Control and safe use of lifting Equipment and accessories
Taking safety precautions when using lifting equipment is mandatory to avoid any undesired events or accidents. Safety procedures and requirements are in place to protect you and others because these incidents can cause costly damage or injuries. you have to ensure that all lifting equipment and accessories are maintained in a safe working condition All lifting equipment and accessories used in lifting are under your company’s supervision. The following Article describes the minimum mandatory requirements for the control and safe use of lifting equipment and accessories as per the table of content below
Also Read: Personnel Hoisting Safety Guideline
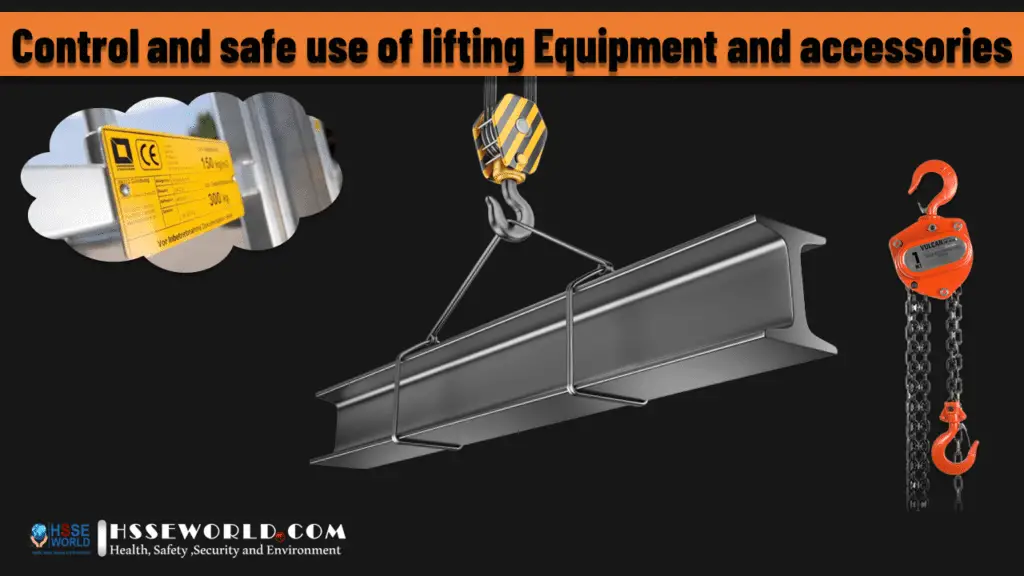
Marking and Identification
All lifting equipment, accessories, and custom-made lifting devices must be clearly marked with:
- Rated Capacity (SWL) – either permanently marked or using a tag or label
- The inspection status – tag, label, or a color coding system
- A unique identifier
Additionally:
- Lifting beams must be clearly marked with their weight
- Where the SWL depends upon the accessories or equipment’s configuration, this must be clearly identified for each configuration. Alternatively, this information must be retained with the equipment
- If a crane has more than one hoist, each hoist must be clearly marked with the SWL
For further information concerning marking and identification see Guide to Marking Inspection, Test and Maintenance of Lifting Equipment and Accessories
Inventory of Lifting Equipment and Accessories
Each Site* must maintain an inventory of all items of lifting equipment and accessories, containing the following, as a minimum:
- Item unique identifier
- Date of each inspection/examination, who carried it out, and the certificate number (where applicable – usually for externally sourced inspections/tests)
- Details of any defect found and the steps are taken to remedy such defects
- Date of any re-test
- Dates of any heat treatment or normalizing of chains or slings
- The due date for the next inspection or test
*Note: Where equipment and accessories are provided to project sites from off-site locations e.g. Tooling or Service Centres, inspection records must be readily accessible from the project site
Inspection, Examination, and Testing Frequencies
The minimum requirements are as follows:
Lifting Equipment:
- Pre-use Inspection (not documented)
- Monthly Inspection (documented)
- 6-Monthly Inspection for equipment used to lift people (documented)
- Annual Thorough Examination (documented)
Accessories / Rigging:
- Pre-use Inspection (not documented)
- Annual Thorough Examination (documented)
Note: Equipment and Accessories / Rigging not in regular use or held in Tooling Centres pending the next outage may be quarantined until needed but it must be ensured that each item has a valid formal inspection before release.
Additional intermediate thorough examinations may be introduced locally, where necessary e.g. severe working environments, high-frequency usage, based on risk assessment
Additionally, lifting equipment must undergo thorough examination:
- Before being brought into use for the first time, unless accompanied by valid regulatory documentation
- Where a new or applicable regulatory requirement is identified
- Where the equipment is involved in an incident or dangerous occurrence
- After a significant change in conditions of use e.g. after installation/assembly/relocation/modification/repair
- After 6 months or more without using
- Each time that an exceptional circumstance (such as overload / Engineered Lift) may have jeopardized the safety of the lifting equipment
- Due to any restrictions, which may apply to the equipment under certain circumstances e.g. low temperatures.
Where local regulations are more stringent, additional inspections must be performed as required. More detailed requirements are provided in the Guide to Marking Inspection, Test, and Maintenance of Lifting Equipment and Accessories
Custom-made Lifting Devices
Custom-made lifting devices must only be used if they have been:
- Designed by a Competent Person and formally certified as safe for the purpose intended by a qualified person*
- The lifting equipment must provide an appropriate factor of safety against failure under foreseeable failure modes, taking into consideration national and international standards relevant to the particular type of device
- Proof-load tested to 125% of rated capacity
- Certified, examined, and inspected according to local legal requirements and/or designer’s recommendations
- Used in accordance with the designer’s or manufacturer’s instructions
*Checks must be made to verify the competency of Third Party lifting equipment testers and examiners involved in the certification of custom-made lifting devices, prior to the placement of the order for these services. In addition to this, the Responsible Supervisor at the site must verify that these checks have been made. If competency cannot be verified or if a problem is suspected, work must not proceed until the equipment has been proven safe for use
Examples of Custom-made lifting devices include:
- Transport Skids, Lifting Frames, and Spreader Beams – anything to which the load (e.g. turbines and rotors) is secured/attached in order the facilitate handling and/or lifting, usually in conjunction with other lifting accessories. The overall load is the combined weight of the skid and the device.
- Such devices must be subject to design controls and engineering calculations used as a basis for determining the SWL
- The SWL, center of gravity, weight, and a unique number (to provide traceability to design calculations, etc.) must be marked on the device
- All devices must be inspected before use
- If the device remains in company possession for more than 6 months, details of the device must be entered into a lifting accessory register or similar and an inspection program implemented
- If removable lifting accessories such as eyebolts or shackles are used to assist with lifting, these must be treated as stand-alone lifting accessories, and any threaded holes/attachment points on the device, including in the device’s periodic inspections
- Rotor Stands (and similar) are not strictly lifting devices but to be treated as such:
- Stands must be subject to design controls and engineering calculations used as a basis for determining the SWL
- The SWL must be marked on the stand
- A unique number must be allocated and marked on the stand (by the manufacturer) to allow traceability to design calculations etc.
- Stands must be inspected before use
- If the stand remains in the company’s possession for more than 6 months, details of the stand must be entered into a lifting accessory register or similar and an inspection program implemented
Thorough Examinations and Inspections
Thorough examinations must be performed in accordance with a pre-determined examination scheme, prepared by a Competent Person, drawn up to suit the operating conditions of each specific item of lifting equipment and type of accessory
Examination schemes must include:
- A detailed schedule of checks, appropriate examination techniques, and testing requirements
- Details of any inspections to be performed between thorough examinations.
- Details of pre-use checks, in-service inspections, and thorough examinations for equipment and accessories that are seldom used or have been out of service for extended periods of time
For further guidance see Guide to Marking Inspection, Test and Maintenance of Lifting Equipment and Accessories.
Any new lifting equipment or accessory, that has not been used before, must be accompanied by a test certificate/declaration of conformity, which confirms that it has undergone a thorough examination (not more than 12 months previously) and specifies the SWL, prior to first use.
In buildings where passenger lifts / elevators are installed, the owner of the building must ensure that the passenger lift is safe to use and that it receives periodic thorough examinations and inspections, in accordance with local regulations. Where FieldCore is not the owner, the Site Manager must make inquiries to ensure that the lift is safe to use.
Alterations to Lifting Equipment and Accessories
Any alterations to lifting equipment or accessories are prohibited. Seek the advice of a company lifting specialist if there are any concerns regarding the suitability of any equipment or accessory for a specific lifting operation.
Defective and Lost Items
Items of lifting equipment or accessories identified as not complying with legislative requirements, or by users having doubts as to its safety (e.g. broken, damaged, or defective, no inspection status, not identified with SWL, or absence of a unique identifier), must be dealt with as follows:
- Lifting Equipment – taken out of service in a secure manner (e.g. LOTO for fixed equipment or retention of keys for mobile equipment) until the non-conformity is corrected
- Lifting Accessories – removed from use and kept in a locked or clearly demarcated quarantine area until the non-conformity is corrected
- Items must then be either:
- Repaired and once repaired, re-certified by a Competent Person before being placed back into service, or
- Destroyed/prevented from being re-used
- Items that are lost must be recorded as such in the site register
Handling, Storage, and Maintenance of Lifting Accessories
Refer to Guide to Marking Inspection, Test, and Maintenance of Lifting Equipment and Accessories
Cranes on Customer Sites
if you are working on a project or customer site you have to follow the following guidance
- RESPONSIBILITIES
- Customer (Operator of Plant) or Site Owner
The Site owner has the overall responsibility for the crane, auxiliary equipment and installations, and its safe operations. This responsibility includes the regular testing of the cranes and their operating personnel in accordance with the local legal regulations and the requirements of the manufacturer’s manual for the operation and maintenance of the equipment.
- Crane-Operators and Riggers
The employer (may be the Customer or a Third Party) is responsible for the professional competence of crane operators and riggers
- Company
The company is often contractually responsible for the timely execution of the works on Site, therefore it is mandatory to ensure that the lifting equipment is tested and certified and operators are competent for their tasks.
Furthermore, it is expected that company Site Staff can recognize whether or not lifting equipment and operating personnel is compliant with the requirements. If deficiencies or defects are observed, then the Site Owner must be informed immediately so that the issue can be resolved in a timely and professional manner.
- GUIDELINE FOR PROJECT SITE PREPARATIONS
- 21 Months prior to the start of the outage. Review the expected status of the crane based on the experience or the previous outage at the same power station
- If crane defects are already known, contact the operator of the power station and ask for information about planned repairs and testing/certification of the crane
- 3-4 Months prior to the start of the outage. If possible, have all certificates available (for cranes, crane operators, and riggers)
- 4-6 weeks prior to the start of the outage. All certificates must be available (for cranes, crane operators and riggers)
Also Read: E-Books: Code of Practice for the Safe Use of Lifting Equipment – Edition 9 (Nov 2019)
- PRE-OUTAGE EXAMINATIONS AND TESTING – REFERENCE DOCUMENTS AND STANDARDS
- Manufacturer’s Manual
The Manufacturer’s operations and maintenance manual must be consulted by the testing body in advance of any testing and certification of a crane
- Local Legal Regulations
The Local Legal Regulations may be different from Country to Country and therefore must be considered prior to testing and certification of a crane. Within the FieldCore organization, such applicable Local Legal Regulations should be obtained from the Sub-Region office.
- Standards
The applicable standards must be considered before conducting of any testing and certification of a crane. A list of possible standards is to be found at the end of this document
- MINIMUM CONTENT OF TESTS AND CERTIFICATES
- Content of an Inspection / Thorough Examination of a Crane
The testing and certification of a crane must be carried out in compliance with the applicable standard, manufacturer’s operation and maintenance manual, local legal regulations and the written scheme of examination (where applicable – Guide to Marking Inspection, Test and Maintenance of Lifting Equipment and Accessories.
- Checks should include the following:
- Good operation of the crane to be demonstrated
- Conditions of hoist ropes/chains
- Brakes
- Operation of all limit switches, alarms, and proximity sensors
- Operation of radio control in all modes (if fitted)
- Rope anchors and deadends
- Sheaves and bearings
- Crane nameplate and details
- The general condition of electrical equipment including pendant controls and phase failure protection
- The support structure of the crane (including foundations)
- Rails and securing attachments
- Driver controls (where fitted)
- Cross travel trolley
- Rope drums and wrap
- Couplings
- Handrails, ladders, and guards
- Derailment catchers
- End stops and buffers
- Wheels, including bearings and axles
- Crane structure and fastening including welds, rivets and bolts and cab to crane structure
- Coating condition (paint etc.)
- Lubrication
- Hooks
- Lifting beam
- CRANE OPERATOR’S AND RIGGER’S CERTIFICATES
The crane operators and the riggers involved must be adequately trained and competent for the tasks allocated to them
A respective certificate/confirmation must be provided by the employer to the company before the deployment of the personnel to an Outage Site
- INSPECTION / THOROUGH EXAMINATION CERTIFICATE (CRANE CERTIFICATE)
The appearance and content of inspection certificates vary between the authorized bodies performing the examination and or due to local, however, there is a minimum requirement regarding the content of a “Crane Certificate” and without this, no proper evidence is given that a thorough examination was conducted and that the crane is safe for use. The minimum content of a “Crane Certificate “is as follows:
- Plant/site Name, Operator of Power Plant, Country where the Power Plant is located.
- Manufacturer and year of manufacture, identification number of crane, safe working load
- Applicable standard/local legal regulation the test is referring to.
- Type and content of the test:
- Visual check
- Functional test
- Load test
- Recognized defects
- Components that are still safe for operation but show wear and tear
- Mandatory repairs/replacement of components of the crane
- A declaration that the crane is safe to use (without which the crane must not be used) or if there are any restrictions (i.e. reduced max. load)
- Decision, if further tests are required – if no complete testing was done or repairs are required before complete testing can be done
- Due date for next regular test
- Date, signature, and stamp of the authorized party conducting the examination
Also Read: Crane Suspended Personnel Platform (MANBASKET) Permit
- LOAD TEST / OVERLOAD TEST
Only a load test can provide the final evidence that the crane is capable to lift the expected loads and that the brakes are in well-working order to keep the such load in a lifted position. Therefore, a load test should be considered for the annual thorough examination/inspection (as required for example by, BS 7121-3: 2003).
However, after a major repair or change on a crane, a load test with a test load at least equal to the maximum working load of the crane must be carried out.
If the crane is new or if it must be certified for a workload other than it was originally designed, an overload test (125%) is mandatory.
Training
Competent Persons must be provided with training that includes:
- Local Statutory Legislative Requirements
- Lifting Equipment & Accessory Examination/Inspection (Theory & Practical)
- Systems – tagging, color coding, reporting, quarantine
- Methods of Testing
- Documentation/Certification & Report Writing
Records
Records for documented Inspections and Thorough Examinations or company lifting equipment and accessories must be maintained for the current year and the previous 5 years.
Also Read:How to properly investigate accidents in your workplace 10 Critical Stepsbrowser tab)
For more safety Resources Please Visit Safetybagresources