What is The meaning of Back Fire, Sustained Backfire, and Flashback ? and what is its preventive measures in welding Applications
Used properly, modern oxy-fuel process equipment is safe to handle without extra protection. There is no substitute for training and diligence among those who operate oxy-fuel equipment. However, the use of special technical safety devices such as flashback arrestors is now a requirement and a safety best practice to prevent incidents with oxy-fuel equipment.
This Safety Article deals with the most frequently used safety devices for the prevention of flashback in oxy-fuel gas equipment.
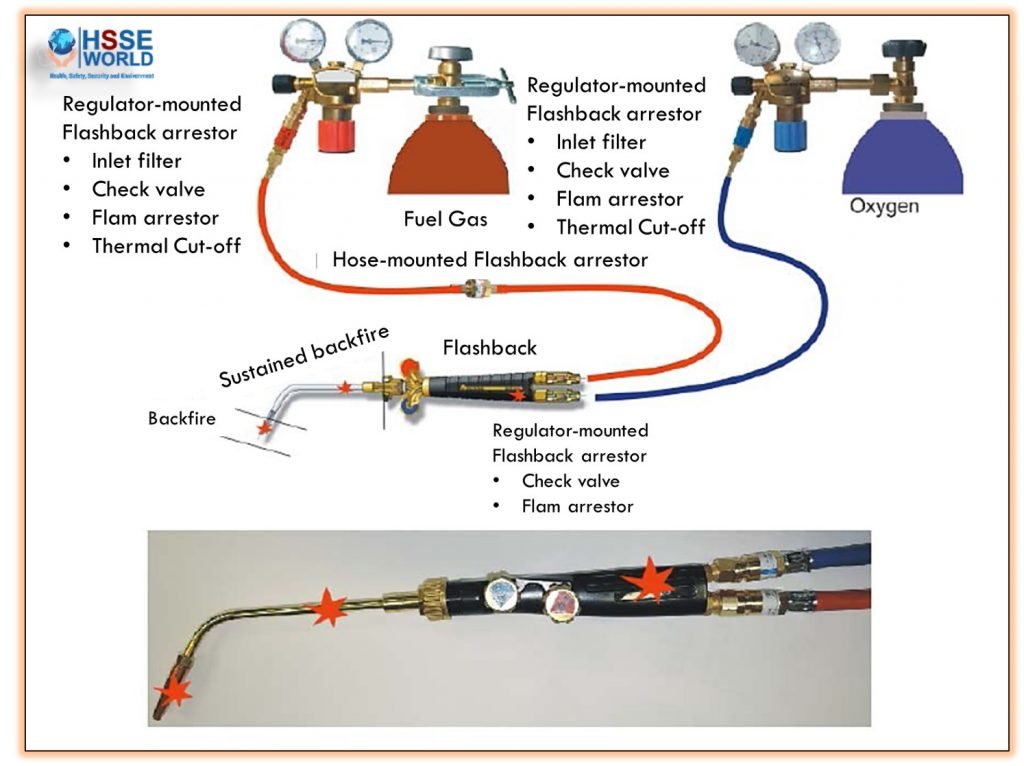
Hazards
Oxy-fuel welding, cutting, and heating torches are subject to three types of phenomena:
- Backfire,
- Sustained backfire,
- Flashback.
A backfire is the momentary retrogression of the flame into the torch nozzle outlet with a cracking sound. It looks as if the flame is sucked into the nozzle and the user hears a “pop”. Either the flame is extinguished, or it is reignited at the nozzle opening. This is normally not a safety concern.
A sustained backfire is the burning of the flame from the nozzle outlet back inside the torch, often reaching the mixing point for oxygen and fuel gas. An initial cracking sound is followed by a whistling sound a hissing or squealing sound and/or a smoky, sharp-pointed flame.
What to do?
The user should immediately close both torch valves to avoid damage or injury. If a sustained backfire continues to burn without closing torch valves, severe damage to the torch, as well as an increased risk of fire, would result. Most sustained backfires can be contained inside the torch until the user can shut off the flow of gas and will not breach outside the torch wall. There are, however, some circumstances (torch designs with thin wall construction) in which the flame will breach the wall and spew fire and molten metal for a short time
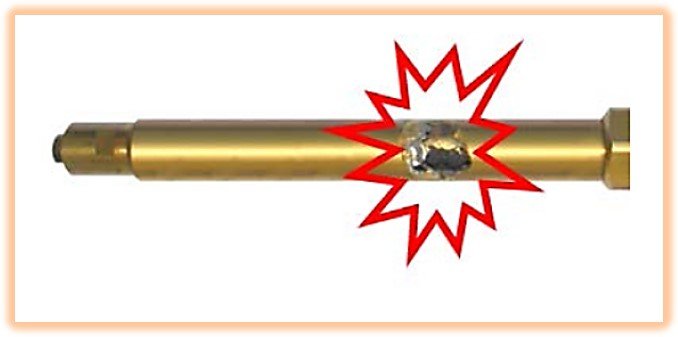
A flashback is a momentary or sustained retrogression of the flame in the torch upstream of the mixing point at a very high speed. This is a potentially dangerous situation, particularly if the flame reaches the gas supply hoses. The hose can explode, or in the worst case, the flame can continue into the regulator and into the cylinder.
A flashback is always a consequence of a backfire in combination with a gas mixture in parts of equipment upstream from the mixing point. The gas mixture in the hose results from reverse flow when gas at higher pressure flows into a hose with lower pressure.
This reverse flow is usually the result of:
- improper shutdown and/or startup procedures;
- allowing cylinder pressures to become too low; or
- a check valve that is not working properly.
Preventive measures
While backfire can be prevented only by the proper use of equipment, the flashback can be prevented in most cases by using special safety devices, usually simply called flashback arrestors.
Flashback prevention
Flashback arrestors are essential safety devices which provide the maximum protection for the operator and his equipment in the event of a flashback. They need very little maintenance.
Flashback arrestors are multifunctional devices and typically use a combination of different elements (different safety functions) to stop a flashback and/or reverse the flow of gas.
Flashback arrestors include a minimum of two elements or functions:
- a check valve (a non-return valve) which prevents the passage of gas in a direction opposite to the flow and creation of a dangerous gas mixture. The valve is held open by the energy in the gas stream and closes when downstream pressure is approximately equal to or greater than that in the normal direction of flow. The check valve cannot stop a flashback once it has started to occur;
- a flame arrestor that quenches the flame front. It prevents flashback by cooling the flame to below the ignition temperature of the gas or gas mixture. Gas can flow through the arrestor ‘filter’, but good thermal conductivity and high porosity of the sintered metal elements of the ‘filter’ lead to flame quenching.
In addition to these two basic safety functions a flashback arrestor can also have:
- a temperature-sensitive cut-off valve which prevents excessive temperatures by closing automatically at a set temperature and cutting off the gas flow long before the ignition temperature of the gas mixture is reached. The valve is held open by a fusible metal link or similar device and is actuated by a sustained temperature rise.
- a pressure-sensitive gas cut-off valve which stops the gas flow in the event of a back-pressure from the downstream side. The valve is held open by a spring or similar device is actuated by a pressure increase from the downstream side and is then automatically held closed.
The flashback arrestors are suitable for most industrial gases and fuel gases such as acetylene, hydrogen, methane, propane, propylene, and butane as well as oxygen and compressed air. Flashback arrestors shall be tested for non-return flow of gas, for tightness, and for gas flow by a qualified person, depending on the country-specific regulations or manufacturer recommendation, as indicated by a validity period.
Where flashback arrestors shall be mounted?
Flashback arrestors can be either:
- torch-mounted;
- hose-mounted; or
- regulator-mounted.
Flashback arrestor type | Safety element (safety function) |
---|---|
Torch-mounted Torch arrestors are most important because their location is ideal for preventing reverse flow flashbacks into the hoses. The size of these types of flashback arrestors is limited so as not to make the torch too cumbersome to handle. | • Check valve • Flame arrestor Sintered elements of the flame arrestor create a pressure drop. This means pressures at the mixer are lower. Lower pressures at the mixing point mean lower exit velocities of the gas mixture at the tip or nozzle. This could result in a sustained backfire if the torch gets too close to the workpiece. Heavy heating applications are especially vulnerable to this event since heating tips use large volumes of gas and are highly susceptible to backfires, which could become sustained, if mixing point pressures are too low. |
Regulator-mounted These flashback arrestors are typically larger and gave a higher flow capacity than torch types because the sintered element has more surface area, allowing more flow. | • Inlet filter • Check valve • Flame arrestor • Thermal cut-off valve If only regulator mounted arrestors are used, flashbacks can still occur in the hoses. |
Hose-mounted These arrestors are functionally similar to torch-mounted ones, but as the name implies, mounted on the gas hoses as near as possible to the torch. | • Check valve • Flame arrestor |
The advantage of having a flashback arrestor mounted on the regulator outlet is that it can have a far greater flow capacity than a torch-mounted flashback arrestor. The disadvantage of having the arrestor mounted on the regulator is that it cannot prevent a hose explosion, which a torch-mounted one can do.
Maximum safety is therefore achieved by having arrestors on both the regulator and torch.
It is important to apply for this protection not only to the fuel gas but also to the oxygen side. A flashback arrestor on the oxygen regulator can for example prevent oxygen from continuing to flow out in case of fire. This is important as the additional oxygen raises the combustion rate.
Backfire prevention
A way to avoid the hazards associated with sustained backfire is to compensate for the pressure drop when using flashback arrestors. Most arrestor manufacturers supply pressure drop charts along with their products. These charts should be closely followed when setting pressures in systems using flashback arrestors.