Hand Protection from Chemical Exposure

Hand accidents account for between 40% to 60% of recordable workplace accidents each year.1 Yet, knowing how to best protect employees’ hands from chemicals is a common safety problem. A combination of harsh working environments, failure to choose appropriate hand protection, or not wearing hand protection at all are the three major causes of skin and tissue damage. Injuries are also increased when cut, nicked, or cracked hands are ex- posed to workplace chemicals. When the skin’s outermost layer, the epidermis, is weakened, chemicals more easily penetrate the underlying layers, potentially causing severe damage.
This article explains the importance of employers and employees using proper hand protection in the workplace when working in harsh environmental conditions to ensure Readers:
- are aware of workplace conditions that require hand protection;
- understand the steps that make up a hand protection program;
- know how to choose the proper hand protection for a specific job and worksite; and
- understand the different types of hand protection.
Also Read: Types of Hand Protection
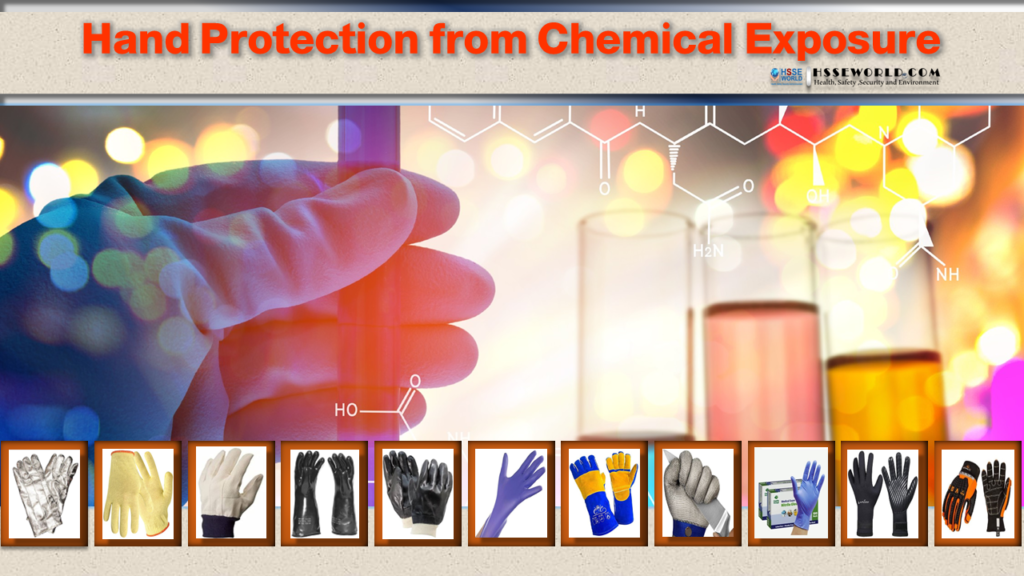
Glove Selection
Selecting a pair of work gloves goes beyond finding the right fit and form. The first step in choosing hand protection is to identify the workplace conditions and chemicals that employees’ hands contact. Checking Safety Data Sheets (SDS) and manufacturers’ labels for specific chemicals or hazardous materials are the best places for employers to start.
Choosing the right type of gloves requires identifying these factors:
- type of chemicals handled (check the SDSs for recommendations based on each chemical or hazard);
- type of contact the worker has with the chemical (total immersion, potential splashing, etc.);
- length of time the worker is in contact with the chemical;
- areas of the body that require protection (hands only, forearms, arms);
- types of gripping or grasping required (dry, wet, oily);
- whether thermal or abrasion protection is needed; and
- size and comfort.
In addition, when selecting the proper type of gloves, employers should:
- check gloves currently in use by employees for signs of wear or damage;
- assess how quickly specific chemicals penetrate or become reactive with the gloves; and
- consider the different effects various chemicals have on particular gloves.
There are many types of gloves available today to protect against a wide variety of hazards. However, these are the general types of work safety gloves and when they should be used:
Also Read: key factors to Find the right glove
Aluminized Gloves
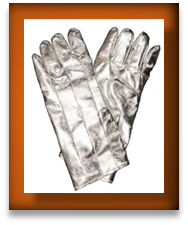
These are one of the best types of gloves to wear when working with heat. They provide both reflective and insulating protection. They are extremely resistant to high temperatures, which is why they are common in welding, foundries, and laboratories. They can protect employees’ hands at temperatures of up to 2,000ºF.
Aramid Fiber Gloves

The durability of aramid fiber gloves (often known as Kevlar® gloves) makes them an ideal choice for industrial situations. The material offers lightweight hand protection making movement easy yet remaining strong under duress. Aramid fiber gloves wear well, are resistant to cuts and punctures, protect against heat and cold, and are often used as a lining in other types of gloves.
Butyl Rubber Gloves
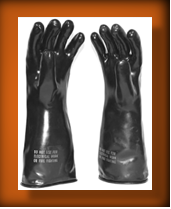
Butyl gloves are the best solution when working with chemicals because they are made of synthetic rubber that does not absorb liquids. The rubber resists harmful chemicals like alcohols, ketones, nitro-compounds, highly corrosive acids (nitric acid, sulfuric acid, hydrofluoric acid, and red-fuming nitric acid), strong bases, esters, and even rocket fuel. They can withstand heat, abrasion, oxidation, and ozone corrosion, and remain flexible at low temperatures. However, butyl rubber does not perform well with aliphatic and aromatic hydrocarbons and halogenated solvents.
Coated Fabric Gloves
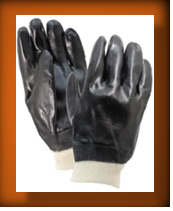
Coated fabric gloves are normally made from cotton flannel with napping on one side. They provide a little more protection than fabric gloves against punctures, cuts, and chemicals. Nitrile, polyvinyl chloride (PVC), and polyurethane are common types of coatings, but the actual coating needed depends on the job itself. By coating the non-napped side with plastic, fabric gloves are transformed into general-purpose hand protection offering slip-resistant qualities. These gloves are used for tasks ranging from handling bricks and wire to chemical laboratory containers.
Cotton/Fabric Gloves
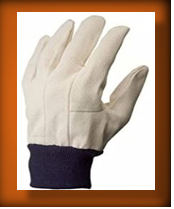
Cotton and fabric gloves are the most common for general work or projects when a high level of protection is not needed. These gloves offer a thin, lightweight fabric covering mostly designed to protect against dirt, splinters, chafing, and minor scrapes. However, these gloves offer little safety to the user when it comes to preventing punctures, burns, or cuts.
Latex or Plastic Gloves
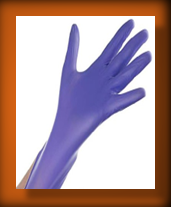
These gloves are most commonly used in medical settings or laboratories. They are usually form-fitting to allow for movability but offer protection from biohazards, chemicals, solvents, and other harmful substances. However, because the material is so thin and flexible, these gloves offer no puncture or heat resistance. They are not ideal when using sharp tools or flames, or when working with abrasive surfaces.
Also, latex gloves have caused allergic reactions in some individuals and may not be appropriate for all employees, Hypoallergenic gloves, glove liners, and powderless gloves are possible alternatives for employees who are allergic to latex.
Leather Gloves
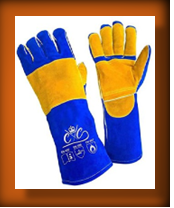
Leather gloves are desirable for many reasons. They protect against sparks, moderate heat, blows, chips, and rough objects. They also provide good grip and durability. They are thicker than regular fabric, which offers a higher level of protection. However, leather gloves can dry, crack, or shrivel when exposed to high temperatures, which makes them not ideal for working with heat. Despite this, they offer suitable burn protection when in good condition. For example, welders often use leather gloves with a durable liner to offer extra protection.
Metal Mesh Gloves
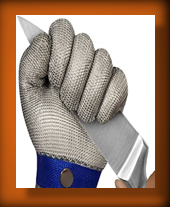
These gloves are specifically designed to resist cuts or punctures to the hand. The woven design helps to deflect sharp objects that could puncture the skin. Industries that perform manual cutting, such as construction, food service, and warehousing, can benefit from puncture-resistant gloves.
Neoprene Gloves
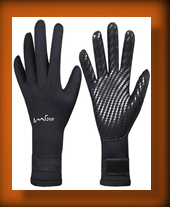
Neoprene gloves are made of synthetic rubber and offer good pliability, finger dexterity, high density, and tear resistance. They protect against hydraulic fluids, gasoline, alcohol, organic acids, and alkalis. They generally have better chemical and wear-resistance properties than those made of natural rubber.
Nitrile Gloves
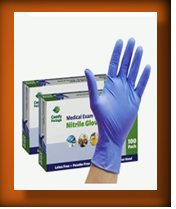
Nitrile gloves are made of a copolymer and protect from chlorinated solvents such as trichloroethylene and perchloroethylene. Although intended for jobs requiring dexterity and sensitivity, nitrile gloves stand up to heavy use even after prolonged exposure to substances that cause other gloves to wear. They offer protection when working with oils, greases, acids, caustics, and alcohols but are generally not recommended for use with strong oxidizing agents, aromatic solvents, ketones, and acetates.
Impact-Resistant and Vibration-Resistant Gloves
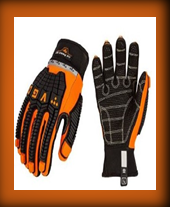
The impact of prolonged vibration is becoming a top concern among safety leaders. Fortunately, there are impact-resistant and vibration-resistant gloves that can help reduce the effects of extended vibration. Impact-resistant work gloves use materials such as thermoplastic rubber (TPR) to scatter the force of the impact and protect a worker from injury. Vibration-resistant gloves cushion the palm, fingers, and thumbs but do not eliminate all the dangers continual vibration poses. However, these gloves help absorb much of the impact of vibrating tools or equipment so that less energy is transferred to workers’ hands. They are most commonly used in the fabrication, automotive, and construction industries where workers use vibrating tools for extended periods. Once the employer has selected the right gloves, ensure that the gloves are used properly. Never substitute one type of glove for another. For example, if an employee is using heavily insulated leather gloves to weld metal, the same pair of gloves would not be used to lift and move heavy, sharp metal plates, since the plates could cut openings in the gloves.
Handwashing and Protective Creams
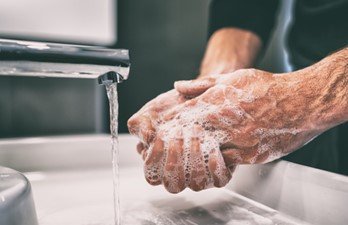
If the employer provides a washroom for employee use, the employer must ensure that proper industrial hygiene practices are used. Simple practices such as proper handwashing will help protect employees. Handwashing is the single most important means of preventing the spread of infection.
Bar Soap vs. Liquid Soap
The type of soap provided can also affect the condition of employees’ hands. Always avoid harsh cleaners that can aggravate skin conditions or dry the skin. Bar soaps can be a poor choice because they can pass bacteria from one employee to another. The best soap choice is a liquid, pH-balanced synthetic soap that moisturizes the skin. Avoid animal-derived soaps, which can contain high levels of alkali and fatty acids.
Antibacterial Soap vs. Plain Soap
Despite commercial claims, antibacterial soaps are no more effective than plain soap and water for killing disease-causing germs outside of health care settings.5 There is no evidence that antibacterial soaps are
more effective than plain soap for preventing infection under most circumstances in public places or the home.6 Therefore, plain soap is recommended in public, non-healthcare settings.
Hand Sanitizers

Another way to clean hands is to provide hand sanitizers in convenient locations in the workplace. The best choice for employees is to wash their hands with soap and water when their hands are visibly soiled. However, if soap and water are not available, using an alcohol-based hand sanitizer in wipe or gel form can quickly reduce the number of germs in most situations.7 (According to Texas Administrative Code §228.38, food handlers in restaurants, schools, delis, and grocery stores must wash their hands with soap and water before applying hand sanitizers.)
Also Read: Photo of the day: Hand safety Facts
Protective Creams
Protective creams can also be an excellent source of hand protection. They can help keep chemicals from penetrating gloves. However, they should never be used as a replacement for gloves. As with gloves and soaps, special care must be taken when selecting protective creams. Both the employer and the employee need to understand how to use the proper protective cream for the job. If an employee is working with petroleum-based hazards, they should use creams that are water-based to naturally repel the petroleum solvent. For protection against water-based hazards, oil-based creams should be used.8 For protective creams to work effectively, they need to be first applied to clean skin at the appropriate time in the employee’s job duty sequence. For example, if an employee works on a machine that uses cutting oil, the cream must be applied to the employee’s skin before work begins. The cream may not offer any protection to the employee if it is applied after the cutting oil has already penetrated the skin. It is important that the employer and the worker carefully read the SDS data to help determine what type of protective cream to use for the task and when. Protective creams can help reduce risks of skin irritation and keep employees productive at work. Remember, employees only have one set of hands. Help them handle them with care on the job.
Also Read: Photo of the day: Hand Safety Facts
Glove Selection Chart for Protection Against Chemicals
Table 1: The following table from the U.S. Department of Energy, reprinted in OSHA’s Personal Protective Equipment Manual (pgs. 26-29), rates various gloves for their protection against specific chemicals. The purpose is to help employers select the most appropriate gloves to protect employees. The ratings are abbreviated as follows: VG: Very Good; G: Good; F: Fair; P: Poor (not recommended). Chemicals marked with an asterisk (*) are for limited service.
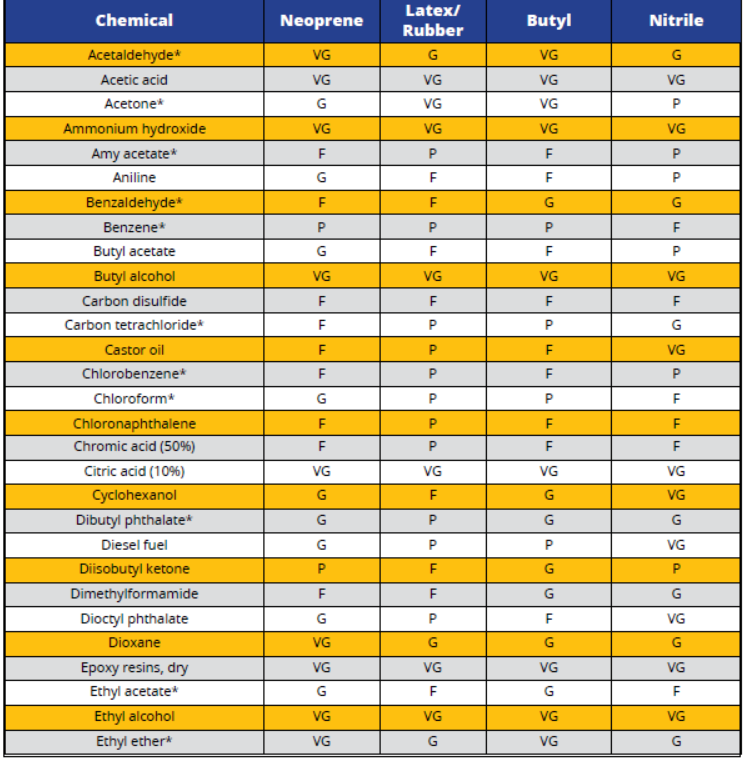
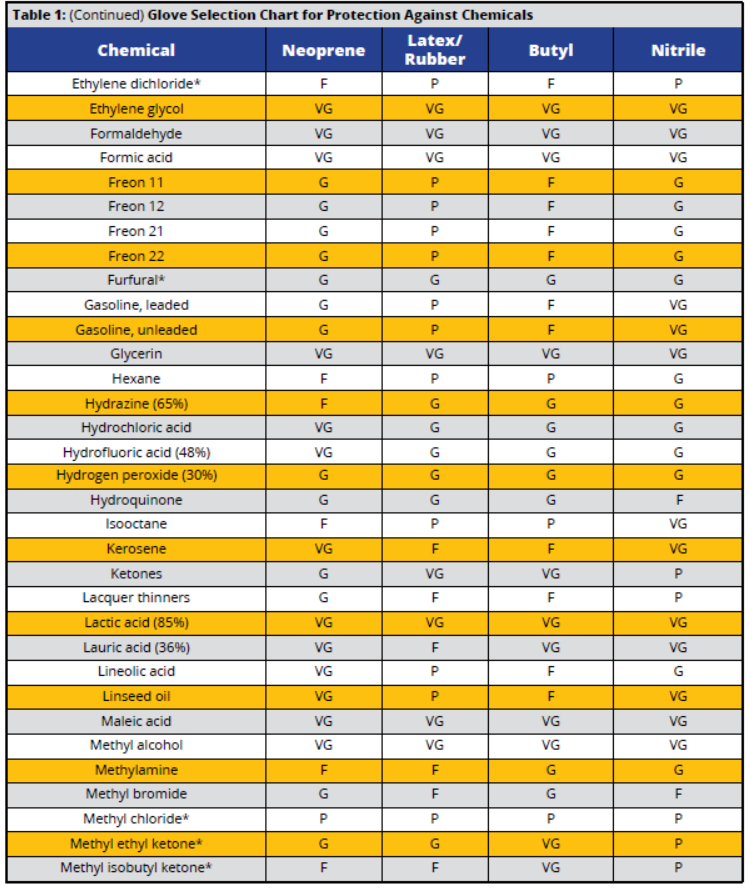

Also, Read: the Chemical Risk Assessment form
Please visit our Safety Resources SAFETY BAG to have many Safety Resources