Simultaneous Operation (SIMOPS) checklist
6 min readThe purpose of any Simultaneous Operations (SIMOPS) Procedure is to provide all personnel from the construction and commissioning groups who are involved with simultaneous operations on the projects with a sound knowledge of the relevant safe work practices and procedures applicable to simultaneous operations.
These Procedures shall also be used to determine the compatibility, interference, and limitations raised during the planning and operational stages of any simultaneous operation.

The activities covered by procedures shall not be limited to the following
- The remaining construction activities (i.e. lifting and rigging, confined space, naked flame, and hot works, etc.)
- The commissioning activities.
- Production activities after partial handover to production.
- Assuring compliance with Permit to Work Procedure.
Should it be deemed necessary, specific operations must be reviewed on a case-by-case basis with a risk assessment such as a job safety analysis being developed as the need arises.
Additionally, the requirements of the SIMOPS Procedure shall ensure that any activity or works in any given area, where joint activities may be ongoing simultaneously, are reviewed and analyzed for potential interference or limitation. The requirements of these Procedures are;
- Establish a mechanism for the review of proposed activities (e.g. meetings, toolbox talks, etc.) to identify department and subcontractor participation.
- Establish a matrix of responsible persons who shall authorize such simultaneous activities.
- Ensure simultaneous activities are controlled and performed in a safe manner by; a) Defining the responsibilities of all personnel involved in the tasks.
- Appointing a Simultaneous Operations Leader (SOL) to coordinate the activities between the different organizations.
- Identifying any preventive safety measures, which shall be implemented prior to commencement of the simultaneous activities
- Limiting the number of simultaneous activities in any given area.
- Avoiding interference during Production Operations after Early Production.
- Establishing communication channels.
- Providing training of all personnel involved in the tasks.
To minimize the potential for personnel injury and equipment damage by:
- Controlling and restricting personnel access to areas where simultaneous activities may be taking place.
- Providing specific instruction for securing (making safe) operations and mustering personnel in case of emergency.
- Ensuring that all personnel involved in the simultaneous tasks are aware of the specifics of simultaneous operations and emergency procedures.
- Identifying hazards and evaluating the consequence of failures.
The SIMOPS Procedures shall further ensure that nothing is done, during the performance of these tasks, to prejudice the safety of personnel or the Plant.
The work activities covered by the SIMOPS Procedure shall include but not be limited to the following;
- Any works significant in nature such as large construction jobs, change-out of major rotating equipment, naked flame and hot works in restricted areas, blasting and painting works, radiography, entry into confined space, rigging and lifting works over live equipment or plant, etc. and which occur in the areas under commissioning control
- Any works that pose a significant hazard such as working in areas where there is a risk of hydrogen sulphide gas (H2S), activities where special chemicals are utilized, work in which multiple subcontractors are involved,
The above examples are not inclusive and other work activities may also be covered under the SIMOPS Procedure.
SCOPE
The requirements of the Simultaneous Operations Procedure (SIMOPS) shall be applied to all construction, commissioning, and production activities to highlight and mitigate any potential restrictions and/or safety impact when planning SIMOPS work activities due to take place at the same time and in the same/vicinity location.
As a minimum, the Procedure shall be distributed to the personnel referenced in the list below.
Minimum distribution List
- Site Manager
- General Construction Manager
- Area Construction Managers
- Commissioning Manager
- Installation Commissioning Authorities.
- Area Commissioning Authorities.
- HSE Manager
- Area HSE Managers
- Simultaneous Operations Leader
- Production Superintendent
- Fire and Rescue Chief
- Subcontractor Site Representatives
Organization for SIMOPS
All Site personnel, without exception, have an individual responsibility to ensure that any SIMOPS activities are carried out correctly and efficiently. The named positions in column 1 of the following Table have further specific and clearly defined responsibilities.
Not all of the named positions are Project Job Titles but are functional titles for the purpose of this SIMOPS Procedure. Each of the positions and their associated responsibilities shall be described individually in the sub-section of the SIMOPS procedure.
The blow table is arranged to show the correspondence between the POGC Functional Titles (as defined in this SIMPOPS Procedure) and the duties associated with those functions.
Procedure Definition | Duties | Responsible Person |
---|---|---|
Site Manager | Has overall responsibility for SIMOPS. | Site Manager |
General Construction Manager | Coordinates construction activities are related to SIMOPS. | General Construction Manager |
SIMOPS Leader (S.O.L.) | Coordinates all SIMOPS activities between the various departments. Authorises planned work to go-ahead. | Assistant Commissioning Manager |
Commissioning Manager | Coordinates all Commissioning activities relating to SIMOPS. | Commissioning Manager |
Installation Authority | Defines plant status for work. Authorizes commissioning work to go-ahead. | Area Commissioning Manager |
Area Authority | Arranges any required isolations. Authorizes work permit. Monitors working practices. | Commissioning Shift Supervisor |
Permit Controller | Arranges for permit approval. Checks permit before issue. Closes permit upon completion of the SIMOPS task. | Permit Controller |
Safety Authority | Defines safety requirements. Provides Risk Assessment. Monitors working practices. | Area HSE Manager/SI |
Task Supervisor | Initiates permits. Defines the scope of work. Ensures that all persons working under his control conform to PTW conditions. Ensures the task is completed to schedule. | The person responsible for the work |
Table 1: SIMOPS Procedure Definitions and Duties
Check-lists
The preparation of the SIMOPS activities as far as organization, equipment, material, and procedures are concerned, shall be shared between construction and commissioning organizations. To assist these organizations in preparing for predetermined start-up phases, the following checklist will be used prior to each step of the works and responsibilities allocated to the disciplines and supervisors in charge. See and download the checklist of the SIMOPS below.
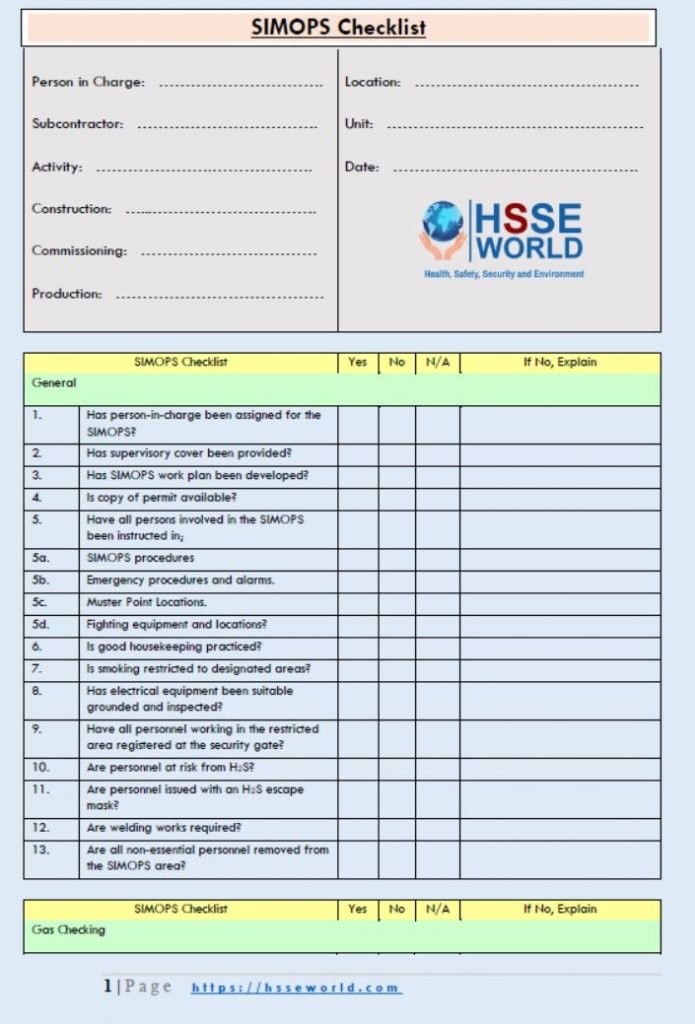
Download The checklist
SIMOPS checkilist could be used as a guideline during the Preparation of SIMOPS Procedure and it’s Implementation.the checklist are editable and could be modified to fit your purpose
Download SIMOPS checklist
Download PDF Checklist
More Forms
- Downloadable Kitchen Safety Inspection Checklist for Restaurants
- Mastering LOTO: Protecting Workers with Energy Isolation and Isolation Confirmation Certificates
- Flammable and Combustible Storage Checklist Free Download
- Secure Your Lifts:Guidelines for Safe Lifting Operations Free Planning Tool
- Sample of Accident Prevention Program ( APP) Template for General Industry Free Download
- Free ISO 14001:2015 Environmental Management System Audit Checklist Download
- Guides for Walking and Working Surfaces Safety Program
- Workshop Safety Guideline and free Posters
- Free Ergonomics Checklist for General Industry
- Work Area Safety Checklist
- Machine Safety and 43-Equipment Inspection Checklists
- Scaffold Safety self Audit and checklist
- Hot Work Controls and its Permit to work Form
- Safety Observation Report Template
- Forklift Operator’s Daily Checklist and safety Tips
- Inspecting Fall Protection Equipment Forms
- Templates: HSE Incentives and rewards
- 35 Inspection forms for Rig Check
- Chemical Risk Assessment form
- 22-Safety Inspection Checklists
- Safety Task Assessment Form
- Suspended Scaffold Pre-Operation Inspection Checklist
- Photo of the day: New worker Orientation & Safety Orientation checklist
- Grating-Decking-Floor- handrail-Removal Form
- Electrical Inspection Checklists
- E-Books: Fire Safety Logbook templates
- General Safety Guidelines and Employee Acknowledgment form
- Annual Internal Audit Form
- Mobile Scaffold Inspection checklist
- Simultaneous Operation (SIMOPS) checklist
- Temporary Construction Facilities (TCF) Inspection checklist
- HIRA, HSE Hazards & Effects Management Process (HEMP) & Risk Register Template
- Hazard Identification Plan (HIP) Template
- Ladder Inspection Form
- Free Pre-Startup Safety Review Checklist (PSSR)
- Hazard Identification Checklist
- Workplace Housekeeping Checklist
- ISO 45001:2018 READINESS CHECKLIST
- Lifting Plan Audit Checklist
- Job Safety Analysis (JSA) Forms What’s Right and Wrong?
- Electrical Isolation Permit to Work forms and checklist
- Canteen Inspection Checklist
- Work at Height Checklist
- Health Safety at Work Improvement Action Plan
- Fire Pump Daily Inspection Checklist
- Construction Site Traffic Management Plan (CSTMP) Guidance
- Safety Templates: COVID-19 Safety Plan
- Workplace Safety Inspections Forms
- Lock Removal Form
- Templates: Management of Change NEW Modified Equipment Safety Checklist
- Lifeline & Harness Inspection Guide checklist
- Contractor Pre-qualification Questionnaire Checklist
- Fall safety at construction checklist
- Construction safety Inspection checklist
- Equipment Safe Operating Procedures- SOP 61 checklist
- Permit to Work (PTW ) AUDIT CHECKLIST
- Hygiene and Sanitation Inspection Checklist