Introduction to industrial ventilation
Ventilation is the mechanical system in a building that brings in “fresh” outdoor air and removes the “contaminated” indoor air.
In a workplace, ventilation is used to control exposure to airborne contaminants. It is commonly used to remove contaminants such as fumes, dust, and vapors, in order to provide a healthy and safe working environment. Ventilation can be accomplished by natural means (e.g., opening a window) or mechanical means (e.g., fans or blowers).
Industrial systems are designed to move out (exhaust) and bring in (intake) a specific amount of air at a specific speed (velocity), which results in the removal of undesirable contaminants. While all ventilation systems follow the same basic principles, each system is designed specifically to match the type of work and the rate of contaminant release at that workplace.
So what is the purpose of an industrial ventilation system?

Ventilation is considered an “engineering control” to remove or control contaminants released in indoor work environments. It is one of the preferred ways to control employee exposure to air contaminants.
Other ways to control contaminants include:
- eliminate the use of the hazardous chemical or material,
- substitute with less toxic chemicals,
- process change, or
- work practice change.
The purpose of a ventilation system
There are four purposes of ventilation:
- Provide a continuous supply of fresh outside air.
- Maintain temperature and humidity at comfortable levels.
- Reduce potential fire or explosion hazards.
- Remove or dilute airborne contaminants.
The main parts of an industrial ventilation system?
An industrial ventilation system has two main parts: a fresh air supply system and an exhaust system.
In general, the supply system is a heating, ventilation, and air-conditioning system (HVAC) and consists of:
- air inlet,
- air filtering equipment,
- heating/cooling equipment,
- fan,
- ducts,
- air distribution registers.
The exhaust system consists of:
- an “air intake” area,
- ducts to move air from one area to another,
- air cleaning device(s),
- fan(s) to bring in outside air and exhaust the indoor contaminated air, and
- discharge stacks.
The basic types of ventilation systems
There are two types of mechanical ventilation systems used in industrial settings:
General industrial ventilation reduces the concentration of the air contaminants or controls the amount of heat that accumulates in hot industrial environments, by mixing (diluting) the contaminated air with fresh, clean, uncontaminated air. This ventilation system is also known as dilution ventilation.
Local exhaust ventilation captures contaminants at, or very near, the source and exhausts them outside.
The main features of dilution ventilation
Dilution ventilation supplies and exhausts large amounts of air to and from an area or building. It usually involves large exhaust fans placed in the walls or roof of a building.
Dilution ventilation controls pollutants generated at a worksite by ventilating the entire workplace. The use of general ventilation distributes pollutants, to some degree, throughout the entire worksite and could therefore affect persons who are far from the source of contamination.
Dilution ventilation can be made more effective if the exhaust fan is located close to exposed workers and the makeup air is located behind the worker so that the contaminated air is drawn away from the worker’s breathing zone. See Figures 1 to 4 for examples of better ventilation system layouts, and Figure 5 for poor dilution ventilation design.
When used to control chemical pollutants, dilution must be limited to only situations where:
- the amounts of pollutants generated are not very high,
- their toxicity is relatively moderate,
- workers do not carry out their tasks in the immediate vicinity of the source of contamination, and
- the emission rate of contaminants is relatively uniform.
It is therefore unusual to recommend the use of dilution ventilation for the control of chemical substances except in the case of solvents that have admissible exposure concentrations of more than 100 parts per million.

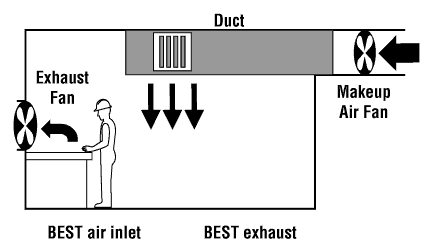

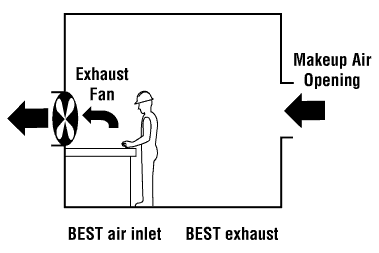
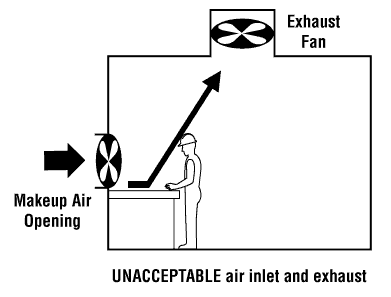
Figures 1 to 4: Examples of recommended dilution ventilation layouts
Figure 5: Example of not recommended dilution ventilation layout
The limitations of dilution ventilation
As a method for protecting workers, it is important to know that dilution ventilation:
- Does not completely remove contaminants.
- Cannot be used for highly toxic chemicals.
- Is not effective for dusts or metal fumes or large amounts of gases or vapours.
- Requires large amounts of makeup air to be heated or cooled.
- Is not effective for handling surges of gases or vapours or irregular emissions.
Regular “floor” or “desk” fans are also sometimes used as a method of ventilation, but these fans typically blow the contaminant around the work area without effectively controlling it. Opening doors or windows can be used as dilution ventilation, but again, this method is not reliable since air movement is not controlled.
As a general note, the air or “volumetric” flow rate of dilution ventilation depends largely on how fast the contaminant enters the air as well as the efficiency of the fresh air and workroom air mixing process.
The local exhaust ventilation
A local exhaust system is used to control air contaminants by trapping them at or near the source, in contrast to dilution ventilation which lets the contaminant spread throughout the workplace. Local exhaust is generally a far more effective way of controlling highly toxic contaminants before they reach the workers’ breathing zones. This type of system is usually the preferred control method if:
- Air contaminants pose serious health risk.
- Large amounts of dusts or fumes are generated.
- Increased heating costs from ventilation in cold weather are a concern.
- Emission sources are few in number.
- Emission sources are near the workers’ breathing zones.
In a general way, a local exhaust system operates similar to a household vacuum cleaner with the hose as close as possible to the place where dirt would be created. ( read more: Welding gases & fumes Exposure )
The components of local exhaust ventilation?
A local exhaust system has five basic elements (see Figure 6):
- The “hood” or opening that captures the contaminant at the source.
- Ducts that transport the airborne chemicals through the system (exhaust air) and the air that is recirculated.
- An air cleaning device that removes the contaminant from the moving air in the system (not always required).
- Fans that move the air through the system and discharges the exhaust air outdoors.
- An exhaust stack through which the contaminated air is discharged.

How do I know which type of ventilation system is best for my workplace?
All industrial ventilation systems, when designed properly, should be able to provide long-term worker protection. The two types of ventilation, dilution, and local exhaust, are compared in the following table.
The limitations of any ventilation system
Some limitations include:
- The systems deteriorate over the years because of contaminant build-up within the system, especially filters.
- Require ongoing maintenance.
- Regular and routine testing is needed to identify problems early and implement corrective measures.
- Only qualified persons should make modifications to a ventilation system to make sure the system continues to work effectively.
The following is an example of changes that can affect how a system works:
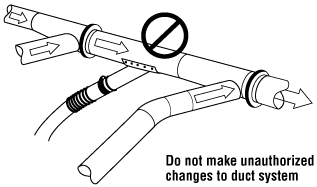
Addition of an exhaust duct branch
When an additional exhaust branch is added to an existing duct the local exhaust ventilation will pull air into the system from the new location. This will reduce the airflow from other locations that are further away from the exhaust fan. The airflow through the entire ventilation system will be affected. This change will result in a rapid plugging of the system and in an exhaust airflow, throughout all ducts, that may not be adequate enough to remove the contaminants.
What should I know about make-up air?
An important and sometimes overlooked aspect of local ventilation is the need to provide enough air to replace the air that is exhausted from the workplace. If enough make-up air is not provided when large volumes of air are exhausted, the workplace becomes “starved” for air and negative pressure is created.
Negative pressure in the workplace increases resistance on the ventilation system causing it to move less air. Air will also enter a building through cracks around doors or windows or other small openings to try to “equal” the rate of air being removed. The result is that workers may be exposed to cold air in the winter, and additional heating costs may occur.
One way to figure out if a room is under negative pressure is to open the door about 3 millimeters and hold a smoke tube (or another object that releases smoke) in front of the opening. If the smoke is drawn into the room, the room is under negative pressure. If the smoke is pushed away from the room, the room is under positive pressure. If the smoke rises straight into the air, then the pressure in the room is the same as the outside pressure.
Another way to judge if a building is under excessive negative pressure is to open a door that pushes towards the outside. If you have to pull (or push from inside) hard to open the door, the building is under negative pressure (the outside pressure is higher than inside, and forces the door shut).