Material handling Hazards and controls
Materials handling is the lifting, moving, and placing of items in various forms. It may be done manually or with equipment. Materials handling is one of the leading causes of disabling occupational injuries. According to the National Safety Council, 20% to 25% of all disabling occupational injuries result from materials handling.
Materials handling includes the use of many kinds of equipment designed to help in the tasks. Manipulators, jacks, hoists, derricks, industrial trucks, cranes, backhoes, conveyors, rigging, escalators, elevators, and other equipment are part of the materials handling arsenal. There are many kinds of objects and materials to handle, each posing different hazards. There may be individual objects or groups of objects in boxes, bins, totes, or pallets. We use buckets and scoops of various types to handle bulk materials, like grain, gravel, earth, and loose parts.
This article discusses many of these activities and the types of equipment used in them.
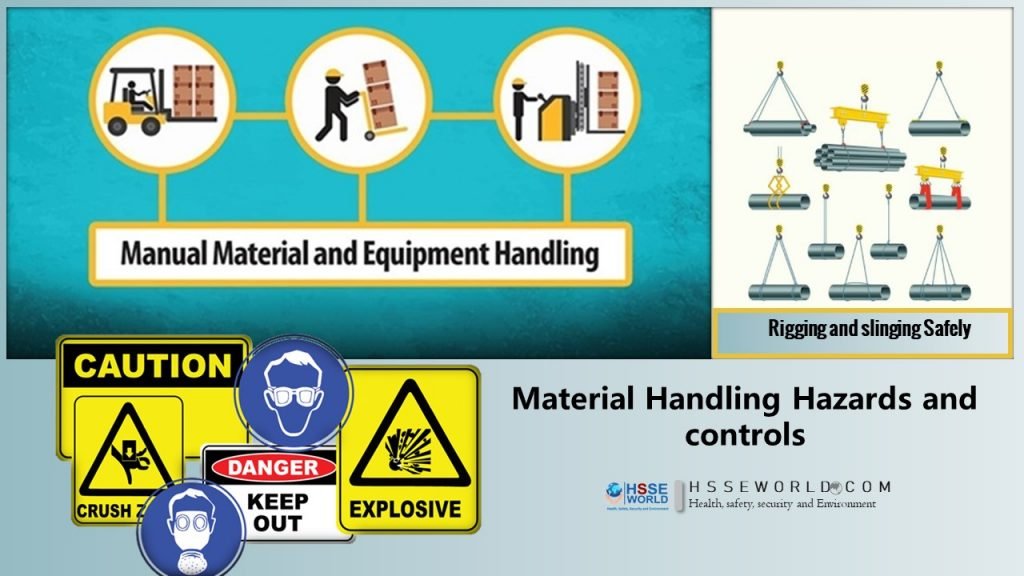
Hazards
There are many kinds of hazards for materials handling activities and equipment. Some are unique to particular activities, equipment, or kinds of materials.
Equipment
- Manual materials handling poses dangers that may be different from the use of cranes or hoists.
- Electrically powered equipment has some hazards resulting from the electricity that is different from those powered by other energy sources.
- Mobile equipment has hazards different from a fixed equipment.
- Lifting and moving a coil of steel has different hazards from loading grain into a bin.
Handheld Materials
- Materials may be flammable or toxic.
Environment
Environments may contribute to hazards in materials handling.
- Good lighting, sufficiently wide aisles, good ventilation, traffic controls, and visibility, and uncongested and unobstructed pathways are important.
- So is keeping lift zones clear of people.
- Proper maintenance of materials handling equipment is essential.
- Failure of structural elements, brakes, controls, and other components can lead to accidents.
Training
- Training is also important. Workers must learn how to lift items to minimize the chances of injury.
- Operators must learn how. to operate materials handling equipment, to properly plan a safe lift, to understand what can go wrong and how to protect themselves, others, and property.
- Other participants in materials handling operations must know procedures, such as hand signals, staying out from under loads and away from elevated loads, and use of proper rigging.
Planning
- It is also important to plan materials handling jobs and instruct participants in the steps that will be taken.
Failure of lifting equipment
- Failure of lifting equipment is one major class of hazard in materials handling. The failures are often the result of overloads for certain lifting conditions. For example,
- in humans, we see sprains and strains of backs, arms, and legs.
- A crane boom may buckle, a chain or wire rope that is part of the lifting device may break, rigging that restrains load may fail, or conveyor support may collapse.
Loads
Another class of hazards is falling loads.
- Materials may fall on people and cause injury,
or they may fall on property and cause damage.
- A load may shift and tip over.
- A load may be inadequately rigged, restrained, or anchored.
Motion
Another class of hazard is material in motion. The speed and mass of materials and equipment are important considerations.
- Objects may strike something else and cause damage or strike a person and cause injury.
- One may operate equipment too fast, tip it over, and be out of control or unable to stop it quickly.
- People may be run over or have their hands or bodies caught, crushed, or pinched.
- The rate of flow is important, particularly when materials are handled in different ways in an overall process. Unless there is a balanced flow, materials will pile up at certain points, possibly causing workers to rush and do things in an unsafe manner.
Controls
There are many different controls for preventing materials handling accidents. Controls are related to the kind of activity, kind of equipment, and kind of material. There are also controls for the environments where material handling occurs.
Eliminate Handling Analysis of operations may identify ways to eliminate material handling tasks. If material handling steps are eliminated, there are fewer opportunities for handling hazards, which makes sense from a safety point of view as well as making good economic sense. Material handling takes time, costs money, and increases the likelihood of damage to items handled. ( Read more:safe-lifting-at-work/)
Planning If materials handling is needed, one should plan the details.
- Handling locations should be clear of hazards.
- Planning should include a selection of correct equipment,
- identification and analysis of steps that may go wrong,
- and establishment of procedures for dealing with contingency problems.
- Hand signals, two-way radio systems, and other means of communication must be arranged, and participants must understand the plans.
- Even a seemingly simple, two-person lift requires planning.
- Participants should, as a minimum, go over how they will proceed from start to finish, what they will do if something starts to go wrong, and how they will communicate during the process. Mechanical handling is generally preferred to manual handling. Manual handling is usually more expensive than mechanical handling.
Design and Selection Materials handling tools, devices, and equipment require proper design.
- Standards from various sources may be applicable.
- Design
considerations must include :
- structural strength,
- operational features,
- control systems,
- visibility,
- failure modes,
- incorporation of safety features, and other factors.
- Even permanently installed materials handling equipment must have safety features. For example,
- conveyors that move above workers in a factory must have overhead protection for the people below to prevent objects and materials from falling on them.
- Some materials handling equipment must have access ways and guardrails for maintenance and lubrication tasks.
- There may be a need for exhaust ventilation or sprayers to isolate or control dust.
- Power equipment may need emergency shutoff controls and guards may be required.
- Each design requires an analysis of uses and use environments. Selection of equipment must match use requirements to availability of necessary features to ensure safe use.
- Selection of the right handling equipment for a job also is important.
- Specific jobs require particular handling equipment.
- Special features may be needed for certain uses.
- Whoever makes the selection must know the task, the equipment, and the use environment.
Use People must use the equipment correctly. Many examples of proper and safe use can be cited. Loads on materials handling equipment must not exceed safe load limits. Operators must drive mobile equipment safely. Cranes should not be operated within certain distances of power lines.
Training The use of each kind of materials handling equipment requires particular knowledge and skill. Operators and those involved in the area of use must learn what hazards equipment and its use impose and how to control the hazards.
They need to develop skills in operating controls, develop skill in recognizing when things could and do go wrong, and be knowledgeable of the suitable action to take. They must develop skills in the procedures and judgments related to planning and executing materials handling tasks. They must know what conditions in the use environment add to the hazards of the material handling task, and they must know when stopping the activity is more important than the loss of equipment or materials or more important than injury or loss of life.
Environments There are many different and important use environment factors.
- Lighting, visibility, weather, terrain, properties of materials (weight, toxicity, stability, etc.), and location of people on or near a site must be evaluated.
- Proper controls must be in place before handling tasks start.
- Even communication means have to be worked out on loading docks where workers do not speak the same language.
(learn more: ergonomics-and-psychology-developments-in-theory-and-practice/)