The connection between Near Misses and Incidents
10 min readSafety managers worry about incidents that result in an injury to someone in their workplace. It’s only natural to keep your focus on the events that have serious outcomes. But if you’re not looking at some of the less dramatic safety events, you might be overlooking an important tool that could help you keep workers safe.
Note
Near miss occurrences don’t seem terribly dangerous on the surface – after all, no one got hurt. But they are the biggest predictor of workplace incidents over the long-term. The connection has been borne out in multiple studies: more near misses means a higher likelihood of incidents. There are, however, some important nuances here that are worth unpacking before we go deeper and layout some proactive measures.


NEAR MISSES AS A LEADING INDICATOR FOR INCIDENTS
Research shows that near-miss data is a leading indicator of serious accidents and other workplace incidents. This isn’t a numerically fixed relationship, however. Fifty workplace incidents don’t necessarily lead to one serious incident, and 500 won’t necessarily lead to a workplace death – near misses don’t work like stamp cards for a free coffee. If, however, the near-miss occurrences start trending up from their historical occurrence rate, then the chances of a serious incident happening also go up. Depending on how finely you slice workplace safety data, the trend increase can be pinpointed to work location, work area, work type, team, and so on. As you can imagine, this fine-grained level segmenting is incredibly helpful for heading off the trend and better focusing your training efforts.
NEAR MISSES AND INCOMPLETE DATA
It’s important to recognize that the data will sometimes show a different relationship between reported safety issues. There are cases in which the odds of a serious workplace accident actually coincides with near miss rates going down. What accounts for this apparent reversal in the natural order of workplace safety? In almost every case, it’s either due to implementing a more accurate reporting solution or an explicit organizational push to increase safety.
A new reporting and recordkeeping system can result in a big bump in the number of near misses being captured. Whether through the ease of use (as with mobile data submission) or simply by speeding up how quickly data is compiled, safety data solutions won’t increase the number of near misses taking place in your workplace, but they will capture some that previously went unnoticed and unreported. This reporting increase is a permanent increase over the baseline established by the previous (often paper-based) system and it isn’t usually accompanied by an increase in the number of serious workplace incidents. The second case is a shift in safety culture prompted by an organizational initiative. In this instance, near misses go up because employees have been reminded about the importance of reporting them. Again, the chances of a serious incident generally won’t increase due to more reporting. Even though it may just look like a management directive, reminding employees to report near misses primes them to look for near-miss occurrences and increases their awareness of workplace hazards. That increased awareness can lead to a safer workplace. However, this incident-free bump and increased reporting of near misses might only be temporary if it results from management pressure rather than a genuine improvement to the safety culture.
USING SAFETY SYSTEMS TO REDUCE NEAR-MISS OCCURRENCES AND AVOID WORKPLACE ACCIDENTS
tween near misses and incidents, let’s look at what we can do about them. There are a number of safety best practices that have stood the test of time in terms of improving workplace safety. We’ll cover four of these fundamental building blocks of workplace safety systems and then look at how modern data collection and analysis can optimize their delivery. SAFETY TRAINING ONBOARDING AND DIGITAL RECORDS Safety managers are responsible for making sure employees have the safety training they need before the job starts. The bulk of this training generally comes right when the employee is hired and often covers the whole gamut of work in the facility or Jobsite. Lumping all of the training together is efficient, but it’s not necessarily effective. Spending several hours passively absorbing information is rarely the best way to retain most of it. All too often, an employee is onboarded, the training is checked off as complete, and then no one bothers making a serious effort to repeat or reinforce the information they learned.
(Learn More: near-miss incidents overview )
that an employee’s actions went against their safety training. But if there is no system in place for reinforcing or refreshing the relevant portions of the training, the company does bear responsibility for failing to make an honest effort to keep the employee’s training up to date. Without a doubt, a proper onboarding safety course is critical. Unfortunately, it is wasted if there isn’t any opportunity to reinforce the learning or refreshers to back it up as the employee continues with the company. Safety meetings, toolbox talks, and the like do help as refreshers, but there is a strong case for tracking employee education more robustly. One best practice that is growing in popularity is to track the modules within the onboarding safety training and set staggered “expiry dates” for them. This is set at an employee level using a training database. If an employee’s role involves using harnesses, the harness safety module may expire every 6 months or even every 3 months depending on how many harness-related near misses or incidents the company experiences. If another employee’s job mostly involves driving a forklift, their forklift module can be set to expire every quarter while the harness training may be set to an annual cycle.
This more robust method of not only keeping records but also using them to define individual training schedules helps safety managers prioritize their training efforts, reinforcing the most relevant topics first. Prior to digital recordkeeping, this type of safety training system became more and more cumbersome as the number of employees grew or the seasonal turnover increased. Now, reminders can be set through the system in order to flag groups of workers well before their training expires. These advanced warnings give safety managers more time to set up additional training hours throughout the month and undertake other preparatory steps. This way, the company can maintain its commitment to safety training by offering workers several training sessions to choose from as they near their training expiry dates. Empowering workers to select the training times that work best for them tends to reduce the impact that having all workers on training at once has on production schedules.
Safety managers are always asking themselves, “Does this employee have the training to do this task? When was their last refresher?” A properly managed database takes away the guesswork by making that information readily accessible on the safety manager’s smartphone.
SAFETY MEETINGS
In most organizations, the safety meeting is the primary communication tool. It is a deep-dive conversation into the hazards and issues encountered in a particular job. The subject can be the type of work being done that day, a briefing on the specific hazards at the Jobsite, or anything else related to safety. The whole point of a safety meeting is to have an entire meeting dedicated to safety in the same way as you would for other critical issues. This sets safety up as something that is a core concern for the company, just like its sales and finances. Safety meetings shine when they are focused on relevant information. If you identify trends in near-miss reports or a particular hazard is introduced by a new phase of the job (such as the risk of chemical burns when wet concrete is being poured), these are good topics for discussion in a safety meeting.
One major challenge is that it can be hard to justify and fill an entire meeting with safety topics while avoiding the kind of repetition that drives employees to annoyance. Monthly safety meetings usually go over well but pushing this format to weekly often strains just about every worker’s patience. As an alternative, there are miniaturized versions of the safety meeting that capture chunks of important information without putting your team through long lectures on safety writ large. That said, safety meetings are usually the only venue in which the safety system as a whole gets discussed, including discussions of training cycles, compliance with industry standards, updates to current procedures, and new types of docaugmentation. Bite-sized safety meetings are appealing, but they rarely allow time to dive into how the company’s approach toward safety can be improved. They are more concerned with refreshing and ensuring compliance with the procedures and processes that are already in place.
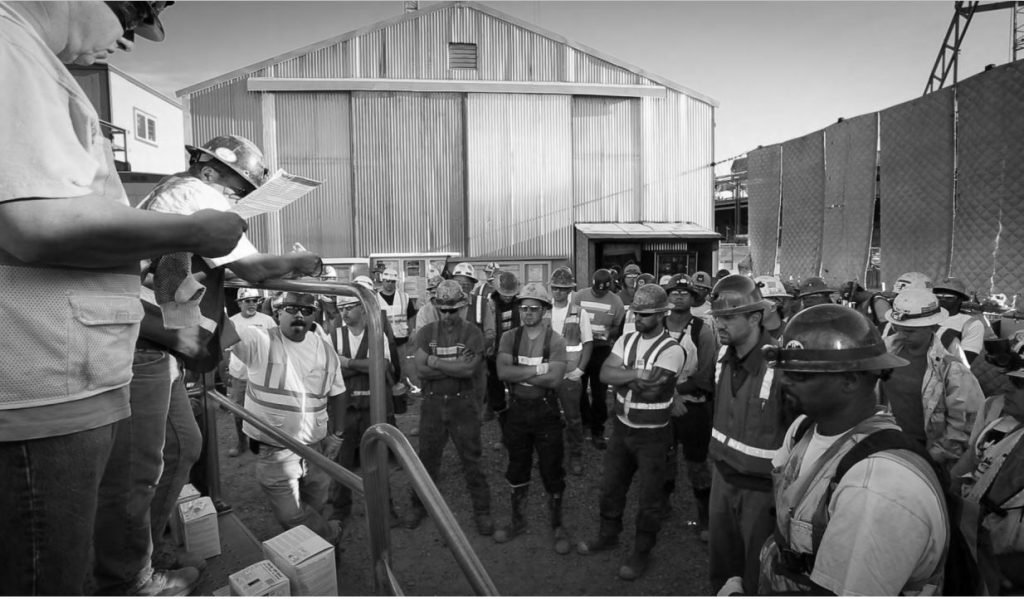
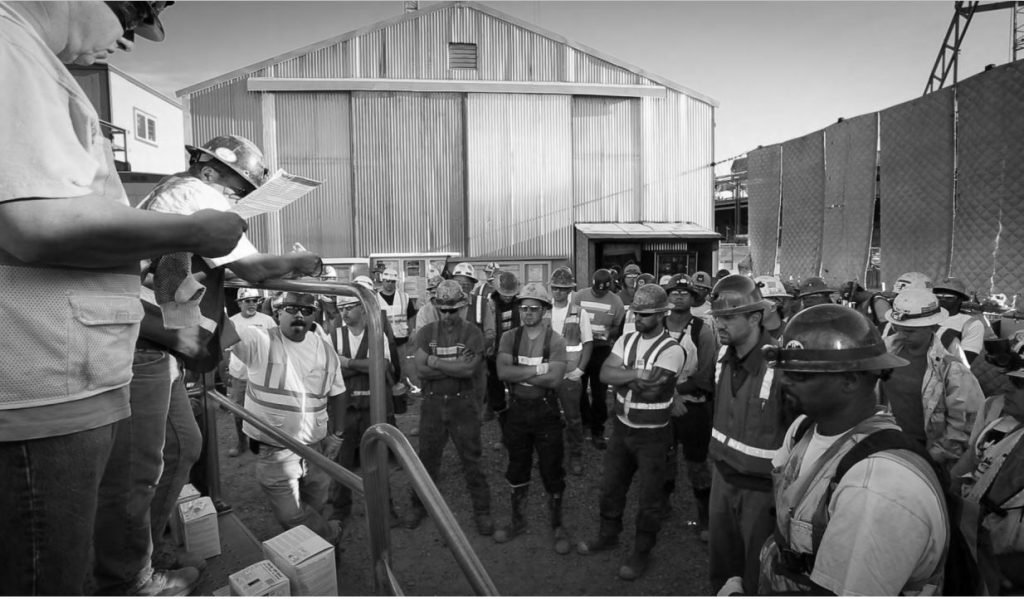
SAFETY TALKS AND SAFETY MOMENTS
Safety talks are safety meetings lite. They go by different names in different workplaces – toolbox talks, safety briefings, tailgate meetings – but they all have the same format: short, informal, and straight to the point. It’s a good approach for doing basic safety checks, covering the hazards for the day, and sharing relevant safety information. The toolbox talk is not a training tool (the assumption is that the training is already taken care of) but a refresher on the vital points covered in training can be included. Because these are just 10-15 minute chats with the team at the Jobsite, there’s a tendency to skip documenting it. This is a mistake. The safety talk is one of the biggest opportunities to bend the curve on near misses and serious incidents on a job site. Toolbox talks get the team thinking about their environment, the hazards they face, the risks associated with the work they’ll perform during that shift, the PPE needed to work safely, and any other points the safety manager wants to make sure is at the top of their minds. Tracking the content of the safety talks over time and comparing it with near miss and incident reports by job phase and type will help you tailor safety talks. If certain project phases are plagued with a particular set of near misses and incident risks, those become topics in the safety talk. Proactive hazard communication and task-specific safety reminders on even basic topics have a much better chance of reducing incidents because they prime up your team right before they start doing the work instead of relying on a training session that took place three months ago.
Safety moments are an even smaller slice of training time. Although they are often included as part of safety talks and safety meetings, safety moments can be used as stand-alone primers that can be rolled out at any time. They are the smallest unit that builds towards a true safety culture. While they can be focused on the job at hand, they are generally broader, covering anything from the importance of proper PPE to winter driving safety. The topics can even go beyond workplace safety in order to remind employees that they also need to make safety part of their personal lives. In the hands of a well-informed safety manager, safety moments can be used to reinforce organizational training while also catching important seasonal milestones – snow shoveling safety moments after the first snow of the season, for example. A database of safety moments and a digital record of when they were last used is, of course, a big help in keeping the communications organized.


SAFETY CHECKLISTS
Of all the traditional safety tools that have been updated by mobile technology, safety checklists have improved the most. The concept behind a checklist is sound. It forces a worker to take a moment to confirm that safety checks have been done and that safety processes have been followed before work starts or finishes. As a paper form, however, it faced a number of practical limitations. The big one is the inconvenience of making workers who are already loaded with tools and PPE carry around a clipboard and pen (with a backup in case the ink dries out). With everything workers need to keep on their person or close at hand, these extra items add to their pre-existing reluctance to spend much time fussing over paperwork. It’s no surprise, then, that many safety managers have stories of discovering pre-filled safety checklists forgotten in the cab of a crew truck. And sure, it may be because the crew didn’t want the forms to get blown away or rained on, but pre-filling a checklist away from the actual Jobsite defeats the whole point of having a checklist in the first place. Fortunately, the latest technologies make the whole thing digital and internet-enabled. This removes the paper part of the paperwork, speeds up record filing, and adds the ability to confirm that safety processes are being followed almost in real-time. Now a safety checklist can be submitted digitally and include pictures confirming that lockout procedures have been properly performed and hazards have been marked. This level of documentation is incredibly powerful for safety compliance as well as for accurate work tracking on large projects. With the data flowing back and forth, the safety checklists can be tailored to the job being done, which reduces the burden of filling out a form where only five of 20 boxes actually apply to the work. With all these advancements, mobile technology has made the safety checklist relevant once again.
1 thought on “The connection between Near Misses and Incidents”