Maintaining your safety for maintenance workers
15 min read
Maintenance workers maintain all aspects of operations and equipment. They are such an important part of the process that they feel pressure to get all repairs done fast! In this article, maintenance workers learn how to overcome the pressure and redouble their efforts to always follow safe work procedures. Also featured are reenactments of common maintenance incidents, testimonials, and examples of safe work practices.
- Why maintenance workers must overcome the pressure to skip safety procedures.
- Why a job hazard analysis should be conducted before beginning a new task.
- Why all LOTO procedures must be followed to control energy sources.
- The responsibilities for those workers who are qualified to do electrical work.
- What precautions employees must take to prevent falls when performing jobs that are above ground level.
- Why we must always choose the proper tools for the job and use them safely.
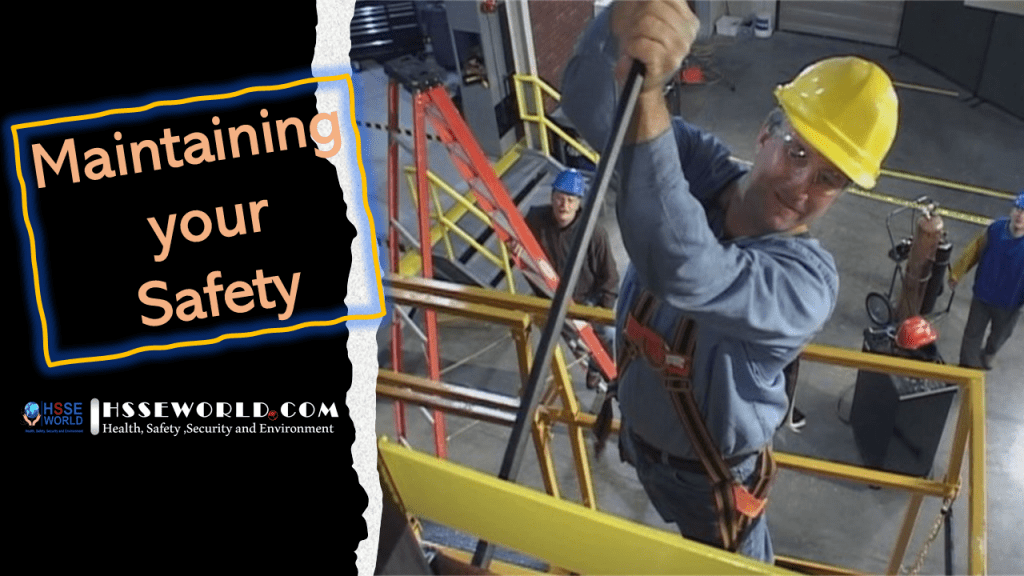
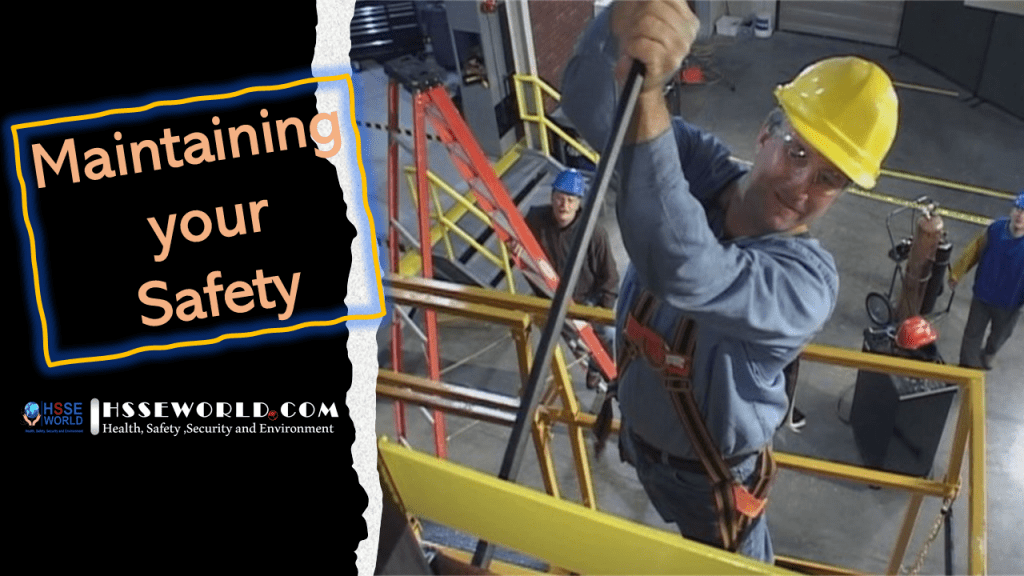
Safety must be the maintenance worker’s first priority
- No matter where we happen to work or what products we make, it takes a variety of systems and processes, tools and equipment, machines and instruments, and of course, personnel to put it all together and make it happen. In addition to making products, keeping ourselves and our co-workers safe each day is our top priority.
- When everything is up and running properly, staying safe is easy: stay inside marked walkways, observe and follow instructions on safety signs, don’t reach into machinery or remove guarding and stay on the safe side of guardrails.
- We all know things don’t always go as planned, and when our processes and equipment need service or repair, there is a group of workers who must leave the sanctuary of marked aisle ways and guardrails in order to perform the critical work needed to keep our facility up and running.
- These are the maintenance workers, and their work is critical to our operation. Due to the nature of their work, maintenance workers have the potential to be exposed to hazards from which other workers are protected.
- While their work maintaining our equipment and processes is important, maintaining their own safety must be the first priority of every maintenance worker.
Overcoming pressure to skip safety procedures
- A crane operator attempting to move a pipe for shipment says to his supervisor, “See, I told you. The crane hook won’t lower down, so I can’t get this pipe moved up the line.”
- “that’s the last piece of an order that has to truck out today. There’s a late penalty built into the contract, plus more costs if the trucker can’t get going,” his supervisor responds. “can’t you do something?”
- The operator replies, “I called maintenance. I don’t know what else to do. They’ll take care of it.”
- “I called maintenance. They’ll take care of it.” A lot of hope, expectation, and trust is built into those words. One of the biggest hazards a maintenance worker faces occurs before he ever starts a job: the expectations and pressures placed on him by affected workers, supervisors, and even other maintenance workers.
- After the crane operator and supervisor tell the maintenance worker they are counting on him, he says, “I’ll get it fixed as quick as I can, but first, I need to get the crane rail and pipe trolley locked out before I can get up there with the boom lift.”
- “how long will that take?” Interrupts the supervisor. “how about I stand guard over the e-stop on the pipe cradle line and mike holds up the other crane operators by radio?”
- “Sorry guys, but your crisis is not worth my life,” replies the maintenance worker. “that’s why we have maintenance procedures in the first place. I’ll keep you posted.”
- In an interview, one maintenance employee says, “in maintenance, you just have to follow the procedure every time, no matter what.”
- “it usually takes several things to go wrong before a crisis develops. People need to understand that it’s going to take several steps to make everything right again; it’s going to take time. Skipping steps gets people hurt and ultimately takes even longer” adds a second worker.
- A third worker concludes, “there’s always pressure coming from somewhere to ‘get it fixed fast.’ when cooler heads prevail, everyone agrees that it doesn’t make sense to risk a life to fix a piece of machinery, but until that happens, it’s up to you, the maintenance worker, to be the one with a cool head because it’s your life on the line if you don’t.”
Failing to follow safe work procedures
- That’s good advice, because failing to follow safe work procedures, no matter what the reason, injures and kills many maintenance workers each year.
- For example, failing to follow line-breaking procedures such as blocking and bleeding can lead to chemical exposure and burns.
- Failing to follow lockout/Tagout procedures, including testing your lockout, can expose you to the unexpected start-up of machinery.
- Performing electrical troubleshooting without following safe electrical work practices can lead to electrocution or burns from an arc flash.
Job hazard analysis
- Following safe work, procedures are critical to maintaining your safety and every procedure should include a hazard analysis.
- “once you arrive at the location where you will be working, you need to do a quick hazard assessment to understand what is going on around you that may get you hurt,” says one maintenance worker.
- Another worker adds, “recognizing hazards is one of the most important skills a maintenance worker can develop.”
- Study the area for moving equipment or the actions of nearby machines that could strike you, pinch you, or pull you in.
- Look around for stored or potential energy sources, which may release suddenly. Examples include pressurized lines, gravity-fed vessels, and hoppers, as well as elevated stored materials, which could fall.
- Don’t forget to look overhead for hazards, especially cranes, hoists, and other elevated material handling equipment, which could move into your work area unexpectedly.
- Be sure to evaluate your work area for slip, trip, and fall hazards. Loose items, open holes, or slippery surfaces cause many injuries each year.
- A proper hazard analysis allows workers to identify those things which could hurt them while working. More importantly, it allows workers to correct or control those hazards before beginning a new job task.
( Learn the steps-to-conducting-an-effective-job-safety-analysis-jsa/)
Lockout/Tagout
- “lockout is a way to keep the machine from starting while you work on it, all in all, a pretty important concept,” a maintenance worker says when interviewed.
- A pretty important concept? More like a life and death concept. Following lockout/Tagout procedures are the heart and soul of safe maintenance operations.
- Every system, machine, tank, pipe, motor, or piece of equipment can hurt you if the energy sources connected to it are released while you are nearby or in the line of fire.
- “lockout/Tagout controls the dangerous parts of a machine while you work on it. It keeps you from getting hurt if you do it,” notes a maintenance employee.
( watch video about lockout-tagout-safety-training/)
Neglecting lockout on machine results in amputation
- Controlling hazards by locking and tagging a system’s energy sources is a simple, yet critical concept, but one not fully appreciated by Jason Montague as he was adjusting and greasing the chain drives on the mixer line.
- “before he started, Jason asked me if the motor was off. He couldn’t see the controls from where he was. I said it was because I had just pressed the stop button then left the area,” a co-worker says.
- Jason removed the guarding and began the process of greasing and tightening the chains. Unbeknownst to Jason, another worker was passing by the control station and questioned why the line was not running.
- In the split second, it took for that worker to push the start button, Jason’s fate and his future as a double amputee were sealed as his arms were pulled into the chains and gears of the moving machine.
- That’s why lockout/Tagout procedures must be followed; they contain specific steps to prevent this type of needless tragedy.
- Before starting any job, identify and control all sources of energy connected to the equipment. Be aware that some equipment is fed from multiple power sources.
- Be sure to control the force of gravity as well as hydraulic and pneumatic systems, which could cause equipment to move unexpectedly.
- Consult the written lockout procedure if you are unsure about a particular piece of equipment or process.
- Remember that a lockout is not complete until it is tested.
- Many pieces of equipment and power supplies look alike and have similar labels. Serious injuries occur each year when maintenance workers lock out the incorrect power supply before servicing a piece of equipment.
- Prevent this by attempting to start the machine using its normal operational controls, as well as any remote or automated controls, to ensure the lockout has been done properly.
Qualified electrical work
- In many cases, maintenance workers are also qualified electrical workers. A qualified electrical worker is trained to recognize and avoid the hazards associated with energized electrical parts.
- Energized parts present two main hazards. First is the danger of electric shock and second is the danger presented by an arc flash.
- At a minimum, when working near exposed parts over 50 volts, electrical workers must wear rubber-insulated gloves for shock protection.
- For protection from an arc flash, electrical workers must wear arc-rated clothing, head and face protection, and other PPE rated for the incident energy of a potential arc flash.
- Arc-rated clothing, unlike cotton and other fabrics, will not burst into flames and burn when exposed to the intense heat of an arc blast.
- Qualified electrical workers must understand how to properly select and use appropriate shock and arc flash protection when exposed to energized parts.
- If you are not sure what type of PPE is needed for a particular job task or piece of equipment, stop and find out.
- Be sure to establish an appropriate boundary to keep unqualified workers a safe distance from energized parts. Failing to establish an approaching boundary could allow an unqualified worker to come in contact with live parts or be exposed to an electrical arc flash.
- Understand that equipment is not considered de-energized until you have verified with a working voltmeter that no voltage exists; therefore, when testing for zero energy, you must treat the equipment as energized and wear all appropriate arc flash protection until an electrically safe work condition is verified.
- Identifying and controlling electrical hazards is an important part of any job hazard analysis. To repeat an important point, a qualified electrical worker is able to recognize and avoid electrical hazards.
- If you don’t know how to select protective equipment for arc flash and shock protection or understand how to determine the distance of approach boundaries, then you are not qualified to work on or near energized electrical parts.
( learn more about electrical-contact-release/)
Ladder safety
- Once all hazards are analyzed and controlled, maintenance workers must consider and plan how they will safely access the work to be done. If the work is elevated, this often means using a ladder.
- Just like all tools and equipment, ladders can make our work easier and safe when they are used properly. Proper use begins with an inspection.
- Check all rails and rungs for damage and slippery substances. Don’t forget to check the soles of your shoes; simply slipping off a rung is one of the more common ladder injuries.
- Make sure spreader bars are operational and that the ladder’s feet are in good condition.
- Of course, like any other tool, using the correct ladder for the job is of utmost importance. Similar to how an incorrectly sized wrench won’t fit a nut and may slip, an incorrectly sized ladder won’t properly fit your work situation; however, in this case, it’s you who may slip.
- A properly sized a-frame ladder will allow you to reach your work while keeping the top of the ladder at waist level. You have better balance when your waist can serve as a point of contact with the ladder.
- When using straight or extension ladders, keep your waist at or below the top of the ladder.
- To ensure a stable base of support for a straight ladder, it should be placed one foot away from the wall for every four feet the ladder rises. For example, if the ladder contacts the wall at 12 feet, the feet of the ladder should be placed three feet from the wall.
- No matter what type of ladder you use, position it so you can keep your belt buckle between the rails while working. Leaning beyond the rails to reach your work can lead to a fall; instead, climb down and reposition the ladder.
- When using straight or extension ladders to access another level, the rails must extend above the platform by three feet and be tied off securely.
- If your ladder is too short to allow you to reach your work while keeping your waist below the top rung, then the ladder is too short and is not a proper fit for the job.
- Of course, most maintenance workers already know how to use a ladder safely; the real problem is when they simply choose not to. Remember, there is never a good reason to risk your life while on a ladder.
- “I always treat ladders with respect and a bit of fear. I know guys who have fallen just four feet and died,” says one maintenance worker.
- Another employee adds, “whether it’s a ladder, lift, or an elevated platform, making sure I don’t fall is the number one concern.”
( learn how to inspect your ladder )
Elevated work platforms
- Falling is a real hazard for maintenance workers. In addition to ladders, there are other ways maintenance can access elevated work areas.
- Elevated lifts and mobile working platforms are other common method of accessing elevated work. In fact, this equipment is often preferred to a ladder as it provides a stable, secure working surface and has guardrails for fall prevention.
- Mobile lifts, like all other equipment, require training and authorization prior to use. Never use the equipment for which you have not been trained and never allow co-workers who have not been trained to operate this equipment.
- Lifting platforms have very unique and specific stability characteristics which must be followed to prevent tip-overs. Many tip-overs are caused when workers subject lifts to uses and loads for which they are not designed, often in a misguided effort to be a problem-solver and get the job done quickly.
Problem-solver killed when side-loaded scissor lift tips over
- Martin parker was known as a problem-solver. He had lots of skill and experience doing a large variety of jobs and seemed to always know a way to get a hard job done quickly.
- “martin kind of took over the job once he showed up. We were about 15 feet up and needed to bust loose an old pipe from its clamps, and the nuts were stripped off,” says one of his co-workers. “most of us wanted to go get a grinder and cut the nuts off. Martin insisted on taking a big pry bar up there and kind of try to force it loose. He kind of got his back up about it saying we just didn’t know how to get things done.”
- “you guys just don’t know how to get a job done,” Martin said to the workers standing around the lift. “sometimes, you just got to go with what you got handy and make it work. I’ll take care of it.”
- Once martin “got his back up” about how he wanted to fix the problem, he was letting his emotions control his actions rather than following his training—a very dangerous situation for any worker, especially a maintenance worker.
- A scissor lift, when fully elevated, is only designed to support its rated load vertically, straight up and down. It is not designed for side-loading, and when martin put all his effort into the pry bar, it didn’t take much force to turn the lift over, killing him.
- “We all received the same training on the lifts, but I guess martin forgot about not side-loading,” says martin’s co-worker.
- Martin was trained and authorized for the lift he was in; he knew not to sideload the lift. More likely, what he forgot was not to let his emotions impact his safety, an all too common mistake.
- Similar mistakes maintenance workers make while using lifts are overloading them with equipment and tools, failing to deploy stabilizers, using the lift as a crane or to push or pull objects, and finally, climbing out of a lift to more easily reach their work or to access another elevated surface is all too often a fatal mistake.
- Of course, wearing required restraint devices will not only prevent workers from climbing out of the basket, it will also keep them from being ejected during a collision with another moving vehicle.
- All of these unsafe actions are prohibited and are not part of any safe work procedure; and yet, maintenance injuries and deaths continue to occur from just such actions. It serves to underscore the fact that it takes more than safety training to stay safe; it takes a safety commitment.
Fall arrest equipment
- An important part of a maintenance worker’s commitment to safety includes the use of fall arrest equipment. Fall arrest systems are designed to minimize injury should a fall occur.
- In addition to keeping you from hitting the ground, a fall arrest system will reduce the amount of force placed on your body during a fall, either by using a shock-absorbing lanyard or by limiting the fall distance to just a few inches by means of a quick-stop device.
- “some workers work above ground quite frequently and may even lose respect for it; that can be a very dangerous thing,” says a maintenance worker.
- Another employee adds, “most people nowadays wear seatbelts, right? So I just don’t get those people who resist tying off in a fall harness. That concrete is awfully hard, you know?”
(learn what-is-the-difference-between-fall-protection-and-fall-prevention/ )
A worker without fall protection falls to his death
- Just like seat belts in your car or truck, fall restraint systems can save your life, but they do no good when left unconnected. As Larry Fitzgerald found out, no matter how many times you have done a certain task without incident, it only takes once to become a statistic.
- “Larry had worked that area for years and as far as I know, always wore his harness and lanyard. That’s why I was surprised when I saw him up there without being tied off,” says a co-worker. “I was going to say something, but I thought he knew what he was doing.”
- Larry’s co-worker turned away without speaking up and larry started his usual and familiar routine of inspecting the elevated tank. It’s when maintenance tasks become usual and familiar that unexpected incidents occur.
- The investigation revealed that larry tripped over his own tools as he backed away from the tank, causing him to fall to his death.
- As a maintenance worker, larry had been trained many times in the use of fall restraint systems. It wasn’t a lack of knowledge that killed him; larry’s fatal mistake was a lapse in his personal commitment to safety.
Using tools safely
- To maintain our safety, we must also be aware of the dangers presented by the items we use the most: our tools.
- We have all heard the oft-repeated mantra of “use the right tool for the job,” so why do we still skin our knuckles when pliers slip on a nut when a wrench was the proper choice?
- Why do we use improperly sized screwdrivers, which slip, cutting or stabbing hands, arms, even eyes? Like any other safety decision, we just decide to select the correct tool and use it properly.
- It’s an easy choice when the correct tool is handy, but it takes extra effort when it involves a return trip to the tool room. Maintaining your safety means making time to gather the proper tools rather than risking injury by making do with what you have handy.
- Always wear the proper PPE for whatever tool you are using. Remember, PPE is your last line of defense when things go wrong.
Conclusion
- As for maintenance workers, we follow procedures and have a work plan, but despite our best efforts, things don’t always go as expected. This is why taking steps to maintain our safety is so important.
- Perform a job hazard analysis to identify hazards.
- Follow lockout/Tagout procedures as well as other safe work practices to control hazards.
- Use fall protection, arc-rated clothing, and other personal protective equipment to protect against the unexpected.
- In this article, we have discussed just a few ways maintenance workers can stay safe while working. The list of potential hazards to which maintenance workers are exposed is endless, and no program can discuss them all.
- This is why your attitude and commitment to safe work practices is so important. A good safety attitude helps resist the pressures placed on maintenance workers to “get it fixed fast” and allows you to perform a hazard analysis and follow safe work procedures on every job you perform.
- Always remember, maintaining your safety is the most important maintenance job you have.