22-Safety Inspection Checklists
5 min readSELF-INSPECTION. The most widely accepted way to identify hazards in the workplace is to conduct safety and health self-inspections. You can only be certain that actual situations exist in the workplace if you check them from time to time.
Begin a program of self-inspection in your workplace. Self-inspection is necessary if you are to know where probable hazards exist and whether they are under control.
This Article contains twenty-two safety inspection checklists designed to help you evaluate your work areas. They will give you some indication of where you should begin action to make your workplace safer and more healthful for your employees.
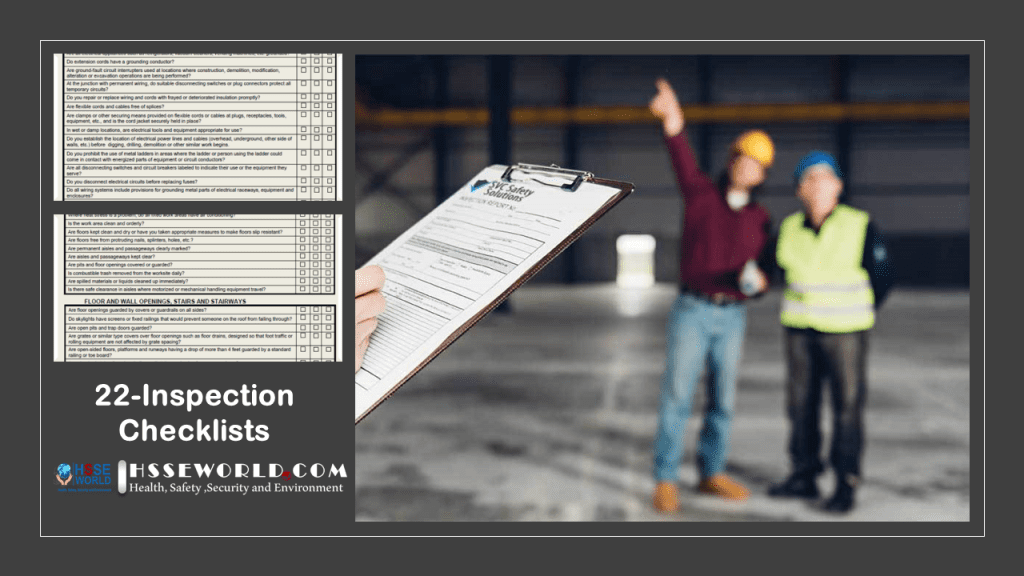
These checklists are not all-inclusive. You may wish to add to them or delete portions that do not apply to your workplace. Carefully consider each item as you come to it and then make your decision. Do not spend time with items that have no application to your workplace. Make sure you check each item on the list and leave nothing to memory or chance. Write down what you see (or do not see) and what you think should be done about it. YOU MUST COMPLY WITH THE OCCUPATIONAL SAFETY AND HEALTH LAW FOR MANY OF THE TOPICS COVERED IN THESE CHECKLISTS.
When you have completed the checklists, you will have enough information to decide if problems exist. Once you have identified hazards, you can begin corrective actions and control procedures.
SCOPE. The scope of self-inspections should cover the following areas:
- Processing, Receiving, Shipping and Storage. Equipment, job planning, layout, heights, floor loads, materials handling, and storage methods.
- Building and Grounds. Floors, walls, ceilings, exits, stairs, walkways, ramps, platforms, driveways, and aisles.
- Housekeeping Program. Waste disposal, tools, objects, materials, leakage and spillage, cleaning methods, schedules, work areas, remote areas, and storage areas.
- Electrical. Equipment, switches, breakers, fuses, switch boxes, junctions, special fixtures, circuits, insulation, extension cords, tools, motors, grounding, compliance with codes.
- Lighting. Type, intensity, controls, conditions, diffusion, location, glare, and shadow control.
- Heating and Ventilation. Type, effectiveness, temperature, humidity, controls, natural and artificial ventilation, and exhausting.
- Machinery. Points of operation, flywheels, gears, shafts, pulleys, keyways, belts, couplings, sprockets, chains frames, controls, lighting for tools and equipment, brakes, exhausting, feeding, oiling, adjusting, maintenance, lockout, grounding, workspace, location and purchasing standards.
- Personnel. Training, experience, methods of checking machines before use, clothing, personnel protective equipment, use of guards, tool storage, work practices, method of cleaning, oiling, or adjusting machinery.
- Hand and Power Tools. Purchasing standards, inspection, storage, repair, types, maintenance, grounding, use, and handling.
- Chemicals. Storage, handling, transportation, spills, disposal, amounts used, toxicity or other harmful effects, warning signs, supervision, material safety data sheets, supervision, training, personal protective equipment, and clothing.
- Fire Prevention. Extinguishers, alarms, sprinklers, smoking rules, exits, personnel assignments, separation of flammable materials and dangerous operations, explosive-proof fixtures in hazardous locations, and waste disposal.
- Maintenance. Regularity, effectiveness, training of personnel, materials, and equipment used, records maintained, method of locking out machinery, and general methods.
- Personal Protective Equipment. Type, size, maintenance, repair, storage, assignment of responsibility, purchasing methods, standards observed, training in care and use, rules of use, and method of assignment.
( learn more about workplace-inspections/ )
The attached file below includes the following Inspection checklists:
- General work environment
- Hazard communication program
- Personal protective equipment
- Electrical safety
- Hazardous chemical exposure
- Confined space operations
- Fire safety
- Lockout and Tagout procedures
- Medical services and first aid
- Scaffold safety
- Industrial noise
- Hand and power tools and equipment
- Construction site safety
- Portable ladder safety
- Transporting employees and materials
- Machine guarding safety
- Compressors and compressed gas cylinders
- Motor vehicle service and repair operations
- Welding and hot work operations
- Spray painting operations
- Hoists and auxiliary equipment
- Forklifts and industrial trucks
Snapshot of some checklists
These checklists are not all inclusive. You may wish to add to them or delete portions that do not apply to your workplace. Carefully consider each item as you come to it and then make your decision. Do not spend time with items that have no application to your workplace.
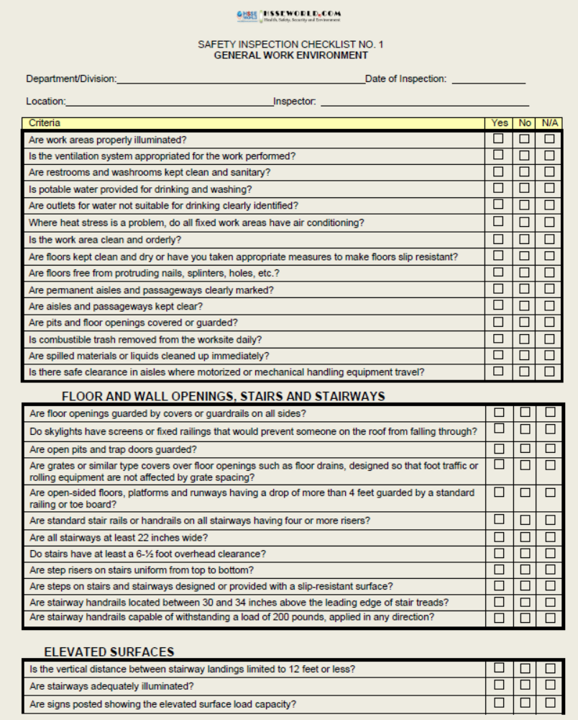
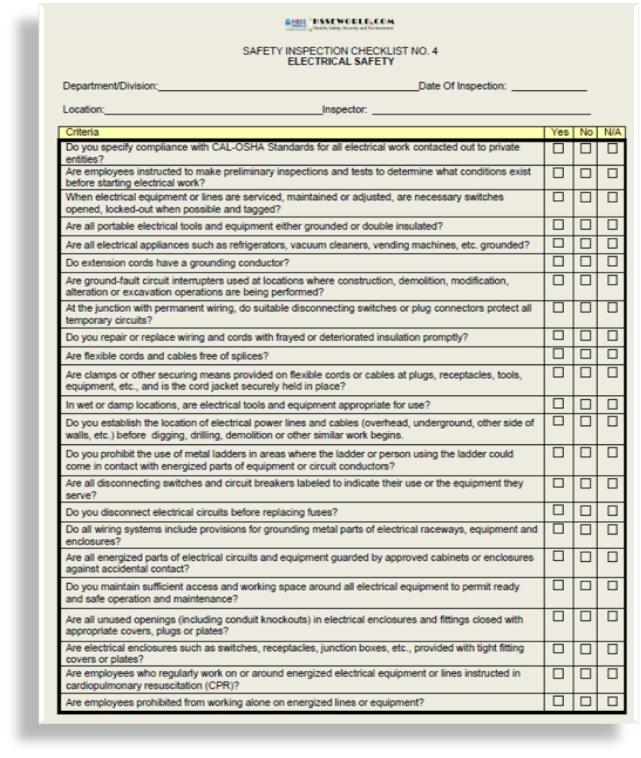
This Document contains twenty-two safety inspection checklists designed to help you evaluate your work areas. They will give you some indication of where you should begin action to make your workplace safer and more healthful for your employees.
Now you can download the PDF and editable Form and use it to fit your purpose just click on download below
Download the Checklists
22-Safety Inspection Checklists PDF
22-Safety Inspection Checklists Doc
More Forms
- Downloadable Kitchen Safety Inspection Checklist for Restaurants
- Mastering LOTO: Protecting Workers with Energy Isolation and Isolation Confirmation Certificates
- Flammable and Combustible Storage Checklist Free Download
- Secure Your Lifts:Guidelines for Safe Lifting Operations Free Planning Tool
- Sample of Accident Prevention Program ( APP) Template for General Industry Free Download
- Free ISO 14001:2015 Environmental Management System Audit Checklist Download
- Guides for Walking and Working Surfaces Safety Program
- Workshop Safety Guideline and free Posters
- Free Ergonomics Checklist for General Industry
- Work Area Safety Checklist
- Machine Safety and 43-Equipment Inspection Checklists
- Scaffold Safety self Audit and checklist
- Hot Work Controls and its Permit to work Form
- Safety Observation Report Template
- Forklift Operator’s Daily Checklist and safety Tips
- Inspecting Fall Protection Equipment Forms
- Templates: HSE Incentives and rewards
- 35 Inspection forms for Rig Check
- Chemical Risk Assessment form
- 22-Safety Inspection Checklists
- Safety Task Assessment Form
- Suspended Scaffold Pre-Operation Inspection Checklist
- Photo of the day: New worker Orientation & Safety Orientation checklist
- Grating-Decking-Floor- handrail-Removal Form
- Electrical Inspection Checklists
- E-Books: Fire Safety Logbook templates
- General Safety Guidelines and Employee Acknowledgment form
- Annual Internal Audit Form
- Mobile Scaffold Inspection checklist
- Simultaneous Operation (SIMOPS) checklist
- Temporary Construction Facilities (TCF) Inspection checklist
- HIRA, HSE Hazards & Effects Management Process (HEMP) & Risk Register Template
- Hazard Identification Plan (HIP) Template
- Ladder Inspection Form
- Free Pre-Startup Safety Review Checklist (PSSR)
- Hazard Identification Checklist
- Workplace Housekeeping Checklist
- ISO 45001:2018 READINESS CHECKLIST
- Lifting Plan Audit Checklist
- Job Safety Analysis (JSA) Forms What’s Right and Wrong?
- Electrical Isolation Permit to Work forms and checklist
- Canteen Inspection Checklist
- Work at Height Checklist
- Health Safety at Work Improvement Action Plan
- Fire Pump Daily Inspection Checklist
- Construction Site Traffic Management Plan (CSTMP) Guidance
- Safety Templates: COVID-19 Safety Plan
- Workplace Safety Inspections Forms
- Lock Removal Form
- Templates: Management of Change NEW Modified Equipment Safety Checklist
- Lifeline & Harness Inspection Guide checklist
- Contractor Pre-qualification Questionnaire Checklist
- Fall safety at construction checklist
- Construction safety Inspection checklist
- Equipment Safe Operating Procedures- SOP 61 checklist
- Permit to Work (PTW ) AUDIT CHECKLIST
- Hygiene and Sanitation Inspection Checklist