Prevention tips to reduce the incidence of chemical spills
Many businesses from a range of industries handle hazardous chemicals on a daily basis. Apart from the health risks posed to workers by chemical leaks and spills, these substances can also potentially harm the environment, damage equipment, and expose companies to financial losses. It’s important to understand that the size of any chemical spill is not an indicator of whether or not it is dangerous. In fact, in the instance of flammable and corrosive chemicals, smaller leaks and spills can pose just as serious a danger to health and safety as larger spills.
By taking requisite precautionary measures to mitigate the risk of a chemical spillage, businesses can ensure that they handle potentially dangerous chemicals securely in a way that protects employees and the surrounding environment.
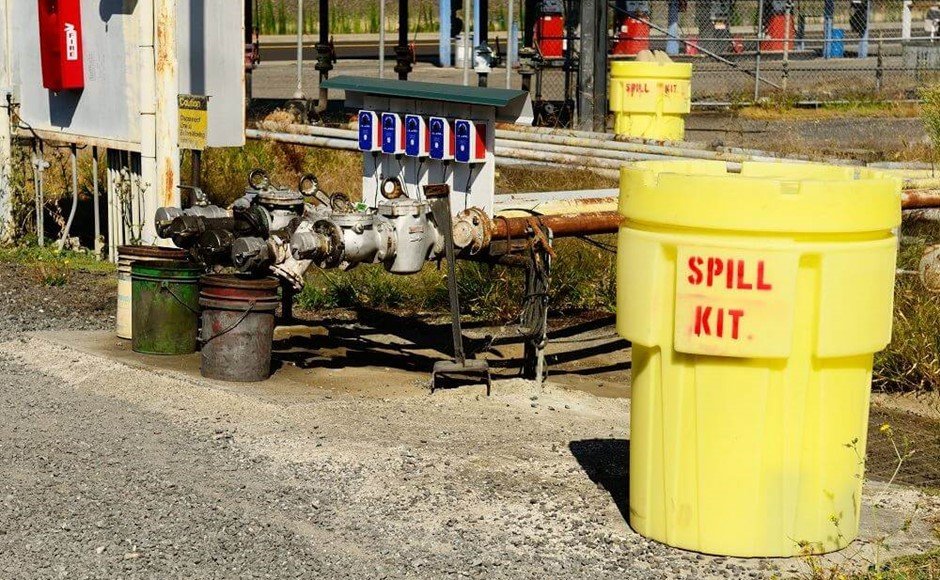
Store Chemicals in Covered Areas
Hazardous chemicals in the workplace should always be stored in covered areas where they are not exposed to rainfall. The inherent issue with rainfall is that it increases the volume of liquid that could potentially contaminate the workplace, making it more likely for spills to occur.
A chemical spill involving rainwater is also more difficult to clean simply because the spillage usually covers a larger area. By shielding all hazardous chemicals from the rain with appropriate covers, businesses can reduce the likelihood of a harmful chemical incident occurring.
Use Spill Kits, Bunds, and Spill Pallets
Spill kits should be located near areas where hazardous chemicals are stored or used in the workplace. Spill kits contain materials that rapidly absorb leaked chemicals and contain the spilled chemical, which minimizes the impact of any leak.
Spill pallets and bunds will capture and contain any spilled chemicals. Spill pallets and chemical bunds are typically fitted with a removable spill deck that prevents the containers from becoming submerged in liquids.
(see: what-is-the-difference-between-primary-and-secondary-spill-containment/).
(See flammable-liquid-storage-safety-moment ).
Store Containers on Secure Shelving
An important facet of correct chemical storage is ensuring that vessels containing harmful substances are stored on secure shelving units. Extra precautions should be taken to securely fasten any shelves used for chemical storage to a wall or floor for maximum stability. Shelves should also be fitted with raised edges, or “lips,” that help prevent chemical containers from slipping off the surface. The safe working load (SWL) should be clearly marked on each shelf.
Prevent Overcrowding in Chemical Storage Units
Overcrowding of shelves with storage containers can easily cause a chemical spill. Furthermore, storing too many containers in one area makes it difficult to identify what material is involved in a spillage, while also hampering access to the spill area for inspection and clean-up.
Ensure Chemicals Are Stored at or Below Eye Level
Chemical containers, especially heavier containers, should be placed as close to the floor as possible without coming into direct contact with it. This keeps the containers within easy reach of employees and minimizes the chances of a spill.
Storing chemicals near the floor is not always possible, so a good rule of thumb is to never store any hazardous chemicals above eye level.
Regularly Inspect Chemical Containers on Site for Leaks or Deterioration
Regular inspections of chemical containers can go a long way toward preventing a hazardous spill. Companies should pay particular attention to:
- Ensuring the exterior parts of the containers are free of any spills and stains
- Assessing screw caps and closures for any signs of deformity
- Checking that the containers show no signs of deterioration, including rust or bulges
Safeguard the Transportation of Chemical Containers
Appropriate precautions need to be taken when transporting chemical containers, including:
- Using carts suitable for the weight involved (these carts should be built with high edges to prevent spills or trays to contain them)
- Carrying any glass containers in bottle carriers
- Moving containers that contain 55 gallons or more with a functioning drum cart
- Using gas cylinder handcarts when large gas cylinders need to be transported (employees should check that the cylinders are securely strapped to the cart before transporting them)
Implement Strict Decanting Procedures
Stringent decanting procedures need to be implemented by businesses and enforced by employees to reduce the risk of harmful spills occurring and the potential for exposure (see 6-tips-to-ensure-ghs-compliance-for-smaller-down-packed-chemical-container-labels/). These procedures involve:
- Ensuring any receiving container is of adequate volume when transferring chemicals between containers to prevent overfilling
- Using pumps or other mechanical methods to transfer liquids from large containers; manual pouring is too much of a risk
- Setting up funnels and containment trays when transferring liquids to catch any leaking chemicals
- Specifically using only approved safety containers to transfer both flammable and combustible liquids
- Grounding both the drum and the receiving vessel when transferring a flammable liquid
It is surprising how quickly a chemical spill or leak can lead to a significant injury or incident. Due to their volatile nature, the manufacturing, storage, and transport of chemicals each present a number of opportunities for accidents to occur. Having a solid emergency response plan in place and established spill prevention procedures can go a long way to significantly increasing chemical safety in the workplace.