Elevate Safety: 7 Cutting Edge Modern Overhead Crane Safety Systems
8 min readOverhead cranes play a crucial role in industrial production. Modernizing their safety systems and applying advanced technologies are essential for ensuring operational safety and improving efficiency. This article will explore the modern features and technologies in overhead crane safety systems, supplemented with practical application cases, to demonstrate their use and effectiveness across various industries.
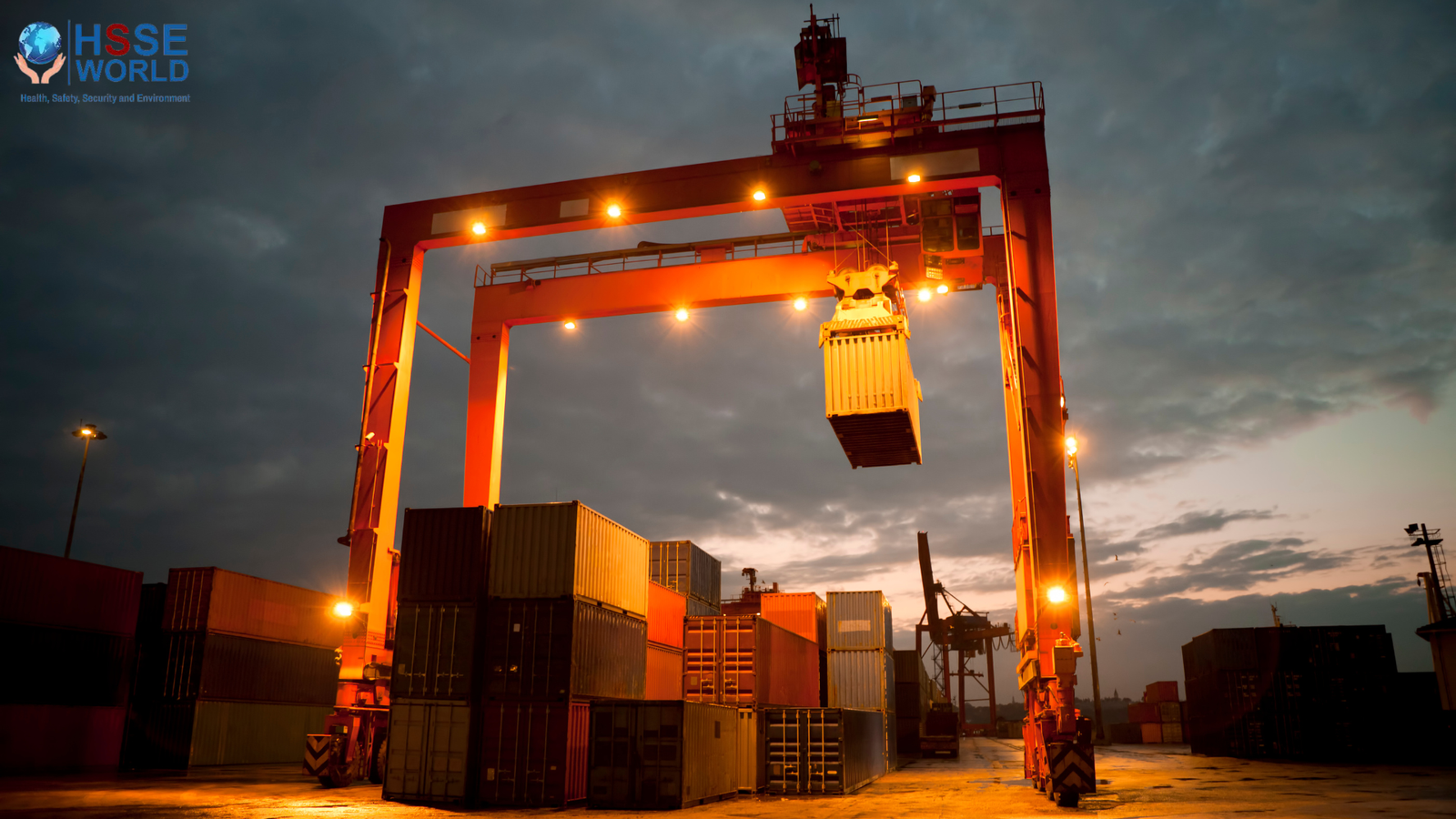
Intelligent overhead crane remote control system
Technical overview
The intelligent overhead crane remote control system leverages advanced wireless communication technology, enabling operators to control the crane remotely from a safe distance. This system typically features a touchscreen interface and human-machine interaction capabilities, making operations more convenient and efficient.
Advantages
- Enhanced Operational Safety: The wireless remote control keeps operators from hazardous areas.
- Increased Work Efficiency: The remote control system reduces blind spots and uses intelligent control to optimize operating paths and speeds.
- Improved Operational Flexibility: It adapts to diverse working environments and task requirements.
Automatic overhead crane anti-collision system
Technical overview
The automatic anti-collision system for overhead cranes is intelligent and utilizes sensors and control technology to prevent collision accidents during crane operations. This overhead crane collision avoidance system detects changes in the crane and its surrounding environment, automatically adjusting and controlling its movements to ensure operational safety.
Advantages
- Enhanced Safety: Automatically detects and avoids obstacles, significantly reducing collision accidents, and protecting equipment and personnel safety.
- Reduced Downtime: Effectively prevents equipment damage and repairs caused by collisions, reducing downtime and increasing production efficiency.
- Simplified Operation: Reduces the operator’s burden by eliminating the need for continuous monitoring and manual path adjustments, enhancing operational convenience.
- Cost Savings: Lowering maintenance and replacement costs due to collision accidents, extending the equipment’s lifespan.
Overhead crane load monitoring system
Technical overview
The crane load monitoring system is a technology specifically designed to monitor the load conditions of cranes in real time. Using sensors and data analysis ensures that the crane operates within a safe load range, preventing accidents caused by overloading and unbalanced loads. This technology typically includes components such as weight sensors, data transmission units, data processing units, and alarm systems.
The crane load monitoring system is an option on the single girder EOT crane. Customers can choose not to install the system to save costs.
Advantages
- Increased Safety: Real time monitoring of load conditions prevents overloading operations, reducing the risk of accidents.
- Extended Equipment Lifespan: Prevents excessive wear and fatigue damage to structural components caused by overloading, thereby extending the crane’s service life.
- Reduced Maintenance Costs: Provides historical load data to help develop scientific maintenance and care plans.
Download: photo-of-the-day-run-project-safely-with-crane-hand-signals
Overhead crane anti-sway system
Technical overview
The overhead crane anti-sway system is a technology used to control and reduce the sway of a crane’s load during lifting, moving, and placing operations. This system utilizes sensors and control algorithms to adjust the crane’s movement parameters in real time, maintaining load stability and preventing operational risks and efficiency losses caused by sway.
Advantages
- Increased Safety: Effectively reduces load sway, lowering the risk of collisions and drops, thus ensuring the safety of operators and equipment.
- Improved Operational Efficiency: By suppressing sway, the load remains more stable during movement, reducing positioning and placement time, and increasing work efficiency.
- Reduced Equipment Wear: Smooth operation minimizes mechanical component impacts and wear, extending the lifespan of the crane and its related components.
- Enhanced Work Environment: Stable operation improves the controllability and comfort of lifting tasks, reducing operator fatigue.
Automatic overhead crane positioning system
Technical overview
The automatic overhead crane positioning system is a technology used for precise control of the crane’s lifting devices or loads within a three-dimensional space. By integrating various sensors such as GPS, LiDAR, ultrasonic, and cameras, the system monitors and adjusts the crane’s position and movement trajectory in real time to ensure the load is accurately placed at the specified location.
Advantages
- Increased Operational Precision: High precision positioning sensors and control systems ensure the load can accurately reach the target location, minimizing errors.
- Improved Work Efficiency: The automatic positioning system speeds up the positioning and placement process, reducing operation time and increasing work efficiency.
- Enhanced Safety: Reduces the risk of collisions and accidents caused by human error, ensuring the safety of operators and equipment.
- Lowered Operational Complexity: Operators do not need to perform complex manual positioning operations, reducing the difficulty and technical requirements of the task.
Read: guideline-for-crane-stability-and-ground-pressure
Overhead crane data recording and analysis system
Technical overview
The data recording and analysis system is a technology used for real time monitoring and recording of crane operating parameters, and optimizing operation and maintenance strategies through data analysis. This system typically includes sensors, data acquisition units, storage devices, and analysis software, capable of recording key data such as crane operating status, load conditions, work cycles, and fault information.
Advantages
- Enhanced Operational Safety: Timely detection and warning of potential safety hazards. Provides detailed operation logs that aid in accident analysis and responsibility determination.
- Improved Work Efficiency: Data analysis helps optimize crane operating parameters, increasing operational efficiency.
- Optimized Equipment Maintenance: Predictive maintenance based on data analysis allows for early detection and handling of equipment faults, reducing downtime.
- Decision Support: Provides detailed operational data and analysis reports to support data-driven decision-making by management.
- Improved Data Management: Centralized data storage and management facilitate unified data management and access.
Overhead crane safety interlock system
Technical overview
The safety interlock system is a key technology designed to ensure the safe operation of cranes under specific operating conditions. By setting various mechanical and electrical interlock devices, this system prevents hazardous operations and equipment misuse, thereby protecting the safety of operators and ensuring the normal operation of the equipment. The safety interlock system typically includes position sensors, limit switches, safety control units, and alarm devices.
Advantages
- Enhanced Operational Safety: Prevents incorrect and hazardous operations through mechanical and electrical interlock devices, reducing the risk of accidents.
- Increased Operational Reliability: Ensures that each operation step follows the predetermined safety logic sequence, improving operational reliability.
- Simplified Maintenance and Management: The interlock system’s protection reduces unexpected equipment failures and maintenance frequency, thereby lowering maintenance costs.
Read: the-impact-of-changing-working-conditions-and-faulty-technical-equipment-on-industrial-safety
Case study
Some strong crane manufacturers have gradually started implementing these safety systems in cranes across various application scenarios and have received positive feedback. It is believed that these crane safety systems will become increasingly widespread in the future. Here are a few examples to give readers a more intuitive understanding of the role and convenience of these safety systems.
Kuangshan Crane intelligent overhead crane for garlic warehouse storage
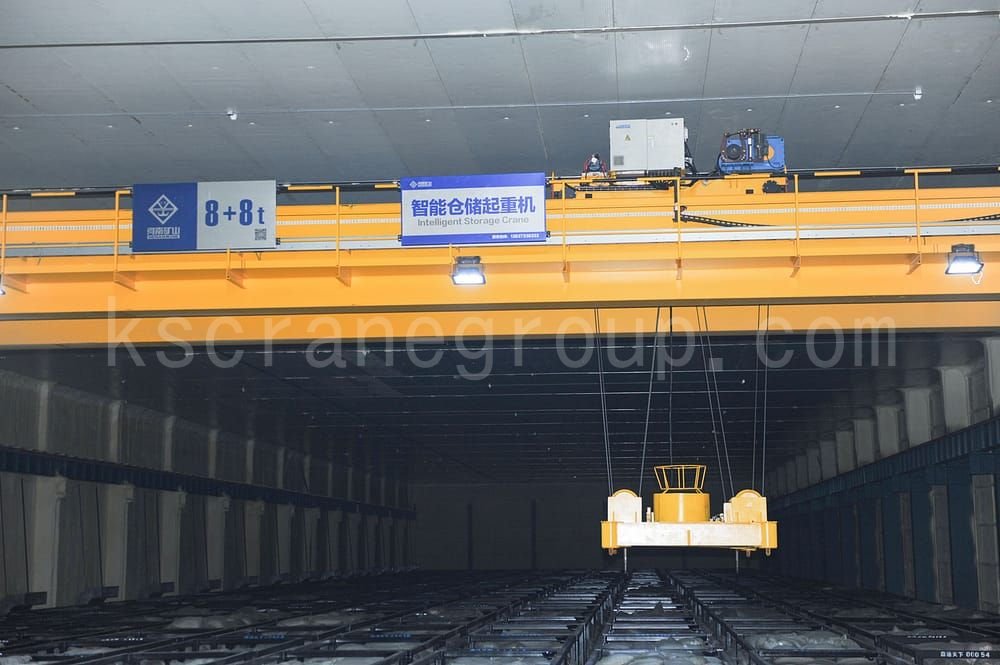
The (8+8)t intelligent warehousing crane is China’s first automated intelligent crane applied to agricultural warehousing. The unique pungent odor of garlic makes the working environment extremely harsh, requiring storage and transport workers to wear oxygen masks for prolonged periods.
Based on practical research, Henan Kuangshan proposed a new garlic storage solution, replacing the original small basket storage method with a system where finished garlic is stored in specially designed large baskets. They also designed a specialized lifting device for these large baskets. The intelligent crane automatically recognizes the basket codes, performing automatic stacking and dispatching, fully replacing manual stacking.
This crane features smooth operation without fluctuations, multiple positioning points (over 1,400 high precision positioning points), and high accuracy (≤±5mm for the lifting device). It interfaces with the backend database and connects with smart terminals to monitor the status of warehoused goods in real time. Additionally, it includes functions such as automatic grabbing and stacking of the lifting device, automatic positioning, electrical anti-sway, remote monitoring, and intelligent management.
The successful development of this crane offers the following advantages:
- Enables high density storage: With a single warehouse capacity of 60,000 tons, it is 10 times more efficient than conventional cold storage based on land use efficiency.
- Continuous 24 hour operation: Utilizing computer technology for information tracking, position storage, load optimization, and positioning operations, reduces downtime.
- Reduces manual handling losses: Through precise positioning and anti-sway technology, it minimizes damage during manual handling of large baskets.
- Cost savings: Saves on electricity, reduces the number of required staff, and saves time, collectively reducing the overall warehousing costs by 60%.
DEMAG customized an overhead crane system for a steel service center.
Due to the increasing annual production capacity and orders of the steel service center, the existing facilities and lifting equipment were no longer sufficient to meet its needs. The new crane system manufactured with Demag’s involvement has doubled the production capacity of the steel service center.
Advantages of the new crane system
- Data Integration with Demag Warehouse Management System (WMS): The WMS automatically adjusts to match given inventory factors, ensuring optimal space utilization.
- Positioning Control System: The cranes are equipped with a positioning control system that allows them to approach specified positions with the aid of a laser-assisted positioning system. This system monitors the position of the cranes on the runway and the distance between them with high precision.
- Intelligent Tandem Mode: This mode allows two cranes to operate as a team, synchronously handling large or very heavy loads. In tandem mode, not only is the operation made more convenient, but a high level of safety is also ensured.
- Safety-Oriented Monitoring: The cranes feature safety-oriented monitoring to oversee the complex interaction between long travel and cross travel devices and lifting movements. If any anomalies or overloads occur, the system will issue a warning signal or stop the movement sequence, thus preventing hazardous operating conditions.
CPA designed a safety interlock system for bridge cranes.
Casper, Phillips & Associates Inc. (CPA) designed a custom interlock system for two 10-ton bridge cranes at a factory that produces composite aircraft components.
When the bridge crane docks and locks with the workstation, the trolley moves from the bridge crane to the workstation, positioning and placing the components for the next manufacturing stage. After manufacturing is completed, the components are lifted by the trolley and moved via the interlock device back to the bridge crane, which then transports them to the next workstation.
The CPA system prevents the trolley from slipping off the bridge crane or workstation when not locked, ensuring operational safety. While interlocks are common on cranes, this is a highly customized setup, which took a full year from design to commissioning. The interlock device is now fully deployed across the entire bridge crane system, and the end user is satisfied with its performance.
Conclusion
Modern safety systems for bridge cranes significantly enhance operational safety and efficiency by integrating advanced technologies such as automatic anti-collision, load monitoring, anti-sway, intelligent remote control, automatic positioning, data recording and analysis, and safety interlocks.
Successful case studies of these technologies in practical applications demonstrate that these modern features not only protect the safety of equipment and operators but also bring significant economic benefits and management advantages to various industries. As technology continues to advance, the safety systems of bridge cranes will further develop, providing more reliable assurance for safe production across industries.
Read: ensuring-workplace-safety-comprehensive-guide-to-overhead-crane-safety
have more safety resources at : https://safetybagresources.com/