Compare between Welded and Mechanical Chain Slings
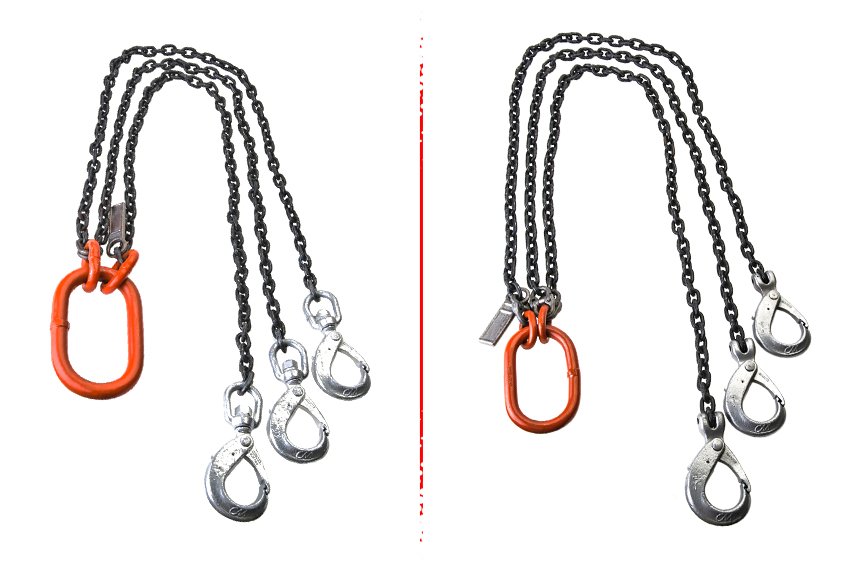
What do you use in your lifting applications, welded chain sling or mechanical chain sling? Have you ever compared the two to see which is better for your company?
In the following article, you will start on the journey to help you make the best choice for your company.
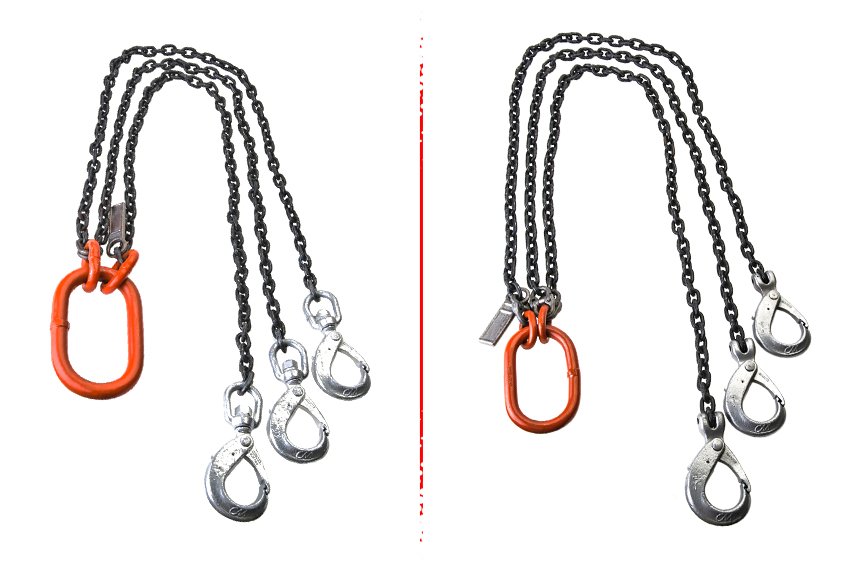
Chain slings are an important part of lifting equipment, but over time, they wear out and need to be replaced, but what do you need to consider before purchasing new slings?
If you use a welded chain sling, is a mechanical chain sling a better option for your company? Likewise, if you’re using mechanical chain slings, does it make sense to switch to welded chain slings?
Before you figure out what is best for the needs of your company and what is most compatible with your existing rigging equipment, we must first examine:
- What each chain sling is
- What grades of chain are used in sling construction
- What is the process of replacing broken or worn attachments
- The inspection process for chain slings
- The benefits and disadvantages to both types of chain slings
- Whether there is a cost difference between welded and mechanical chain slings
Let’s get started on the journey to help you make the best choice for your company.
Define Welded and Mechanical Chain Slings
When talking chain slings, “welded” or “mechanical” refers to the end fittings, including hooks and rings, on either end of the chain and how they are attached.
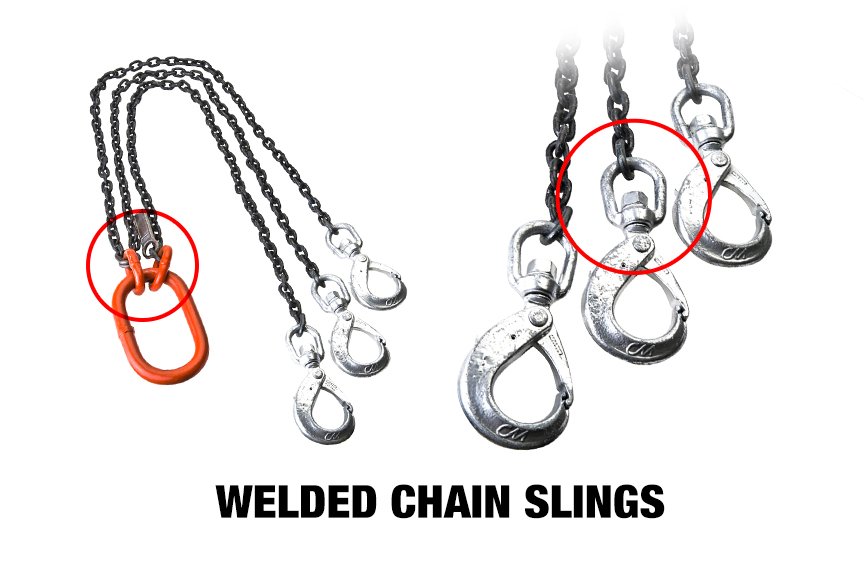
“Welded” chain sling attachments are just that, welded to both sides of the chain, and then, heat treated. These are permanent connections to the chain sling assembly.
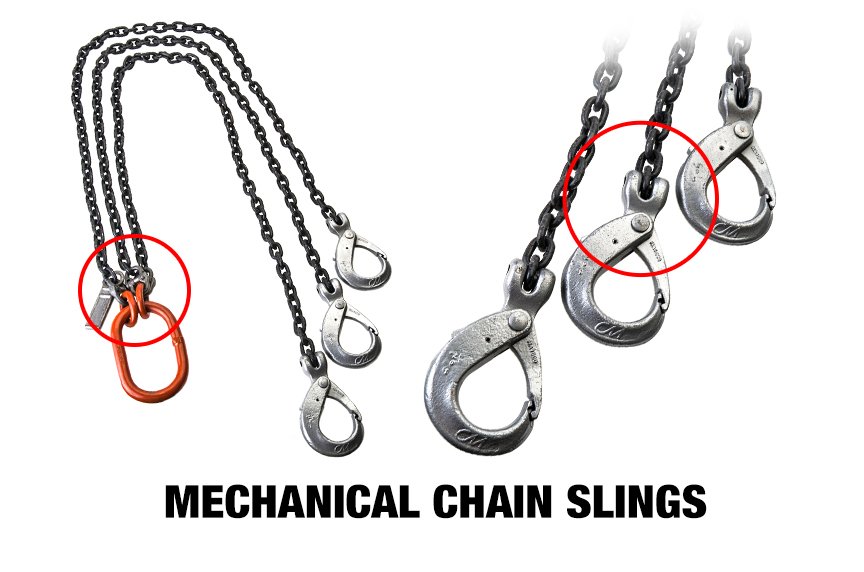
“Mechanical” chain sling attachments are connected to a welded chain and held in place by pins. Mechanical components can be removed and interchanged with other hooks and lifting devices, if necessary.
What are the Different Grades of Chain?
What type of grade is needed for lifting?
First, it is important to note that whether you go with welded or mechanical chain slings, in most cases, both lifting devices will be made of alloy steel. According to industry standards by the American Society of Mechanical Engineers (ASME), Grade 80, Grade 100, and Grade 120 alloy chain slings are approved for lifting.
Understanding that alloy chain is most often used for overhead lifting, there are some applications where a special material chain or even carbon chain proves to be a better answer for the application. These non-alloy applications usually involve some type of acid or high heat that can attack alloy quicker than other non-alloy materials. For these applications, the non-alloy materials can result in longer sling life than alloy.
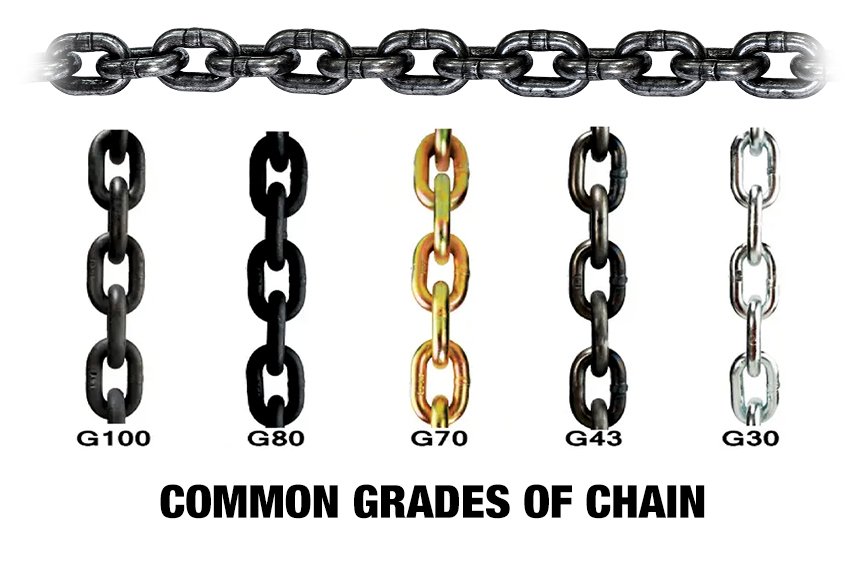
Grade 80 Chain Slings
For lifting purposes, Grade 80 is the lowest acceptable standard, and Grades 100 and 120 can be used depending upon the specific needs of the project it is being purchased to complete.
According to Columbus McKinnon (CM), Grade 80 alloy chain is a higher-strength, heat-treated alloy steel chain primarily used as a sling component for overhead lifting, but also, can be used in rigging and tie-down applications where a lighter weight, higher strength chain is desirable.
Grade 80 chains are recommended for overhead lifting by the National Association of Chain Manufacturers (NACM), Occupational Safety and Health Administration (OSHA), and ASME.
Grade 100 Chain Slings
Grade 100 chain has approximately 25 percent higher strength than Grade 80 and is used primarily as a sling component for overhead lifting. Grade 100 chain can be used for all the same applications as Grades 30 through 80, according to CM.
Much like Grade 80, Grade 100 alloy chains are recommended for lifting by NACM, ASME, and OSHA.
Grade 120 Chain Slings
Grade 120 chain has squared edges instead of the typical rounded edges found in other grades and is considered the highest-strength chain available for lifting. However, it is not as commonly produced, and thus, more expensive than Grades 80 and 100 chain slings.
Durability and Repairs of Chain Slings
Whether you go with a welded or mechanical chain sling, both have the same working load limits at equal specifications and configurations and have the same performance in extreme heat/cold temperatures.
Chain slings are one of the few types of slings that can be repaired or modified. If you need repairs, mechanical chain sling attachments can be fixed quicker and easier when parts wear out or become unusable. Mechanical chain sling attachments can be replaced by any competent employee on the Jobsite.
The downside to any employee being able to modify the chain sling attachments is the sling identification tag becomes outdated and the company itself needs to put its name on the tag as the repairing entity because it took on the responsibility for the modifications. Doing so means the company accepts the liability should the sling malfunction after the modifications are made.
When welded chain slings need new attachments, the modification must be done by an experienced welder at a certified manufacturer.
How is a Chain Sling Inspected?
Regardless of the methods used to modify the chain sling, any repairs or modifications must be proof tested before it can go back into service.
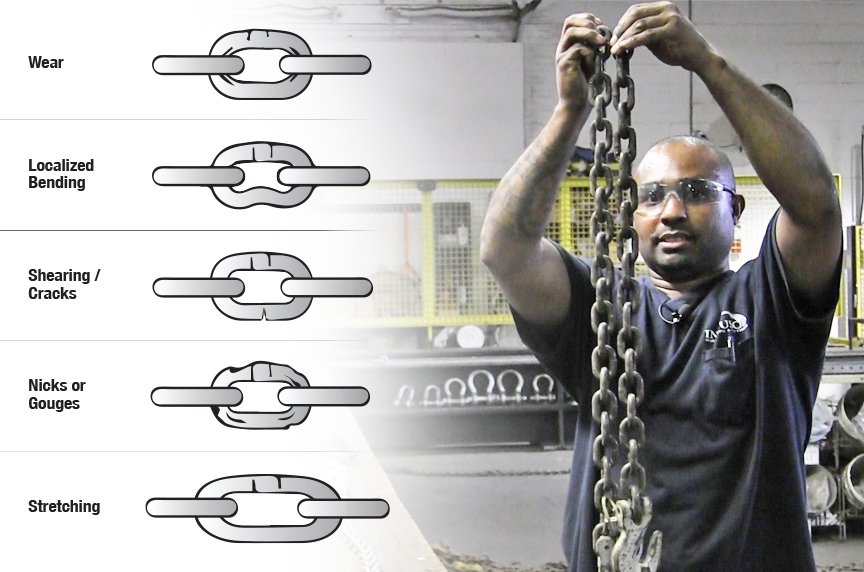
When a link in a welded chain sling is damaged or broken, it must be repaired by a certified manufacturer. If a link in a mechanical chain sling is damaged or broken, you must replace the entire length of the chain. Following the repairs, the chain sling must be proof tested to meet or exceed OSHA/ASME standards.
Mazzella uses an ISO procedure to proof test its repair work for both mechanical and welded chain slings. Any sling proof tested by Mazzella is done per the proof load requirements in the ASME B30.9 Slings standard, and then, inspected for any damage done to the links or other components before returning it to service.
“When inspecting mechanical or welded chain slings, the process is the same for rigging technicians,” says Tom Horner, Mazzella’s Rigging Inspection Manager. “You have to pay more attention when inspecting a mechanical chain sling because mechanical components may affect the way a chain sling hangs off a crane hook or lays on a table or the ground.
“If you have an assembly with four legs and extra adjusters, that’s a lot hanging off a large master link. If those extra components get kinked or bunched up, it may cause the four hooks at the bottom to look like they’re hanging unevenly — which may give an indication of stretch to the untrained eye.”
Pros and Cons of Welded Chain Slings
Pros
- No mechanical components that could wear out quicker
- Sling repairs are done by experts – usually the sling manufacturer or a qualified person – before being put back in service
- Sling repairs are proof tested and certified after assembly for workmanship/strength of the welds
- Offers users durability and long-lasting life when maintained and inspected regularly
Cons
- Because of the heat-treating process, welded chain slings take more time to fabricate or repair
- Welded chain slings require specialized welding equipment and certified manufacturers to repair
- May require longer lead time when ordering due to welding and heat-treating processes
Pros and Cons of Mechanical Chain Slings
Pros
- Easier and quicker to repair
- Slings can be repaired/modified by qualified on-site personnel
- Offers users durability and long-lasting life when maintained and inspected regularly
Cons
- Components can wear out quicker than on a welded chain sling
- People on-site can make adjustments
- How is that a pro AND con?
- Because you take on the liability that the repair is done right. If it fails, you and your company would be liable for any damages to persons/property if that adjustment was done improperly.
- You are required to update the sling tag and put your company name on it because of the modifications.
- Because repairs require proof testing, a company doing their own repairs must either send out repaired slings to have them tested, or they must invest in proof test equipment to adequately do the tests.
Is There a Difference in Cost?
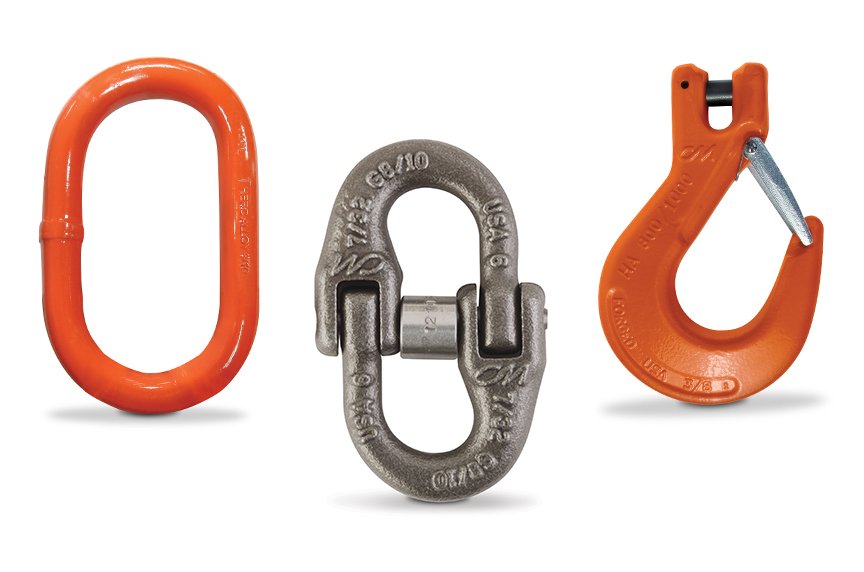
Neither welded chain sling nor mechanical chain sling assemblies have a true advantage when it comes to cost or price differences. For slings of equal configuration and capacity, the price should be pretty much the same. Some factors that may affect the price include differences in:
- Length
- Chain diameter
- Capacity
- Grade of chain
- Specialized fittings (hooks, links, rings, etc.)