Q& A: Which is better Cast Iron or concrete counterweight in the tower crane? and What is the purpose of a counterweight?
9 min readHow Do the Counterweights in Tower Cranes Work? Did you ever think about this question? We mostly take for granted how these often-massive devices form our surroundings. It’s difficult to understand how the crane does what it does without falling over from a distance or the deck. It’s difficult to imagine how anything so significant might be built without anything equally large next to it to aid in the process. Cranes combine sheer height with the ability to carry heavy materials easily up to several floors. Without cranes, this job becomes challenging and time-consuming, so cranes help speed up the building process while still making it much simpler.so our question now is which is better cast iron or concrete counterweight in the tower crane? and what is the purpose of a counterweight? let’s know firstly the parts of the Crane and how the Tower crane is installed.
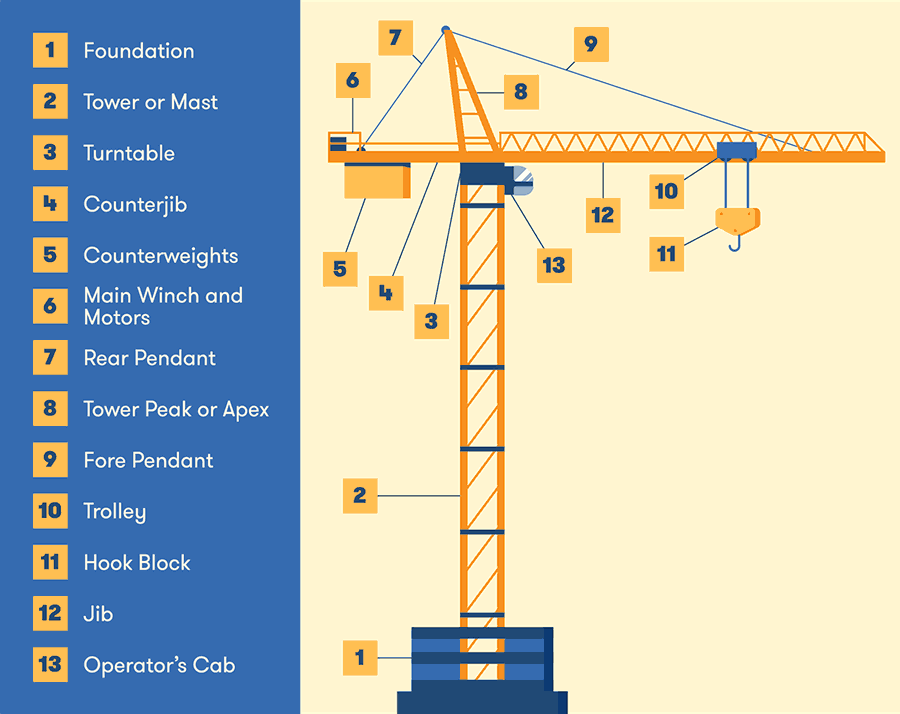
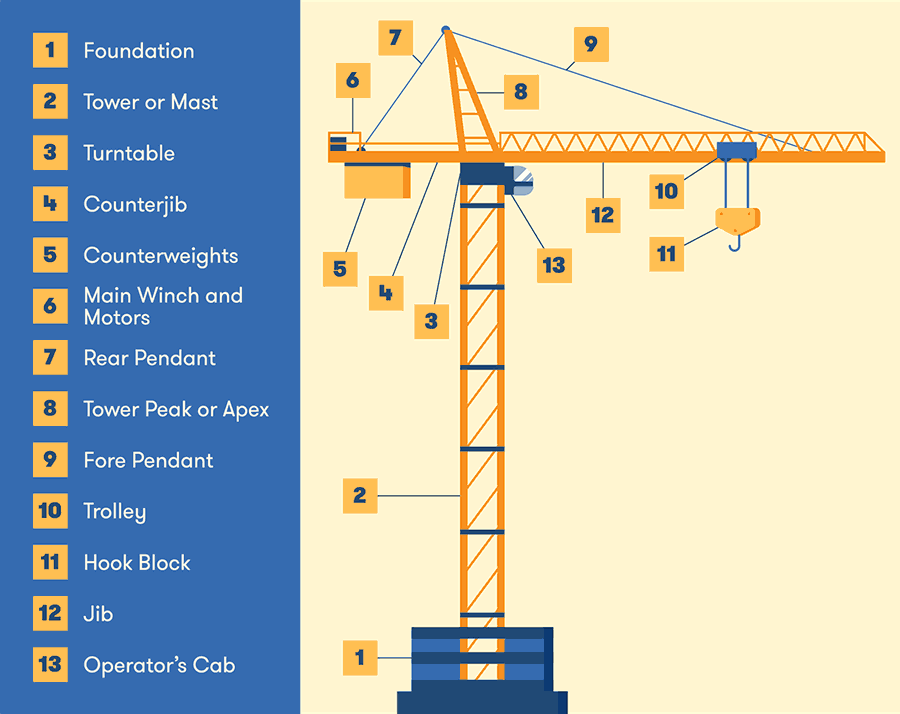
Parts of a Crane
To understand a crane’s movement, it’s helpful to have a good grasp of the various parts that make up a construction crane. All these parts work together to make the incredible lifting power of a crane possible
When looking at a crane, you can identify all the parts easily by starting at the base of the crane and working your way up, then running your eyes along the length of the crane from the long end to the short end.
- Concrete foundation: A tower crane always sits on a concrete foundation, where anchors are placed to secure the crane to the ground.
- Tower or mast: From its base, the crane rises up with the tower, also called the mast, which consists of lattice sections stacked on top of one another.
- Turntable: At the top of the tower, the crane has a turntable that enables it to rotate 360 degrees.
- Operator’s cab: Near the turntable, the operator’s cab gives the crane operator a place to control the crane with an unobstructed view.
- Jib: Stretching out forward from the cab is the jib, the long horizontal section of a crane.
- Trolley and hook block: Along the jib, a trolley with a hook block runs back and forth, enabling loads to be moved along the length of the crane.
- Counterjib and counterweights: Behind the cab is the counterjib, where counterweights are placed to stabilize the crane at rest and during movement.
- Main winch and motors: At the back of the counterjib sits the main winch and motors, which enables the long rope to be lowered or raised to hoist heavy loads.
- Tower peak or apex: Rising above the cab is the tower peak, also known as the apex, where the pendants extend out to support the jib and counterjib.
Remember that there are many varieties of tower cranes, and some will have parts that are not mentioned here. For example, a luffing jib crane has an arm that is able to raise up and down, and a flat top crane does not have the apex and pendant system shown in the crane above.
(Learn more about Mobile Cranes: Basic Terms You Should Know )
How is a tower crane installation done?
Before a tower crane can be assembled, foundations must be dug for it, and the crane’s bottom portion must be fixed to steel rods in the foundations. After the concrete has hardened, the crane can be assembled section by section. The tower crane parts are held in place by a mobile crane, which is fixed with a hydraulic wrench. The turntable, where the cabin sits, is the heaviest component of the crane, and once it is in place, the articulated arm, also known as the jib, can be wrenched on.
Ropes and a trolley system are added to the jib for the tower crane to work, and it is wired up to the control pad in the cabin. To offset the weight that the crane will be raising, a counterweight is attached to the opposite end of the articulated jib. Many cranes have an adjustable counterweight depending on how much weight is being raised, but the weight is usually secured just short of the jib’s end. The crane may also be braced to the side of buildings to hold it upright, although this is only possible if the building being operated on is already at a significant height.
What are counterweights in the tower crane?
When lifting or lowering loads, counterweights provide additional support. Counterweights must have the right mass and be at the right distance from the pivot point to function as effectively as possible. This is known as the moment of physics, and it is the counterweight’s mass multiplied by its distance from the pivot. The counterweight moment must be equal to the moment of the load for the most effective operation. This is critical because if one side’s moment is greater than the other’s, the dominant side will tip over.
What is the purpose of a counterweight in tower cranes installation?
When it comes to cranes, counterweights are also crucial for job protection in the construction zone. A crane counterweight aims to keep the crane from tipping over. The counterweight is used to balance the weight of the object being lifted. Most of the time, these weights support cranes hoist heavy loads or dig into the ground. Although counterweights do not move very quickly, it is essential to be cautious when working with them. If you’re walking by the counterweight, make sure the crane operator knows you are there, so you don’t get stuck between the counterweight and any stationary objects nearby. Between the two points, you might be pinched and seriously wounded, if not killed. The counterweight is crucially significant. If it isn’t built correctly and isn’t the right size and shape, it becomes a complicated topic that can cause the vehicle to tip over in the load’s direction or backward. If the counterweight set up is too light for the load and booms the configuration, a crane will fall over in the load’s direction while attempting to lift it. Otherwise, a crane’s counterweight will tip it backward in the following situations:
- For the boom setup, the counterweight is too high.
- The crane is travelling up a slope.
- Insufficient timbers are mounted under the outrigger pads below the counterweight while the crane is on soft land.
- Outriggers or any other ground support cannot withstand the combined weights and tipping forces because they are not extended or lowered into place.
- If the boom configuration is raised too high and not enough weight is added to it.
Calculating the correct counterweight helps in avoiding mishaps at the crane site
The most common cause of toppling over is a mathematical error. As a result, it is critical to determine the correct weight and size before the manufacturing process during the design phase. This is the only way to ensure the crane counterweight’s safe operation. When designing the part, use the following mathematical formula to reduce potential risks and provide an efficient counterbalance:
P =V x μ x g
P is the requisite counterweight’s weight; V is its volume; –μ is the density of the material used to make the counterweight, and g is the gravitational constant (9.81).
Advantages of cast iron counterweights compared to concrete ones:
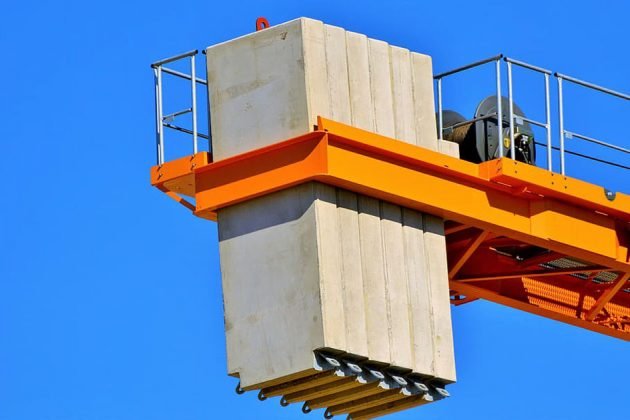
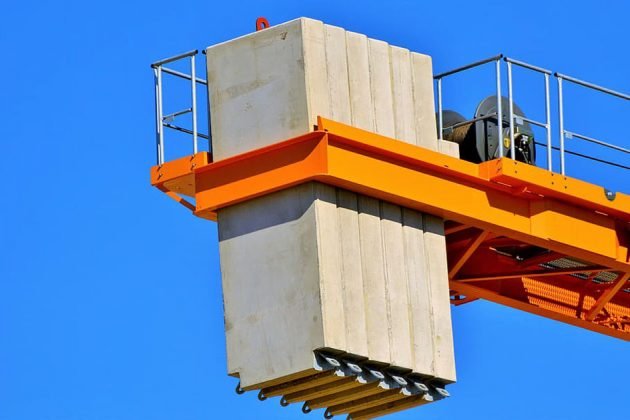
Density
Cast iron is denser than most materials, thus cast metals for counterweights have on average three times more density than pure concrete. This enables iron to achieve the target weight in less space and volume compared to concrete which eliminates the cost of additional material.
Product Cost
Concrete density can be improved by adding dense aggregates such as limonite, hematite, magnetite, or metal bits and scraps into the concrete mix. This increases the concrete’s cost substantially, but its density is still less than those of the iron. Â
Fragility
Cast iron is indeed stronger and harder than concrete which automatically makes counterweights more resistant to impact and strains and guarantees longer fatigue life against cyclic stress. Usually, counterweights need screws for fastening or mounting additional equipment. The concrete’s surface cracks easily and hardly supports any additional constructions.
Shaping
In usages where counterweights need to fit into specific shapes, for example, tractor suitcase counterweights are differently shaped according to space on the rear axle of tractors; concrete turns to be more expensive to carve out the desired shape into it. Cracking is less likely to occur when creating a finer shape on cast iron.
Environmental Impact
Cast iron is a product of recycling and doesn’t require any extraction of new raw materials, which is not the case with concrete.
Conclusion:
Counterweights are an integral part of a variety of big machines dealing with huge loads. By balancing the weight, they secure a safety performance of tractors, forklift trucks, cranes, excavators, and others. The manufacturers prefer using either full cast iron, full concrete, or a mix of concrete and metal bits. For example, forklift counterweights are commonly made of metals for maximum space utilization. But some industries such as agriculture (tractors) or off-highway (excavators and cranes) have counterweight needs that can be fulfilled by both – metal and concrete. Although concrete is cheaper than iron, it’s wiser to choose iron, since concrete applications are prone to many problems, that cast iron counterweights can overcome. ( learn more E-Books: Handbook of Rigging Lifting, Hoisting, and Scaffolding for Construction and Industrial Operations )