Photo of the day: Concrete Truck Driver Hand Signals
Concrete pumping is an efficient method of moving and placing concrete. This process is used in the manufacture of pre-cast and tilt-up panels, concrete formwork, slab construction, concrete paving, and concrete spraying.
The construction and concrete pumping industries must be aware of the obligations to prevent harm to employees, contractors, and others under the Health and Safety in Employment Act 1992 (the Act) and its regulations.
The photo of today provides practical advice about the safe operation and maintenance of concrete pumping equipment. The emphasis is to ensure a safe working environment whenever this equipment is used.
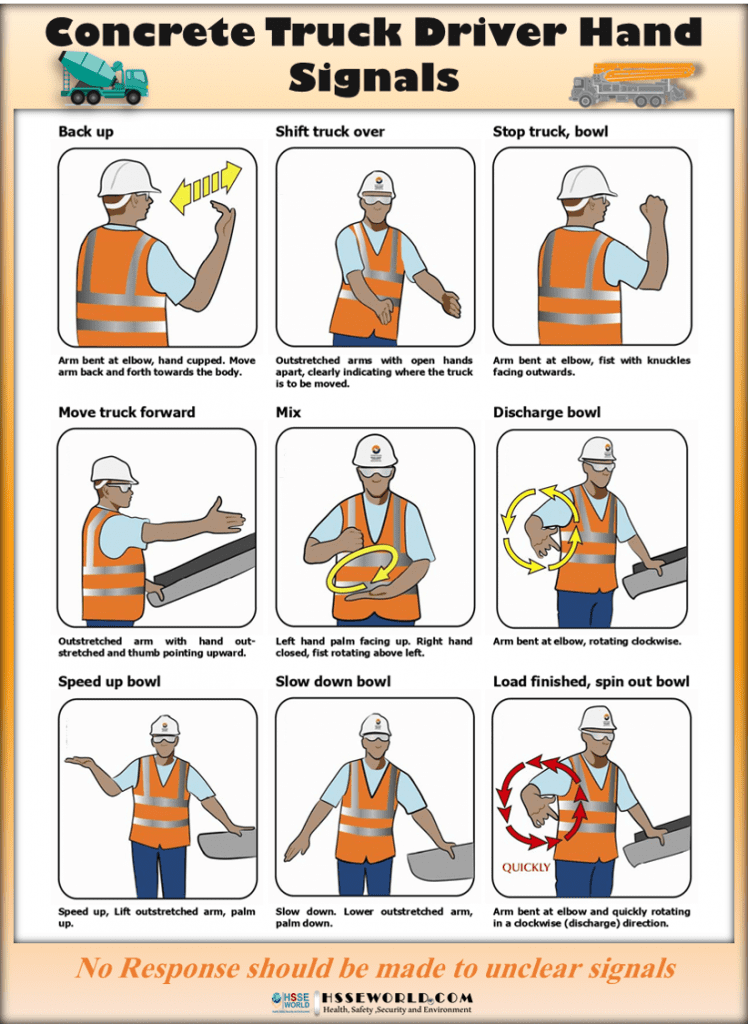
SET-UP safely
Concrete pumping equipment in operation should not create a hazard to the operators, other workers or the public.
Arrival on site
When arriving on-site (where practicable), the concrete pump operator, or another experienced representative, should be shown the set-up area, and the site conditions reviewed with the other contractors involved in the pumping operation. Where any of the conditions under which the pumping equipment is to operate are not satisfactory, or if confirmation of the equipment’s mechanical soundness is not available, rectification should occur before pumping commences.
Pump set-up
The concrete pumping area should be reasonably level, solid, and free of obstructions, with careful attention paid to the positioning of the pumping equipment and any stabilizing devices. In particular, the area should be:
- clear of excavations, trenches, or holes in the ground
- clear of inadequately compacted or soft ground
- clear of cellars, basements, pits, or back-filled ground, unless stability is approved in writing by a qualified engineer
- clear of overhead power lines and fixed electrical equipment
- of a size enough to allow for safe operation
- of a size enough to allow for the safe discharge from the concrete delivery trucks.
Boom set-up
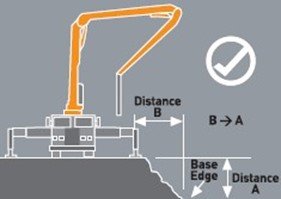
Figure 1: Position pumping equipment clear of excavations
The boom placement system should be set up at a level or at no greater angle than recommended by the manufacturer, as specified in the operator’s instruction manual.
Outriggers
Where outriggers are fitted, ensure that:
- adequate packing of sufficient strength and the load-bearing area is available for the outrigger stabilizing pads. Packing may include engineered bog mats or suitable timbers. The use of loose softwood timbers is not recommended
- before the boom is erected, that the outriggers are extended, lowered, and locked in position. Wherever possible, the outriggers should be fully extended.
- If outriggers are not fully extended, the reduced safe operating radius must be known and recorded in the task analysis.
- the pads are clear of excavations; soft or filled ground or other obstacles are liable to interfere with the safe operation of the machine
- regular inspections of the outrigger pads are conducted to check for subsidence and loss of stability
- the boom is folded in the travel position before raising the outriggers when making any positioning adjustments.
Placing the boom
A concrete placing boom should not be:
- raised or left extended when winds exceed the maximum safe wind speed for operation (specified by the manufacturer)
- raised or left extended during an electrical storm or thunderstorm
- used as a crane
- used to pump concrete with the rams in tension, unless designed for this purpose
- raised, lowered, or moved when there is insufficient light to do so safely.
In addition, any truck-mounted placing boom should:
- have the earth safety chain deployed before the operation
- not be raised from the travel position if under a power line, unless complying with section 2.6.
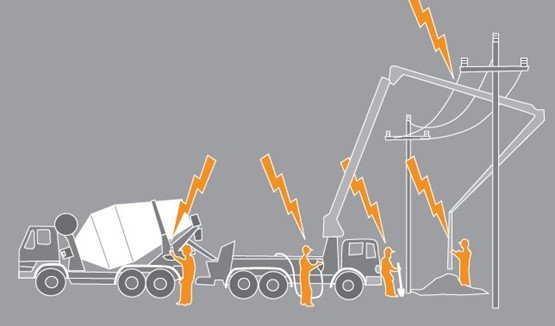
Note: Tiger battens do not protect people from the risk of electrocution or electric shock – they only provide a visual warning for people working in the area of power lines.
Receiving hopper
The concrete pump should be positioned so the receiving hopper is at a height that allows a gravity flow of concrete from the pre-mix delivery trucks into the hopper.
Hopper guard
The concrete pump should not be operated unless the hopper opening is fitted with a grille-type safety guard:
- upon which no-one is allowed to stand
- which prevents access to dangerous moving parts
- is constructed of parallel or mesh bars complying with AS 1418.15: Cranes (Including Hoists and Winches) – Concrete Placing Equipment
- which requires a tool to be removed
- is connected to an interlocked cut-out switch designed to stop all moving parts if the guard is lifted.
A correctly fitted hopper guard reduces the risk of body entrapment within the moving parts of the hopper, but due to its design, it cannot protect against all possible contact with the moving parts. Equipment manufacturers use a range of additional measures to limit the likelihood of entrapment, including:
- separating the operator’s controls away from the moving parts
- raising the height of the hopper lid from the ground.
When working in the vicinity of the hopper, the manufacturer’s operating and safety instructions should be strictly observed.
Operational safety zone
Access to areas around the concrete pump and delivery pipeline should be restricted – the most appropriate method of isolating the area should be used.
The use of one or more of the following controls is recommended:
- covered walkways
- barricades
- posts and safety mesh
- posts and danger tape or flags.
Where the pumping or pipeline set-up is for a longer duration project, the isolation methods should be made more permanent.
Other people
No person, other than those workers directly involved in the concrete pumping operation, should be in the operational safety zone during concrete pumping.
Concrete delivery area
The concrete truck delivery area, including the area around the pump hopper, should be set up to ensure that:
- workers are safe from other vehicles
- adequate lighting is provided if pumping in non-daylight hours
- appropriate signage is posted
- there is clear access for delivery trucks.
If multiple concrete deliveries are expected and on-site traffic management is not provided, only one delivery truck should approach and discharge into the hopper at a time.
If a designated on-site traffic controller is provided, the following safety rules should be followed:
- all personnel connected with discharging from concrete trucks are to wear appropriate high-visibility safety vests
- all concrete delivery trucks must have operational reversing beepers
- the traffic controller and truck driver should be in positions that prevent them from being caught between the hopper and a reversing truck
- the traffic controller should warn the driver at the pump of the presence of another truck being reversed into position
- the traffic controller should be in a position visible to the reversing driver and where the hopper area can be observed
- delivery drivers should ensure that their vehicles remain clear of the discharge area until signaled to reverse into position by the traffic controller
- if the driver loses sight of the traffic controller when reversing into position, the driver should stop immediately.
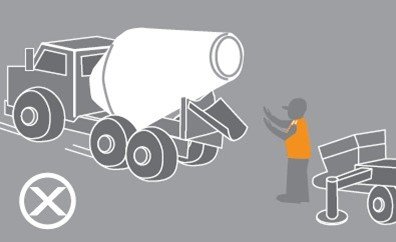
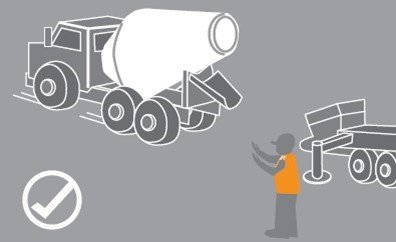
Hand signals
Information about hand signals for concrete truck reversing is located at the Main photo or download it from the bottom below.
Public areas
If the concrete pumping equipment or pipeline is in an area accessible to the general public, the principal should provide adequate control measures to protect the public from any dangers associated with the pumping operation.
- Pedestrian Controls
If the general public can come close to any part of the concrete pumping operation, the following options are recommended:
- directing the public to an alternative footpath, or providing an alternative pathway
- installing protective screens to prevent concrete splashing on members of the public
- erecting barricades and warning signs.
For longer concrete pumping operations, pedestrian controls should be of a more permanent nature.
- Traffic Controls
The principal, in consultation with the pumping contractor, should provide adequate traffic control measures.
Delivery pipeline set-up
When installing a pipeline system, all individual components must be compatible and comply with the pump manufacturer’s specifications for minimum pressure rating and maximum diameter. A pipeline should be installed in accordance with AS 2550.15: Cranes – Safe use – Concrete placing equipment, ensuring that:
- unnecessary bends are avoided
- each section of the pipeline is adequately supported and secured to the building to avoid extra load on the pipe clamps
- when changing the pipeline from the horizontal to the vertical, the pipeline is fixed to stop the movement of the bend or the vertical and horizontal lines which may cause the 90˚ bend to snap off at the clamps
- cranes or hoist towers, scaffolding, or formwork are not to be used to secure the pipeline unless designed for this purpose
- all metal pipes and pipeline components are identified and inspected before installation
- the designed pressure of the pipeline is compatible with the rated maximum concrete pressure of all pumps to be used on the pipeline during normal operations.

Note: If a pump fails during operation, a replacement may be required to complete the pour and clean out the pipeline. If a pump of the same or lower (if suitable) pressure rating is not available, a higher pressure rated pump may be used to complete the pour, provided:
- the concrete pressure rating of the pipeline is known
- there is a method of monitoring concrete pressure
- an operator is continually monitoring the concrete pressure
- the concrete pressure does not exceed the pressure rating of the pipeline.
Note: if the manufacturer provides a conversion factor, the pump’s hydraulic pressure gauge may be used as an indicator of concrete pressure.
Pipe clamps
Clamps connecting concrete piping need to be of the correct size, appropriate for the pressure rating of the pump and maintained in good condition.
All pipe clamps used on any pipeline system must be:
- able to sustain the maximum concrete pressure applied to the pipeline by the pump
- regularly inspected by a competent person for signs of wear or fatigue
- immediately replaced if deformed or damaged.
Clamps should
also be permanently marked with the manufacturer’s name (or trademark), and the maximum permissible
operating pressure. The clamps should be rated at a working pressure
equal to or greater than the maximum working pressure of the concrete pump.

Quick-release pipe clamps may only be used if provided with locking pins and should be visually checked prior to each pumping operation.
Locking pins, R-type or equivalent, are to be fitted and engaged when quick-release pipe clamps are used on fixed or vertical pipelines, or:
- where compressed air is used for cleaning pipelines
- the rated maximum concrete pressure exceeds 40 Bar.
All pipeline connections from the boom must be secured by safety chains or wire strops to prevent the pipeline from falling to the ground if a clamp fails.
Pipeline movement
The pipeline should be adequately secured to the building or structure, with attention given to the reaction forces generated where high pump pressures are involved. The mounting system should be designed to ensure the pipeline remains in place. Support brackets in a vertical pipeline should be spaced no more than three meters apart. Expansion anchors of the high-load slip control type or other fixing methods of at least the same structural strength should be used if fixed to masonry. The surging action of the pump should not cause excessive pipe movement. If required, additional anchor brackets or other suitable methods to restrict pipe movement should be used.
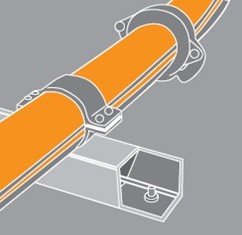
End-hose
The rubber delivery end-hose should:
- be inspected for excessive wear or damage prior to being fitted
- where connected to a boom: be secured by a safety chain, sling, or another restraining device
- not contain metallic parts
- not be longer than specified by the pump manufacturer.
If concrete pumping has stopped and the hose is maneuvered overwork or public area, the operator must prevent concrete from falling from the hose outlet.
End-hose and reducer combination
If the delivery end-hose is replaced by a hose and reducer combination, only those combinations assembled to the manufacturer’s instructions should be used, and:
- locking pins are to be engaged on all quick-release pipe clamps in the assembly
- each piece must be capable of withstanding the rated maximum pressure of the pump
- each hanging piece is tethered by a safety cable, sling or chain
- the combined weight of all pieces MUST NOT EXCEED the weight of the manufacturer’s recommended end-hose.
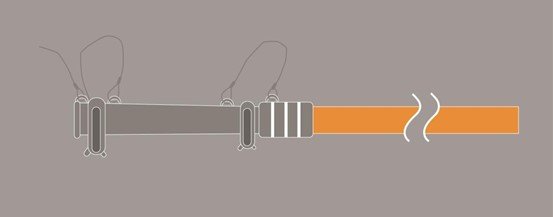
Download the infographic
Concrete Truck Driver Hand Signals
More Photos
- What are the Best Practices for Managing Subcontractor Risk
- Photo of the day: 10 Essential Safety Tips for Driving in Hot Weather Conditions
- Photo of the day: best workplace safety tips
- Photo of the day: The Importance of Stop Work Authority in Maintaining Workplace Safety
- Photo of the day: Tomorrow’s Reward for Working Safely Today: Cultivating a Culture of Safety
- Photo of the day: Preventing slips and trips at work
- Photo of the day: Learn the DRSABCD action Plan
- Working with Electricity Electrical Accidents Guide for Electrical Workers
- Photo of the day: Hearing Protection Device Selection
- Photo of the day: If An Earthquake Shakes You-Infographic free
- Fire Safety Posters Free Download
- Photo of the day: First Aid for Electrical Burns-Infographic free
- Infographic: First Aid for Cuts and Scrapes free download
- Photo of The day: Work Safe with Lasers-Laser Safety free
- Photo of the day: Working Safely with chemicals and chemical Management
- Photo of the day: Safe work practices when using MEWPs ( updated)
- Photo of the day: Preventing Common Kitchen Hazards
- Photo of the day: Safe handling of Gas Cylinders and lecture bottles
- Photo of the day: Forklift Stability Triangle
- Photo of the day: Defective Tools Safe Work Practice
- Photo of the day: Lift With Your Legs Not With Your Back
- Photo of the day: First Aid for burns
- Photo of the day: The 7 Principles of HACCP
- Photo of the day: Working Safely with Suspended Loads
- Photo of the day: Heat Stroke First Aid and safety posters
- Photo of the day: Near-Miss Reporting and Posters
- Photo of the day: Ergonomic chair and office chair safety tips
- Photo of the day: Whole Body Vibration
- Photo of the day: Substation Safety Equipment
- Photo of the day: Bypassing Safety Controls Rules
- Photo of the day: Lightning Safety Tips
- Photo of the day: Overhead Power lines Clearance
- Photo of the day: Floor Marking
- Photo of the day: Types of Foot Protection
- Photo of the day: Types of Hand Protection
- Photo of the day: Lockout and Tagout Safety
- Photo of the day: Fall Protection Plans
- Photo of the day: Flood Safety Tips
- Photo of the day: Read All Labels Work safe
- Photo of the day: Run Project safely with Crane Hand Signals
- Photo of the day: Flagman and Traffic control
- Photo of the day: Managing Risks of Exposure to Solvents in the workplace
- Photo of the day: Scissor Lift Safety
- Photo of the day: HSE Bulletin Board
- Photo of the day: Arc-Fault Circuit Interrupters (AFCI)
- Photo of the day: Safe use of ladders and step ladders
- Photo of the day: Concrete Truck Driver Hand Signals
- Photo of the day: Extension Cord Safety Tips
- Photo of the day: Protect your Head
- Photo of the day: choosing the right Anchorage
- Photo of the day: Work-Related Asthma
- Photo of the day: Top FIVE Heavy Equipment Construction Site Safety Tips
- Photo of the day: sun safety in the workplace
- Photo of the day: Cannabis and Impairment in the Workplace
- Photo of the day: Position for safety and comfort-Safety Tips
- Photo of the day: Generator Safety
- Photo of the day: Controlling COVID-19 in the Workplace-Physical Barriers
- Photo of the day: Manual Material handling
- Photo of the day: Personal Protective Equipment last resort
- Photo of the day: WHMIS 2015 – Pictograms
- Photo of the day: Indoor Air Quality
- Photo of the day: Noise in the affected workplace
- Photo of the day: Fatigue at Work
- Photo of the day: Don’t be Driven to Distraction
- Photo of the day: working in heat and Humidex Rating
- How to use Plate Clamps Safely: Safety Moment#34
- Photo of the day: Sitting at work
- Photo of the day: 5 ways to reduce the risk of Slipping and Tripping
- Photo of the day: Preventing the spread of contagious illness
- Photo of the day: Incident Investigations
- Photo of the day: 10 Scaffold Safety Essentials
- Photo of the day: Effective Health and Safety Committees
- Photo of the day: New worker Orientation & Safety Orientation checklist
- Photo of the day: Workplace Inspection
- Photo of the day: musculoskeletal disorders
- Photo of the day: Emergency preparedness in the workplace
- Photo of the day: Mental health in the workplace
- Photo of the day: Trenching Safety Tips That Can Save a Life