Forklift Maintenance Tips
6 min readWith 85 forklift fatalities and 34,900 serious injuries each year, there’s no question that forklifts are a workplace hazard that needs serious attention. But keeping forklifts running well means maintaining them – and that’s a dangerous job in and of itself (see Forklift Safety guide for a discussion of general forklift hazards).
In this article, we’ll look at:
- The importance of conducting regular maintenance on your forklift fleet
- Maintenance hazards (and best practices for mitigating them)
- How to get started creating a forklift maintenance plan
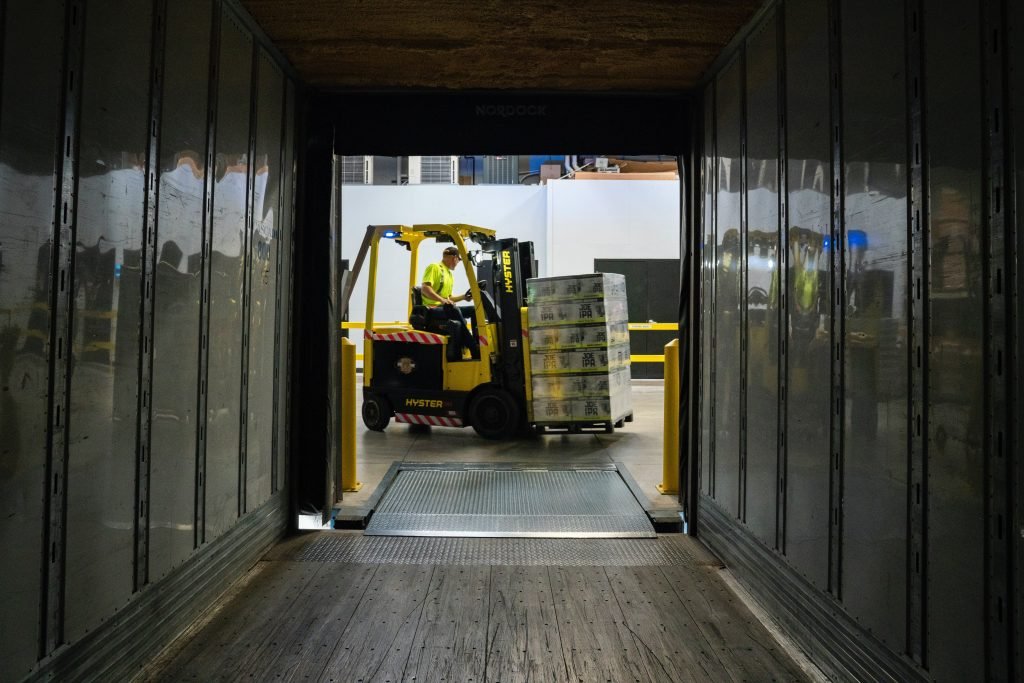
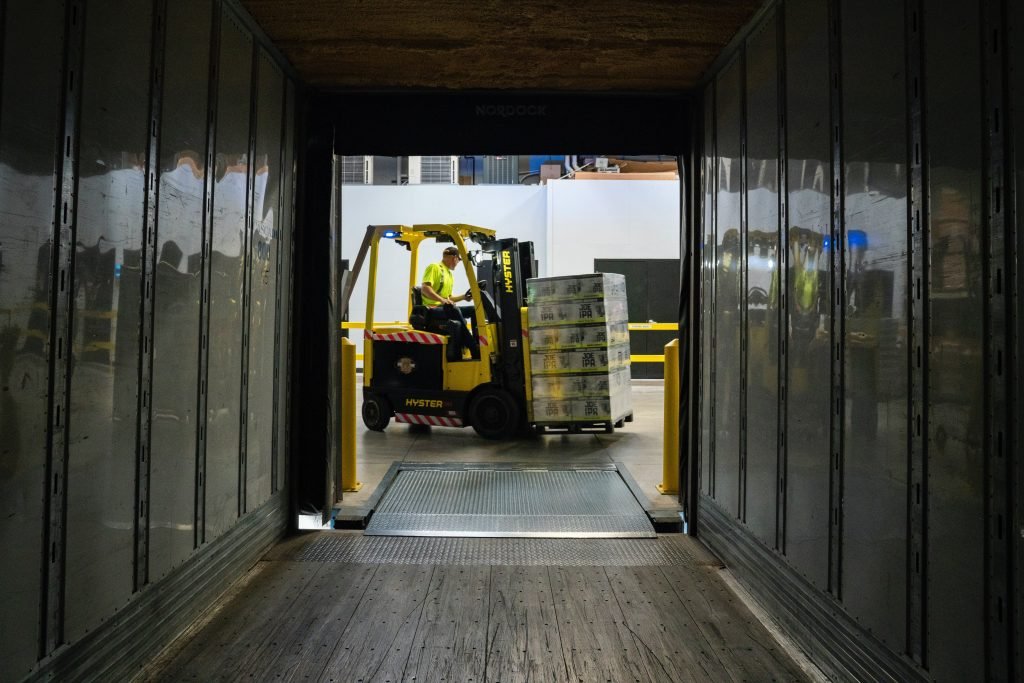
Why Do Forklifts Require Maintenance?
There are two broad reasons you should carry out regular maintenance on your forklifts:
- Well maintained forklifts run smoothly and are less likely to be involved in accidents
- Forklift downtime is extremely costly
Just like regular vehicles, lift trucks require servicing to keep them running well. Also, like cars, they emit dangerous fumes that get worse with poor maintenance. And since most lift trucks operate in enclosed spaces like warehouses, loading docks, and trailers, these fumes can cause serious or fatal injury if not properly managed (learn 3 Ways to Manage Carbon Monoxide Risks at Loading Docks).
Conducting regular maintenance also prolongs the lifespan of forklifts and can save the company money on expensive repairs that could have been avoided with regular check-ups and preventive action.
4 Forklift Maintenance Hazards
Before you start servicing a lift truck, it’s important to understand the potential hazards you face so you can take appropriate precautions. Some of the most common ones include:
1. Handling Hazardous Materials
Lead-acid batteries, battery charging equipment, fuel, anti-freeze, and oil are all common parts of forklifts – and each is a health and safety hazard for workers. Potential risks must be anticipated and managed appropriately, including skin irritation, chemical burns, corrosion, and reactivity.
2. Accidental Forklift Movement
If a forklift hasn’t been properly blocked, it could move during maintenance or servicing. And it doesn’t take much for machinery that heavy to cause serious harm. The entire vehicle poses a safety risk, but workers should be aware of the potential fork movement as well.
3. Fire
The lift truck and its components can become quite heated, even if they are functioning properly. This, combined with the fuel or any other nearby flammable materials, could result in a fire.
4. Poor Manual Handling
Forklifts are heavy machinery, so it goes without saying that some of their parts are on the heavier side. Using poor manual handling skills like bending, lifting, and carrying can result in strains and injuries – especially when repeated over a long period of time.
Best Practices for Safe Forklift Maintenance
Given these risks, it’s best to take additional precautions when inspecting and servicing your company’s heavy machinery. Follow these best practices to help ensure your safety.
Only Qualified and Trained Professionals Should Inspect and Maintain Forklifts
Heavy machinery can be extremely dangerous, so only employees who are qualified, trained, and licensed (as applicable) should perform inspections and maintenance on forklifts.
In the same vein, forklifts should only be reintroduced back into use when a qualified person has deemed them safe.
Lock Out Control Devices and Secure Equipment Against Movement Prior to Servicing a Forklift
While you might think, “no one will touch this while I’m working on it,” you just can’t be certain. Locking out the forklift will ensure that no one turns it on, moves it, or attempts to use it until a qualified person deems it safe and in good working order (find out more in Lockout Tagout: guideline).
Maintenance workers should also keep control of the ignition key while work is being completed.
Immediately Clean Up Any Spilled Fluids
Slips, trips, and falls make up the majority of general workplace accidents and account for 15 percent of all accidental deaths. Whether it’s fuel or engine oil, cleaning up spills immediately after they happen prevents the forklift maintenance worker or their coworkers from slipping on them.
Understand the Hazards and Always Use Appropriate PPE
From batteries and fuel to exhaust fumes and asbestos (which is sometimes discovered during brake and clutch repairs), forklift maintenance poses a number of hazards. Workers servicing lift trucks should wear appropriate gloves, respirators, and any other PPE needed to protect them from hazards like chemical exposures, cuts and abrasions, and falling object hazards.
Refrain from Smoking, Welding, or Lighting Matches Around Forklifts
This is particularly important when it comes to refueling stations and battery-charging areas, as it takes only a small spark to ignite everything.
In case a fire does break out, workers should also be trained on how to properly use a fire extinguisher to put it out.
Only Work Beneath Elevated Forklifts that Are Securely Supported by Blocks
Working underneath an unstable forklift is a recipe for disaster. Any maintenance worker who must conduct work beneath a forklift must ensure that approved blocks are used to elevate the lift truck and that they are completely stable.
Ensure Sufficient Ventilation Before Running LPG, Gas, or Diesel Forklifts
The U.S. Environmental Protection Agency notes that LPG-burning forklift trucks account for more than 60 percent of material handling vehicles and more than 80 percent of all internal combustion forklifts used worldwide. And while properly maintained vehicles aren’t a major source of CO exposure, lift trucks that don’t receive regular engine tune-ups and CO emissions tests can be. For this reason, forklifts should only be run in areas that are well ventilated, where the exhaust will be easily dispersed without negatively impacting maintenance workers.
Know Your Physical Limits
Understanding your limits is key to avoiding muscle stress and strain injuries that can come from poor manual handling practices. Whenever lifting or moving especially heavy forklift parts, workers should enlist help from colleagues or use machinery specifically designed for this purpose.
Keep Full and Accurate Records of Maintenance Procedures
Finally, maintenance workers should be sure to keep track of everything when they’re maintaining a forklift, including the cause and nature of the damage or problems, the repairs required, and an overall assessment of the vehicle’s safety. These details may be necessary for inspections and allow companies to keep track of maintenance and servicing over the lifetime of the lift truck.
Creating a Forklift Maintenance Plan
Now that you understand how to keep forklift maintenance workers safe, let’s turn to the forklifts themselves. To keep them functioning optimally, you’ll need to have a preventative maintenance plan in place. Here are two basic steps to get you started.
Step 1: Consider Your Context
Take stock of your lift trucks and decide what needs to be inspected and how often. Some questions to get you started:
- How old are the forklifts?
- Have they been maintained properly in the past? Is there a service record?
- Is the truck particularly susceptible to damage (like alignment issues)?
Step 2: Create a Schedule
When drafting a maintenance schedule, you’ll want to consider the following:
- What types of forklifts do you have?
- What recommended preventative maintenance checks do you need to carry out?
- Who will perform what tasks?
- How often do the tasks need to be performed?
It can be helpful to create a list of all the tasks that need to be done over the course of a year and then break them down by frequency. For example:
Monthly maintenance | Quarterly maintenance | Semi-annual maintenance |
Oil change | Inspect pedal and hand brake | Replace brake fluid |
Clean air filter | Clean radiator | Check engine bolts and manifold nuts |
Lubricate chassis | Replace hydraulic filter | Inspect brake booster operation |
Inspect drive belt tension | Inspect oil, fuel filter, PCV valve, and hose (engine-powered trucks) | Replace wheel bearing grease and engine coolant |
Adjust idle speed and ignition time (engine trucks) | Drain water separator (diesel trucks) | Replace fuel filter |
Measure CO emissions |
Conclusion
Forklift maintenance is essential to keeping your lift trucks running smoothly and reducing downtime, but servicing heavy machinery can be a dangerous job. Following industry best practices when it comes to maintenance worker safety is the best way to prevent serious injuries.
Are your maintenance workers equipped with the right training to stay safe?