The Impact of Changing Working Conditions and Faulty Technical Equipment on Industrial Safety
3 min readIn today’s fast-paced world, industries are constantly evolving, introducing new jobs, products, materials, tools, and working methods. While these changes often bring advancements and increased efficiency, they also pose challenges to workplace safety. In this article, we will explore the dynamic nature of working conditions and the significant role faulty technical equipment plays in industrial accidents. We will also emphasize the importance of regularly reviewing and updating safety standards to mitigate risks and promote a safer working environment.
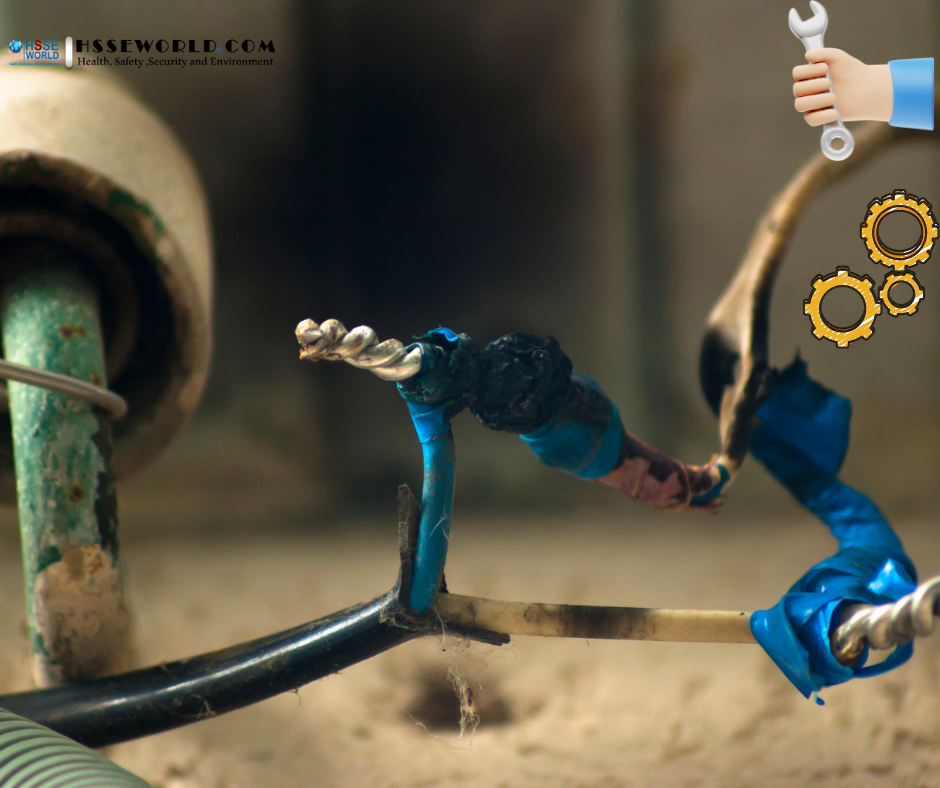
LAYOUT- MATERIALS FLOW
Working conditions are constantly changing. New jobs, products, materials, tools and working methods are being introduced all the time. These changes mean that our experience and the standards of safety we have built up in the past must be reviewed and brought up to date. However, gaps in our knowledge are not the only cause of industrial accidents. Faulty technical equipment is another major cause.
A basic rule is that:
machinery and other technical equipment should be constructed, placed and used so that they do not constitute a risk to health or cause accidents.
https://hsseworld.com/photo-of-the-day-workplace-hazards
This means that machinery and equipment should be safe during all operating conditions and have effective safety guards at all dangerous points. If possible these guards should be an integrated part of the machinery so that the worker/operator is not tempted to remove them.
Machine Safety and 43-Equipment Inspection Checklists
The path of the materials through the workplace constitutes a risk in the working environment. The layout of the manufacturing process should be planned with as little risk of accidents as possible. “Layout” in this case means:
- the way different sections and processes are arranged in relationship to each other
- the arrangement of machinery and equipment within each work area.
Bottle-necks in the flow of materials cause work to become irregular and can thus increase the risk of accidents.
Operations which generate noise and vibrations should be separated from the rest of the manufacturing process. Additionally, the facility should be designed so that it functions well under special conditions, such as an abnormally high workload over a short period.
Transport routes/aisles
Overall planning of safe routes and aisles based on simplicity and easy understanding is the key to a safe workplace.
Many accidents happen while materials or goods are being transported around the workplace.
Therefore, the vehicles and equipment used inside the premises should be included in inspections.
Suitable access routes or aisles are required for access to mechanical equipment. Access to hoists and overhead cranes for service or repair work is also essential.
Safe storage and parking areas should be provided.
Emergency exits should be kept clear of all materials and equipment.
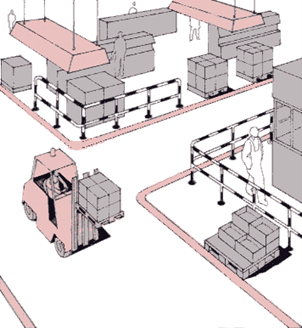
Access routes/aisles which are safe and rational should:
- be planned so that there is no danger of vehicle collision
- be positioned a safe distance from fixed workplaces
- have adequate lighting on stairs and ramps
- be clear of obstacles
- have pedestrians at a safe distance from vehicles
- have lines or markings which clearly show where they lead to
- be wide enough for traffic
- have handrails on the stairs if there are more than three steps
- have a guard barrier where there is a risk of falling
- be adapted for handicapped or disabled persons.
Safe work site Activity for Traffic Management
Read more