Systematic Approach for Safe Mechanical Completion, Pre-commissioning, Commissioning, and Startup
18 min readAfter the Mechanical Completion phase of any new Facility, as oil and Gas plan another new phase started which is commissioning and commissioning ending by startup. Pre-Commissioning and commissioning are two very important and distinct stages of the commissioning process. They are often confused, and it can be tricky to determine what takes place during each of these stages.
in this article Let’s review the importance of each stage of the commissioning process and what activities take place during each stage. and provides the systematic approach for mechanical completion, Pre-commissioning, commissioning, and startup of any new facility, mainly for the Oil and Gas Field.
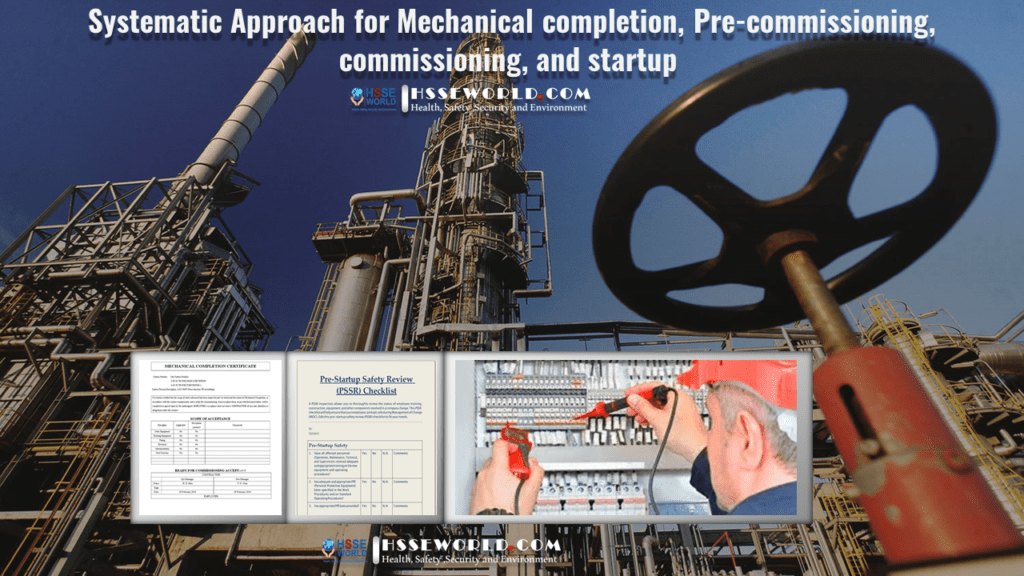
Pre-Commissioning and Mechanical Completion
Pre-commissioning is an important part of the commissioning process. If not done properly, small issues can become much bigger issues later in the project. Handover from the construction team to the commissioning team precedes pre-commissioning, and it is called mechanical completion. This important milestone signifies the start of the pre-commissioning activities. Since the equipment was verified during factory acceptance testing, it was disassembled and shipped to the site, and there is always a possibility of damage during shipping or installation. Pre-commissioning testing confirms that no damage to equipment occurred and that on-site test results align with the test results from the factory.
Terms Related to Off-Site and On-Site Testing
There are a few terms related to off-site and on-site testing.
FAT or Factory Acceptance Testing is the testing that’s conducted by the manufacturer in the factory prior to shipping to the site.
SAT or Site Acceptance Testing is the testing that’s conducted in the field either by the vendor or by the on-site commissioning team. These are the standalone tests of the equipment to confirm no damage during shipping or installation.
SIT or Site Integration Testing is the testing conducted in the field to confirm equipment functions as a subsystem or system.
Typical Mechanical Pre-Commissioning Testing
Pre-commissioning activities vary depending on the equipment to be tested – for example, mechanical versus electrical subsystems. Some typical mechanical pre-commissioning testing includes:
Pipe flushing which is ensuring that piping is free of blockages or any debris.
Leak testing to ensure that all fittings and joints do not leak.
Pressure testing ensures piping can maintain the pressure of liquid or gas.
Verification of rotational equipment which is the first rotation of mechanical shafts and bearings to ensure balancing and no excessive vibration.
HVAC testing is the test and balancing of air flows and ductwork, heating and cooling, sensors, and controls.
Typical Electrical Pre-Commissioning Activities
Some typical electrical pre-commissioning testing includes:
Grounding and bonding checks- confirm the integrity of the ground system and bonding system by measuring the resistance of bonds to ensure bonding to all metallic surfaces is in place.
Cold loop checks and megger checks- confirm that all cable and conductors are terminated to the correct terminal blocks, as well megger checks apply a voltage across the cable conductor and insulation to confirm that the cable has not been damaged or punctured to degrade the dielectric properties of the cable.
Hot loop checks- confirm calibration settings and ranges of each control loop from the HMI to the end device including all cables and instruments. This confirms that ranges and setpoints are correct for each control point.
AC phase checks- verify the installation of each electrical phase in the proper order using a phase rotation meter.
Transformer checks- prior to the first energization of the transformer, oil samples are taken as well as samples taken after energization. The samples are compared to see if any differences could indicate an internal problem within the transformer. Winding resistance measurements are taken as well to measure insulation resistance. Transformer ratios are measured once tap changes are set to confirm that the primary and secondary windings are correct.
Open circuit tests- conducted to measure the no-load current losses as well as short-circuit tests performed with reduced voltage to the primary winding to measure full-load current losses.
During protection relay testing, primary and secondary injections are performed on CTs and PTs to verify relay inputs are correct.
During interlock verification, interlocks are verified by operating equipment without bus voltage applied, and the different operating configurations are verified to confirm that interlocks are functioning correctly before applying any bus power to the system.
AC and DC hi-pot tests measure the ability of a dielectric to withstand rated and transient voltage.
Battery discharge tests– confirm how many hours of rated voltage and current can be supplied during charge and discharge cycles.
Pre-commissioning is complete once you’ve completed all your checklists and verified that each piece of equipment meets the technical requirements of the project. Pre-commissioning activities test equipment as standalone items. Tests during pre-commissioning don’t necessarily operate the equipment as a system yet. Each piece of equipment is individually confirmed to be ready for further commissioning tests.
Pre-commissioning is also known as vendor startup since each vendor’s equipment is started for the first time on-site to confirm the function of each piece of equipment. Following pre-commissioning, we can now move into commissioning tests.
( Download: Electrical Inspection Checklists )
Commissioning
Meaning of commissioning: Commissioning is the phase in a project when design process fluid or safe fluid is introduced to the systems and sub-systems. In simple words, project construction work is over and special activities started to validate that the equipment, machines, systems and subsystems, other system components are installed, tested, and operated in line with project requirement or intent.
For safe, swift, and successful plant commissioning, activities are divided into 12 key elements based on any project philosophy.
- Review and updating of Project HSE plan
- Review of project Risk register
- Planning of commissioning process
- Mechanical completion
- Examination of P&ID
- Pre-Commissioning of system, component or equipment
- Commissioning
- Pre-Startup Safety Review (PSSR)
- Plant Startup
- Initial operation
- Performance test for validating plant intend
- Post commissioning
1. Review and updating of Project HSE plan
HSE Plan provides a document to cover the project Health, Safety & Environment management system and contractor must implement during the execution of the project as per agreed conditions. This is a dynamic document and must be reviewed at various phases of the project right from the construction phase to commissioning, startup, and operation.
2. Review of the project Risk register
The risk register provides the assurance to the project team that they have identified all the work-related hazards and risk is managed at the ALARP level. This document is continuously reviewed and revised at each phase of the project. Before planning the commissioning phase, the Risk register must be revised by identifying the new hazards, analyzing the existing controls, and assessing the risk. It also provides information about any further requirements of safe work practices and work procedures.
3. Planning of commissioning process
Planning is the first element to commission any facility safely and in time. Here clear organizational chart with the roles and responsibilities of all members of the commissioning team is framed. Decide all different types of checklists i.e., structure, piping, mechanical, electrical, instrumentation, etc, and develop an operating manual. Other important procedures are:
- Pre-commissioning procedures viz. air blowing, water flushing, steam blowing,
- Commissioning procedures for the systems and units.
- Safety procedures
- Quality control procedures
- Security procedures
- Emergency management plan and Response procedures
Other than the above procedures, Commissioning status progress reports need to be developed to measure commissioning progress. Test records need to be maintained to keep track of all pre-commissioning and commissioning activities. Develop a punch list format with a construction department together. Planning of manpower requirements including the pre-commissioning team, the commissioning team, the operating team, and the maintenance team.
Planning must be done along with the client so that their team should join the commissioning activities on site (Involvement of client engineers/ operators is very important as this is the best opportunity to train them.). Other agencies may be involved as contractors’ vendors and process engineers.
Ensure advance planning of material requirements. Material like blinds, split pieces, hoses, steam blowing equipment, tool box/ kit, etc my requirements during pre-commissioning and commissioning activities.
4. Mechanical completion
Mechanical completion means construction completion and here mainly the construction team is involved but some time commissioning team may be involved for better understanding. In the Mechanical completion phase all machines, all equipment, and site construction are inspected and tested to validate that the installation is in line with approved drawings, specifications and ready for pre-commissioning or commissioning in a safe manner. It also confirms the compliance with project requirements.
As in the project, different disciplines are working and therefore mechanical completion may be separated by different disciplines viz. Mechanical, Piping, Electrical, Instrumentation, Automation, Structural integrity, etc.
- Mechanical Discipline: Validation for completion and correction of
- Nameplate, display details at tanks, vessels, rotating equipment and other machines.
- Internal inspection of tanks and vessels
- Hydro-static tests of vessels and tanks
- Dimension control
- Bolt tension
- Preservation
Vendor representatives must be on-site for complicated machines viz. compressors, blowers, pumps.
- Piping Discipline: Validation for completion and correction of
- NDT
- Pipe supports
- Confirm that damages during flushing, cleaning and pressure testing are rectified
- Blowing/ flushing finished
- Chemical cleaning & drying
- Preservation
- Reinstatement
- Bolt tension
- Insulation on piping except on flanges and flow coding.
- Electrical Discipline: Validation for completion and correction of
- Electrical panels installation
- Cable trays and its supports
- Cabling in tray and cable dressing
- Bend radius of the cables
- Connection/ Termination
- Grounding
- Megger testing
- Instrumentation Discipline: Validation for completion and correction of
- Instrument panel installation
- Cable trays and its supports
- Cabling in tray and cable dressing
- Bend radius of the cables
- Connection/ Termination
- Grounding
- Instruments
- MOVs
- loop checks
- Tightness test & flushing of tubing
- Automation Discipline: Validation for completion and correction of
- DCS console and its user-friendly installation
- Central process unit
- Cabling & tagging
- Termination
- Grounding
- Loop checking
- Structural Discipline: Inspection of all supporting structures for
- Dimensions
- Integrity
- Bolt tension
5. Examination of P&IDs
Commissioning engineers are examining the P&ID to validate the system for engineering and construction error after handing over of system or system from construction to commissioning team, here punch points are submitted for rectification.
To perform this stage, ensure the latest revision of P&IDs marked with system boundaries, equipment drawings/ datasheet, different types of checklists, national and international standards, hookup drawings, and vendor documents for complicated equipment.
Below items should be checked during the P&ID examination.
- All piping, fittings and valves
- All equipment and machines ie. Motors, pumps, vessels, exchanges, heaters, turbines, compressor, etc along with vendor representative.
- All instrumentation including nameplate, flow direction, mounting position, temperature range, pressure range, flow and other measurement range.
- Safety consideration i.e. Whether it is safe installation and Support safe operation too.
- Operational convenience i.e. Requirement of platform or other safe approach.
- Maintenance convenience i.e. requirement of monorail/ hoist over motors and pumps.
During P&IDs examination, some additional activities may be carried out like provision of temporary identification tags & signs for piping, valves, machines, and equipment.
Any deviations in this process must be marked in the punch point list, signed, and submitted to the construction team and QA/QC engineers. After correction of punch items and confirmation from the construction and QA/QC department, the joint visit should be done to validate the compliances and closed immediately by signing off.
6. Pre-Commissioning of system, component, or equipment
After finished mechanical completion i.e. construction completion, Pre-commissioning activities start to validate the equipment or component is fabricated, installed, cleaned, and tested in accordance with a design intend and ready for commissioning. Pre-commissioning activities include energizing of equipment/ machines, flushing, and cleaning, drying, leak testing, running of equipment, running of electrical motors, loading of catalyst in the reactor, loading of catalyst in columns, dry run, etc. sometimes pre-commissioning activities are included into mechanical completion.
It also ensures the closing of columns, vessels, drums, tanks, the final restoration of systems or subsystems after cleaning, airtightness or leak testing of systems, lubricants application, etc.
Sometimes pre-commissioning includes installation of filters, packing of distillation columns, molecular sieve beds, refractory dry out, instrument/ electrical and motor loop testing, etc. All the findings/deviations must be noted in the punch list.
Pre-commissioning activities should be prioritized & as per approved pre-commissioning procedures viz.
- Procedure for necessary spectacular blind installation
- Procedure for field non-return valve internal installation
- Procedure for checking refractory lining installation and checking of mechanical interlock.
- Procedure for checking of distillation or scrubbing columns packing.
- Procedure for catalyst loading in reactor with installation of filter
- Procedure for air blowing, steam blowing, etc.
- Procedure for water flushing
- Procedure for chemical cleaning
- Procedure for tightness test
- Procedure for cooling water
- Procedure for mechanical test run of pumps, etc
The below sequence is recommended for pre-commissioning activities based on its priorities.
- Power and control system i.e. electrical substations, Building power, etc
- DCS and PLC systems and instrumentation
- Row water and firefighting systems
- Wastewater treatment systems
- Oil, cleaning & chemical sewer systems and neutralization pits
- Service water, potable water and cooling water systems
- Instrument air, plant air and air regeneration systems
- Water treatment systems.
- De-mineralisation plant
- Boiler water system
- The nitrogen system
- Flare system
- Plant safety equipment and fire and gas detection
- Fuel gas and fuel oil system
- Slop systems
- Flushing oil system
- Boiler systems with steam and condensate networks
- Aromatics and caustic drain systems
- Feed and product storage systems
- Product and feed systems
- Amine treatment section
- All the process systems, etc
Pre-commissioning checklists must be developed for different types of machines, equipment, and systems to record the result of inspection and to confirm readiness for commissioning. All these checklists should be witnessed by the client, Project Management Control (PMC), the licensor, etc. Test records must be maintained for all system checking, preparation activities, and other tasks like chemical cleaning, drying, airtightness test, loading of catalyst, blind list status, and performance indicators. Similarly, records for QA/QC documentation, system punch list associated with various pre-commissioning activities viz piping, stationary equipment, rotating equipment, instrumentation pre-commissioning activities, and tightness tests should be maintained. This will help to track the planned vs completion and the remaining tasks which must be done. The status of the punch list report for outstanding punch points must be monitored.
Vendor specialists should be on-site for major items of rotating machinery, major utility systems, special electrical & instrument control equipment, package units that have been assembled by someone at site shipped by a vendor, the licensor does the final inspection of critical equipment installation as well as the supervision of catalyst and chemical loading.
After completing the Pre-commissioning check with validating all punch points, the facility will be ready for commissioning.
Simultaneous Operation (SIMOPS) checklist
7. Commissioning
In a project, after pre-commissioning, the next phase is commissioning where design process fluids or safe fluid are introduced to the systems and subsystems. Commissioning is the stage where the project finished its construction phase and is planned to entire in the commercial operation stage. In this stage, it is validated that each system or subsystem is fabricated, installed, cleaned, and tested as per design intend and the systems are ready for startup. Sometimes it is called cold and hot commissioning. Cold commissioning is of two types i.e. dry commissioning and wet commissioning.
- Dry commissioning: means tests and procedures that are conducted without solvents or process fluids. Eg. interlock and emergency shutdown tests or control system sequence checks, etc
- Wet commissioning: means water/ safe fluid or a solvent has been introduced into the systems or subsystems for testing purpose to simulate the operating scenarios to understand the system’s behavior. Eg. running of pumps in closed loops or interlock and emergency shutdown tests.
- Hot commissioning: means design process fluids are introduced to the systems and subsystems and the activity is similar to wet commissioning activities like running pumps with a closed loop.
For safe commissioning of the facility, ensure safety measures like permit to work system. If the new facility is adjacent to the existing one and employees/ operators would be the same, then the existing PTW should be used otherwise it should be modified adequately.
The construction area might be fenced to separate it from the existing operational facility then security and access control must be ensured. Emergency response procedures must be made aware to all commissioning teams and other related workforce. Final leak testing, final drying, final purging, and energizing must be completed in a safe manner. For initiating systems and subsystems filling with process media, operation of systems and subsystems, completion of the system, etc lot of documentation is required in the commissioning phase. Therefore, the commissioning sequence must be followed for commissioning of the facilities system by system and unit-by-unit basis and it should be the backward approach. Below backward sequence is suggested;
- Control systems DCS /PLC
- Utilities i.e. air, nitrogen, water, steam etc.
- Product storage tank systems
- Loading systems
- Process units ie. reactor, furnace, exchangers, vessels, columns, etc
- Raw material feeds
- Raw materials storage, etc
For safe commissioning, whatever commissioning procedures are finalized in the planning stage, all procedures must be followed. Eg.
- Commissioning procedures for utilities and services
- Commissioning procedure for uses of water or a solvent in each system
- Commissioning procedure for introducing process fluid in each system
- Procedure for Interfacing (operation and maintenance work with commissioning work)
- Product quality control procedure
- Procedure for laboratory analyzes for the new facilities
- Procedure for production planning.
on the operation of the new facilities must be integrated during the commissioning startup and initial operation phase this commences with first requirements for fuel gas and other things from the existing plant for boilers startup and dry out through initial feedstock transfer and final product storage blending and shipping.
maintenance support must be ensured by the company to monitor pump temperature and vibration during commissioning. All commissioning activities by contractors, vendor specialists, etc must be carried out under the supervision of the commissioning team and the licensor. Process licensors may supervise the commissioning activities for important and critical systems and must provide technical assistance during all stages of commissioning. Process operating parameters and conditions will be advised by process licenses, process engineers.
8. Pre-Startup Safety Review (PSSR)
The purpose of the Pre-Startup Safety Review (PSSR) is to ensure that the new/modified facility is ready for safe and continuous operation. The PSSR must confirm the following, prior to the introduction of process fluids to a process/systems/subsystem.
- Construction and equipment meet design specifications.
- Safety, operation, maintenance and emergency procedures are present and adequate.
- For new/modified facilities, a MOC procedure had been followed, and all HAZOP recommendations have been implemented before startup.
- Training of each employees involved in operating a process has been completed.
PSSR is the last step in the commissioning process and is managed by the commissioning manager and the client commissioning team jointly. Vendors and licensors may join PSSR. Completion of PSSR and compliance of all its punch points will validate the facility/system for its readiness and to commence safe startup. ( Download: Pre-Startup Safety Review Checklist (PSSR) )
9. Plant Startup
Plant startup is the phase where the entire plant, all systems, and subsystems are taken into operation, process fluids are introduced, and process conditions are established with the intent of making products. For continuous startup activities, employees must be assigned to work shift duties so that client, the contractor, and some vendors and licensors should be available 24×7. A shift logbook with clear instructions for its filling should be specified before starting the plant.
Once again assure the compliance of punch points of PSSR and ensure the pre-startup checklist by a tick mark on it step by step. Checks are;
- Whether all utilities available for safe startup
- Whether feed is available
- Whether enough product storage available
- Whether all involved startup team members are well aware about different startup procedures
- Pipe and equipment purging procedure
- Pipe and equipment evacuation procedure
- Procedure for Initial introduction of feed and chemicals
- Procedure for initial heating or cooling
- Procedure for loading catalyst or other media into initial conditions
- Startup sequence with normal operating data
- Procedure for plant operating under normal conditions
- Procedures for shutdown
- Procedures for emergency shutdown
- Procedure for simultaneous operation
Ensure implementation of proper interfaces, i.e. operations and maintenance, product quality control by the company with quality control laboratory analyses, production planning by the company, and emergency response for contractors, security, and safety together by company and contractor. Similarly, maintenance support by the company and on-duty technical support managed by the contractor and the licensure. Where required, the process licensor supervises the start-up of relevant systems and provides technical assistance. Process operating parameters and conditions will be advised by the process licensor and process engineers.
All process parameters and data must be maintained which would be most useful for the next phase i.e initial operation phase. After finishing of a successful startup, the plant is ready for initial operation.
10. Initial operation
Initial operation means the entire plant is running in continuous operation, fine-tuned, and prepared for the performance test. The most important things are fine-tuning control loops, completing processes, and testing operational limits. Check the limit that the emergency shutdown starts and observe that the emergency shutdown is working well. Maintain all important data related to equipment, relevant processed data, and as well performance data. This will help for the next stage i.e. performance tests.
Still successful completion of initial operation stage, licensor involvement may be there as per requirement for relevant systems to provide technical assistance and may advise for process operating parameters and conditions.
11. Performance test for validating plant intend
Performance testing validates the plant that it is operating according to design intent. Performance testing includes facility operation and performing numbers of specified activities, demonstrations, and tests to measure the new plant and equipment against the approved project design and specified parameters.
Time duration for performance tests varies from plant to plant and as well type of industry to industry. A simple water treatment plant may finish a performance test within a 24 hours’ time period or 48 or 72 hours but other large plants or complicated plants like oil refining units with numbers of trains may take a month or several months because each train will be run step by step then all trains should be run simultaneously/ together. Shift duties must be assured for continuous monitoring and observing the performance trend. If at a certain period, the performance test gets fail, then licenser intervention is required. It is good practice to have/ maintain a separate logbook by the client and the contractor and totally with each other to detect any error. Performance tests procedures must be ensured by both the party and follow the same agreed sequence.
During the performance test below activity should be ensured by both client and contractor;
- Quality control
- Production planning
- Emergency response
- Security and safety together
- Maintenance and technical support
- Supervision and monitoring of process parameter.
- Recording of all readings
- Install an additional measurement device if existing is not adequate.
- Comparison of process data with specifications
- Maintain shift book
- Monitor the DCS system
- Sampling of products and lab analysis
- Analysis and assessment of performance test parameters
If all performance parameters are matching with project intended parameters, then we will have a final acceptance. Generally, performance test data requires about two to three weeks for evaluation by the client contractors and the licenser. If it is satisfactory then final acceptance i.e. cares, and custody is transferred from the contractor to the client and this is called project plant handover. A satisfactory result of the performance test may result in the official handover of the plant and proves that the commissioning team has fulfilled the obligations. But there may be a minor punch list that is to be attached with the final acceptance certificate.
12. Post commissioning
Post commissioning is the phase after handing over of plant to the client. Handing over to the client means the final acceptance certificate is now signed by the client and operations assistance is not needed anymore.
Outstanding punch points are solved, and some adjustments, modifications, and fault corrections are completed. Also, some routine maintenance checks and performance findings are being evaluated and monitored for process equipment and items covered under warranty.
Problems and operating data are being collected and evaluated to ensure consistent plant operations. Here contractor commissioning team who was involved in the commissioning process will stay and be responsible for solving the outstanding punch points and solving any troubleshooting. As these commissioning peoples are having experience of this particular plant, they know everything, where to go for which particular problem, what will be the solution for particular deviations, etc. After a few weeks or months as per the project agreement, one or two persons may stay along with the client and they will be responsible and coordinate for production planning, operations, maintenance, product quality control, emergency response, etc. Licensor may also stay there as per project agreement for technical guidance on process parameters.
Conclusion:
This is the difference between pre-commissioning and commissioning – the difference of testing equipment individually versus testing a group of equipment as a subsystem. Sometimes tests can be classified slightly differently from project to project, and classification as one or the other is not too critical. It is most important that no tests are skipped.
Some projects may try to skip pre-commissioning tests and go straight to commissioning, this always leads to problems. For example, if the debris remains in mechanical piping, flow rates will not be as expected, and guaranteed that more time will be required to disassemble piping, remove the debris, then continue with commissioning tests. Skipping tests in the process rarely results in saved time. A properly planned and executed commissioning sequence will include all pre-commissioning and commissioning tests required to demonstrate a properly functioning system.
Safe commissioning of any new facility or modified facility can be achieved successfully by proper commissioning planning, well-organized team framework, proper coordination between client, contractor, vendors, and licensor, ensuring availability of Manual and procedures, security and safety system, well-developed data entry formats and checklists, logbook and other records, etc. Compliance with the Safety management system and proper coordination between different disciplines are the key areas for safe and successful commissioning of the project, where the operational facility is adjacent to a new project.
Read more: Accident-Incident Investigation Technique guideline