Tailoring Zinc: Crafting Custom Specifications for Unique Applications
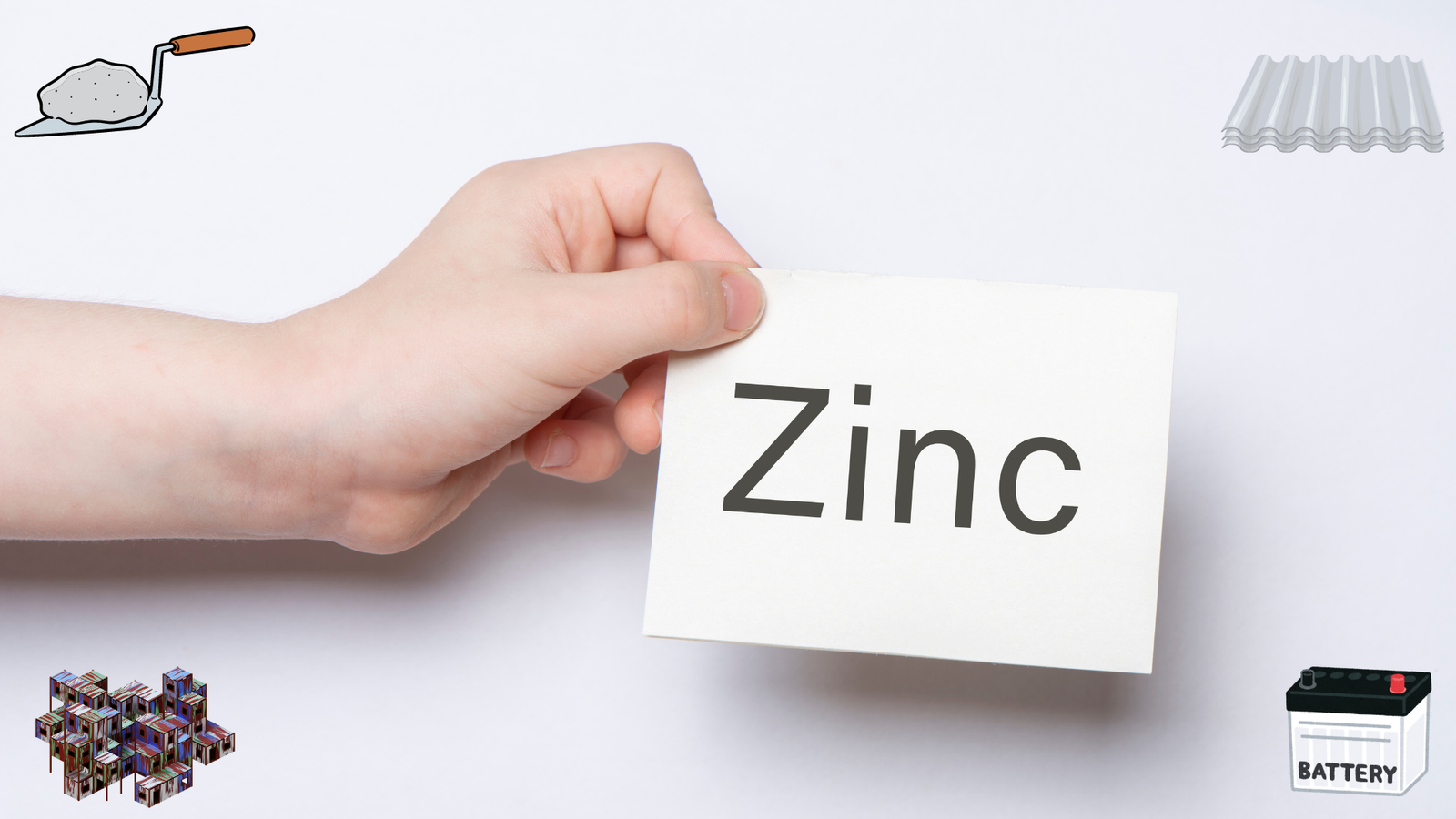
In construction, zinc’s adaptability and durability are highly valued. It is often used in roofing and façade applications, where its resistance to weathering ensures long-term performance. Architectural elements crafted from zinc not only provide structural benefits but also contribute to sustainable building practices, as zinc is a recyclable material with a low environmental footprint. The ability to tailor zinc to specific architectural styles and climates further enhances its appeal in modern construction projects.
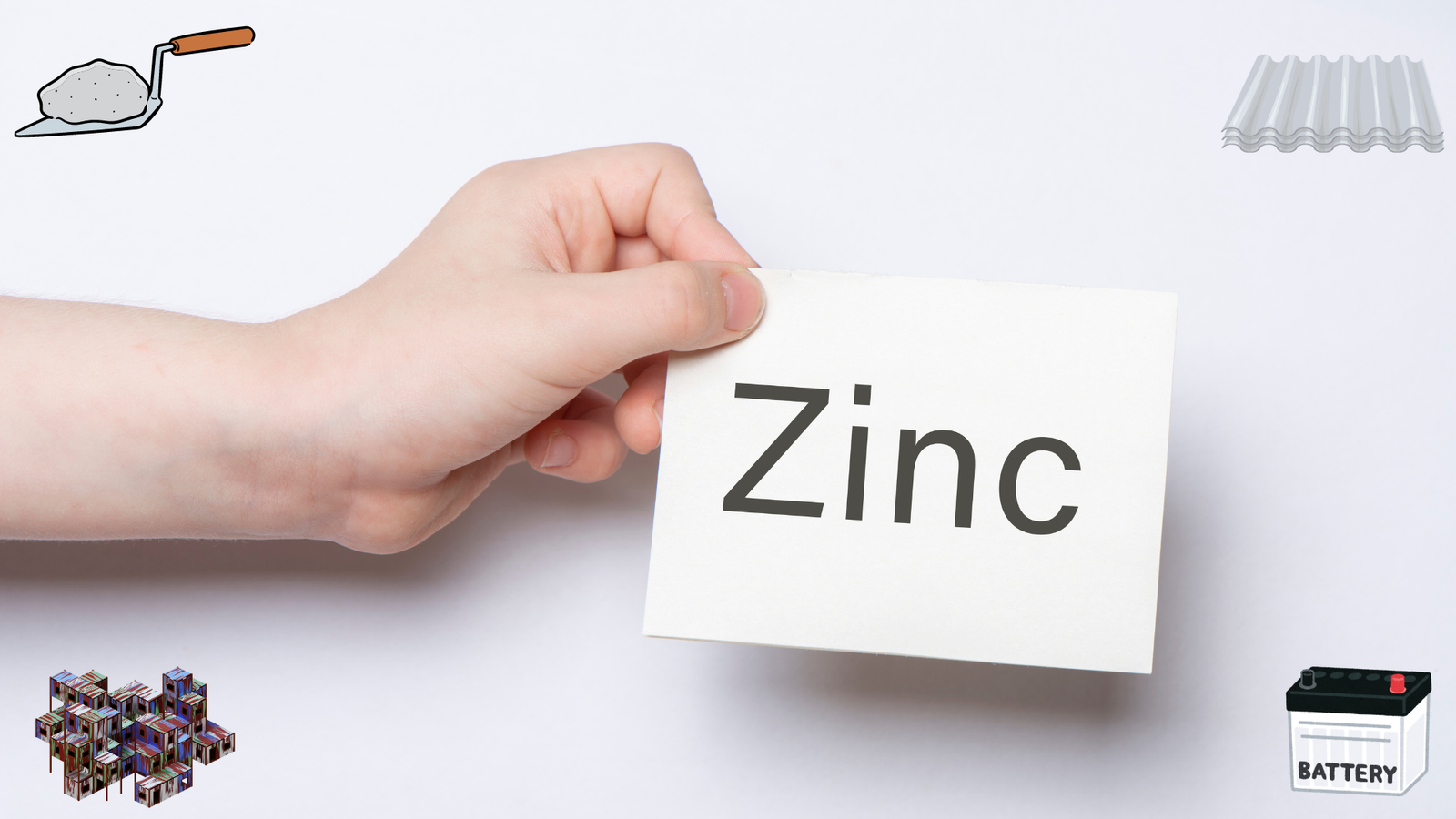
The Versatility of Zinc
Zinc’s versatility stems from its inherent properties. Its excellent resistance to corrosion makes it a protective layer for steel and iron, preventing rust and extending the lifespan of structures and components. Additionally, zinc’s malleability allows it to be easily shaped and formed, accommodating complex designs without compromising structural integrity. These properties make zinc a popular choice for applications where durability and longevity are paramount.
Customizing Zinc Through Alloying
One of the primary methods of tailoring zinc is through alloying. By combining zinc with other metals, such as aluminum, copper, or magnesium, its properties can be significantly altered to suit specific applications. For instance, zinc-aluminum alloys are known for their improved strength and corrosion resistance, making them ideal for automotive components like die-cast parts and body panels. Copper-zinc alloys, commonly known as brass, offer enhanced machinability and aesthetic appeal, widely used in plumbing fixtures and decorative elements.
Coating and Surface Treatments
Zinc’s ability to act as a protective barrier can be further enhanced through coating and surface treatment techniques. Galvanization, where zinc is applied as a coating to steel or iron, is one of the most common methods. This process not only prevents corrosion but also adds an appealing finish to the coated material. Additionally, a zinc dust manufacturer can provide zinc that can be electroplated onto various substrates, offering a thin, uniform layer that enhances both aesthetic and functional qualities.
rubber-insulating-product-5-steps-to-safety-success/
Forming Techniques for Unique Applications
The malleability of zinc allows it to be formed into intricate shapes, meeting the demands of unique applications. Techniques such as casting, extrusion, and stamping enable manufacturers to create complex components with precision. In the construction industry, zinc is often used for roofing and cladding due to its ability to withstand harsh weather conditions while offering a sleek, modern appearance. In electronics, zinc’s conductivity and thermal properties make it suitable for components like heat sinks and connectors.
Zinc in the Construction Industry
In construction, zinc’s adaptability and durability are highly valued. It is often used in roofing and façade applications, where its resistance to weathering ensures long-term performance. Architectural elements crafted from zinc not only provide structural benefits but also contribute to sustainable building practices, as zinc is a recyclable material with a low environmental footprint. The ability to tailor zinc to specific architectural styles and climates further enhances its appeal in modern construction projects.
osha-republic-steel-exposed-employees-to-excessive-lead-levels/
Automotive Applications
The automotive industry relies on zinc for its ability to provide lightweight, durable solutions. Zinc die-casting offers precision and efficiency in manufacturing components such as engine parts, transmission housings, and decorative trims. The customization of zinc alloys allows for the optimization of strength-to-weight ratios, contributing to fuel efficiency and performance improvements in vehicles. Zinc’s role in automotive applications exemplifies its adaptability to meet stringent industry standards.
Electronics and Beyond
In the electronics sector, zinc’s conductive properties are harnessed in the production of batteries, capacitors, and other essential components. Tailoring zinc for these applications involves meticulous control over its purity and alloying elements to achieve desired electrical characteristics. Furthermore, zinc’s role extends to the realm of art and design, where its aesthetic potential is explored in sculptures and decorative pieces.
Conclusion
Zinc’s remarkable adaptability and functionality make it essential across various industries. Through techniques like alloying and coating, it meets and often exceeds the expectations of designers and engineers. Its crucial role in construction, automotive, and electronics highlights its versatility in modern manufacturing, ensuring it remains vital for innovative applications and sustainable practices.
Have more wellness guidance here