Personnel Hoisting Safety Guideline
11 min readThe use of a crane basket ( personnel Hoisting device )is strictly prohibited except where there is no safe alternative available and where conventional means (scaffolding, ladders, mobile elevated work platforms, and aerial lifts) would create a greater hazard. When the use of a crane-suspended personnel basket is the safest alternative, its use shall meet the applicable in-country regulatory requirements (i.e. OSHA CFR 29 1926.1431) and the requirements of company procedure. Use requires approval of the respective EHS Director and issuing a specific Work Permit approval form.
The purpose of this article is to outline Hoisting Personnel safety requirements when used by company and subcontractors employees at worksites including the following :
- Definitions
- Requirements
- Crane and Rigging Requirements
- Planning
- Proof Testing
- Safe Work Practices
- Personnel Platform Design and Specifications
- Environmental Conditions
Also Read: What Is a Sling Angle?
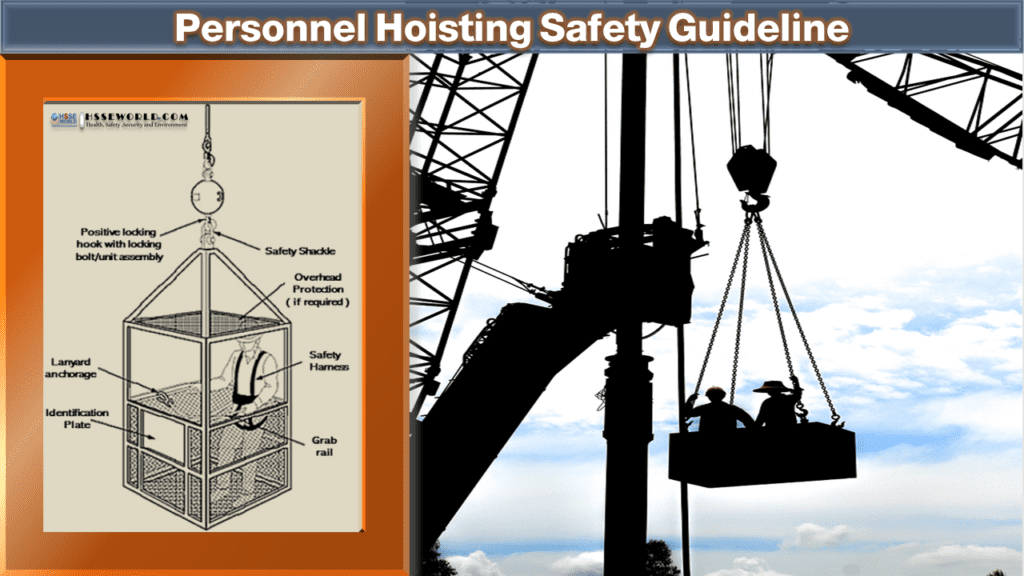
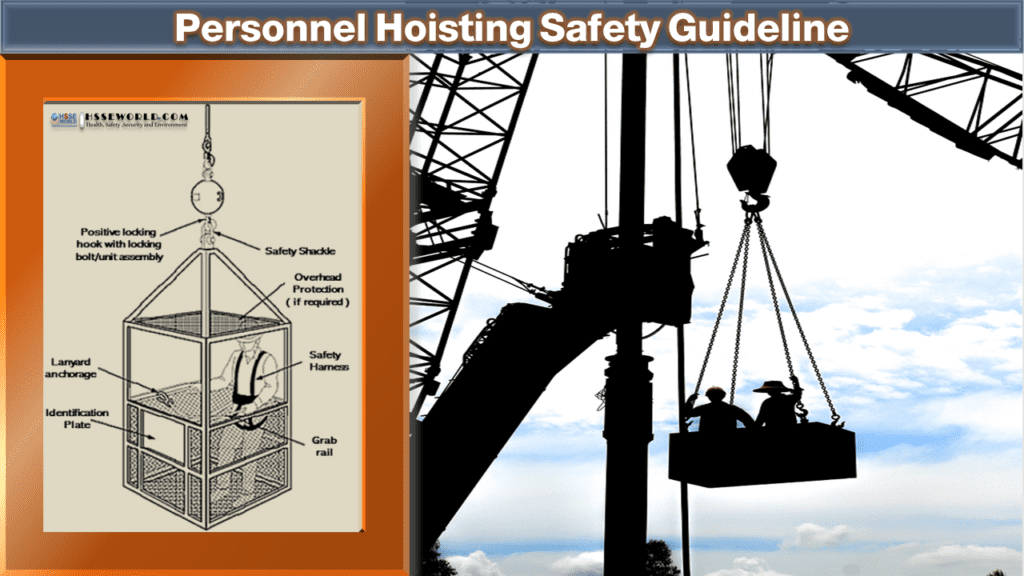
Definitions
Qualified Person – One who, by possession of a recognized degree, certificate, or professional standing, or who by extensive knowledge, training, and experience, has successfully demonstrated his ability to solve or resolve problems relating to the subject matter, the work, or the project.
Competent Person – One who is capable of identifying existing and predictable hazards in the surroundings or working conditions that are unsanitary, hazardous, or dangerous to employees, and who has the authorization to take prompt corrective measures to eliminate them.
Note: The person carrying out a thorough examination should have appropriate practical and theoretical knowledge and experience of the lifting equipment which will enable them to detect defects or weaknesses and assess their importance in relation to the safety and continued use of the lifting equipment.
Although the competent person may often be employed by another organization, this is not necessary, provided they are sufficiently independent and impartial to ensure that in-house examinations are made without fear or favor. However, this should not be the same person who undertakes routine maintenance of the equipment – as they would then be responsible for assessing their own maintenance work.
Personnel Platforms – Any personnel platform or basket used to lift personnel with a crane or derrick designed by a qualified engineer and is to have the following markings: a uniquely identifiable number; a marked SWL and the date of last thorough examination.
Thorough Examination – A systematic and detailed examination of the equipment and safety-critical parts, carried out at specified intervals by a competent person who must then complete a written report.
Requirements
The Regional EHS Director or Nominated Delegate and associated Service Director or Nominated Delegate are responsible for providing approval for the use of a crane-suspended personnel platform or basket under this procedure.
The specified in-country regulatory requirements (i.e. OSHA CFR 29 1926.1431) shall be reviewed by the supervisor responsible for the activity, prior to making the lift. No variances to the company procedure or legal requirements can be made except in an emergency life-threatening rescue situation. The scope and duration of work shall be scheduled consistent with the weather forecast of the day.
The Crane Operator shall determine that all systems, controls, and safety devices are activated and functioning properly; that nothing interferes with the equipment or the personnel platform in the course of the trial lift, and that the lift will not exceed 50 percent of the rated capacity of the crane or derrick for the radius and configuration of the crane or derrick.
Crane and Rigging Requirements
- Cranes with variable-angle booms must have a boom angle indicator that is visible to the operator.
- Cranes with telescoping booms must be equipped with a device to clearly indicate to the operator the booms extended length.
- An anti-two-blocking device shall be used to prevent the load block or hook from contacting the tip of the boom.
- The load line or hoist drum will have a device that regulates the lowering speed (controlled load lowering).
- Hooks or attachment means to the crane basket shall be of the type that can be closed and locked, eliminating the hook throat opening.
- Wire rope, shackles, rings, and master links used for rigging shall have a safety factor of seven times the intended or maximum load applied.
- When a wire rope bridle is used to connect the platform to the load line, the bridle legs must be connected to a master link or shackle so that the load is evenly positioned among the bridle legs. Bridles and associated rigging for attaching the personnel platform to the hoist line must not be used for any other purpose.
- All eyes in wire ropes shall be fabricated thimbles.
- The combined weight of the loaded personnel platform and its rigging must not exceed 50 percent of the rated capacity of the crane or derrick for the radius and configuration of the crane or derrick.
Also Read: E-Books: Hoisting and Rigging Safety Manua
Planning
- Prior to hoisting personnel, the Regional EHS Director or Nominated Delegate and associated Service Director or Nominated Delegate must be notified.
- A Safety Risk Assessment (SRA) Safety Task Assessment (STA) or Safety Risk Assessment (SRA) and Point of Work Risk Assessment (POWRA) and a written plan of the activity must be developed by the Site Management and forwarded to the Regional EHS Director or Nominated Delegate and associated Service Director or Nominated Delegate for approval.
- A meeting attended by the Supervisor, Crane Operator, Signal Person, Spotter, and team members to be lifted shall be held and documented prior to the lift. The risk assessments and lift plan shall be reviewed and any concerns addressed prior to commencement. A copy of this plan shall be sent immediately to the Regional EHS Director or Nominated Delegate and associated Service Director or Nominated Delegate. This meeting shall review the following items:
- Associated risk assessments (i.e. SRA and STA or SRA and POWRA);
- Platform and crane maintenance, load test, and inspection documentation;
- A review and inspection of all safety equipment: anti-two-blocking device, positive lock on hook, harness, lanyard, etc.;
- A discussion and review of work area locations and tasks to be performed;
- Communication method to be used between the Crane Operator, Signal Person, Spotter, and team members;
- Emergency actions and plans
- Any other conditions which could affect the safety of the personnel on the suspended platform
- Lifting personnel requires a critical lift plan in conjunction with the approval form enclosed in this procedure.
- All equipment used for lifting of persons must be reviewed by a Competent Person to ensure that risks to personnel being lifted are reduced to as low as reasonably practicable. It is also necessary to check the requirements of the applicable state / applicable regional regulatory requirements, should they differ from the procedure.
- Trial Lift and Inspection
- A trial lift with the unoccupied personnel basket loaded at least to the anticipated lift weight must be made from the level at which team members will enter the basket to each location where the basket is to be hoisted and positioned. This trial lift shall be performed immediately prior to each shift in which personnel will be hoisted. Each trial lift shall be documented in the approval form enclosed in the procedure.
- The trial lift must be performed immediately prior to placing personnel on the platform.
- The Crane Operator shall determine that all systems, controls, and safety devices are activated and functioning properly; that nothing interferes with the equipment or the personnel platform in the course of the trial lift; and that the lift will not exceed 50 percent of the rated capacity of the crane or derrick for the radius and configuration of the crane or derrick.
- Immediately after the trial lift, the Crane Operator and Supervisor shall conduct a visual inspection of the equipment, base support or ground, and personnel platform, to determine whether the trial lift has exposed any defect or problem or produced any adverse effect and confirm that, upon the completion of the trial lift process, the test weight has been removed.
- The trial lift shall be repeated prior to hoisting employees whenever the crane or derrick is moved and set up in a new location or returned to a previously used location or the lift route is changed unless the Competent Person determines that the new route presents no new factors affecting safety.
- After the trial lift, and prior to hoisting personnel, the platform shall be hoisted a few inches with the personnel and materials/tools on board and inspected to ensure that it is secure and properly balanced.
- The following conditions must be determined before the lift of personnel proceeds:
- Hoist ropes are free of deficiencies and kinks.
- Multiple-part lines are not to be twisted around each other.
- The primary attachment is centered on the platform.
- If the load rope is slack, the hoisting system must be inspected to ensure that all ropes are properly seated on drums and in sheaves.
Proof Testing
In order to verify that lifting equipment and accessories remain safe for use, and to detect and remedy any deterioration in good time, thorough examinations are required throughout the lifetime of the equipment, including examinations:
- Before using it for the first time – if it was assembled on site, it must be examined by a competent person to ensure that the assembly was completed correctly and safely;
- After assembly and before use at each location – for equipment that requires assembly or installation before use;
- Regularly while in service – if the equipment is exposed to conditions that cause deterioration which is likely to result in dangerous situations. Most lifting equipment will be subject to wear and tear and so will need regular in-service examination. Some may be exposed to significant environmental conditions which may cause further deterioration
- Arrange for a thorough examination to be carried out at intervals no greater than every 6 months, or in accordance with an examination scheme, drawn up by a competent person.
- Following exceptional circumstances – liable to jeopardize the safety of lifting equipment, which may include:
- Damage or failure;
- Being out of use for long periods;
- Major changes, which are likely to affect the equipment’s integrity (e.g. modifications, or replacement/repair of critical parts).
The thorough examination is to be conducted by a competent person and a report is to be provided to FieldCore. This report must contain the following information:
- The date of the report;
- The address of the premises at which the thorough examination was made;
- Particulars sufficient to identify the lifting equipment including were known its date of manufacture;
- The date of the last thorough examination;
- The safe working load of the lifting equipment or (where its safe working load depends on the configuration of the lifting equipment) its safe working load for the last configuration in which it was thoroughly examined;
- Periodicity of the examination;
- Reason for examination i.e. within the 6-month requirement or as outlined in Section 2.6 (Following Exceptional Circumstances);
- In relation to every thorough examination of lifting equipment:
- Identification of any part found to have a defect which is or could become a danger to persons, and a description of the defect;
- Particulars of any repair, renewal or alteration required to remedy a defect found to be a danger to persons;
- In the case of a defect that is not yet but could become a danger to persons:
- the time by which it could become such danger;
- particulars of any repair, renewal, or alteration required to remedy it.
- The latest date by which the next thorough examination must be carried out;
- Where the thorough examination included testing, particulars of any test i.e. NDT;
- The date of the thorough examination;
- The name, address, and qualifications of the person making the report; that he is self-employed or, if employed, the name and address of his employer;
- The name and address of a person signing or authenticating the report on behalf of its author.
- Personnel hoisting shall not be conducted until the proof testing requirements are satisfied.
Note: Where explicit country regulatory requirements for ‘Proof Testing’ exceed or are more prescriptive than the requirements in the above section, in-country requirements must be adopted – for example:
USA – OSHA 1926.1431(j)(1):
“At each Jobsite, prior to hoisting employees on the personnel platform, and after any repair or modification, the platform and rigging must be proof tested to 125 percent of the platform’s rated capacity. The proof test may be done concurrently with the trial lift”
Safe Work Practices
Hoisting of the personnel platform must be performed in a slow, controlled, cautious manner, with no sudden movements of the equipment or the platform.
Platform occupants shall keep all parts of the body inside the platform during raising, lowering, and horizontal movement.
The crane operator should remain at the controls at all times while personnel are suspended from the platform.
Personnel being hoisted shall remain in continuous sight or direct communication with the operator or signal person.
Employees on the platform shall use a personal fall arrest system that is attached to properly identified anchorages. This anchor point shall not be part of the basket or other device carrying personnel. All personnel that are being lifted inside a crane basket must have completed the appropriate fall protection training course.
The platform must be secured before employees may leave the platform. Tag lines must be used when necessary to control the platform unless their use creates an unsafe condition.
A radio communications system for uninterrupted voice contact between the Crane Operator and a person in the personnel basket is required.
A Spotter, with constant visual contact of the personnel basket, will be in a position to ensure good communication with the Crane Operator. The Spotter is separate from a Signal Person.
The personnel platform must not be closer than 10 feet to any electrical line (non-insulated or insulated) unless the electrical line has been de-energized. Lockout/Tagout must be performed on the de-energized lines.
The personnel platform cannot be lifted into the path of moving parts and/or equipment (i.e. Wind Turbine Rotor). Equipment must be de-energized and all personnel involved in the lift must perform Lockout/Tagout following the equipment specific LOTO procedure.
Personnel platforms must be used only for employees, their tools, and the materials necessary to do their work. Platforms must not be used to hoist materials or tools when not hoisting personnel
Personnel Platform Design and Specifications
Consideration in terms of safety, cost and time should be given to the commercial availability of manufactured personnel platforms. The personnel platform and suspension system shall be designed by a qualified engineer competent in structural design. All field drawings, as-built drawings, and engineering calculations for each personnel platform must be maintained at the job site and readily available for management review.
The personnel platform itself (excluding the guardrail system and personal fall arrest system anchorages), must be capable of supporting, without failure, its own weight and at least five times the maximum intended load.
The personnel platform must be equipped with a guardrail system and must be enclosed at least from the toe board to mid-rail with either solid construction material or expanded metal having openings no greater than ½ inch.
A grab rail must be installed inside the entire perimeter of the personnel platform to minimize hand exposure.
An access gate should be provided. The access gate shall swing inward and be equipped with restraining device that prevents accidental opening.
All edges exposed to employee contact must be smooth enough to prevent injury.
The weight of the platform and its rated capacity or maximum intended load must be conspicuously posted on the platform with a plate or other permanent marking.
The system used to connect the personnel platform to the equipment must allow the platform to remain within 10 degrees of level, regardless of boom angle.
The suspension system must be designed to minimize tipping of the platform due to movement of employees occupying the platform.
Headroom must be sufficient to allow employees to stand upright in the platform
In addition to the use of hard hats, employees shall be protected by overhead protection on the personnel platform when exposed to falling objects. The platform overhead protection must not obstruct the view of the operator or platform occupants (such as wire mesh that has up to ½ inch openings), unless full protection is necessary.
Example of Design:
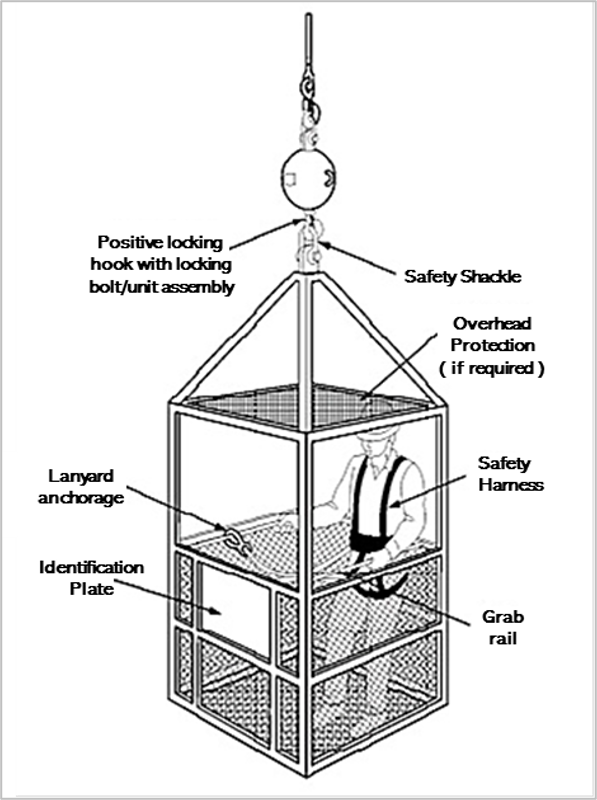
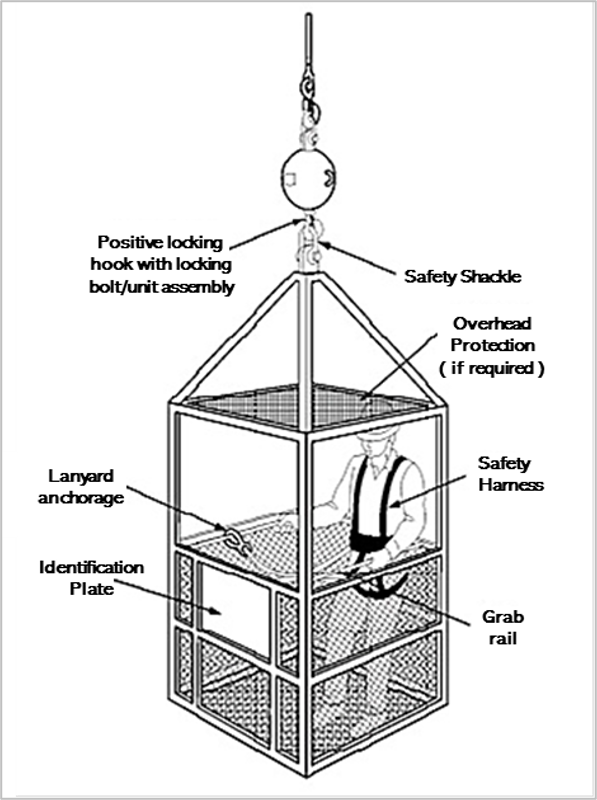
Environmental Conditions
The hoisting of employees will be discontinued upon indication of the following:
- Winds speeds >15 mph or <7 m/s
- If crane capacity requires wind speeds lower than 15 mph consult crane charts, etc., and reduce upper limitation.
- At the first signs of thunder or lightning
- Heavy rain, light rain, or drizzle
- Snow, hail, or fog
NOTE: Wind speed limits may be lower depending on country-specific regulations. Whenever local requirements define specific wind speed limits, the most restrictive should be followed.
Other weather and environmental conditions:
A competent person must determine if, in light of indications of dangerous weather conditions, or other impending or existing danger, it is not safe to lift personnel. If it is not, the lifting operation must not begin (or, if already in progress, must be terminated).
Also Read: How to properly investigate accidents in your workplace 10 Critical Steps.
Please visit our Safety Resources SAFETY BAG to have many Safety Resources
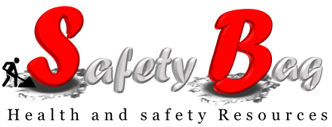
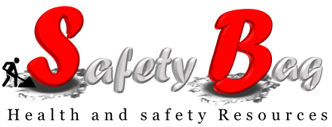
1 thought on “Personnel Hoisting Safety Guideline”