Understanding Designated Hot Work Areas: Key Definitions and Safety Requirements
7 min readIn the high-risk environments of gas plants and construction sites, ensuring the safety of workers is paramount. One critical aspect of maintaining a safe work environment is understanding and properly managing designated hot work areas. Hot work, including activities such as welding, cutting, and grinding, poses significant hazards due to the presence of ignition sources, flames, and sparks. This blog post aims to provide a comprehensive guide to the key definitions and safety requirements related to designated hot work areas, equipping you with the knowledge to mitigate risks and enhance workplace safety.
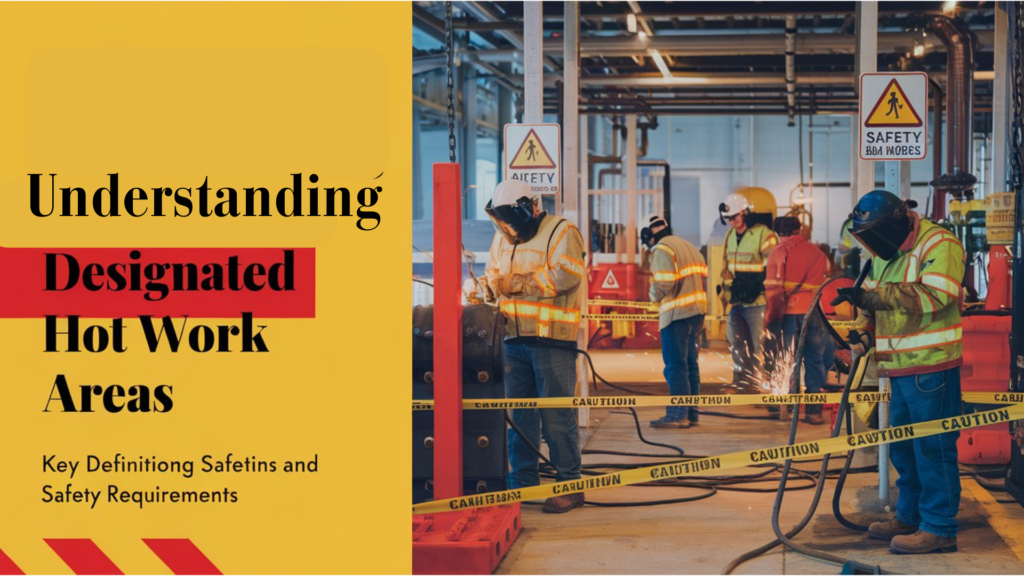
Introduction to Designated Hot Work Areas
Designated hot work areas are specific zones established to safely perform tasks that can ignite fires or cause explosions. These tasks include welding, cutting, grinding, and brazing. The areas are equipped with:
- Fire-resistant barriers
- Proper ventilation
- Fire detection systems
Personnel must follow strict protocols:
- Wear personal protective equipment (PPE).
- Implement fire watch procedures.
- Use fire extinguishers and emergency alarms.
Authorities should regularly inspect these areas to ensure compliance. By adhering to these guidelines, risks can be minimized, safeguarding both personnel and property from potential hazards.
Importance of Designated Hot Work Areas in Industrial Settings
Designated hot work areas play a critical role in maintaining safety in industrial environments. These areas are specifically designed to manage the risks associated with tasks that generate heat, sparks, or flames. Properly designated zones help prevent accidents by:
- Containing potential hazards: Isolating hot work processes reduces the risk of fires and explosions.
- Enhancing control measures: Increased monitoring and safety protocols ensure thorough adherence to safety standards.
- Minimizing exposure: Protecting other operations and personnel from the risks associated with hot work.
- Compliance with regulations: Meeting legal and industry-specific safety requirements.
Key Definitions Related to Hot Work
Hot work involves activities that could generate heat, sparks, or flames.
- Hot Work: Any task involving open flames, sparks, or high heat that poses a fire risk.
- Designated Hot Work Area: A specific location designed and approved for hot work operations due to its safety measures.
- Hot Work Permit: An authorization document ensuring all safety protocols are followed during hot work activities.
- Fire Watch: Personnel assigned to monitor the hot work area for any fire risks both during and after operations.
- Combustibles: Materials capable of igniting and burning; common examples include paper, wood, and certain chemicals.
Common Types of Hot Work and Their Risks
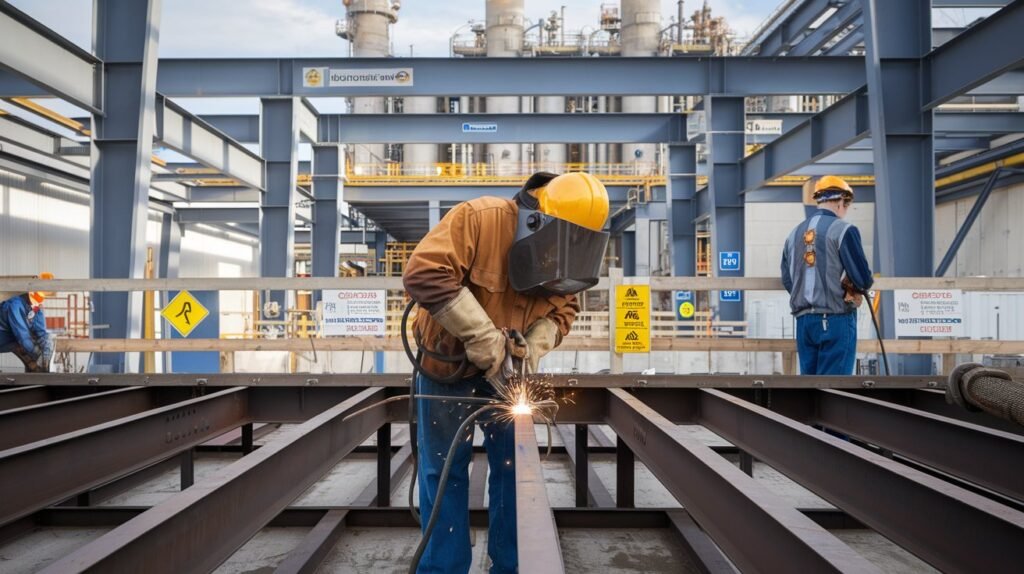
- Welding:
- Risks: Fire, explosion, toxic fumes, electric shock.
- Cutting:
- Risks: Sparks, flying debris, burns, eye injury.
- Brazing:
- Risks: Exposure to heat, chemical exposures, burns.
- Grinding:
- Risks: Flying particles, noise-induced hearing loss, fire.
- Soldering:
- Risks: Exposure to lead fumes, burns.
Hot work operations necessitate stringent safety controls to mitigate inherent risks.
- Heat Treating:
- Risks: High temperatures, toxic emissions, burns.
- Torch-Applied Roofing:
- Risks: Fire hazards, toxic smoke, falls.
- Thawing Pipes:
- Risks: Fire, electric shock, burns.
Safety Requirements for Designated Hot Work Areas
To ensure safety during hot work activities, several critical requirements must be met:
- Fire-Resistant Barriers: Install barriers to contain sparks and prevent fire spread.
- Ventilation: Provide adequate ventilation to disperse fumes and smoke.
- Fire Safety Equipment:
- Fire extinguishers
- Fire blankets
- Personnel Training: Ensure workers are trained in fire safety and hot work procedures.
- Emergency Protocols: Establish clear emergency response protocols.
- Permits: Obtain necessary hot work permits before commencing activities.
- Frequent Inspections: Conduct regular inspections of the area’s safety measures.
These measures collectively mitigate risks and safeguard personnel and property.
Read: Hot Work Controls and its Permit to work Form
Essential Safety Equipment for Hot Work
Ensuring safety during hot work requires specific equipment. Every designated area should be equipped with:
- Fire Extinguishers: Suitable for the types of fires that may occur.
- Fire Blankets: For smothering small fires quickly.
- Protective Clothing: Including flame-resistant gloves and aprons.
- Respirators: To protect against inhalation of harmful fumes.
- First Aid Kits: Fully stocked and easily accessible.
- Fire Watch: Personnel trained to identify and extinguish fires.
- Ventilation Systems: To remove fumes and maintain air quality.
- Signage: Clear instructions and hazard warnings displayed prominently.
Safety depends on proper use and maintenance of this equipment.
Video: Preventing Fires During Hot Work Operations
Training and Certification for Hot Work Personnel
Ensuring that personnel conducting hot work are adequately trained and certified is critical. Training programs should cover:
- Understanding Hot Work Hazards: Identifying potential fire and explosion risks.
- Proper Equipment Handling: Safe operation and maintenance of hot work tools.
- Emergency Procedures: Steps to take in case of an incident.
- Fire Watch Duties: Responsibilities during and after hot work activities.
- Personal Protective Equipment (PPE): Proper use of PPE to prevent injuries.
Certification should include:
- Formal testing of knowledge.
- Practical evaluations.
- Periodic re-certification to ensure continued competence.
- Awareness of relevant regulations and standards.
Establishing and Maintaining a Hot Work Permit System
To establish and maintain a hot work permit system, several key steps must be followed:
- Risk Assessment: Perform a risk assessment to identify potential hazards associated with hot work activities.
- Permit Issuance: Designate qualified personnel to issue permits, ensuring that all safety measures are addressed.
- Training: Provide comprehensive training for employees involved in hot work operations.
- Monitoring: Implement continuous monitoring to ensure compliance with safety requirements.
- Record Keeping: Maintain accurate records of all issued permits and associated safety checks.
- Review: Regularly review and update the permit system to incorporate new safety standards and practices.
Case Studies: Incidents and Lessons Learned
Incident 1: Warehouse Fire
A warehouse fire caused millions in damages. Hot work was conducted without a fire watch. Lack of sufficient fire-retardant barriers. The nearby flammable materials caught fire quickly.
Lessons Learned:
- Always have a fire watch present.
- Ensure fire-retardant barriers are used.
- Maintain distance from flammable materials.
Incident 2: Oil Refinery Explosion
An explosion occurred during pipe welding. Incomplete inspection of the workspace. Gas leaks present were not detected.
Lessons Learned:
- Conduct thorough pre-work inspections.
- Use gas detection equipment.
- Train personnel on hazard identification.
Incident 3: Shipyard Welding Accident
A worker sustained burns due to welding in a confined space. Lack of proper ventilation and PPE.
Lessons Learned:
- Ensure adequate ventilation.
- Provide appropriate PPE.
- Train in confined space protocols.
Best Practices for Enhancing Safety in Hot Work Areas
- Conduct Thorough Risk Assessments: Identify potential hazards before initiating any hot work activity. Use checklists and risk matrices to document findings.
- Implement Control Measures: Use physical barriers, guards, and fire-resistant materials to mitigate identified risks. Ensure that fire extinguishers and suppression systems are readily available.
- Provide Proper Training: Ensure that all personnel are trained in hot work safety, including emergency response procedures. Regular refresher courses should be mandatory.
- Maintain Cleanliness: Keep the work area free of flammable materials and debris. Regular housekeeping should be enforced.
- Monitor Atmospheric Conditions: Utilize gas detectors to monitor for the presence of combustible gases or vapors.
- Assign a Fire Watch: Designate a trained individual to oversee the hot work process and promptly respond to any fire hazards. This individual should have no other duties.
Read: E-Books: Hot Work on Drums and Tanks(Opens in a new browser tab)
Regular Audits and Inspections: Ensuring Compliance
Regular audits and inspections serve as critical mechanisms for maintaining compliance in designated hot work areas. They help identify potential hazards and enforce standardized safety protocols. Key procedures include:
- Scheduled Audits: Conducted periodically to review safety practices and document adherence to guidelines.
- Random Inspections: Unannounced checks to ensure ongoing compliance with safety regulations.
- Training Reviews: Assessment of staff knowledge about hot work protocols.
- Incident Analysis: Review of past incidents to prevent future occurrences.
- Equipment Checks: Verification that all safety equipment is functional and up-to-date.
By implementing these measures, organizations can significantly reduce risks associated with hot work activities.
Developing an Emergency Response Plan for Hot Work Incidents
Developing an emergency response plan for hot work incidents is vital for maintaining safety.
Steps to follow:
- Risk Assessment:
- Evaluate potential hazards.
- Identify vulnerable areas and personnel.
- Establish Communication Protocols:
- Document chain of command.
- Ensure all workers know emergency contact information.
- Prepare Emergency Equipment:
- Provide fire extinguishers, first-aid kits.
- Install smoke detectors, alarms.
- Training and Drills:
- Conduct regular training for workers.
- Simulate emergency scenarios periodically.
- Post-Incident Review:
- Analyze the response effectiveness.
- Implement improvements for future readiness.
Ensuring these measures helps mitigate risks associated with hot work activities.
Technological Advances in Hot Work Safety
Technological innovations have significantly enhanced hot work safety measures. Key advancements include:
- Automated Monitoring Systems: Sensors and cameras continuously detect and alert personnel to potential hazards.
- Wearable Safety Devices: Smart helmets and wearables monitor worker health and environmental conditions.
- Fire-Resistant Materials: New fire-retardant fabrics improve protective gear.
- Digital Safety Training: Virtual reality (VR) and augmented reality (AR) offer immersive training experiences.
- Integrated Safety Management Systems: Software platforms centralize safety data, facilitating real-time decision-making.
- Advanced Ventilation Solutions: Improved airflow systems reduce inhalation of harmful fumes.
These technologies collectively enhance the safety and efficiency of hot work operations.
Conclusion: The Future of Hot Work Safety Management
As technology advances, so do the methods and tools for managing hot work safety. The integration of smart sensors can provide real-time monitoring of environmental conditions, swiftly detecting any dangerous fluctuations. Digital reporting systems may replace paper logs, streamlining the documentation process.
- Enhanced Training Programs: VR-based simulations could offer safer, immersive training experiences for workers.
- Automated Compliance: AI-driven platforms can ensure adherence to safety regulations by automatically updating protocols.
- Remote Monitoring: IoT devices could allow safety managers to oversee multiple designated hot work areas simultaneously.
Investing in these innovations will ensure safer, more efficient hot work environments.
Templates:Hot Work ٍSafety Program