The 5 Main Hazards to the Eyes and Face
8 min readWe perceive the world through our senses. And although we have five of them, we often give vision pride of place.
In their 2002 book Telling Ain’t Training, researchers Dr. Harold Stolovitch and Dr. Erica J. Keeps make the case that when analyzing a situation, vision is responsible for 83% of all received information, followed by hearing for 11% and the other three collectively making up the last 6%. Sight is by far our most important sense in perceiving the world around us and allowing us to function at work and home.
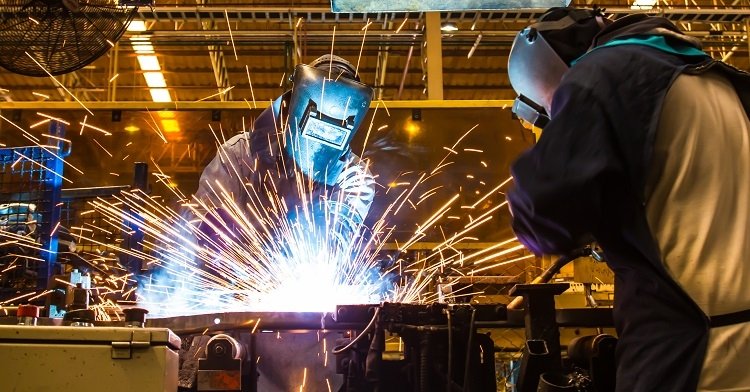
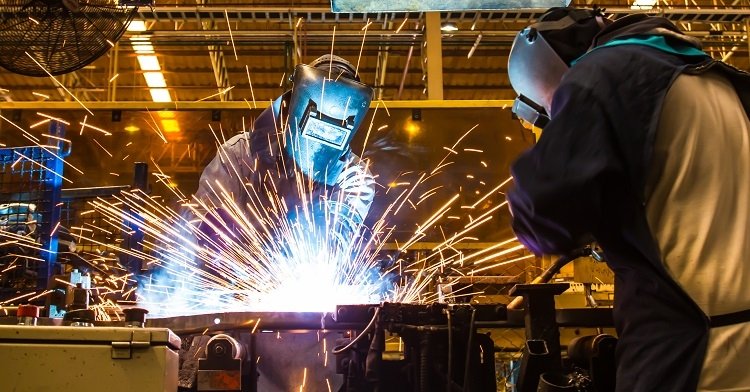
According to the CDC, 2,000 US employees sustain work-related eye injuries that require medical treatment per day. And more than 100 of these injuries require more than one day away from work. It is also estimated that eye injuries alone cost U.S. industries more than 300 million each year in lost production time, medical expenses, and worker compensation. Oh, and some of us are literally left in the dark!
Our eyes and sight receptors are fragile and can’t regenerate. It’s extremely important that we protect them adequately.
What OSHA Says
Eye and face protection is addressed in standard CFR 1926.102. It states that “The employer shall ensure that each affected employee uses appropriate eye or face protection when exposed to eye or face hazards from flying particles, molten metal, liquid chemicals, acids or caustic liquids, chemical gases or vapors, or potentially injurious light radiation.“
This opening statement helpfully provides us with the top five workplace hazards that put the eyes and face at risk:
- Impact from flying particles
- Exposure to high temperature
- Exposure to chemicals
- Fine particles (dust)
- Radiation
Regardless of the type of protection needed, eye protection shall meet the following minimum requirements:
- Distinctly marked to facilitate identification of the manufacturer
- Provide adequate protection against the particular hazards for which they are designed
- Reasonably comfortable when worn under the designated conditions
- Snug fit that will not unduly interfere with the movements of the wearer
- Durability
- Safe design and construction for the work to be performed
- Capable of being disinfected
- Easy to clean
Types of Eye and Face Protection
The CSA Standard Z94.3.1-16 Guideline For Selection, Use, And Care Of Eye And Face Protection cited by CCOHS divides the eye and face protection in the following classes:
- Class 1: Safety glasses
- Class 2: Goggles
- Class 3: Helmets
- Class 4: Hand shields
- Class 5: Hoods
- Class 6:Â Face shields
The 5 Main Hazards to the Eyes and Face
Impact
Impact hazards are those in which a particle coming into contact with the eye at high velocity could produce physical damage to the eye, which could result in physical injury, inducing a degenerative condition, or the loss of sight. The particles that cause impact hazards are usually the result of tasks that involve breaking or cutting materials (such as chipping, drilling, grinding, and sawing).
OSHA standard 1926.102(a)(3) stipulates that if flying objects have the potential to enter an employee’s eye, the employer should ensure the employee uses eye protection with side shields. This should protect against most impact hazards, but there have been many reported cases where employees were wearing the recommended eye protection with side shield but were still injured by a flying particle that found just the right angle to get through the gap between the eye protection and the face.
While CSA Z94.3.1-16 seems to suggest that just about any equipment form Classes 1, 2, 5, and 6 (glasses, goggles, hoods, and face shields) would do, it makes more sense to use double eye protection when facing this hazard. That is, safety glasses and a face shield. In combination, they provide a higher degree of protection, not only to the eyes, but also to the face.
High Temperature
Exposure to high temperatures is damaging to our eyes because they need to be wet in order to function properly.
Hazardous heat usually emanates from industrial processes, such as furnace operations, pouring, casting, welding, or hot dipping. Direct contact with these hot substances can result in immediate and irreparable damage to the eyeball.
Depending on how hot the material and the environment are, the appropriate PPE can range from safety glasses with side shield or safety goggles to face shields and hoods. As above, in order to protect the face and not only the eyes, PPE that provides more coverage (like face shields and hoods) is preferable.
Exposure to Chemicals
When it comes into contact with a chemical substance, the eye will sustain a chemical burn. The more distant that substance’s pH is from the pH of our eyes (about 7.5, give or take some decimal points), the more severe the damage. That means both alkali (pH 7 to 14) and acids (pH 0 to 7) have the potential to create serious eye and face injuries.
If you want to know the pH of the substance you’re working with, check the Safety Data Sheet (SDS).
Although both can harm the eye, alkali burns are more dangerous than acid burns because alkali have a higher penetration, meaning they can not only cause damage to the external structure but also the internal structure of the eye.
Keep in mind that you don’t have to splash the substance directly in the eye to sustain a chemical injury. Mists, vapors, and fumes in the working environment can be absorbed through the eyes and cause damage.
Chemical burns represent 7-10% of all eye injuries, and about 15-20% of burns to the face affect at least one eye. Most of these injuries occur at work, so an employer-specific WHMIS/GHS course is extremely important in teaching employees about the physical and chemical properties of the substances in the workplace and how to work safely with or around them.
According to CSA standard Z94.3.1-16, goggles, hoods, and face shields are recommended for working with chemical substances.
Where splashes are a concern, you should consider potential gaps in your PPE. Using a face shield might seem perfectly fine when you are looking down and the shield is touching your chest, but when you are looking up, the shield follows your face and leaves your neck and chest exposed. Hoods attached to a suit or a one-piece suit might be a better choice in such environments.
Eyewash Stations
Chemical substances do not just damage the eye on contact. Many of them (especially corrosive substances) continue to burn and cause eye damage after the initial contact is made.
The eye is wet and water makes a good solvent. Once diluted by water, chemicals are spread over a larger surface than the impact area, resulting in more damage. This is why it is imperative that employees working near chemicals have proper access to an eyewash station where they can further dilute and flush away harmful substances.
On a construction site, where the likely hazard are non-chemical substances like dust and concrete, an eyewash bottle or spray might be adequate. Where exposure to more hazardous chemical might occur, however, an eyewash station capable of providing minimum 15 minutes of continuous flow is recommended by ANSI Z358.1-2014. The longer the continuous flow the better (plumbed stations being great for this), since a longer flow allows for more time to clean the eye and for emergency services to arrive.
Chemicals and Contact Lenses
For a long time, it has been common practice to discourage the use of contact lenses when handling chemicals. However, he myths behind this recommendation have recently been dispelled.
The American College of Occupational and Environmental Medicine (ACOEM) considers contact lenses to be safe when handling dangerous chemicals in the workplace. They do note, however, that contact lenses do not constitute protective devices. There are, moreover, a handful of substances that both the ACOEM and OSHA (29 CFR 1910.1052 Appendix A and 29 CFR 1910.1450 Appendix A) caution can create additional hazards for those who wear contact lenses, and discourage handling them when wearing contact.
Exposure to Fine Particles (Dust)
This is probably the most common cause of eye injury in the workplace, since dust is ubiquitous. Operations such as woodworking and buffing have more exposure than office work, and PPE should be worn when performing these activities or agitating the air in these workplaces (e.g., when cleaning).
To protect against dust, a proper seal around the eyes is essential. OSHA seems to indicate that safety goggles are the PPE of choice, while CSA standard Z94.3.1-16 offers a wider range of option when selecting PPE to protect against flying particles and dust (sealed glasses, goggles, hoods, and face shields).
One consideration for dusty environments is that dust settles on everything, including on PPE. Special care should be taken when removing the PPE to avoid particles falling and reaching the eye.
Storing the PPE in the work area can also result in dust accumulation inside the eye protective equipment. Store them, instead, in a clean location, and make cleaning the PPE common practice.
Exposure to Radiation
Although radiation sounds like the kind of thing that would only affect a minority of employees, the reality is that optical radiation affects all of us, albeit to varying degrees.
Sunlight is one of the mildest forms of optical radiation, but continuous exposure to sun’s UV radiation can result in sight damage. As such, tinted, UV-treated sunglasses should be provided for employees working outdoors.
Welding is another common source of optical radiation. This could take the form of high intensity light (cutting with acetylene torch) or UV (MIG, rod welding). While properly tinted goggles are sometimes acceptable for cutting with a torch, a welding helmet or hand shield are always recommended to provide impact and irradiative protection for the whole face.
Lasers can create concentrations of heat as well as UV, IR, and reflected light radiation. Exposure to these can produce a series of eye injuries, from retinal burns, to cataracts and even permanent blindness. OSHA recommends assessing the laser’s intensity and providing protective glasses that are rated for the highest intensity the laser might produce. CSA standard Z94.3.1-16 recommends Class 2D goggles.
If you’re not sure how to choose the proper PPE for lasers, either contact the manufacturer and ask for their recommendation or take the laser specifications to your PPE provider and have them provide a PPE to match those specifications.
Conclusion
It is important to remember that, more often than not, employees are exposed to more than one hazard at a time. Your chosen PPE should protect them from all of the hazards they face at once. Sometimes, that will mean combining several types of eye and face protection.
Perform a proper hazard assessment and consider the hazards before your personal preferences. Make sure the PPE you select minimizes the exposure to an acceptable level. Eye and face injuries are common and sometimes very serious and irreversible. They should not be taken lightly.
Click here for more of our Personal Protective Equipment content.