How To Improve Your Total Recordable Injury Frequency Rate on the Job Site
5 min readWork related injuries are defined as the accidents that happen in the workplace that lead to an employee’s inability to safely work the next full work day. But how can we effectively limit the number of these work injuries?
According to The National Safety Council (NSC), a worker is injured on the job every seven seconds. The NSC also states that work-related medically consulted injuries totaled 4.5 million in 2017, and total work injury costs were estimated at $161.5 billion (costs included wage and productivity losses, medical expenses, administrative expenses, motor vehicle property damage, and employer costs.)
While these numbers appear staggering at first glance, this doesn’t mean your workplace has to succumb to the deadly statistics. The answer to how you can improve your team’s total recordable injury frequency rate is better left with the the experts.
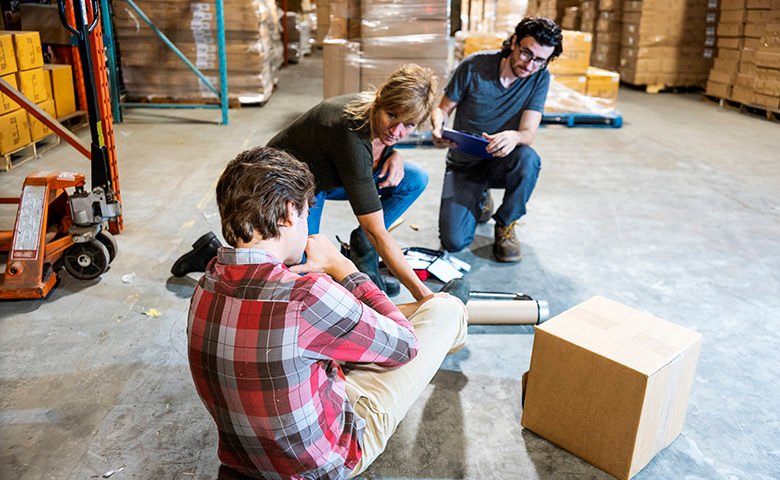
We wanted to consider their thoughts on this issue around the workplace. So we reached out and asked them for their top tips.
Here’s what they said.
Establish Frequent, Relevant and Required Safety Training at Every Level
The best way to improve your total recordable injury frequency rate is to have a culture of safety thoroughly underpinned by frequent, relevant and required safety training at every level of the organization. Initially, tailor your training to the root cause of your most common injuries.
Have the training be participatory – don’t just spray and pray, but show employees the correct method or process and have them practice in front of a group.
Ensure every single employee that sets foot on the worksite participates in the training. Don’t skimp on the time associated with training. You may see it as non-productive time, but evaluate the cost of poor safety against the few additional minutes spent in training designed to reduce your injury rate.
Celebrate runs of accident-free days with the employees, and then set the goal higher. No one wants to walk onto the job site and see that you have zero accident-free days.
Finally, ensure leadership promotes safety through observation and immediately shuts down unsafe practices, no matter who is performing them. Have a zero tolerance policy for unsafe acts, and create a culture of zero injuries.
Look for, Contain, and Correct the Hazards Based on Risk
Lower your injuries by looking for, containing, and correcting the hazards that you know are likely to hurt people. First, you should train your supervisors in how to identify and prioritize hazards based on the risk level.
Once your supervisors are competent in identifying hazards, they should immediately contain the hazard (identifying a hazard but without a documented containment you put your company in legal jeopardy if someone is injured before you correct the hazard.)
Once the containment is in place, the supervisor should determine a permanent correction and put in a work order with a clear deadline on it that appropriately corresponds to the risk posed by the hazard. Management should monitor the progress toward completion and intervene when deadlines aren’t met.
Ensure Workers’ First-Aid Training Is Up to Date
Some ways to improve a team’s total recordable injury frequency rate on the job site are:
- Ensure workers update their first aid training regularly.
- Ensure workers have daily safety meetings before work to go over the personal protective equipment required (hard hat, goggles, gloves, high visibility vests, etc).
- Remove trip and fall hazards. (Read How to Prevent Slips, Trips and Falls.)
- Ensure railings are at all areas where falls are possible.
- Have meetings to go over past workplace injuries and discuss what went wrong and how they can be avoided.
- Have readily available safety equipment for staff to use if they want (ie back support brace, etc).
- Keep a billboard visible to all staff that gets adjusted each day that says “X” days without a workplace injury”.
- Have bonuses/incentives for all staff for going a certain amount of time without injuries.
Get to Know the Leading Indicators of Accidents
Gaining awareness and improving overall safety awareness can be made possible by ongoing effective communication with your team on the front lines.
Genuinely ask your team today; “What are you noticing that we should change? What’s happening that I can fix to make your job safer?” Really listen to what they tell you, and act on it immediately. That builds trust and respect, and leads to shared awareness. It costs nothing really and has an incredibly valuable impact; not the least of which is making sure everyone goes home safely at the end of each day.
(Read:accident incident investigation technique guideline).
Eliminate Paperwork Errors
Remember that incidence rates are generated from data. For example, a common mistake I see on the OSHA 300 is recording an injury as a “days away” case because the employee didn’t return until the next day.
We don’t record the day of the injury. When I see a case on the 300 log that has only one day recorded (days away or restricted/transferred – any day count), I always investigate because there’s a chance we can delete that entry. Consider hiring an OSHA record keeping expert to review cases going back three years. Or, call OSHA’s free onsite consultation program to do the same; all of their Consultants are very good with OSHA record keeping.
Strategize to Reduce Lost Time Accidents on Site
Strategies should be in place prior to the commencement of any works. The procurement process for suppliers, contractors and outsourcers should specify selection using the hierarchy of controls which require the most effective elimination of the hazard, to be implemented before relying on the least effective, PPE.
In order to minimize incidents, an analysis of past performance data should identify failings in relation to who, what, where and how accidents occurred, then remedial actions can be targeted to best effect. A focus on underlying causes can facilitate their elimination.
The planning stage for tasks should also have risk assessments based on the hierarchy of controls. This is the time for creative thinking in the approach to incident prevention, ISO 45001 is based on the philosophy of risks and opportunities.
For example, the application of new technologies can eliminate the need for workers to be exposed to risk by using drones for avoiding working at height or confined space entry. Also, in areas where workers are exposed to transport risks, new wearables alert both machine and worker to their close proximities.
In addition, there are new developments in providing real time data for personal bio-rhythms and stress measurements, which can be used to manage risks.
The bywords to effective incident control are procurement pre-qualification. Thereby applying clear organizational OHSMS criteria which filter out the less competent and unreliable providers in the supply chain. Also, systems innovation to create an environment of continual improvement by applying new ideas and adapting to change