How to use Plate Clamps Safely: Safety Moment#34
10 min readPlate clamps, or sheet clamps, make difficult lifts safer and easier. While these strong lifting tools allow for faster production speeds, they should not be used haphazardly. The use of plate lifting clamps requires an operator who is trained on their use and who takes safety seriously.
in our safety moment today, you will learn the Different Types of Plate Clamps and how to use them safely


How Plate Clamps Work
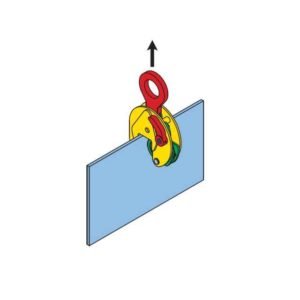
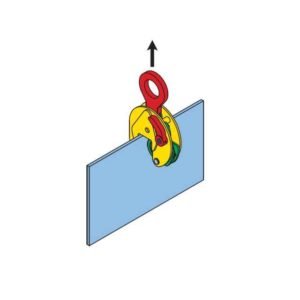
Plate clamps eliminate the need for drilling or creating a hitch. The most important parts of a plate clamp include the lifting shackle, spring, teeth within the jaw, and the various links and pins. To lift a plate, the teeth of the plate clamp need to be pushed into the plate. With help from the powerful spring, this turns the lifting point of the clamp into the lifting point of the plate and essentially causes the two objects to become one.
What’s great about plate clamps is that their grip strength automatically increases as the load gets heavier. Essentially, the weight of the load determines how much link tension there will be and the link tension determines jaw torque and ultimately grip strength. Learn more about what this means below.
Learn from Incident
Plate clamps (or friction-type pressure gripping lifters, according to ASME B30.20) are a lifting aid that grips the load. They are a necessity in the lifting operations for many industries, but when a lift goes wrong, there is an opportunity for education. In this case, a worker lifted a 5/8″, 460-pound, plate of steel from a horizontal position and rotated the plate to vertical with a plate clamp. While attempting to attach a tag line to the clamp the plate slipped and landed on the worker’s foot breaking three bones. An accident investigation identified the following:
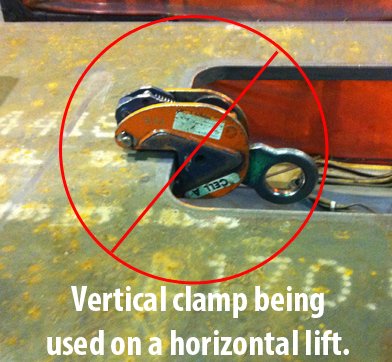
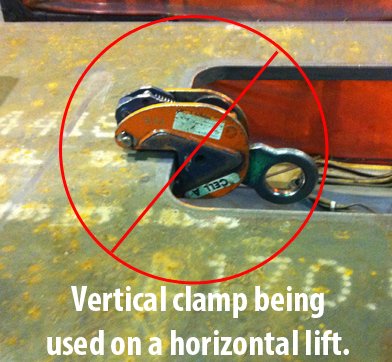
- The plate clamp being used was designated for 1-1/4″ to 2″ plate and was rated for 6,000 pounds.
- The plate clamp used to lift and rotate the plate was clearly marked for vertical lifting only.
- The weight of the plate was too light for the plate clamp size that was used.
- The employee was not properly trained in the use of plate clamps.
While we are thankful that the injury was not more serious, could it have been avoided? Absolutely! So let’s look at the following tips to help maintain safety when using plate clamps.
How to Pick the Proper Size and Type of Plate Clamp


Choosing the proper size plate clamp will not only maximize safety but also extend the life of the plate clamp. To do this, you should buy a clamp with the closest working load limit (WLL) to the weight of the plate being lifted. This ensures that the jaw provides optimal clamping force and penetration. Keep in mind that bigger is not always better with plate clamps. There are minimum load requirements because a load that is too light will not be able to create sufficient grip strength. That’s why most plate clamps have both minimum and maximum load requirements stamped on them. It’s recommended that you avoid lifting a load that’s 20% below the rated capacity of the clamp.
You also need to pay close attention to the max jaw capacity of the plate clamp. Jaw capacity should be as close as possible to the thickness of the material you’re lifting.
Lastly, you should not be lifting plates that have a surface that is harder than the teeth of the clamp. For plates that have an extremely hard surface or a surface that could be easily damaged, there are certain types of lifting clamps that have a non-marring jaw and no teeth.
How should you inspect the exterior of a clamp?
- Follow the clamp manufacturers’ maintenance recommendations.
- Inspect internal and external surfaces for forging or weld fractures, wear, and distortion.
- Check all pin holes for wear.
- Inspect the throat (clamp opening) width. At zero grip, the cam should be in full contact with the pad.
- Measure the width of the throat. If the measurement at the base, where the pad is located is greater than at the top, the body has been overloaded. Replace the clamp and tag the defective clamp and remove it from service.
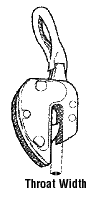
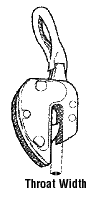
How should you inspect the internal parts of the clamp?
- Soak overnight in a degreasing solvent to remove all dirt and grease that prevent proper inspection of components. Degreasing solvents should be used inappropriately in well-ventilated areas. Handle the wet clamp parts while wearing gloves made of material that is chemically resistant to the solvent.
- Remove the body pins or bolts and slide out the complete internal mechanism.
- Check each body pin or bolt for wear or bending due to overloading.
- Check each spacer, rivet, bolt, or internal part for play or wear.
- Replace any worn, distorted, or defective part.
What should you know about the spring, cam, lock, and pads?
- The cam spring should be strong enough to hold the cam against the pad.
- The locking spring should give initial pressure at a near-zero grip without material in the clamp.
- There should be “definite tension” in the locked position.
- The spring should not be bent or distorted.
- The lock assembly should rotate freely without binding and must restfully on the stop pin.
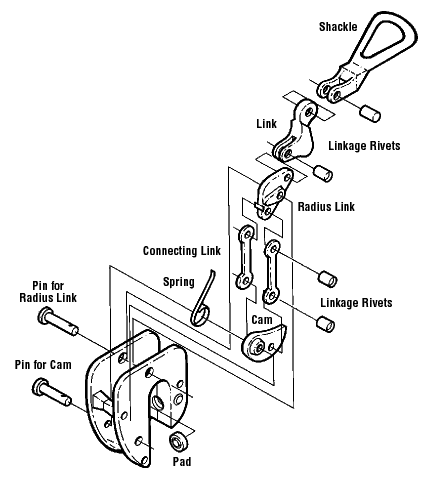
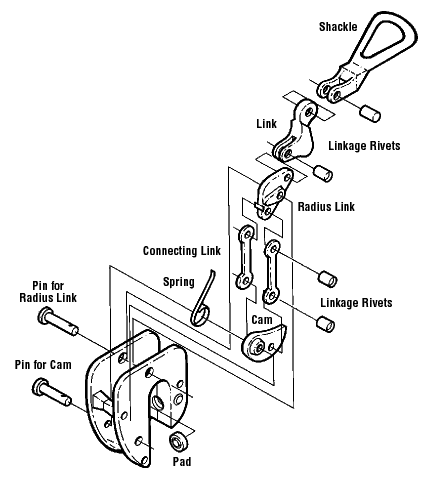
- Cams and pads are vital parts of a clamp and are exposed to wear. Use on one size plate thickness will cause wear only in one area of the cam working surface. Replacement is required sooner than when a cam is used to handle different plate thicknesses.
- Examine the cam surface. If the teeth are flattened by 50% or more, replace the cam and pad.
- Teeth must be sharp and free of foreign material.
- The shackle must not show signs of elongation or wear.
How should you use plate clamps safely?
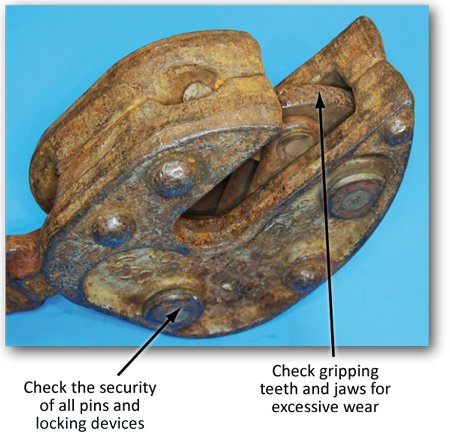
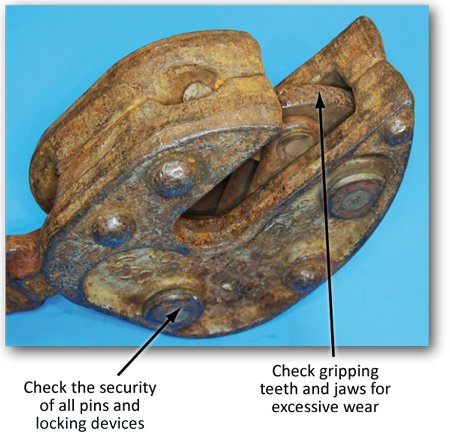
- Prior to lifting using a plate clamp, the user should determine if there is a safer way to accomplish the work. If it is deemed this is the safest and acceptable method, then before lifting review the specification sheet that’s supplied with the purchase of every plate clamp.
- It’s a good idea to laminate the specification sheets so they can withstand the elements in the field, and keep them where they will be readily available to users for review prior to plate clamp used.
- Inspect plate clamps before each use. The user needs to understand the manufacturer’s specifications on teeth, jaw, pin, and assembly wear and rejection criteria. This information is manufacturer-specific, so the user needs to be knowledgeable of each manufacturer’s specs. If a plate clamp appears excessively worn, mark it and remove it from the work area.
- There are three types of plate clamps designed for overhead lifting. Be sure to use the correct clamp for the job task:
- vertical lift only,
- horizontal — to and from vertical through a 90-degree plane, and
- horizontal — to and from vertical through a 180-degree plane.
- Plate clamps are not designed to lift plates that exceed 300 Brinell hardness.
- Plate clamps are designed to lift the thickness of the plate identified by the manufacturer’s identification plate located on the clamp. They must never be used to lift plates less than or greater than the thickness identified on the plate clamp identification tag.
- Plate clamps must only lift one plate at a time. (The exception to this rule is lifting a stack of plates horizontally with two or four clamps approved for this type of lifting.)
- Plate clamps must never be overloaded. Always calculate the plate weight and size your clamp appropriately.
- Plate clamps are vulnerable to “under-loading” when they lift less than 50% of the WLL of the clamp. An “under-loaded” plate clamp can allow a load to slip free.
- Always center the plate clamp directly above the plate’s center of gravity. A plate that hangs out of level puts undue side stress on jaw teeth allowing load slippage.
- If a tag line is to be used to control the load it must be fastened to the plate clamp prior to lifting.
- Keep loads low to the ground and stay out of the “fall area.” Remember that a steel plate may fall on its edge but then falls over to one side. Never place your body in the “fall-zone.”
- Be especially careful when lifting steel plates to any elevated area. The plate will act like a sail and the wind load can cause the plate to swing out of control resulting in loss of the load. In these cases, the “fall-zone” must be expanded.
- Specific plate clamps are designed to lift finished and polished plates with non-marring smooth gripping surfaces. These should be used in pairs supported by slings and a spreader beam.
- Just like any other lift, avoid shock-loading when using plate clamps.
- Lift one plate at a time unless using clamps and methods approved otherwise.
- Use two or more clamps to balance a long or flexible load.
- Install the clamp (or clamps) over the center of gravity of the plate.
- When using a vertical type of plate clamp, use a locking device to prevent accidental loosening.
- Use horizontal types of plate clamps in pairs.
- Use clamps within their rated capacity and flange width.
- Lock a clamp closed before lifting a load.
- Use a sling between the clamp and the crane or hoist hook.
- Use non-marring (rubber pad) clamps in pairs when lifting finished and polished plates.
- Lift smoothly; avoid jolts.
- If the use of a tag line is necessary, attach it to the clamp before lifting the plate.
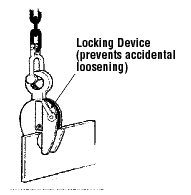
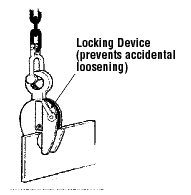
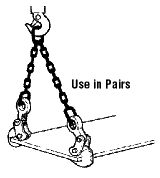
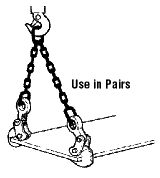
Safety Tips for Vertical Plate Lifting Clamps
Vertical plate lifting clamps can lift and turn over flat plates 180 degrees and can be used to transport plates in a vertical position.
Vertical lifting clamps should never be sideloaded and you should never try to lift more than one plate at a time. If you’re lifting a long plate, you should consider using two clamps connected to a spreader bar to minimize swing and maximize lifting safety. Also, keep in mind that plates that are hot in temperature can damage the structural integrity of the plate clamp. Columbus McKinnon recommends that you do not lift plates that are 250 degrees or higher.
Safety Tips for Horizontal Plate Lifting Clamps
Just as their name suggests, horizontal lifting clamps are used to lift horizontal objects. If you are lifting along the plate horizontally, never use a quad sling. This will cause the horizontal clamps to turn and potentially slip off. Instead, use a spreader bar with double-leg slings that connect to the plate clamp. When it comes to lifting short plates horizontally, one double sling with horizontal plate clamps on each end will suffice. To maintain proper lifting strength and control, always ensure there is a minimum included angle of at least 90 degrees. Never use vertical plate clamps for a horizontal lift.
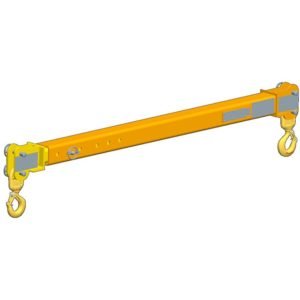
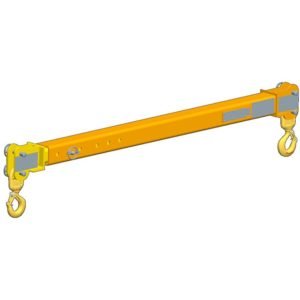
What should you avoid when using plate clamps?
- Do not lift over workers.
- Do not stand near a load.
- Position yourself away from and fully clear of the load. Remember to also consider how the load might fall when it lands.
- Do not overload or underload a clamp.
- Do not lift from the side with a vertical clamp.
- Do not lift more than one plate at a time with a vertical clamp.
- Do not lift the plate from the bottom of a plate stack.
- Do not drag the load using the plate clamp.
- Do not grind, weld, or modify a clamp.
- Do not use a clamp having a minimum jaw opening larger than the thickness of the load.
- Do not leave suspended loads unattended.
Download the Infographic
More Safety Moments
- 15 Home Insurance Safety Tips to Lower Premiums
- 66 Safety Tips at work-Safety Moment#17
- Abrasive blasting: Know the hazards -Safety Moment #7
- Annual inspection and certification requirements for mobile cranes and boom trucks-Safety Moment#18
- Arc Flash Protection -Safety Moment #3
- Cleaning chemicals Tips: Know the risks -Safety Moment #9
- Common Causes of the workplace incident: Safety Moment#32
- Cranes Stability and Tipping: Safety Moment#29
- Don’t ignore shoulder pain-Safety Moment #11
- Electrical Safety Tips -Safety Moment #6
- Electrical Safety While Working From Home: Safety Moment#30
- Explain chemical Data Sheets For Non-Technical People-Safety Moment #10
- Exposure Limit Terms -Safety Moment#21
- Falls from heights :Video-Safety Moment #14
- Flammable Liquid Storage -Safety Moment #1
- Gasoline Safety Tips
- Hidden Hazards:25 steps to a safer office -Safety Moment #15
- How to use Plate Clamps Safely: Safety Moment#34
- Keeping Warehouse Personnel Safe 6 Key Tips -Safety Moment#20
- Know how to handle a hammer -Safety Moment #4
- Machinery Guarding: Safety Moment#31
- Oil & extraction: hazards, controls & resources -Safety Moment#22
- Photo of the day: 10 Scaffold Safety Essentials
- Photo of the day: Flood Safety Tips
- Photo of the day: Incident Investigations
- Practice caution when handling fuel-Safety Moment #13
- Quick Tips for Avoiding Pinch Point Injuries: Safety Moment#27
- Risk of Explosion during Removal of Split Rim/Multi Piece Wheels from Vehicles-Safety Moment #8
- Safety Net Regulations: Safety Moment#28
- Scaffolding Safety Tips
- The Golden safety rules :Video-Safety Moment #12
- Tick’s Threats when working outdoors -Safety Moment #16
- Tips to Avoid Standstill Accidents: Safety Moment#33
- Tips to prevent heat illness -Safety Moment #5
- Understanding RF radiation-Safety Moment#19
- Vehicle Backing Safety Facts
- Video: Aerial Work Platform Safety: Safety Moment#35
- Video: Avoiding line of Fire: Safety Moment#36
- Video: Electrical Safety Awareness -Safety Moment#23
- Video: Isocyanates Exposure -Safety Moment#24
- Video: Winter’s Hidden Hazard -Safety Moment#25
- Video: Working safely Near powerlines -Safety Moment#26
- Working safely with cement -Safety Moment #2
1 thought on “How to use Plate Clamps Safely: Safety Moment#34”