Workshop Safety Guideline and free Posters
9 min readHaving an efficient workshop can be one of the most cost-effective ways of maintaining plants and equipment on-site. The workshop contains many potential safety hazards. However, with proper control, these hazards can be eliminated. The purpose of this article is to outline the basic workshop safety guidelines to all those who have a responsibility for controlling the work undertaken in a workshop and the environmental conditions under which such work is performed; and to all those who may use the tools, plant, equipment, and facilities offered by the various workshops in the worksite so at the end of the reading you will able to:
- Be familiar with Workshop safety Basic guidelines
- Download free Workshop Safety Posters
- Download the free Workshop safety Inspection checklist
Also Read: E-Books: Safety With Machinery
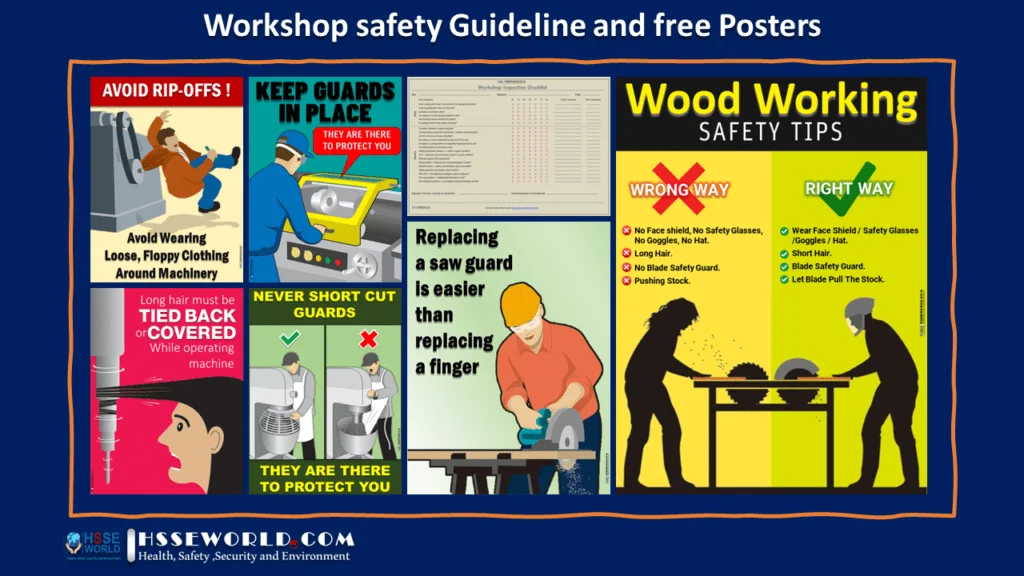
General
Departmental workshops play an important role in the fabrication and maintenance of worksites. However, inappropriate use of workshop equipment can cause serious injuries. To minimize the likelihood of injuries, the following procedures shall apply to all workshops and to the work of workers (other than professionally qualified workshop staff) who are permitted to work in such workshops. Operation of dangerous workshop equipment, outside of a designated workshop, shall not normally be permitted.
- In units that operate workshops, the chair or head shall appoint a workshop supervisor who will be responsible for the safe operation of the workshop.
- Potentially dangerous work in departmental workshops shall only be carried out under the supervision of a workshop supervisor.
- No person other than a workshop supervisor or professionally qualified workshop employee may work alone in a workshop or at times when a workshop supervisor is unavailable to supervise the work.
- supervisors shall ensure that staff whom they supervise are appropriately trained before authorizing them to carry out work in a departmental workshop.
- workers may only undertake such workshop tasks that have been authorized by their supervisor. While carrying out such tasks, workers shall:
- Follow the direction of a workshop supervisor.
- observes workshop safety rules.
- never work alone in the workshop.
Also Read Safety Flash: Electric Shock Resulting in Burn
General Workshop Safety Rules
- Only those authorized to do so by a Workshop Supervisor may work in this shop. Operation of power tools and other potentially dangerous shop work may only be done under the supervision of a Workshop Supervisor.
- Safety glasses (CSA-approved) must be always worn while working with tools. Other protective equipment must be worn as directed by a Workshop Supervisor. Do not wear gloves, loose-fitting clothing, baggy sleeves, dangling jewelry, or neckties that could become entangled in machinery.
- You may not use any power tool until you have been trained in safe operation techniques by a Workshop Supervisor.
- Disconnect power before adjusting power tools. Do not service energized equipment.
- Take appropriate steps to prevent the release of dust or noxious fumes.
- Take appropriate fire prevention precautions when your work generates heat or sparks or involves open flames or flammable liquids.
- Do not remove machine guards.
- Keep the shop clean and tidy. When not in use, store tools, equipment, and supplies properly. Clean up after you complete your work.
Control and supervision
Workshop supervision
For every workshop, there shall be one particular named person who is charged with being responsible for all aspects of safety within that workshop, or under his/her control, including where necessary, the supervision of other individuals using the machines and equipment.
The names of the Supervisor or other competent authorized person(s) should be displayed at the entrance to the workshop.
Employees
All employees, not just the Workshop Supervisor, have a duty to ensure that safety procedures are carried out by themselves and by other employees.
Even employees of minimum skill have a duty to themselves and to others and must always work in a safe manner. It is particularly important that members of this latter group should seek advice on safe methods of working from the senior workshop employee. Trainees are here to learn and improve their skills through observation, practice, and experience. This must never be gained by being exposed to risk. The employees must be fully supervised until such time as he/she is judged by the Workshop Supervisor or other competent authorized person to be competent to work without supervision.
Training of operators
This should consist of three elements:
- General. The basic skills and knowledge common to all machines. This will include aspects of ‘good housekeeping’ plus knowledge of the relevant legislation.
- Machine specific. The basic skill in the operation of the machine, including the position and function of emergency stops; basic safety rules related to the operation of a machine or class of machines; the use and adjustment of guards and safety devices.
- Familiarization. On–the–job operation under close supervision
Only those employees who have received appropriate technical training in relation to workshop machinery will be deemed suitable to operate or supervise other people with such equipment. The line manager or other competent authorized persons concerned will determine the need for appropriate training.
No person may be allowed to operate machinery without first being adequately instructed in its use, by a competent authorized person.
Supervision
Despite the guarding of machines to the standards required, there may still remain a residual risk and the Supervisor must therefore ensure that only competent authorized persons are permitted to use machines and equipment unsupervised.
Whenever a person who is not yet considered by the Workshop Supervisor or other competent authorized person to be fully competent is required or has a need to use a particular machine, then the Workshop Supervisor or other competent authorized person shall arrange that the operator is supervised by another fully competent person who must ensure that only safe methods of working are followed.
No New or Trainee may work unaccompanied in any workshop. There must always be another person within sight and hearing who can render assistance in the event of an emergency.
No employee may work unaccompanied in any workshop unless appropriate precautions and measures have been established, relevant to the equipment being used.
Entry control
Each workshop shall, so far as is reasonably practicable, be securely closed when proper supervision is not available. If this is not possible, all hazardous equipment must be secured to prevent unauthorized use, and electrical equipment isolated or the power turned off. Apart from those regularly employed as operators or supervisors in workshops; permission to use any machine must always be first obtained from the person in charge.
Each workshop entrance must display a notice to include, but not be limited to the following:
- Any person entering this workshop must make himself or herself known to the person in charge.
- Any person wishing to use this workshop must have completed a Workshop Induction Record.
- No piece of equipment may be used without having completed the relevant section of the Workshop Induction Record.
- In the interests of safety, the person in charge has the right to refuse or limit entry to this workshop.
- Power tools must not be used unless an appropriate person is present to supervise.
- Machine guards must be properly adjusted and used were provided and never removed when machines are in use.
- The extraction must be used if required.
- Appropriate PPE must be worn at all times.
- Jigs & fixtures must be inspected before use for defects and suitability.
- All machines will be left with their blades and cutters stationary and brakes on, (where fitted), and the power isolator in the off position.
- No tools or equipment may be removed from this workshop without the permission of the person in charge.
IF IN DOUBT STOP AND ASK.
Safe work rules
The completion of work by safe methods must always take precedence over any deadlines determined by the person commissioning the work.
Appropriate clothing must be worn when in workshops. The Workshop Supervisor or other competent authorized person will determine what is deemed appropriate, bearing in mind that not only machine operators will require ’appropriate’ clothing, but also others who may only be observing operations. Loose clothing, e.g. ties, necklaces, chains, etc. present a danger when using rotating machinery and must be prohibited.
Long hair must be covered or tied back as appropriate if the Workshop Supervisor or other competent authorized person(s) considers the length to be such as to be hazardous.
Personal protective equipment, appropriate tools, etc. must be used as required by regulations, in particular, Personal Protective Equipment at Work Regulations 1992,
Control of Lead at Work Regulations SI 1980: 1248, Control of Substances Hazardous to Health Regulations 2002, The Electricity at Work Regulations 1989, Noise at Work Regulations 2005.
New work/processes involving the use of hazardous substances must not be started unless a COSHH (Control of Substances Hazardous to Health) risk assessment form has been completed, whereby appropriate proper controls etc. must be implemented.
[Management of Health and Safety at Work 1999]. COSHH risk assessment forms can be obtained from the Health and Safety web page ‘Risk Assessment’ section.
The Workshop Supervisor or other competent authorized person must ensure that work equipment risk assessment forms are completed and readily available. Work equipment risk assessment forms can be obtained from Here.
All persons are responsible for housekeeping and ensuring that spillages are cleaned up immediately and that the floor is kept as non-slip as possible.
Personal hygiene
- Food and drink must not be consumed or brought into the workshops.
- Mineral oils are known to cause dermatitis and in some cases, cancer. Operators and
- others coming into contact with minerals and other chemicals, for example, cleaning fluids, solvents, acids/alkalis, etc must be made aware of the need for cleanliness and thorough hand washing. Regular and effective cleaning of overalls and any personal clothing, which comes into contact with chemicals, is essential.
Location of machines
Machines must always be located in a workshop in such a way as to ensure that there is always adequate room to work without the risk of endangering an operator at any machine nearby, or any other person in the workshop area. The clearance between moving sideways and fixed adjacent objects should not be less than 0.5 meters.
Labeling of machines
All machinery must have a colored sticker to indicate the level of risk inherent to it.
(Stickers colors Examples):
- Green would signify low risk (only to be used after training);
- Yellow would signify medium risk (only to be used with permission);
- Blue would signify medium risk (only to be used after sufficient training & under supervision);
- Red would signify high risk (approved employee use only).
( Also Read: Machine Safety and 43-Equipment Inspection Checklists )
Housekeeping, lighting, ventilation, and temperature
Environment
Persons using the workshop must ensure that the working environment is satisfactory and safe and that any deficiencies are brought to the attention of the appropriate supervisor, Estates (Badger maintenance reporting system), or the Health & Safety Manager, as appropriate.
Temperature
The workshops should always be warm. At low temperatures, mistakes and accidents can occur. Excessive heat can also increase the chance of an accident.
Waste
Each workshop must have a robust system for the collection, handling, storage, and disposal of waste materials. The Workshop Supervisor or other competent authorized person will be responsible for the safe management of waste.
Due to manual handling regulations, each workshop must ensure that rubbish bags are not overloaded.
All swarf and other sharp-edged waste materials (glass, metal, etc.) must be regularly cleaned up and placed in an approved type of metal ‘sharps’ bin. No rubbish of any kind must be allowed to accumulate. Compressed air must not be used for cleaning operations.
Lighting
The Workshop Supervisor or other competent authorized person must ensure that the lighting of the area under his/her control is adequate for the nature of the work being carried out. Under certain circumstances, fluorescent lighting may produce a stroboscopic effect in relation to rotating machinery. When appropriate, local tungsten lighting should be used. Persons using machines under fluorescent lighting must be warned that the stroboscopic effect could make moving parts appear stationary.
Ventilation
The Workshop Supervisor or other competent authorized person must satisfy themselves that ventilation in the area under his/her control is satisfactory with regard to the nature of work being carried out, particularly in respect to welding, spray painting, glassblowing, wood machining and other processes involving the use of hazardous substances. (Control of Substances Hazardous to Health Regulations 2002).
(Know more about Industrial ventilation )
Accidents and emergencies
Accidents
All accidents and near misses must be reported using the Accident and Incident Reporting forms.
Remember, you must not use machinery when tired or if you have taken medication, drugs, or alcohol.
( Also read: Accident-Incident Investigation Technique guideline )
First aid
Each workshop must have a first aid box. The Workshop Supervisor or other competent authorized person must ensure that the first aid box is checked and if necessary, restocked weekly.
Go here to know what should be in your first aid kit.
Fire
Workshop employees should know how to use fire-fighting equipment and should know where the equipment is located. (See Fire and Emergency Drill Manual and Building Inspection Guide).
Download Workshop Safety Inspection Checklist
you can use the following workshop Safety inspection checklist to use on a daily and weekly basis and ensure all safety requirements for the workshop are in place.
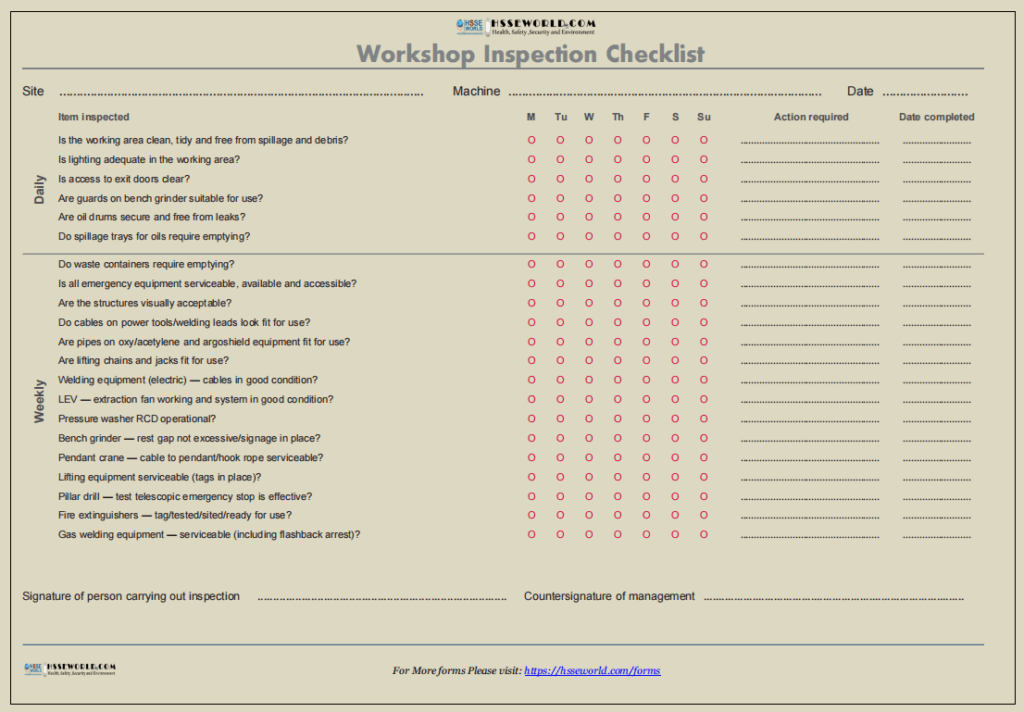
Download the Checklist:
Download Workshop Safety Posters
you can download the posters below and post them at the workshop to communicate with workers about workshop hazards and controls
For many Safety Resources please visit Safetybagresources