Lessons Learned from Hand Injuries
12 min readFrom our earliest moments, we use our hands to learn, to explore, and to interact with the world around us, and now as working adults, our hands continue to be “out front,” touching, grasping, pushing, pulling, and lifting our way through work and through life. Unfortunately, being “out front” can also mean being placed in danger, and sometimes things go wrong. This article features reenactments of workplace hand injury scenarios to teach valuable safety lessons about protecting our hands in every situation where hazards exist.
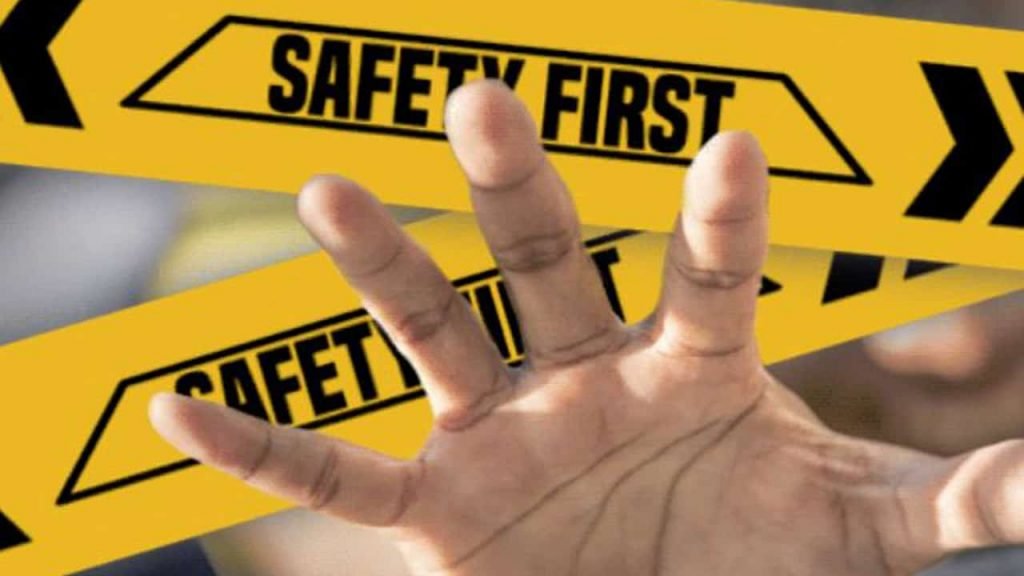
THE CAUSES & EFFECTS OF HAND INJURIES
- Misplaced hands and fingers can quickly be crushed, and industrial knives can easily lacerate; unprotected hands can be burned by hot materials or frostbitten by extreme cold. Even the chemicals we work with can cause injury if precautions are not taken.
- Hand, wrist, and finger injuries like these account for 25 percent of all workplace injuries and put half a million people out of work each year. Serious hand injuries have traumatic consequences and can affect every aspect of your life.
- “I just couldn’t believe how fast it happened,” says Nick Curran, a punch press operator. “I removed a guard to reset a sensor and the next thing I know, my hand is crushed.”
- “And he still can’t work. PT and OT are his full-time jobs. He didn’t just crush his hand that day; he crushed all the plans we had made,” adds Nick’s wife.
- A common theme expressed by workers who have suffered a hand injury is, “I didn’t think anything would happen.” Workers often take safety, especially hand safety for granted, often because they have performed the same task in the past without injury.
- “I knew the metal was sharp and could have burrs, but I have handled them many times before without gloves, so I figured nothing would happen,” says a mill employee who was injured carrying sheet-metal bus bars. “Of course, I didn’t plan on the stack falling over.”
- Trying to hold onto the falling metal parts resulted in a serious laceration to the palm, thumb, and underlying tendon.
- “My gloves were right there. I ask myself every day, ‘Why didn’t you put them on?’ I still don’t have a good answer,” the mill worker concludes.
PROTECTIVE GLOVES
- Protective gloves, just like all protective equipment, do no good if they are not worn. One study showed that 70 percent of workers suffering hand injuries were not wearing gloves; wearing the proper type of protective glove is one of the most effective ways to prevent hand injuries.
- Lightweight cloth gloves protect against minor hazards that can result in scratches, blisters, or irritation.
- Heavy leather gloves are good for working around materials with sharp or rough edges as well as wooden objects, which may have splinters.
- There are many types of cut-resistant gloves available for workers who frequently use knives, cutters, or handle extremely sharp objects. Cut-resistant gloves may be made of Kevlar, metal mesh, or other materials.
- Hot work such as welding, cutting, or brazing will require gloves made of heavy leather and designed for handling hot materials.
- Intensely hot items or work areas will require specialized heat-resistant gloves made from such materials as Nomex, Carbon-X, and Kevlar.
- Certain chemicals will require specific types of protective gloves. Check the Material Safety Data Sheet or chemical label to select the appropriate chemical glove.
- Disposable latex or rubber gloves can protect against bloodborne pathogens as well as bacteria and germs. Remember that they should only be worn once and then disposed of properly.
- As you have seen, there are almost as many types of protective gloves as there are various jobs to be done. Your employer has determined the types of hand hazards at your facility and provides the protective equipment and training necessary to ensure your safety, but it is also your responsibility to take an active role in preventing hand injuries when performing each and every task.
- Of course, you must be sure to select the proper glove for the job. Selecting the wrong glove can be just as hazardous as not wearing a glove at all.
- Glove selection mistakes are often made when workers participate in job rotation and fail to change gloves or are asked to perform an unfamiliar task.
(learn more:how-to-choose-the-right-safety-gloves-12-types-of-hand-protection-gloves/)
Series Of Unsafe Acts Contribute To Shipping Clerk’s Severe Hand Injury
- Sarah Noles, a shipping clerk, was asked to help cut packaging material for a large rush order. She didn’t think twice about wearing her normal lightweight cotton gloves.
- One of Sarah’s co-workers, Mark, says, “I noticed that Sarah wore cotton gloves instead of cut-resistant gloves, but I figured she knew what she was doing. Besides she’s been here a lot longer than me.”
- “Even though I was new to that job, I thought I was doing pretty well,” says Sarah. “We were working fast, but I was still able to have a conversation with Mark.”
- “I guess when I started talking I quit paying attention to where my hand was placed. The foam was thick and my knife was dull so I had to bear down and slice pretty hard. That’s when my hand got in the way,” she continues.
- Sarah’s lightweight cloth glove provided little protection from the blade of her knife. She suffered a deep laceration across the top of her hand, severely injuring the tendons that control her fingers.
Lessons Learned From Sarah’s Injury
- Some contributing factors to Sarah’s injury were wearing an improper glove, being distracted by talking, using a dull blade, and cutting towards her other hand.
- When using knives and other cutting tools, maintaining a sharp blade allows cuts to be made with less force and more control.
- Always keep your body and non-cutting hand out of the path of the cutting stroke. Slow down if necessary to maintain your safety.
- Had Sarah asked what type of glove to wear, or if Sarah’s co-workers hadn’t been reluctant to offer safety advice, her injuries could have been prevented. This is an all too common example of how a lack of communication can contribute to a serious injury.
- Similar incidents occur when workers, or even visitors, enter work areas with which they are not familiar. Never assume newcomers to your work area understand the hazards; a timely warning can prevent serious injury.
- “If I had just spoken up, Sarah wouldn’t have gotten hurt,” says Mark.
NIP POINTS & OTHER HAND HAZARDS
- Whether you are new to an area or an experienced worker, be aware of where your hands are at all times. A good safety practice to follow is to avoid touching anything unnecessarily.
- Many pipes, valves, vessels, and similar items can be very hot and you often can’t tell by looking. Protect yourself by avoiding contact.
- Take a moment to scan for hand and finger hazards as you move about the workplace. Look for moving chains, gears, belts, pulleys, rollers, and similar items.
- Also, look out for the actions of moving machines and various material handling operations, which move materials past solid objects. These types of hand hazards are commonly called “nip points” and are particularly dangerous.
- A nip point is any place where a body part will fit between a moving object and a fixed surface or between two moving solid objects.
- An especially dangerous type of nip point is an “in-running nip point.” An in-running nip point can not only crush hands and fingers but will also continue to pull you farther into the hazard.
- This often occurs when employees reach into a nip point to clear a jam or to start material being fed into a process. Many hands and arm amputations, as well as fatalities, are the result of being caught in an in-running nip point.
- Under normal conditions, many nip points as well as other types of hand hazards are guarded to prevent injuries. Never defeat or “cheat” any safety devices such as interlock switches, light curtains, or machine guarding.
- It is vital to understand that not all hand hazards can be completely guarded. When this is the case, it is critical to stay alert and always keep hands, fingers, and other body parts the recommended distance away from the actions of machines.
ENTANGLEMENT HAZARDS
- When performing jobs that require close proximity to moving parts, such as lathes, drill presses, grinders, and similar types of equipment, wearing any type of glove can create a serious entanglement hazard.
- When this is the case, wearing no gloves at all may be the safest choice. Check with your supervisor if you are unsure.
- Long hair or lose clothing can also become entangled in nip points or moving machine parts, frequently leading to disastrous consequences. This is why long hair and lose clothing are not allowed near moving machinery.
Factory Worker Loses Finger When Ring Gets Caught In Conveyor
- As Jenny Parker learned, jewelry, especially rings, can cause serious injury.
- “I had just gotten engaged and I was so excited! I wanted to wear my ring to work and show everybody, even though I knew rings were prohibited in my area,” says Jenny.
- “I was standing on a raised platform hanging parts into an overhead conveyor when my ring got caught on part of the hanger assembly,” she continues. “My ring was stuck with my arm fully extended and I was being pulled to the edge of the platform.”
- Jenny knew what was about to happen, but when she was pulled to the edge of the platform, she had no choice but to step off. Her ring finger was amputated when she fell to the floor below.
- “Now I know why rings were prohibited in my work area. It’s the same reason I have to wear my ring on my right hand,” notes Jenny.
(learn more:photo-of-the-day-hand-safety-facts/)
Band Saw Operator’s Thumb Amputated While Daydreaming
- Although not as obvious as loose clothing or jewelry, the hazards of complacency and distraction while working in close proximity to hand hazards can be equally damaging. As Frank Johnson figured out, a simple daydream can quickly turn into a nightmare.
- “I was daydreaming the day I lost my thumb. It’s hard to believe now, but I had gotten so used to my job I just didn’t think about what I was doing,” says Frank. “My job included cutting lengths of material on a band saw. I had a form set up to get the length right, so all I had to do was keep pushing material through.”
- “After work, I was going to the driving range to try out a new club I had been saving for, and in my mind, I was visualizing my stance and a new grip I’d been working on,” he adds. “In reality, I had picked up a shorter piece of stock and placing it into my form, but my right thumb directly in line with the blade.”
- “Then I did the same thing I had done a hundred thousand times before; I pushed it through. I lost a lot more than my thumb that day. I lost respect for myself, something I’m having a hard time dealing with,” admits Frank.
- “I can’t work as I did before and I certainly can’t play golf anymore. And that’s hard to take, real hard,” he concludes.
USE OF ASSIST DEVICES
- In addition to staying alert, many jobs require the use of an assist device. An assist device allows you to manipulate materials or adjust machinery while keeping your hands clear of hazards.
- If your work requires the use of an assist device, use it. Many workers who thought they didn’t need it live each day with a constant reminder that they were wrong.
Operator Unqualified To Service Machine Suffers Traumatic Hand Injury
- Under normal conditions, we are protected from many hand hazards by machine guarding or other protective devices; however, many injuries occur during abnormal conditions.
- This is when it may be tempting to skip a procedure or take a short cut in order to get up and running again as quickly as possible, but as Nick Curran discovered, saving time is a poor trade for a mangled hand.
- “I’d been operating the machine for almost a year and it periodically trips an overheat sensor, which is located behind a guard. I had to call maintenance every time,” says Nick. “Every time they came, they would remove the guard, reset the sensor, replace the guard and say, ‘It’s good to go.’”
- “Every time it tripped, it would take maintenance 30 minutes to get it running again. The last time it tripped I figured I’d save us all some time by resetting it myself. After all, I’d seen it done several times,” he adds.
- What Nick didn’t see was that maintenance also turned off and locked out the power supply to the machine before showing up to remove the guard. Following lockout/Tagout procedures prevents a machine from starting unexpectedly while being serviced.
- Nick hit the stop button, thinking that would keep the machine from starting, and proceeded to remove the guard. He then leaned into the machine to reset the sensor.
- Nick didn’t realize that the PLC controlling the machine was still sending a “run” command, and as soon as he reset the overload sensor, his other hand was crushed by the moving parts of the machine.
- Nick was not qualified or authorized to service the machine. To avoid traumatic hand injury, only perform tasks for which you are trained and authorized, and always follow the safe work procedures created for your specific job task.
- “I knew I wasn’t supposed to remove the guard or service my machine,” Nick says, “But I really didn’t think anything would happen. Boy, was I was wrong.”
USING HAND & POWER TOOLS SAFELY
- When using any hand tool, always use the proper tool for the specific task you are performing. Using the wrong tool, or an improperly-sized tool often leads to a slip and an injury.
- Even properly-used tools can sometimes slip, so keep your hands and fingers out of the line of fire. Of course, using power tools greatly increases the potential for injury.
- Make sure you are familiar with the tool you intend to use and have inspected it to ensure it is in good operating condition. The good condition also means all guards are in place and operational.
- Never remove or tie back the guarding on circular saws.
- Cutting blades should be kept sharp and designed for the material you intend to cut or drill.
- Before changing blades or making adjustments, always unplug the power cord to prevent unintended starting.
- Before starting any cut, arrange yourself and your work so all body parts remain well clear of the blade’s travel path.
(learn morequick-tips-for-avoiding-pinch-point-injuries-safety-moment27/).
PREVENTING CUMULATIVE TRAUMA DISORDERS
- The use of both hand and power tools can also contribute to Cumulative Trauma Disorders (CTD’s) in the nerves, joints, and muscles of the hands and wrists. These injuries can be attributed to the poor ergonomic design of the tool, repetitive movement of the hand and wrist, improper use of the tool, or a combination of all three.
- When using tools, keep your hand and wrist in a neutral or “natural” position as much as possible. Don’t force your hands or wrists into awkward postures just to fit the tool or the work.
- Avoid using power tools that vibrate excessively. Padded gloves may help ease the vibration and stress to your hands and wrists.
- When performing jobs that require frequent, repetitive movements of the wrists and hands, taking periodic breaks or rotating to a different job task can help prevent Cumulative Trauma Disorders.
SUMMARY
- When your work requires the use of hand protection, be sure to use it, every time.
- Never remove guarding or perform machine maintenance unless you are properly trained and authorized.
- If your job requires working in proximity to hand hazards such as moving parts or cutting blades, stay alert, and focused on your job.
- Whenever possible, use an assist device to keep hands a safe distance from a machine’s actions.
- When using hand tools, use the correct tool for the job and keep your hands out of the line of fire.
- With power tools, keep all cutting blades sharp and make sure nobody parts are in the path of the cutting stroke.
- Don’t let complacency, production pressures, or being in a hurry tempt you to take a risk or shortcut that could result in a disabling hand injury. By keeping your good safety attitude close at hand, you can be sure to come home safe and sound each day.