when the equipment is under test by an authorized competent person or is being used for an authorized Engineered Lift.
Also Read: Lifting Plan Audit Checklist
Basic Rules of Lifting
The following minimum requirements must be adhered to at all times:
- A lift plan (and risk assessment) must be prepared, checked, and issued by Competent Person prior to any lifting operation
- All lifting equipment and accessories must have a valid manufacturer’s certificate and thorough examination records
- All lifting equipment accessories must be subject to a pre-use inspection by the user
- An exclusion zone must be established around the lifting operation to prevent unauthorized access (See Appendix A ) Below
- No person must be positioned under any suspended load or between any suspended load and fixed objects (See Appendix A) below
- Under no circumstances must the load being lifted exceed the rated capacity / SWL of the equipment, except when under testing by an authorized Competent Person or is being used for an authorized Engineered Lift.
- There must always be 100% visual contact with the load during the lift
- Never engage in activity that diverts attention during lifting operations
- Never ride on a load whilst it is being lifted
- Any person must be able to stop the lifting operation whenever there is a potential safety issue
- Wind speed and weather conditions must be monitored during all outdoor lifting operations – lifting must stop when the wind speed exceeds the safe operating limit of the lifting equipment
- No component of the crane or load may come within 20 feet (6m) of energized lines up to 350kV. For energized lines, up to 1000 kV, the safe distance is 50 feet (15m). An alternate distance may be used if analysis/risk assessment has been conducted in accordance with applicable regulations.
- Cranes must not be used for pulling
For further guidance concerning preparations for lifting, see Appendix B.
Lifting of People
The Lifting of people must:
- Only be performed when, after risk assessment, it has been demonstrated that there is no reasonably practicable alternative
- Be considered to be a Critical Lift and a Complex Lift Plan prepared accordingly
- Only be performed using equipment specifically designed for that purpose, which must be used and operated within its design parameters and local regulatory requirements
Suitable fall protection, tied off to an approved anchor point, which must not be part of the basket or other accessory carrying the person, must be used and a rescue plan prepared and communicated.
Also Read: Critical Lifts
Communication
- The communication method must be documented in the Lift Plan.
- Team members must be able to communicate in a common language.
- Only the assigned Signaller / Banksman will provide instructions to the Operator, however, the operator must always obey a stop signal, no matter who gives it.
- If a signal is not clear to any member of the Lift Team, then the stop command must be given and the signal clarified with the Operator and Lifting Team prior to re-commencing the lift.
- The Operator and Lifting Team (where applicable) must ensure that affected personnel are also warned of the commencement of the lifting operation.
- See Appendix D for typical hand signals for lifting operations
Use External Lifting Services and/or Equipment
If lifting equipment or services are to be hired/purchased, responsibilities for the supply of equipment, personnel, and documentation must be agreed upon in the contract. Preference must always be to arrange a ‘contract lift’ where the service provider manages all aspects of the lift.
For any fully Contracted Lift:
- Company will:
- Vendor assess the Contractor
- Specify that the lift must be performed in accordance with the requirements of this procedure
- Supply load characteristics, such as sail effect and drag coefficient details, to the lifting Contractor
- The Contractor will:
- Provide equipment and rigging that has been properly maintained, tested and certified
- Provide any required certification or records on request
- Organize and control the lifting operation
- Supply the Competent Person / Lifting Supervisor
- Prepare the lift plan and risk assessment
- Identify maximum permissible wind speeds and direction relative to crane position, for the intended worst-case lifts in the Lift Plan(s)
- Include effect and drag coefficients in the Lift Plan calculations, where applicable
Customer/Rental Cranes
If a company Operator is required to use Customer or rented lifting equipment:
- A company Competent Person must perform a documented inspection prior to performing any lifting operation. For Customer equipment and accessories (including lifting beams and support stands), access to equipment and availability and validity of certification must be verified prior to site mobilization.
- If lifting equipment cannot be inspected or does not pass the inspection, then alternative arrangements for the work must be developed with EHS review/approval.
- Inspections by the FieldCore Competent Person must ensure that:
- Documented evidence that required tests, certification, and inspections have been performed
- Monthly inspections are performed and documented
- Daily inspections are performed and documented. Otherwise, they shall be performed prior to use
- All required markings are correct
- If a company Operator is required to use Customer lifting equipment, written authorization must be obtained from the Customer
- Information on ground and surface conditions must be obtained from the Customer prior to the set-up of mobile cranes. The information must include the location of sub-surface hazards such as voids, tanks, or utilities
Training and Competency
The level and extent of training required must be specific to the lifting equipment to be operated or used and the type of lifting operations to be undertaken.
Crane Operators and Riggers must have licenses, certifications, and authorizations as required by local regulations.
Re-training requirements must comply with applicable national and local regulations but as a minimum, re-training must take place at least every 2 years.
Competent Persons must have the practical skills, theoretical knowledge, and ability to carry out risk assessments, produce and assess lift plans, conduct pre-lift meetings, and have the supervisory skills and experience required to manage a specific lifting operation.
Competency reviews must also be conducted whenever performance observations, an incident, or other information indicates re-training is needed.
Records
All approved Lift Plans – Simple and Complex must be stored in the lifting plan library, after first use, and after any subsequent revisions.
Simple Lift Plans must be subject to periodic documented review (minimum every 3 years) to ensure their continued suitability and effectiveness. Each Lift Plan does not have to be revised to record these reviews unless changes to the content are made. The review may be recorded in a register or similar.
APPENDICES
Appendix A: Maintaining a Safe Distance from Loads
The following suggestions for maintaining a safe distance from loads apply to any non-powered cranes, jibs, and similar lifting equipment where team members may need to physically guide the load to the desired landing position:
- 1.5x Rule: Personnel must be positioned no closer than 1.5 times the height dimension of the load
- 45 Degree Rule: Personnel must be positioned no less than 45 degrees from the center line of the lift
Tools or taglines (flexible or rigid) may be acceptable alternatives, subject to risk assessment when distance-based methods are not feasible.
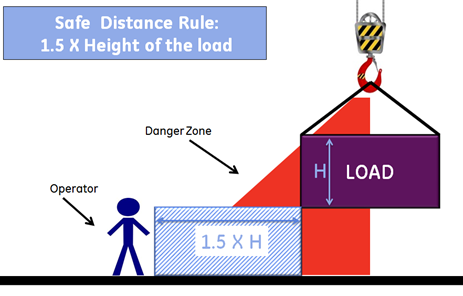
the safe distance of the load
Figure 2

the safe distance of the load 45o Rule
Figure 3
Appendix B: Preparations for Lifting – Guidance
- Lifting Equipment Selection
The following aspects must be considered when selecting lifting equipment:
- How often and where the equipment will be used
- What limitations on use does the manufacturer or supplier of the equipment specify
- The type of load being lifted, its weight, shape, and what it consists of
- The risk of a load falling or striking a person or object
- The risk of the lifting equipment striking a person or some other object
- The risk of the lifting equipment failing or falling over while in use
- It must be ensured that all lifting equipment is manufactured from materials that are suitable for the conditions under which it will be used, having regard for the induced stress at its mounting or fixing points, e.g. the lifting lugs or the base of waste disposal skip
- Does the equipment have appropriate ratings for load size, chemical exposures, and temperature conditions?
- Are sling and lifting attachment angles identified?
- Are attachment points adequate?
- How are slings to be attached?
- Is the hook type appropriate?
- How will manual handling of heavy rigging be done safely?
- Is there a lifting point available directly overhead?
- Are tag lines required and does the lifting team understand the safe use of tag lines?
- Is a tandem lift necessary?
- Is cross-hauling required?
- Are sheaves and attachment points adequate for the possible winch/crane loading?
- Will lifting equipment need to be moved to another location(s) during the lift?
- Do the chains to be used have shortening clutches to balance loads, if required? It is not permitted to twist chains to shorten individual legs
- Lift Plan Content
- The degree of detail in a Lift Plan can vary depending on the type of equipment required and the complexity of the lift but items that should be considered include:
- Initial planning to ensure that the equipment provided is suitable,
- Planning of the individual lifts to ensure they are carried out safely
- Identify and outline controls for identified risks
- Define the pre-use checks required
- Cover procedures that include identification of methods of communication and language
- Detail specific responsibilities if more than one company is involved
- Detail positions and working radii for any mobile cranes to be used, and
- Identify ground loading for mobile crane outriggers
- As a minimum, lifting plans must include:
- Details of all personnel involved in the lifting operation, types of qualifications, roles and responsibilities
- Communication channels – this must be applied when more than one person is involved in the lifting operation
- A description of the type, weight, size, shape and centre of gravity of the load
- Necessary calculations
- Equipment/accessories to be used and necessary diagrams with rigging methods
- The method used for slinging, attaching and detaching the load with the availability of approved lifting points on load when necessary
- The identification of the designated lifting area and the control measures to prevent access such as barriers, signs, etc.
- Sequence of lifts
- Consideration for simultaneous operations and the measures taken to avoid conflicting tasks in the lifting area
- The proximity of hazards and obstructions to the load
- Consideration for overturning, load integrity
- Planning of Lifting Operations
- Factors to be considered when planning lifting operations include:
- Load Characteristics
- Determine the load e.g. weight, center of gravity, stability, and physical size:
- Make ample allowances for unknown factors
- Determine the available capacity of the equipment being used.
- In cases where the assessment of load weight is difficult, safe load indicators or weighing devices must be fitted.
- Rig the load so that it is stable. Unless the center of gravity of the load is below the hook, the load will shift
Also read: Tips for Load Control during rigging
- Positioning of Equipment
- Determine lifting equipment position i.e. where it is to be sited to make the lift
- Determine the suitability of the ground to ensure equipment stability i.e. is the ground able to support the predicted ground loading imposed by the lifting equipment and the load. Obtain accurate data on the ground conditions, including any known underground services, voids or vaults
- Determine access and egress route and any restrictions i.e. the route to the site if necessary as well as the route from the site entrance gate to the identified lifting equipment operating position
- Position lifting equipment to ensure that it is installed to reduce as low as is reasonably practicable the risk of the equipment or load striking a person or from the load drifting or falling freely, or being released unintentionally, and that it is otherwise safe
- Determine the path of the lift and any restrictions e.g. does it have to go over or around buildings or structures?
Also Read: Guideline for Crane Stability and Ground Pressure
- Exclusion Zones
- All areas where loads or lifting equipment might fall must be considered hazardous and therefore properly demarcated. Chains or barriers, complete with warning signs properly displayed, are the preferred means of barricading. The tape must only be used for short-term, vertical, single lifts. If not reasonably practicable, barricading can be replaced by lookouts/bandsmen in sufficient numbers, adequately placed and duly experienced in such tasks
- Determination of detailed restrictions:
- On lifting operations e.g. safety clearances, slew locking, jib extension restrictions, demarcation of the work area, weather conditions
- When working near power lines, ensure that a banksman is stationed at all times within view of the operator to warn him when any part of the lifting equipment or its load is approaching the minimum safe distance Where computerized cranes are used, they must be set to ensure that the crane jib cannot come within any safety clearances.
- Determine specification of crane required and availability – lifting capacity (Jib extension) dimensions, weight. Determine program restriction e.g. time of day, program slot
- Operating perimeters and times of use for mobile lifting equipment must be clearly defined and agreed upon, e.g. during daily coordination meetings, and applied on site.
- Weather Conditions
- Consideration of the weather conditions, where appropriate. Safe workable wind speed varies from crane to crane. In the absence of manufacturers’ specific written advice, seriously consider postponing the lift if the wind speed/gust is in the range of 15-20 mph (7-9 m/s). Above 20 mph (>9 m/s), the lift must be canceled. When the craning operations have been postponed due to high wind/gust conditions loads must be landed and secured
- Safe Working Load (SWL)
- When lifting near the SWL, the load must at first only be raised by a short distance and the operation stopped to check stability and safety before continuing. Wind loading must also be considered in these situations
- When two cranes or other lifting appliances have to be used for one load, each must work within its SWL and must remain stable throughout the lift
- When assessing lifts, the weight in relation to the angle of boom and radius must be considered
- Where the SWL depends upon the equipment’s configuration, this must be clearly identified for each configuration. Alternatively, this information must be retained with the equipment
- The SWL of most lifting equipment does not generally account for the weight of hook blocks, hooks, slings equalizer beams, material handling equipment, and other elements of lifting tackle. Their combined weight must be subtracted from the load capacity of the equipment to determine the maximum allowable load to be lifted
- The maximum SWL of most lifting equipment is determined from static loads and a safety factor is applied to account for dynamic motions of the load and equipment. To ensure that the SWL is not exceeded during operation, allowances must be made for wind loading and dynamic forces set up by the normal operational movements of the machine and load
- Rigging Practices
- Equipment such as chain blocks and pull lifts must be attached to suitable anchor points above the load before any lifting operation can commence. Where the integrity of the anchor point or its ability to support the load, it is intended to lift is not known, no lifting operation must commence until a Competent Person has reviewed the intended anchor point, and confirmed that it is suitable for the intended loads to be applied. Review by a TA may be necessary.
- Where chains and slings are wrapped around loads with sharp edges and corners, suitable protective materials (softeners) shall be placed between the load and the slings to prevent
- To avoid strain on the crane and sliding of the load, the crane hook should be positioned as close to the center of gravity of the load as possible, that is, the hoist line shall be vertical in all directions before starting the lift. The load should be checked as soon as it has been raised slightly to ensure that it is well-secured and properly balanced in the sling or lifting device.
- Two or more separately rigged loads must not be hoisted in one lift. The different weights and centers of gravity may make the combined load difficult to handle and may put a side load on the boom during swinging.
- The load must be controlled at all times. Tag lines or guide ropes should be used on loads that are liable to swing or shall be guided through a restricted space. Care should be taken to guard against injury to workers, structures, or scaffolds from swinging loads. When using tag lines, the line should not be wrapped around any part of the hand or body. It may be necessary to release the line quickly to avoid injury.
- When there is a need to interact with or work around the load (placing or repositioning landing blocks/supports, etc.) the load must be in a stopped position and the use of three-part communication is especially important.
Appendix C: Typical Hand Signals

TypicalHand signals
Figure 4
Appendix D: Comparison of Lift Types with Company Crane Manual
The Company Crane Manual identifies 6 different types of lift, as shown below. The aim of this procedure has been to try to simplify the process and reduce the number of lifts, whilst still meeting the intent of the Manual.
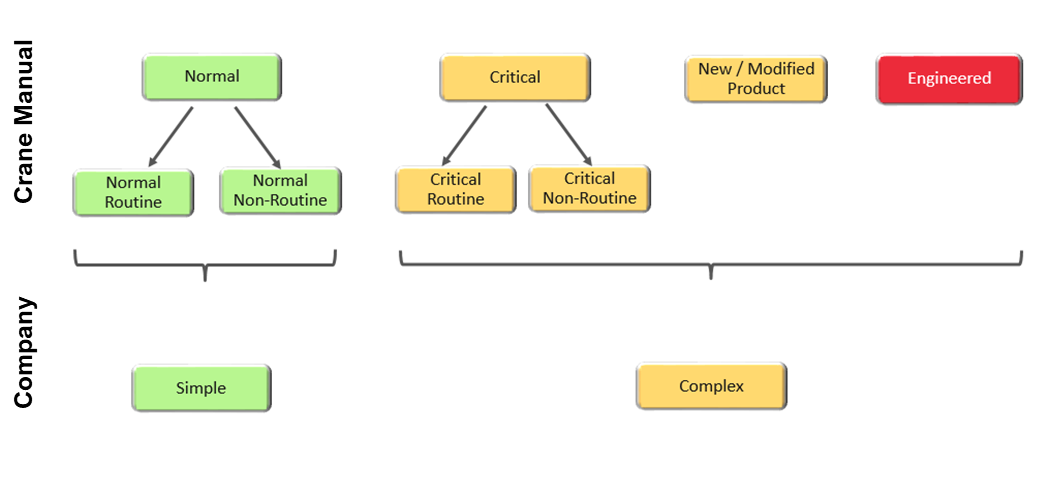
Comparison of Lift Types
Figure 5
Downloads
Simple Lift Plan Form
Complex Lift Plan Tool
Lift Type Selector Tool
Lift Permit.
Pre / Post Lift Briefing Form
Point of Work Lift Assessment (PoWLA)
Also Read: https://hsseworld.com/photo-of-the-day-ergonomic-chair-and-office-chair-safety-tips/
For more safety Resources Please Visit Safetybagresources