Safety Program for Working at Heights
8 min readWhen you stop and think about it, you might be surprised to realize how many of the things you do in everyday life would require the application of a fall protection program if it were done at work. You probably don’t strap a safety harness to your body when cleaning the snow off your roof in the winter or replacing the shingles in the summer, but those elevations would require PPE and other safety measures in an occupational setting.
Employees working from an unprotected elevation starting at 6 feet or more must use fall protection equipment, whether they are traveling or stationary. The 6-foot fall distance is measured from the employee’s feet to the walking and working surface below. This applies to unprotected sides and edges, leading edges, hoist areas, holes and floor openings, formwork and reinforcing steel, excavations, roofing work, precast concrete erection, and other walking-working surfaces.
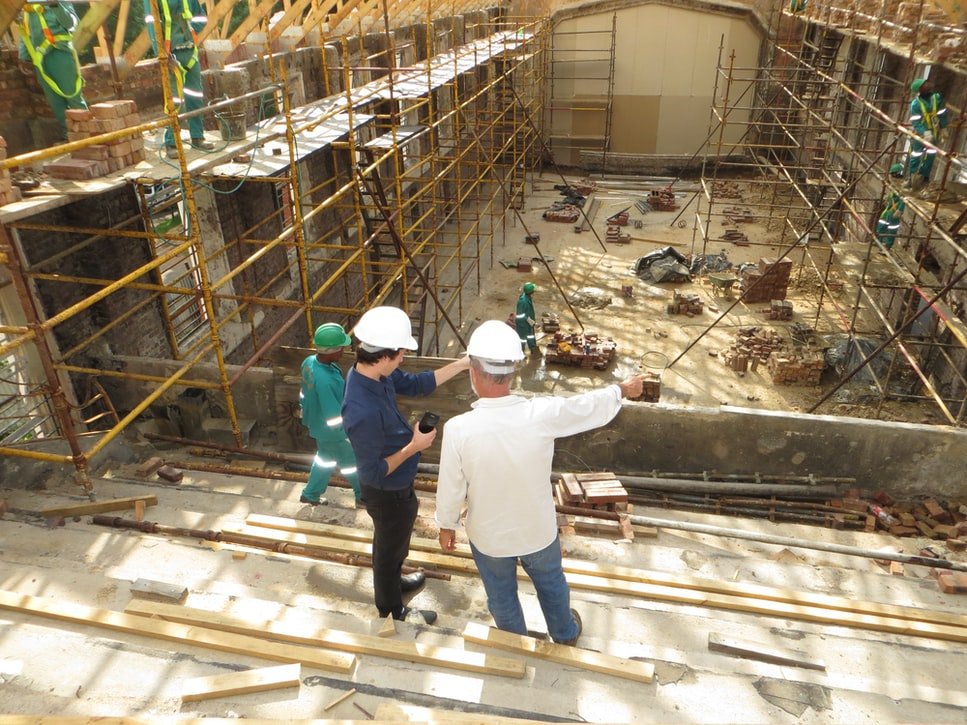
There are different control methods that can be employed to deal with fall hazards. These come in the form of fall prevention systems and they include guardrail systems, scaffolds, aerial lifts, barricades, and hole covers. Other fall protection measures include the use of personal fall arrest systems and safety net. You will also need to provide protection from falling objects and slips and trips from the same level. The use of “controlled access zones” is not permitted.
Now, with those preliminaries out of the way, let’s dive in and look at the elements you might have to include in your workplace’s fall protection program.
Planning
Your planning will include:
- Identifying potential fall hazards
- Using design safety to eliminate or control possible fall exposure
- Determining the appropriate method of protection
- Supplying anchorage
- Providing education, training, and enforcement
- Arranging for rescue and rescue equipment
- Walking/working surfaces not otherwise addressed
The Hierarchy of Fall Hazard Control
Fall hazard control measures should be initiated in the following order.
Design Safety and Engineering Controls
“Design out” or “engineer out” fall hazards by:
- Reviewing drawings and interacting with fabricators and material suppliers to design safety features into the structure, material, or equipment to be used
- Maximizing the use of prefabricated modular units
- Adding stairways and platforms that can be used for access both during construction and maintenance operations
- Designing elevated structures with connecting points to secure retractable devices and other anchorage connectors
Fall Elimination
Eliminate work at elevation by:
- Performing work on the ground when possible
- Attaching guardrail protection to forms and work platforms while on the ground
- Attaching fall arrest systems to formwork, bridge steel, and other structural components before erection
- Using ground release devices to disconnect rigging from the ground
- Maximizing the pre-assembly of formwork, structural steel, pipe, and other components
Fall Prevention
Prevent falls at elevation by using:
- Guardrail systems
- Scaffolds
- Aerial lifts
- Fall restraint
- Hole and floor covers
Fall Protection
None of those other control methods are perfectly effective. Even with them in place, an employee might still fall. When they do, their fall arrest system will protect them. These systems include harnesses, lanyards, anchorage connectors, self-retracting devices, and more.
Note, however, that these are the least desirable method of protection because they only minimize the consequences of a fall rather than prevent its occurrence, and they also rely on human behavior to prevent injury.
Guardrail Protection
Designate work locations requiring guardrail protection include:
- Elevated work platforms, such as on formwork
- Scaffolds
- Openings or holes in bridge decks, floors, roofs, or other unprotected surfaces
- Unprotected sides of ramps/stairways/platforms
- Leading edges
- Edges of bridge surfaces, buildings, floors, roofs, and slabs
- Ladderway floor openings
- Pits and trap door openings that are left uncovered
- Manhole floor openings
- Unprotected elevator shaft openings
(For related reading, see When your Job takes you to the Leading Edges)
Fall Protection Plans
A fall protection plan must specify:
- The fall hazards at the worksite
- A fall protection system to be used at the worksite
- Procedures used to assemble, maintain, inspect, use, and disassemble the fall protection system
- Rescue procedures to be used if a worker falls is suspended by a personal fall arrest system or safety net and needs to be rescued
- The employer must ensure that the fall protection plan is available at the worksite before work with a risk of falling begins
Fall Prevention System Requirements
Guardrail Systems
All work areas, walkways, and platforms that are more than three feet above ground level or the platform below should be equipped with solid guardrails, both upper and intermediate. Rope or tape is insufficient.
Guardrail systems must be surfaced in a way that prevents injury from punctures and snagging of clothes.
Guardrail systems used around holes should be erected on all the unprotected sides and edges of the holes. If the hole is a point of access, such as a ladderway, install guardrails on all sides except at the entrance of the opening. That entrance should be protected instead by a swing gate, barrier, or offset to prevent people from walking directly into the opening.
Plan regular inspections for damage and proper construction. When you locate a damaged guardrail, replace it immediately.
Protection from Falling Objects
Protect workers and equipment from falling objects by using toe boards, screens on guardrail systems, hole covers, tool tethers, barricades, and canopy structures.
Barricade the area to which objects could fall, and prohibit employees from entering that area.
(Find out: fall protection five hazards many workers aren’t aware of/)
Fall Protection Equipment Requirements
General Requirements
A complete fall arrest system will include:
- Proper anchorage
- Body harness
- Connecting device (lanyards or lifelines)
All will be properly rigged to arrest a free fall.
Anchorage
Anchorage planning is the key to designing effective fall arrest systems. Anchorage requirements include:
- Strength – Anchors must be capable of supporting 5,000 lbs (22.2 KN) per employee or twice the anticipated force and designed by a Qualified Person
- Independence – Anchors must be independent of the work platform, guardrail system, or surfaces and structures supporting employees
- Location – Anchors should be located overhead to minimize free fall distance
- Clearance – Calculate the total fall distance to ensure anchorage height is sufficient to prevent collision with any object or the ground and does not create a swing fall hazard
- Identification – Anchor points should be pre-planned and clearly identified to employees
(Find out How to Choose Your Fall Protection Anchorage)
Full-Body Harness
Full-body harnesses should be issued to all employees who may be exposed to fall hazards. They should also be inspected regularly for wear, abrasion, broken stitching, and missing hardware.
Full-body harnesses must fit and be worn properly with the straps tucked away so they don’t get caught on equipment or otherwise cause a hazard.
Snap Hooks
Only self-closing, self-locking snap hooks are allowed for fall protection use. Snap hooks must open and close properly and be fully closed around their anchorage point.
Lanyards
Always use the shortest possible lanyard length. Lanyards should limit the free fall distance to no more than six feet.
Lanyards must be used with a shock absorber unless the fall distance is shortened enough to limit the fall force to 1,800 lbs.
In some situations, dual or “Y” lanyards may be needed to achieve sufficient fall protection.
Retractable Devices and Self-Retracting Lifelines
Retractable devices are designed to arrest a fall within two feet. They should only be attached to fixed overhead anchorage.
To reduce the risk of a swing fall, retractable devices should be at less than a 45-degree angle when attached to the anchor point.
Vertical Lifelines
Vertical lifelines may only be used by one employee at a time.
They must be equipped with a formed eye termination at one end for suspension from the anchor point and must extend below the lowest level of travel. The lower end must either be attached to a second anchor point or weighted to provide stability and tension.
Vertical lifelines used on rope grab systems require additional clearance distance considerations, including lifeline stretch.
(learn: How to calculating fall arrest distance with 4 steps).
Horizontal Lifelines
Horizontal lifeline systems must be designed by a Qualified Person and installed and used under the supervision of a Qualified Person.
Horizontal lifeline systems require additional clearance distance considerations that include the lifeline deflection and elongation associated with cable sag during loading and (when applicable) the use of an in-line energy absorber.
Intermediate stanchions and posts should have a hands-free pass-through feature to eliminate the need to disconnect.
Horizontal lifelines should be located overhead to minimize the fall distance and to provide sufficient fall clearance distance.
Rescue
Site management must ensure that personnel can be promptly rescued or self-rescue themselves in the event of a fall.
Evaluate ahead of time the availability of rescue personnel, aerial lifts, ladders, and any other rescue equipment or services that would be needed.
(Learn more in Who should be responsible for rescuing fallen workers/)
Elevating Equipment
Employees are required to wear full-body harnesses and be tied-off 100% of the time when operating aerial lifts and scissor lifts.
Crane-suspended personnel work platforms should only be used as a last resort.
Housekeeping
Housekeeping tasks should be performed routinely and regularly.
Their purpose is to keep walking and working areas free of debris, materials, and equipment.
(Learn more in Worksite Housekeeping Basics )
Equipment Storage
Fall protection equipment must be stored in a clean, dry location away from exposure to abrasive materials, cutting tools, excessive heat, direct sunlight, and chemicals.
Full-body harnesses should be hung by the D-ring for storage.
Equipment Inspection
Fall protection equipment must be inspected by the user prior to each use.
Designate a Competent Person to conduct inspections of Jobsite fall protection equipment. These inspections should be conducted at least quarterly, although monthly inspections are preferable. Document the results of each inspection.
Some types of fall protection equipment, such as self-retracting lifelines, require periodic re-certification by the manufacturer at scheduled intervals.
Any piece of fall prevention or fall prevention equipment that is found to be defective must be removed from service immediately, tagged as defective, and repaired, replaced, or discarded.
(Lean: how to inspect your fall harness when working alone)
Fall Protection Training
Training for fall arrest systems must include the proper use, care, and limitations of the equipment.
Training must, at a minimum, address the following areas:
- Company fall protection policy
- How to evaluate fall hazards
- Fall prevention measures
- Equipment use, care, and limitations
- Proper fitting and wearing of fall protection equipment
- Requirements and proper use of anchor points
- Equipment inspection
All fall protection training must be documented. Documentation must be signed and dated by the employee and instructor and maintained in the employee’s safety training record.
Conclusion
There are strict guidelines that need to be followed when employees are working at heights. Employers need to ensure that everyone working at heights understand the hazards they face and how to control them. Planning, preparation, and communication will keep employees safe, and that’s why a comprehensive fall protection program is essential.
The information provided in this article will get you started but remember that your fall protection program needs to take into account all the features of your workplace or Jobsite. Assess the hazards and features of the work environment and make sure they’re all taken into account.
For More safety resources please visit: SAFETY BAG