Photo of the day:5-Signs your Near-Miss Reporting is failing
It’s easy to discount the importance of near-miss incidents since they don’t result in any real injury or property damage. However, the near-miss is a dress rehearsal for the real thing and a free shot at fixing problems with your safety program before they do real harm. That’s why forward-thinking companies have implemented near-miss programs to take advantage of these opportunities. New research has emerged shedding light on how to manage near misses effectively.
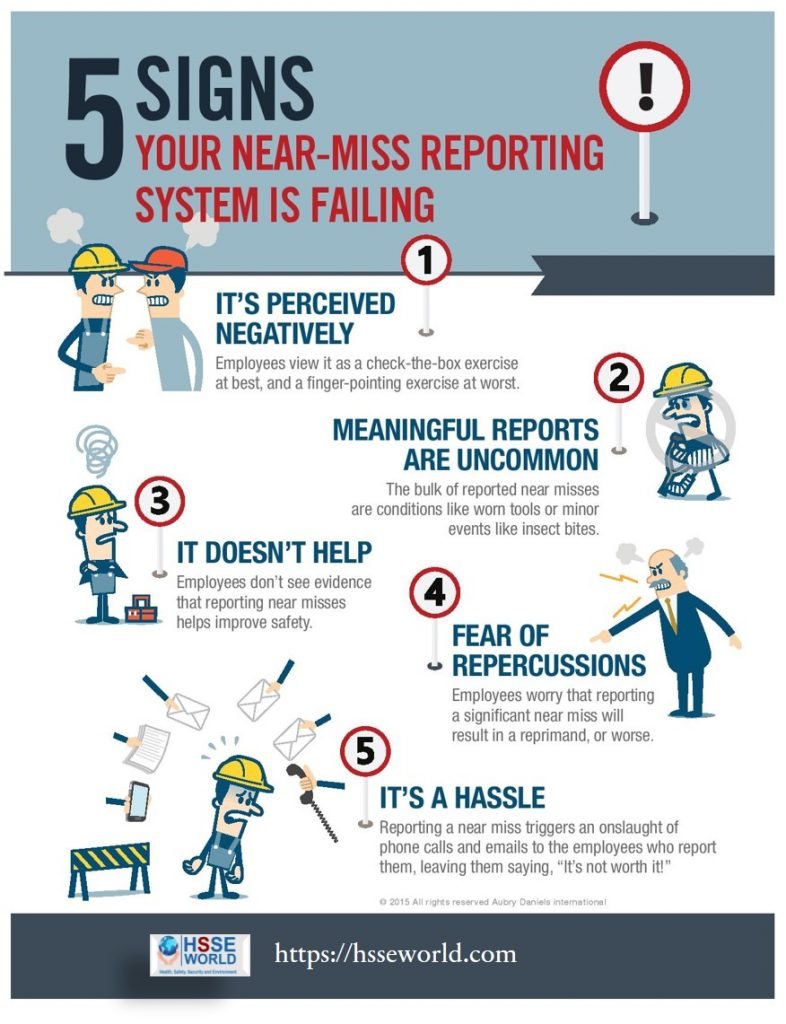
Why Near Misses Are So Important
It’s been recognized that focusing on minor incidents, including near misses provides the wherewithal to reduce the probability of major incidents. Near misses are at the base of the safety pyramid and occur much more frequently than serious incidents at the top. They’re also smaller in scale, simpler to analyze, and easier to resolve.
Working from the top down, major incidents can often be traced back to a number of minor ones that happened earlier. By addressing the causes of these “precursor events,” you can prevent the major events from ever occurring.
Example: Several rows of shelving collapse in a storeroom. No one is hurt and only minor property damage is done. The investigation reveals that the shelves collapsed because they were overloaded. Once you know this, you can revise your stocking restrictions, ensure that shelves are safely loaded, and prevent any more shelves from collapsing due to overloading.
OSHA Doesn’t Require Near Miss Reporting
One of the biggest challenges of a near-miss program is that near-miss incidents frequently go unreported. One reason for that is that while OSHA recommends near-miss reporting and investigation as best practices, it doesn’t expressly require it. For example, near-miss reporting is an element of OSHA’s proposed Federal Injury and Illness Prevention Program (I2P2), and California’s current (IIPP) initiatives, but not part of the current recordkeeping requirements.
In some ways, OSHA actually discourages near miss reporting by using reports of near-miss incidents as evidence of an employer’s knowledge of a particular problem. Thus, having a near incident report about a hazard in your files increases your risk of being cited for the hazard. Of course, the idea is that incidents wouldn’t happen at all if they were preceded by near-misses revealing correctable flaws.
The 8 Steps
Although it’s not a regulatory requirement, near-miss reporting, investigation, and correction have become common practice. Just as with other safety activities, years of practice have provided insight on near-miss management. One great source of such insight is recent research from Wharton Business School. After conducting over 100 interviews of employees at all levels of various Fortune 500 companies, Wharton researchers identified 8 hallmarks of an effective near-miss program:
1- Near Miss Is Defined Broadly
The first thing researchers noticed is that at companies that manage them effectively, the term “near miss” is broadly defined to include, not just events, but unsafe conditions and unsafe behaviors as well. Event triggers were also broad, typically including:
- Minor incidents/injuries that had the potential to be more serious
- Events where injury could have occurred but didn’t
- Events where property damage resulted or could have resulted but didn’t Events where a safety barrier was challenged, such as by a worker bypassing a machine guard regardless of whether it actually caused a potential injury or damage event
- Events where potential environmental damage could result
The definition recommended by the researchers to maximize a near-miss program effectively is: “A near miss is an opportunity to improve health and safety in a workplace based on a condition or an incident with potential for more serious consequences.”
2- Clear and Simple Reporting Procedures Exist
You can’t manage near misses and learn from them unless you know they’re occurring. So, once a near miss is identified, it should be reported, preferably in writing, by either the person who identified the near miss or by a supervisor to whom a near miss was reported verbally by someone else. The researchers recommend having a clear and simple procedure for reporting near misses to encourage this process and increase the probability of reporting them.
The OSHA laws, either directly or implicitly, require workers to report near misses. (The chart below notes the language in each jurisdiction’s OSHA act that contains or suggests this requirement). However, workers may still be reluctant to report near misses. They may be afraid of being disciplined if the near miss involved a violation of your safety rules and/or procedures, or they may not believe management will actually do anything to improve safety if they report a near miss. So, they stay quiet about their close calls.
To overcome workers’ reluctance to report near misses, train them on the value of near misses and their role in properly managing these events. This type of training should cover the following:
- What near misses are and how to identify them
- Why near misses are important
- The role of each person involved in near-miss reporting
- What a near miss program is, and how it works, which includes the responsibilities of all management levels
- How to report a near miss
- How to prioritize a near miss
You can also encourage near miss reporting by providing incentives or by telling workers that they’ll be disciplined for not reporting near misses. Taking swift action in response to a reported near-miss can also encourage reporting because it demonstrates to workers that management is actually listening to them and taking safety seriously.
The researchers don’t recommend allowing anonymous near-miss reporting for two reasons.
First, it’s often necessary to follow-up with the person who reported the event to determine its root cause. Second, anonymous reporting suggests that near misses are unfavorable and undesirable events.
3- Near Miss, Incidents Are Prioritized
Once near misses are reported, you need to prioritize them to determine:
- What steps to take next
- How much attention to give the incident
- How deeply to analyze its causes
- The resources available to implement solutions
- How, if at all, you’ll disseminate information about the incident throughout the company
4- Relevant Information Is Distributed
Companies that manage near misses effectively do a good job of distributing appropriate information about the incident by:
- Transferring the information quickly
- Routing the information to all appropriate people
- Communicating the information in a useful and understandable format
5- Causes Are Determined
Near miss, management requires identification of direct and root causes of incidents, which differs from root cause analysis of actual injury or damage incidents. Often times, investigative teams are formed when the causes of incidents aren’t readily apparent.
6- Solutions Are Determined
The next hallmark of an effective near-miss program is to determine one or more solutions to identified causes. Of course, hazard elimination is always the preferred solution, but the system must provide for hazard management or control where total elimination isn’t feasible.
The hierarchy:
- Elimination of the cause of the hazard
- Reduction of the potential hazard level or degree of risk of exposure to it
- Installation of safety devices
- Installation of warning signs to alert people to the hazard
- Implementation of new safe work procedures to account for the hazard
- Increased worker awareness of the hazard, such as through safety talks
7-Solutions Get Implemented
Once they identify the necessary solutions, companies implement them and inform anyone affected by the particular near miss, such as workers and supervisors who work with the equipment involved or in that area of the workplace. If the solution includes new or revised safety procedures, make sure to train all workers who will be using these procedures.
8- Solutions Are Monitored
The final phase of a near-miss program is monitoring the changes made to ensure that they effectively address the cause of the near-miss incident. In addition, remedying one problem can sometimes create other unforeseen hazards, particularly for subtle changes. Thus, managing these changes and ensuring no new hazards are created is critical to the success of a near-miss program. And make sure that the person who reported the near-miss is aware of the outcome of this process.
Bottom Line
Near misses are a largely untapped safety improvement resource, as stated by the Wharton researchers. An effective near-miss program can help you tap the potential of this valuable source of safety information and use it to improve your workplace’s overall safety program.
This is clearly one way a compliant business can effectively raise the bar on safety and loss prevention.
Download the photo
More photos:
- Photo of the day: Identify the Hazards
- Photo of the day: Hand safety Facts
- Photo of the day: What are the hazards
- Photo of the day: Outline Safety observations
- Photo of the day: Safety Leader
- Photo of the day: Unsafe Conditions
- Photo of the day: Why is PPE important?
- Photo of the day: DO’S and DON’TS of Working At Heights
- Photo of the day: 5 Tips to keep your Crew Healthy and safe at work
- Photo of the day: Tracking Near Miss Incidents
- Photo of the day: 10 Elements of Successful Behavior-Based Safety Program
- Photo of the day:5-Signs your Near-Miss Reporting is failing
- Photo of the day:7 Ineffective Safety Practices (And What To Do Instead)
- Photo of the day:5 keys for effective Self-Management in lone worker safety
- Photo of the day: FrontLine supervisors are the LINCHPINS of safety
- Photo of the day: Fostering Engagement at the front line
- Photo of the day: workplace Hazards
- Photo of the day: What is the line of fire
- Photo of the day: How to Avoid the Fatal Four
- Photo of the day: Fire Safety checklist for workplace
- Photo of the day: Most common safety incidents in the workplace
- Photo of the day: Fire Emergency
- Photo of the day: Ladder Safety Tips
- Photo of the day: 8 Basic steps to wear a safety harness
- Photo of the day: You can prevent workplace Falls
- Photo of the day: Top10 Injuries in office work
- Photo of the day: Overhead powerline safety
- Photo of the day: Eyes on the Road The challenges of safe driving
- Photo of the day: 5 Ways to Reinforce Commuting With Positive Reinforcement
- Photo of the day: Safe Lifting at work
- Photo of the day: 5 Essential outcomes of an effective leadership survey process
- Photo of the day: Conveyors Safety Tips
- Photo of the day: Confined Space rescue
- Photo of the day: Construction Site fire Safety
- Photo of the day: Chemical Spill Emergency Response
- Photo of the day: Electric shock survival
- Breath Safely: The Proper Use of Respiratory Protection
- Photo of the day: Confined space safety Precautions
- Photo of the day: Choosing the Right Face Mask and the difference between a respirator and face mask
- Photo of the day: Importance of Mock drill and Fire Action Emergency Procedure
- H2S Gas and how to handle its Emergency
- Your steps to chemical safety
- Photo of the day: hierarchy of controls
- Photo of the day: Tips to reduce Heat stress in the workplace
- Photo of the day: Safety Equipment for Confined Spaces
- Photo of the day: Dangerous Goods Classes
- Photo of the day: Trenching Safety Tips That Can Save a Life
- Photo of the day: Mental health in the workplace
- Photo of the day: Emergency preparedness in the workplace
- Photo of the day: musculoskeletal disorders
- Photo of the day: Workplace Inspection
- Photo of the day: New worker Orientation & Safety Orientation checklist
- Photo of the day: Effective Health and Safety Committees
- Photo of the day: 10 Scaffold Safety Essentials
- Photo of the day: Incident Investigations
- Photo of the day: Preventing the spread of contagious illness
- Photo of the day: 5 ways to reduce the risk of Slipping and Tripping
- Photo of the day: Sitting at work
- How to use Plate Clamps Safely: Safety Moment#34
- Photo of the day: working in heat and Humidex Rating
- Photo of the day: Don’t be Driven to Distraction
- Photo of the day: Fatigue at Work
- Photo of the day: Noise in the affected workplace
- Photo of the day: Indoor Air Quality
- Photo of the day: WHMIS 2015 – Pictograms
- Photo of the day: Personal Protective Equipment last resort
- Photo of the day: Manual Material handling
- Photo of the day: Controlling COVID-19 in the Workplace-Physical Barriers
- Photo of the day: Generator Safety
- Photo of the day: Position for safety and comfort-Safety Tips
- Photo of the day: Cannabis and Impairment in the Workplace
- Photo of the day: sun safety in the workplace
- Photo of the day: Top FIVE Heavy Equipment Construction Site Safety Tips
- Photo of the day: Work-Related Asthma
- Photo of the day: choosing the right Anchorage
- Photo of the day: Protect your Head
- Photo of the day: Extension Cord Safety Tips
- Photo of the day: Concrete Truck Driver Hand Signals
- Photo of the day: Safe use of ladders and step ladders
- Photo of the day: Arc-Fault Circuit Interrupters (AFCI)
- Photo of the day: HSE Bulletin Board
- Photo of the day: Scissor Lift Safety
- Photo of the day: Managing Risks of Exposure to Solvents in the workplace
- Photo of the day: Flagman and Traffic control
- Photo of the day: Run Project safely with Crane Hand Signals
- Photo of the day: Read All Labels Work safe
- Photo of the day: Flood Safety Tips
- Photo of the day: Fall Protection Plans
- Photo of the day: Lockout and Tagout Safety
- Photo of the day: Types of Hand Protection
- Photo of the day: Types of Foot Protection
- Photo of the day: Floor Marking
- Photo of the day: Overhead Power lines Clearance