Road Work’s Hazards and the controls
12 min readMany Contractors work on road works, which has a high variety of hazards and therefore a high amount of risk.
What are the risks?
Under the Health and Safety at Work Act, every business has a responsibility to ensure, so far as is reasonably practicable, the health and safety of workers, and that others are not put at risk by the work of the business (for example, customers, visitors, children, and young people, or the general public).
First, you must always eliminate the risk where you’re reasonably able to. Where you’re not reasonably able to, then you need to consider what you can do to minimize the risk.
The following are examples of only some of the health and safety risks for people in the road works sector.
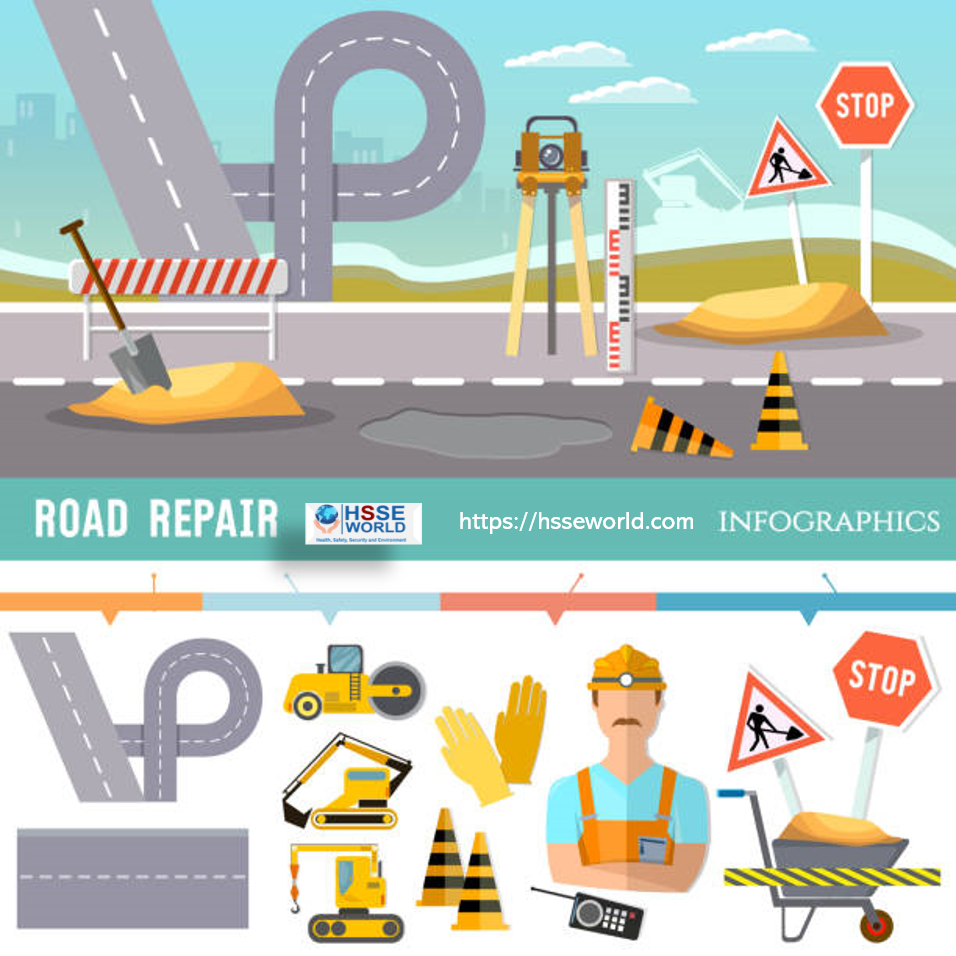
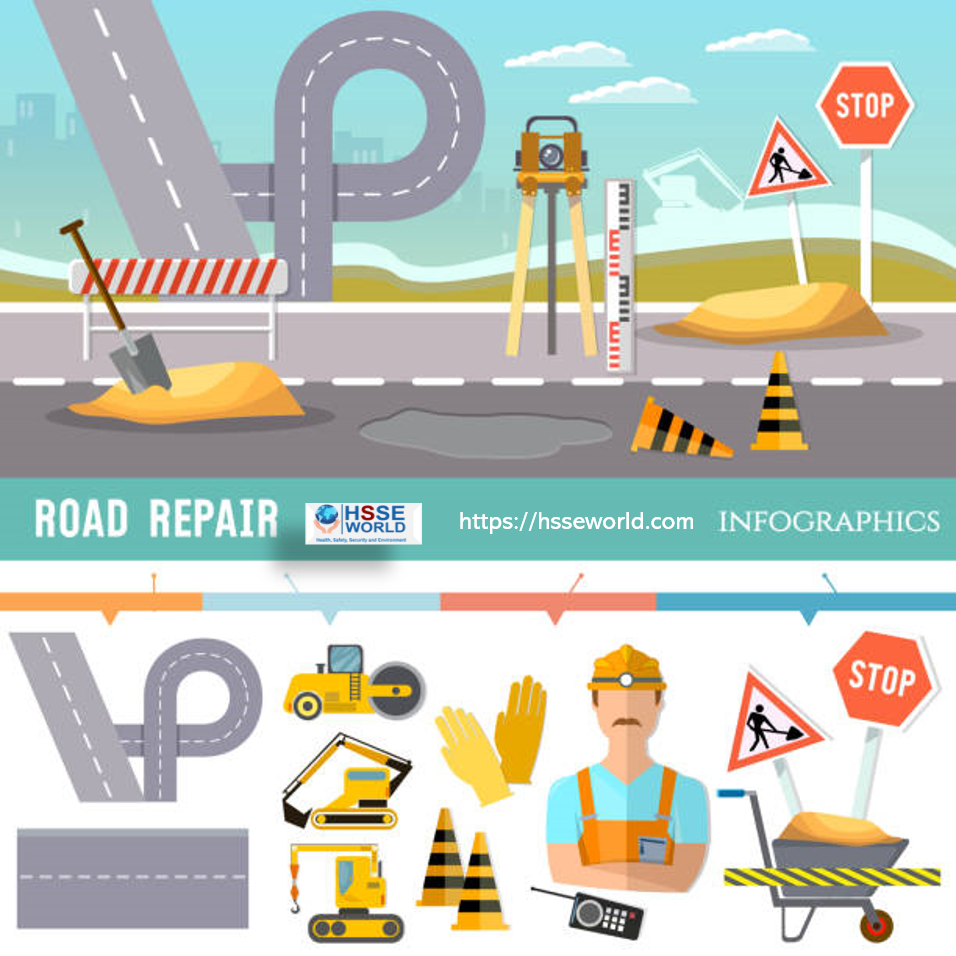
Noise
Constant exposure to noise from tools and machinery can put workers at risk of permanent hearing damage.
How are workers and others harmed?
Loud machines and work tools can affect a workers’ hearing. Hearing loss can also result from sudden loud noises, heavy loads being dropped, or heavy hammering. These types of noises are referred to as ‘impact’ noises and, if loud enough, can cause immediate and permanent damage. If you are working within a meter of someone and you have to shout to be heard, then it’s likely that the noise level is excessive.
What can you do?
First, you must always eliminate the risk where you’re reasonably able to. Where you’re not reasonably able to, then you need to consider what you can do to minimize the risk. Here are some examples:
- Ensure workers are not exposed to noise that exceeds the exposure standard.
- Arrange for a noise assessment if workers are exposed to excessive noise (for example, workers have to raise their voices to communicate over a distance of one meter) and there is uncertainty as to whether workers’ exposure may have exceeded the noise exposure standard.
- Eliminate or minimize the source of the noise. Use noise-insulated equipment (for example, silence compressors), enclose or isolate noisy machinery, reduce vibration, use barriers to absorb and screens to block the direct path of sound, use silencers on air exhausts, exhaust pneumatics out of the area, and where appropriate the quietest tools/machinery available.
- Place warning signs in areas of excessive and continual noise (ie where workers’ exposure is likely to exceed the exposure standard).
- Warn other workers nearby when you will be undertaking noisy work and advise them to move away or wear hearing protection.
- Provide hearing protection and ensure it is worn at all times, and provide workers with audiometric testing. People should provide a choice of different types of hearing protection appropriate to the noise level of work.
- Always ask workers for input on identifying health and safety risks, and when choosing solutions. People are more likely to take responsibility and make good choices if they’ve been involved in the conversation. Workers are the eyes and ears of your business. They know where the health and safety pressure points are, and can suggest practical, cost-effective solutions.
- Always train new workers on what the risks are and how to keep them healthy and safe.
- Make sure workers know how to make suggestions, raise questions or concerns.
Always ask workers for input on identifying health and safety risks, and when choosing solutions. People are more likely to take responsibility and make good choices if they’ve been involved in the conversation. Workers are the eyes and ears of your business. They could suggest practical, cost-effective solutions.
You need to select the most effective control measures that are proportionate to the risk, and appropriate to your work situation.
(Learn More:occupational-noise-hearing-conservation-basics/)
Fumes
Vapour, gas, and other fumes from materials can put workers and the public at risk.
How are workers and others harmed?
Road work can produce a range of fumes, depending on the worksite and the materials used. These include but are not limited to:
- asphalt
- diesel fumes.
Exposure to these and other fumes is dangerous and can cause serious lung disease.
What can you do?
First, you must always eliminate the risk where you’re reasonably able to. Where you’re not reasonably able to, then you need to consider what you can do to minimize the risk. This might mean doing a job differently or using a less toxic material. Here are some other examples to consider:
- Reduce the risk of exposure to fumes by improving ventilation.
- Use water suppression to control dust.
- Use administrative measures such as adequate health and safety training, instructions and information to workers, appropriate supervision, good personal hygiene, and good housekeeping.
- Schedule work for a time when fewer people are present.
- Post warning signs.
- Ensure safe work procedures are clearly displayed.
- Provide workers with the appropriate personal protective equipment (PPE) such as respirators, gloves, footwear, eyewear, and protective clothing. Test PPE and make sure it’s working properly.
- Ensure workers have been trained on how to properly use PPE.
Always ask workers for input on identifying health and safety risks, and when choosing solutions. People are more likely to take responsibility and make good choices if they’ve been involved in the conversation. Workers are the eyes and ears of your business. They could suggest practical, cost-effective solutions.
You need to select the most effective control measures that are proportionate to the risk, and appropriate to your work situation.
(learn more:Respiratory-protective-equipment-rpe-guideline/
Vibration
Permanent injuries to blood vessels, nerves, and joints can be caused by repeated vibrations from power tools or vibrating surfaces.
How are workers and others affected?
Power tools send vibrations through the hands and arms. Vibrating surfaces, where a worker sits or stands, can send vibration throughout the whole body.
Other factors that can increase the likelihood of vibration injury include:
- working in cold, damp conditions
- increased grip force
- using power tools for extended periods of time.
What can you do?
First, you must always eliminate the risk where you’re reasonably able to. Where you’re not reasonably able to, then you need to consider what you can do to minimize the risk. Here are some examples questions and actions to consider:
- Can workers use tools that generate less vibration?
- Can seating be improved and/or cushions provided?
- Can matting be installed?
- Can a process be used that generates less vibration?
- Can you limit how long a worker performs a task? Can job rotation be used?
- Can you schedule frequent breaks for workers?
- Do workers have vibration-dampening personal protective equipment (PPE) such as gloves and hand tool wraps? Is the PPE effective in reducing exposure to vibration?
Always ask workers for input on identifying health and safety risks, and when choosing solutions. People are more likely to take responsibility and make good choices if they’ve been involved in the conversation. Workers are the eyes and ears of your business. They could suggest practical, cost-effective solutions.
You need to select the most effective control measures that are proportionate to the risk, and appropriate to your work situation.
Bullying
Bullying harms workers and is a significant issue in New Zealand. It can affect people both physically and mentally, can disrupt workplaces, and lower work performance. Bullying can happen at any time and at all levels in a business.
How are workers and others harmed?
Bullying at work is repeated and unreasonable behavior towards a worker or group of workers that can lead to physical or psychological harm. Bullying can be physical, verbal, or social.
Some of these behaviors may also fall under other types of behavior such as discrimination or violence.
What can you do?
First, you must always eliminate the risk where you’re reasonably able to. Where you’re not reasonably able to, then you need to consider what you can do to minimize the risk.
For example, building good relationships in a respectful work environment including having a ‘no-bullying tolerated’ work culture.
Always ask workers for input on identifying health and safety risks, and when choosing solutions. People are more likely to take responsibility and make good choices if they’ve been involved in the conversation. Workers are the eyes and ears of your business. They could suggest practical, cost-effective solutions.
You need to select the most effective control measures that are proportionate to the risk, and appropriate to your work situation.
Slips, trips, and falls
Lack of signage, lighting, or barriers can put workers, pedestrians, cyclists, and other road users at risk of slip, trip, and fall injuries.
How are workers and others affected?
When someone falls as a result of a slip or trip, the injury can range from minor (bruises and scrapes) to more serious, including broken bones or head trauma. The severity of the injury will depend on the circumstances.
Examples of how injuries can be caused include:
- a person could fall into an uncovered manhole or excavation
- uneven or damaged pavement or road
- trailing cables.
What can you do?
First, you must always eliminate the risk where you’re reasonably able to. Where you’re not reasonably able to, then you need to consider what you can do to minimize the risk. Here are some examples:
- Keep work and storage areas tidy.
- Use barriers to keep people away from holes and other hazards.
- Ensure the underfoot conditions for designated walkways are good, well signposted, and adequately lit.
- Use mechanical lifting aids rather than carrying heavy or unwieldy loads that obstruct the view ahead.
- Ensure workers wear appropriate footwear with good grip.
- Plan deliveries to minimize the number of materials on site.
- Have designated areas for waste collection, and provide skips and bins. Make sure everyone knows who is responsible for waste removal.
- Use cordless tools where possible. If you need to use cables for temporary lighting or power tools, run the cables at a high level.
- Treat slippery surfaces with stone or grit (depending on the conditions) and signpost slippery areas.
- Consider using a ramp for any changes in level or use signs to warn people to look out for a level change.
- Have well-marked road/pedestrian areas.
- Have designated crossing points.
- Implement speed management (for example, speed bumps, and signage).
Always ask workers for input on identifying health and safety risks, and when choosing solutions. People are more likely to take responsibility and make good choices if they’ve been involved in the conversation. Workers are the eyes and ears of your business. They could suggest practical, cost-effective solutions.
You need to select the most effective control measures that are proportionate to the risk, and appropriate to your work situation.
Vehicles
Moving vehicles and machinery are risky – a good traffic management plan keeps everyone safer.
How are workers and others affected?
People could be harmed by:
- being trapped between a vehicle and a structure
- vehicles colliding with each other or a structure
- being hit by a vehicle
- items that fall off vehicles (unsecured or unstable loads)
- falling from a vehicle.
Other things to take into account include:
- drivers/operators/pedestrians affected by drugs, alcohol, or fatigue.
- drivers/operators/pedestrians affected by medical events (for example, heart attacks).
- environmental conditions (for example, slippery or unstable ground, low light, fog).
- mechanical failure (for example, faulty steering or bad brakes).
- driver distractions (for example, cell phones, noise, work pressures, home pressures).
- vehicles operated outside their limits or capabilities – the wrong vehicle for the job.
- anything that might block the drivers’ view.
When a person is hit by a truck or other construction vehicle or equipment, or a vehicle or equipment hits something else, the consequences can be severe for the person and for the business. For example:
- The person may suffer crush injuries or fractures or die.
- A business may have to deal with property damage, reputational damage, service disruption, and increased insurance costs.
What can you do?
First, you must always eliminate the risk where you’re reasonably able to. Where you’re not reasonably able to, then you need to consider what you can do to minimize the risk. Here are some examples:
- Isolate vehicles and plants from people working on the site.
- Ensure reversing warning devices (for example, sounds or lights) are working
- Turn on hazard lights if the vehicle is a temporary hazard.
- Use spotters or dedicated traffic controllers to manage traffic and pedestrian movements.
- Provide adequate lighting on site so drivers, workers, and others can see what they are doing and can also be seen by others.
- Encourage drivers visiting a site for the first time to walk the route and plan how they will move their vehicle around the site.
- Consider having a policy and process for drug and alcohol screening /testing.
- To minimize driver fatigue, manage when and how long drivers work.
- Collaborate with other businesses on-site to coordinate vehicle movements.
- Where you can, have a one-way system to reduce the need for vehicles to reverse on site.
- Provide warning signs at all entrances and exits to the site.
- Ensure workers wear high visibility clothing.
Always ask workers for input on identifying health and safety risks, and when choosing solutions. People are more likely to take responsibility and make good choices if they’ve been involved in the conversation. Workers are the eyes and ears of your business. They could suggest practical, cost-effective solutions.
You need to select the most effective control measures that are proportionate to the risk, and appropriate to your work situation.
Machinery
Machinery at road working sites can create risks for workers if used incorrectly.
How are workers and others harmed?
People could be harmed from:
- workers not being trained on how to use machinery and equipment correctly.
- not wearing the correct personal protective equipment (PPE).
What can you do?
First, you must eliminate the risk where you’re reasonably able to. Where you’re not reasonably able to, then you need to consider what you can do to minimize the risk. This might mean doing a job differently or making sure you have the right equipment for the job. Here are some examples:
- All workers should be trained in the safe operation of all machinery and equipment.
- Provide workers with appropriate personal protective equipment (PPE) and ensure they have been trained on how to properly use it.
- Regularly maintain machinery, equipment, and personal protective equipment (PPE) (for example, ventilation in spray booths).
Always ask workers for input on identifying health and safety risks, and when choosing solutions. People are more likely to take responsibility and make good choices if they’ve been involved in the conversation. Workers are the eyes and ears of your business. They could suggest practical, cost-effective solutions.
You need to select the most effective control measures that are proportionate to the risk, and appropriate to your work situation.
Dust
Workers are at risk of developing lung disease from inhaling dust particles.
How are workers and others harmed?
Dust particles can permanently damage a worker’s lungs. Even after the worker is no longer exposed to dust particles, lung damage can continue to develop. Control of dust exposure is critical in minimizing risk. Providing health monitoring to workers is a legal duty and also an important part of risk management.
What can you do?
First, you must eliminate the risk where you’re reasonably able to. Where you’re not reasonably able to, then you need to consider what you can do to minimize the risk. This might mean doing a job differently or making sure you have the right equipment for the job. Here are some examples:
- Control dust by wetting work materials, work processes, and work areas with fine water mist and using an H-class HEPA-filtered vacuum cleaner when cleaning up.
- Choose equipment and machinery with good dust control and dust collection systems. If in doubt, contact the manufacturer.
- Schedule potential high-exposure work for times where there are fewer workers and others around (eg breaks or after normal working hours)
- Provide workers with appropriate personal protective equipment (PPE) and ensure their gear has been fitted appropriately. Workers must be trained on how to properly use PPE and how to store it.
- Encourage workers to leave dust-covered clothes at work to be cleaned rather than wearing them home. Workers should not be using compressed air to dust themselves down, as this simply spreads dust particles.
- Ensure workers have been trained to wash hands before eating, drinking, or smoking so that dust particles are not ingested orally.
Always ask workers for input on identifying health and safety risks, and when choosing solutions. People are more likely to take responsibility and make good choices if they’ve been involved in the conversation. Workers are the eyes and ears of your business. They could suggest practical, cost-effective solutions.
You need to select the most effective control measures that are proportionate to the risk, and appropriate to your work situation.