Waste Management: Procedures and Disposal Options
19 min readPreviously we have been spoken about Waste Management including waste analyses and type of wastes and here we are containing the waste management to provide Practical guideline for Procedures and Disposal options which can be followed during construction projects including waste handling process.
All the wastes generated during the EPC and commissioning phases of Construction project, ranging from the most inert to the most toxic shall be collected and managed in accordance with Waste Management Plan.
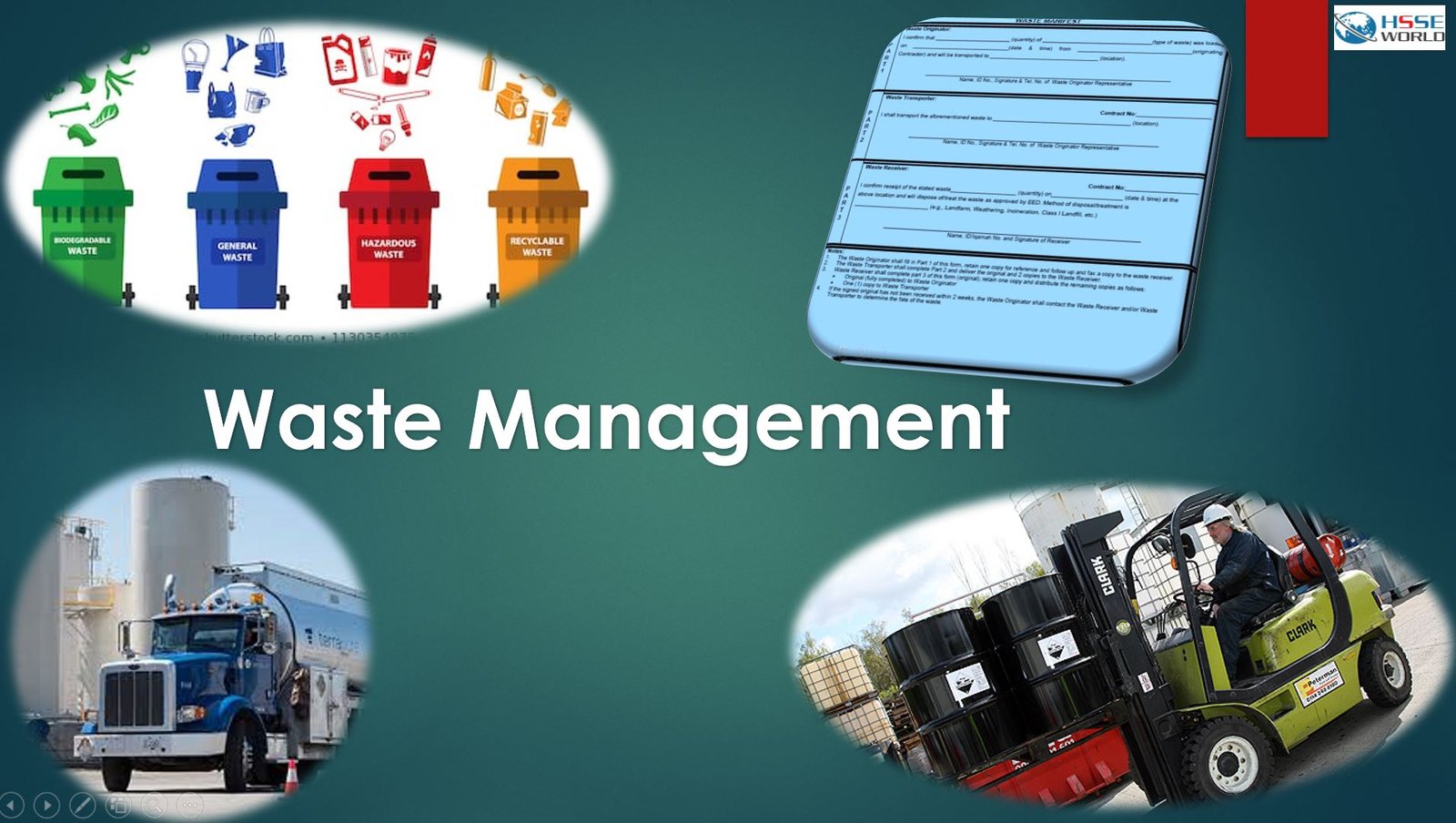
1- Waste Inventory
The Contractor HSE Manager/Environmental Coordinator shall maintain a waste inventory to keep a record of the types and quantities of waste present at the job sites. This record shall be used to monitor the effectiveness of the waste management program.
2- Waste Segregation
- Given the complex nature of the waste expected on any construction Project, Contractor will undertake a waste segregation exercise involving sorting and separating waste on the basis of its characteristics.
- Waste materials shall be segregated at source by providing colored and marked (with universal symbols and signage in Arabic and English) bins/containers for storing the waste as follows:
- Red: Hazardous Wastes
- Green: Refuse
- Brown: Plastics
- Blue: Glass
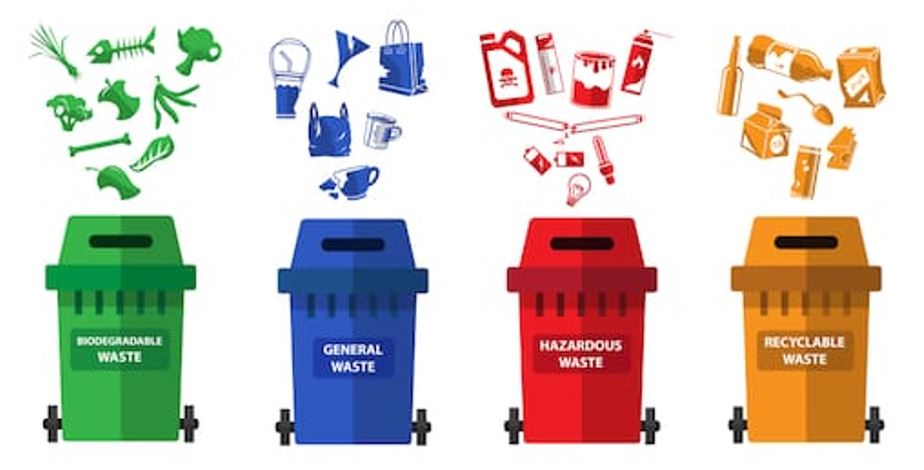
- Placing labels on bins which clearly describe, in Arabic and English and international symbols, the specific type of waste deposited in the bin/container and the precautions to be taken when handling the waste.
- Proper placement of the various bins/containers in offices, construction site, mess centers, clinics, etc.
- Placing sufficient bins/containers for each type of waste at waste collection points, depending on the variety and quantity of the wastes expected from the location.
- Effective and timely replacement of the segregated bins/containers to the waste disposal areas.
- Contractor will provide appropriate treatment of the waste through recycling, reuse, landfilling, incineration, or medical waste disposal incineration.
- A storage shed shall be constructed to store scheduled wastes.
3- Waste Collection and Storage
- All waste generated on site will be removed promptly to the central waste collection area, which will be established by the Contractor.
- Each container shall have a tight sealing lid.
- No waste collection bin/container shall be allowed to overflow before it is emptied.
- Waste storage receptacles shall be replaced promptly, in the event of damage.
4- Drum Handling
- Drum handling is commonly required for the management of hazardous materials and hazardous wastes on a site. Drum handling may be required to respond to immediate worker safety issues, such as drum leakage, improper storage of incompatible materials, or the presence reactive substances.
- Drum handling is usually implemented to un-stack, orient, and organize drums into different areas on site in order to facilitate sampling, waste characterization, and remedial action.
- Drum handling activities can involve:
- Manual movement of drums
- Mechanical movement of drums
- Drum opening
- Drum sampling
- Drum transferring
- Drum excavating
- Drum over-packing
- Drum crushing
- Shock sensitive waste handling
- Lab waste pack handling
- Shipping and transport
- Drum Handling may or may not be necessary depending upon how the drums are positioned at the site. Drums should only be handled as necessary. Prior to handling, all personnel should be warned about drum handling hazards and instructed to minimize and/or avoid unnecessary handling.
- Caution should be exercised in handling drums that are not intact and tightly sealed. Drums should be inspected to assure their integrity prior to moving, to the extent practical.
- Drums that cannot be inspected thoroughly before movement because of storage conditions should be moved to an accessible location and inspected prior to further handling. However, if severe corrosion is obvious or anticipated, it may be necessary to remove the drum contents in place.
- Personnel should not lean over drums and should never stand on top of waste drums.
- Prior to drum handling, spill response procedures and equipment/materials (e.g., over-pack drums, absorbent, cleanup equipment, etc.) should be available. The work area shall be contained within an impervious lined dike area if large quantities of drums are present.
- Manual Methods of Drum Handling
- Manual handling of drums should be used only when other mechanical means are not able to be used. Improper movement of drums by hand can result in chemical spills, back injuries, and crushed hands and fingers. Control over the drum is easily lost during manual movement, due to the shifting weight of the heavy drum (usually 500-600 lbs. when full) during handling. Whenever possible, a forklift, truck with lift-gate, frontend loader/backhoe bucket, and barrel dolly shall be used for movement.
- When manually lifting drums lying horizontally on the ground, at least two people shall be used to stand the drums upright, whenever possible. The manual lifting technique is to first size up the weight of the load to be moved and work in coordination with your partner. Grasp the top of the drum, keep feet close to the drum, back straight, head up, and use body weight and momentum to reposition the drum to an upright position. Drum up-ender bars can also be used to assist in up righting drums from the ground. When working in a sloped ground area, use the slope to your advantage by lifting the drum toward the down slope position.
- For manual movement of upright drums by rolling the drum, the drum rolling technique is to first size up the load to be moved and obtain help if needed.
- Check the path of movement for any obstacles that may be present. To break the drum (shift one end of the drum off the ground), use sturdy gloves and grab the top of the drum along the drum ring opposite from you. Make sure that hands are not positioned at a pinch point between other drums should control of the drum be lost during movement.
- Keep feet close to the drum, back straight, head up, and use body weight and momentum to reposition the drum from a flat standing position to rest on the near side of the bottom rim of the drum. To move the drum, balance the drum on the bottom rim and slowly roll the drum along the rim.
- When handling drums with a drum dolly or drum truck, first check the path of movement for any obstacles such as soft soil, bumps, potholes, and sloping ground that can impede movement.
- Forklift Use for Drum Handling
- When using a forklift to transport a load, the path shall be inspected for obstacles and the load moved at a steady pace with no quick turns. The load shall be raised sufficiently to clear the ground safely but no higher. The forks shall be tilted when ascending or descending grades.
- Forklift operators shall have a clear view of the roadway when carrying drums and have a spotter to help guide as needed. Forklift operators shall look in the direction of travel and must not move the forklift until all persons are clear.
- Forks of forklifts shall be carried as low as possible during operation. Forklift operators shall lower the forks, shut off the engine, and set the brakes (or block the wheels) before leaving the forklift unattended (operator out of sight of, or 25 feet away from the forklift).
- No personnel shall be permitted to go underneath the forks of a forklift (unless the forks are blocked). No personnel shall be permitted to ride on a forklift.
- Forklifts shall not be used to elevate personnel unless a platform with guardrails, a back guard, and a kill switch are provided.

- Heavy Equipment Use for Drum Handling
- Hydraulic excavators with drum grappler attachments, front-end loaders, and backhoes are often used for drum handling purposes.
- Drum grappler equipment can be outfitted to handle pressurized drums and shock-sensitive materials. The buckets of front-end loaders and backhoes are used to load drums and transfer to other areas. Backhoes and excavators are used to excavate buried drums.
- A hydraulic excavator equipped with a drum grappler attachment can be used to un-stack drums, move drums, open drums for sampling (with a spike attachment), place drums directly into over pack containers, and to bulk drum contents into portable tanks.
- Track-mounted heavy equipment shall be used over rubber-tired equipment in areas where the ground does not provide a firm operating surface. Use of heavy equipment with enclosed and air-conditioned cabs may minimize exposure and increase operator efficiency.
- If liquid chemical splashes from drums are likely to occur during heavy equipment handling, heavy splash shields can be placed in front of the cab of the equipment.
- Heavy equipment with high overhead projections shall not be allowed to operate within a 10-foot radius (minimum distance) of overhead power lines (Note: Overhead high voltage power lines >50,000 volts require additional distance). Use of multiple units of heavy equipment may require identification of traffic patterns to be used.
- Equipment operators must have a clear view of the roadway when carrying drums and have a spotter help to guide the operators motion as needed. Workers shall wear reflective safety vests and shall be cautioned to look carefully where they walk to avoid moving equipment and to maintain eye contact with equipment operators. No personnel shall be allowed within the swing radius of heavy equipment.
- When supplied air respirator use is required for heavy equipment operation, an independent air supply system shall be required. A breathing air cylinder, pressure reducing regulator, pak-alarm, and short supply hose can be used.
- The breathing air cylinder shall be secured to the heavy equipment with a chain and come-a-long or equivalent. The equipment operator shall be provided with an auxiliary 5-minute escape SCBA in case of any failure of the airline respirator system.

- Drum Transfer
- Drum transfer is the process of transferring solid or liquid materials from drums into other drums or containers. This may be required when a drum cannot be moved without rupture, leakage, or spillage. Transfer operations should be completed by personnel who are knowledgeable and experienced in such procedures.
- Solid materials are often manually transferred using shovels. Drum contents can also be emptied into a front-end loader/backhoe bucket for consolidation. Presence of windy conditions may impact transfer operations. Use of water spray or other dust control measures may be needed when transferring solid materials.
- The manual transfer of liquid materials is often completed using disposable plastic hand pumps or “pogo” pumps. Pneumatic pumps can also be used to transfer larger quantities of materials from drums. Care must be taken not to overfill the receiving container during transfer activities.
- Ensure that the pump, transfer hoses and fittings, and container selected are compatible with the material to be transferred. Proper bonding and grounding techniques are required when transferring flammable or combustible materials. Also, any electrical equipment used for the transfer of the flammable liquids must be of an approved type for such usage.
- Vacuum trucks outfitted with “stingers” are commonly used to collect liquids from drums for consolidation or bulking purposes. Vacuum hose connections must be secured during transfer. The hose ends must not be distorted, hose gaskets in place, and the ears to cam-lok fittings must be tightly closed.
- Plastic tie straps or wire can additionally be used to secure the closure during pumping. Personnel should stand upwind of the vacuum truck pump exhaust during transfer. Hoses shall be added to the vacuum truck pump exhaust and directed away from the work area and any ignition sources.
- Combustible/Flammable Liquid Transfer
- Special procedures are required during the transfer of combustible or flammable liquids due to the potential fire hazard associated with these materials. All ignition sources must be eliminated from areas where combustible or flammable liquids are stored or where transfer operations are to occur. No smoking, hot work, or other spark producing activity shall be allowed. Static electricity producing equipment shall be grounded and/or bonded whenever transferring flammable/combustible liquids or when working in areas where flammable/combustible materials are present.
- The vapor displaced from the container being filled should be managed to provide a suitable discharge location.
- Portable multi-purpose fire extinguishers shall be maintained on-site, kept fully charged, inspected monthly, and serviced annually. Portable multipurpose fire extinguishers shall be placed within 75 feet of active work areas where flammable/combustible materials are present.
- Bonding and Grounding Procedures
- Bonding and grounding of static electricity producing equipment shall be required whenever transferring flammable/combustible liquids or when working in areas where flammable/combustible materials are stored. Proper use of these procedures will prevent the occurrence of static electricity sparks generated by transfer equipment and operations.
- Bonding is the process of equalizing the electrical potential between two or more drums, containers, materials, or equipment. This is accomplished by connecting a cable, with suitable clamps, between the containers. When attaching the cable clamps, ensure that a direct metalto- metal contact between the container and clamps is made.
- For pliers-type clamps, a back-and-forth motion to work the points through paint, rust, and dirt present on containers should be used. Surface preparation may be required to expose bare metal prior to clamp installation for certain types of clamps (e.g., pipe clamps).
- Always make the first connection of the cable at the hazardous location. By doing this, any static discharge that occurs as the circuit is completed, will occur at the “safe” container.
- Grounding is the process of connecting static electricity generating equipment (e.g., pump, compressor, generator) and drums or other materials to ground so as to dissipate any static charges which may develop. This is accomplished by connecting a grounding cable, with suitable clamps, from the static electricity generating equipment to a suitable conductor in the ground (e.g., grounding rod, buried water pipe).
- Ensure that a metal-to-metal contact is made at the clamp locations.
- When attaching the grounding cables, always make the last connection to the grounding rod in case a spark occurs as the circuit is completed.
- For transfer operations, both containers should be grounded. In this way, if one of the grounding/bonding cables is disconnected, static charges will be conducted to ground as long as the other two lines remain in place.
- When using a grounding rod, drive the rod deep into the ground (minimum 3 feet) so as to ensure contact with moist soil for adequate grounding. For field operations, water can be applied to moisten the soil by the ground rod location.
- During transfer operations involving combustible or flammable liquids, the amount of electrostatic charge generated by the transfer process can be minimized by completing the product transfer slowly and minimizing splashing and spraying.
- Drum Leak Containment
- Where chemical spills may occur, a spill containment program shall be implemented to contain and isolate the entire volume of the hazardous substance involved. Salvage drums and suitable quantities of proper absorbent shall be available for use in areas where spills, leaks, or ruptures may occur.
- Various containment measures that can be implemented include:
- Diking/berming – Diversion
- Absorbents – Covering
- Vapor knockdown or suppression – Re positioning drum
- Over-packing Plug and patch
- Pumping/transfer
- Diking/Berming
Use of a dike or berm surrounding leaking drums can be an effective form of containment. Berms can be made of soil, sandbags, absorbent material, sorbent booms, etc. Ensure that all materials used are compatible with the material(s) to be contained. Use conservative estimating when designing the containment area based on drum volumes. Such secondary containment areas shall be lined with an impervious material to facilitate clean-up.
- Diversion
Diversion of a spill can be used to keep a drum spill from entering a drain, roadway, or waterway. Heavy equipment can be used to create diversion ditches in the case of large drum spills as in truck spills or warehouse fires. Similar materials used for berming can also be used for spill diversion.
- Absorbents
Absorbents can be used to contain liquid spills. Solid absorbents (e.g., vermiculite, perlite, diatomaceous earth) can be applied. Sorbent socks, pillows, and boom can also be used. Ensure that the absorbent material is compatible with the spilled material (e.g., hydrofluoric acid is not compatible with silica-based absorbents).
- Covering
Spills of solid materials can be contained by placing plastic sheeting over the spill area and securing it with sandbags. This prevents the material from being dispersed by wind prior to cleanup. Ensure that static electricity build-up and discharge do not pose an explosion hazard.
- Vapor or Knockdown or Suppression
Flammable or toxic vapors being emitted from a drum spill can be “knocked down” or suppressed with application of a water or foam spray. Care must be taken to provide for containment of the vapor suppressant in these applications.
- Pumping/Transfer
Use of pumps and vacuum trucks can be used to transfer material from leaking containers and assist with containment measures.
- Re positioning Drum
Reducing the flow of material from a leak in a drum can be accomplished by simply repositioning the drum. This is done by laying the drum on its side and placing the leak area at the top. When in this position, the drum hole can then be plugged or patched.
- Plug and Patch
Plugging and patching refers to the use of compatible plugs and patches that are designed to reduce or temporarily stop the flow of materials from small holes in drums and containers. The repaired container may not be reused without proper inspection and certification. There are many plugging and patching techniques available to assist in stopping or limiting the flow of material from a drum. Plugs can be of the inflating type using foam, water, or air or of the formed tapered type. Patches are also available in an assortment that includes magnetic steel, fabrics, adhesives, or epoxies. Piping can be patched with devices that are similar to hose clamps.
- Over-packing
Drum over-packing is the process of placing a leaking or damaged drum inside of a larger drum for containment and shipping purposes. Salvage or recovery drums are common designations for over pack drums. Hazards associated with over-packing are the chemical hazards from the materials contained within the leaking drum and the physical hazards related to the mechanics of the over packing procedure. Over-pack drums are constructed of steel, plastic or composite materials and are of an open top design. Over-pack drum selection is based on the size and configuration of the drum and compatibility with the chemical. Typical over-pack drum sizes are an 85-90 gallon-size (for 55 gallon drum) and a 55 gallon-size (for 30 gallon drum). Over-pack containers typically have a form-fitting gasket in a lid that can be tightly secured with a ring-type closure. If possible, leaking drums should be temporarily repaired with plug and patch techniques prior to over-packing. In the over-packing process, the damaged drum is placed in a slightly oversized, open-top salvage drum. The space between the drums is filled with a compatible cushioning and absorbent material and a tight-fitting lid is secured to the salvage drum. The salvage drum must be labeled and marked in accordance with DOT regulations for the hazardous material/waste contained. Additional DOT requirements related to certification of salvage containers must be strictly adhered to.
- Special Cases
- Bulging Drums
Bulging drums are a result of the buildup of excessive pressure within a drum causing the drum to expand and swell or bulge. This commonly occurs when drums containing a volatile product are subjected to elevated temperatures due to ambient environmental conditions, exposure to fire, or from exothermic chemical reaction. Often times, bulged drums are encountered where combustible, flammable, or volatile liquids are exposed to extreme temperatures and the expansion of the vapor within the drum has caused the bulged condition. If handled at lower temperatures, these bulged drums may not be under significant pressure. Shade from direct sun exposure, working at night, or mechanically cooling the drum’s exterior may provide adequate pressure relief so the drums can be handled with less hazard. Bulged drums should be inspected thoroughly prior to handling. Isolate ignition sources and use beryllium-copper spark resistant tools when handling bulged drums as they commonly contain flammable liquids. Drums that are under significant internal pressure as evidenced by bulging or swelling and unusual sounds or venting coming from the drum, should not be moved.
Do not move drums that are under pressure, until the cause for the excess pressure is determined and appropriate containment procedures have been implemented to protect workers from explosive relief of the drum. If a drum under pressure has to be moved, handle the drum with a grappler unit constructed for explosive containment, if feasible. Either move the bulged drum only as far as necessary to allow seating on firm ground, or carefully over-pack the drum. Exercise extreme caution when working with or adjacent to potentially pressurized drums.
- Drum Staging
Drums must often be staged to facilitate drum sampling, waste characterization, and remedial action. The number of drum staging areas needed is variable and depends upon site-specific factors. Factors include; the number of drums present, condition of the drums, amount of area available for work operations, accessibility for handling or sampling drums, amounts of different types of waste classifications present, need for separation of incompatible materials, etc. Depending upon the needs of the situation, one staging area or multiple areas can be used for drum staging.
Keep drum staging areas to the minimum number necessary to safely identify and classify materials and prepare them for transport. Initial staging consideration should be to segregate incompatible containers and leaking containers. Drums shall be stored in rows of one of two with aisles (8 foot minimum) left between rows to allow access by forklift and/or personnel. An initial staging area can be used to organize drums according to type, size, condition, suspected contents, compatibility, etc. A drum opening/sampling staging area is often used for the opening and sampling of drums. A secondary staging area may be needed to act as a holding area for temporary drum storage following drum sampling/characterization and pending transport. An additional staging area can be used for bulking materials. Drums shall be placed on suitable pallets to facilitate mechanical handling.
- Drum Opening
Drum opening is the process of opening drums in order to collect samples or to transfer contents. Hazards of flammable atmospheres, chemical exposure, chemical splashes, vapor releases, chemical reactions, and possible explosions can be encountered during drum opening operations. During drum opening operations, workers not specifically involved in drum opening tasks shall kept a safe distance away. Drum lids and/or bungs should be removed slowly and carefully to minimize chemical splashes, spills, and updraft of dusty material inside the drum. Protective clothing, respiratory protection and use of air monitoring equipment shall be used when opening drums that have not been characterized. An emergency eyewash/shower and multi-purpose fire extinguisher should be located in the immediate area of drum opening operations. If airline respirators are in use, they shall be protected from physical damage and contamination. Apply fire safety procedures when working with flammable/combustible materials. Open bulging or swelled drums so that excess interior pressure is safely relieved and use shielding if pressure cannot be relieved from a remote location.
- Drum Sampling/Characterization
Drum sampling is the process of collecting liquid, sludge or solid samples from drums. Collection of liquid samples can be completed using glass sample collection rods, coliwasa samplers, bailers, dippers, and other specialized samplers. Glass sample collection rods are commonly used to retrieve liquid samples from closed top drums. To collect a liquid sample, the glass rod is inserted into the liquid and a finger is placed over the top opening of the rod. Rubber aspirator bulbs are also available to assist with this process. Liquid sampling often results in small spills and plastic sheeting and splash protection may be required for operations. Sample characterization can be basic or extensive depending upon the amount and type of information needed. Basic hazard categorization testing for flammability, corrosivity, and oxidation can be completed using a combustible gas indicator, pH paper, and potassium-iodide starch paper, respectively. Full characterization may involve laboratory analysis in accordance with disposal facility waste profiling and acceptance criteria.
- Drum Bulking
Wastes that have been characterized are often mixed together and placed in bulk containers such as tanks or vacuum trucks for shipment to a treatment, storage and disposal facility. Permit bulking of hazardous wastes only after thorough characterization of the material. Bulking of liquid materials can be accomplished using an excavator with a drum grappler attachment, vacuum truck with stinger attachment, and pneumatic pumping equipment. Solid materials can be bulked using a backhoe, hoppers, and forklift with drum dumping attachment. The contents of the drum must be shown on the drum’s label.
- Drum Crushing
Drum crushing is the process of crushing empty unusable drums. Drum crushing machines are used for this purpose; however, sometimes heavy equipment can be used to crush empty drums. Drums should be crushed only when they are essentially empty, do not contain residual materials that could ignite from a spark caused by the crushing process, and any possible spillage from the drum is contained.
- Drum Shipping and Transport
Shipping and transport are the process of preparing drums for shipment and transport off site. The drums to be transported shall be properly identified and classified through the waste characterization process. Materials shall be properly containerized and sealed in the applicable drum.
Drums shall be labeled with the required label for the hazard class of the material.
Drums shall be marked with the proper shipping name and other required information. A required hazardous waste label/marking shall be applied for hazardous waste materials. The drum staging area should be set up with adequate access and egress routes for loading the transport vehicles. Loads shall be segregated and secured on the transport vehicle as required. DOT placards must be displayed on the vehicle as required.
A Waste Manifest for waste shipments shall be completed prior to transporting drums off site. The transport vehicle must have current licensing for transport of hazardous materials and wastes and the driver must have current licensing for hazardous material transport. Drums shall be secured by banding or other effective means.
5 – Waste Transportation System
- Solid wastes will be collected regularly by collection trucks and transported to the appropriate disposal site.
- Scheduled wastes shall be collected, stored, transported and manifested in conformance with local requirements.
- Sanitary wastes will be transported to the sewage plant by an underground sewer collection system where possible.
- Sanitary wastes on jobsite will be handled in chemical toilets.
- A Subcontractor will be employed to empty the chemical toilets and properly dispose of the sanitary waste at a permitted facility.
- Contaminated soils will be collected by earth moving equipment, loaded onto trucks, and transported to remediation or disposal site.
6- Waste Disposal Options
- All disposal options will be contracted out to a waste disposal vendor approved by the appropriate local and governmental Regulatory organizations.
- All waste disposed of offsite shall be tracked by means of a Waste Manifest (see Attachment below). Contractors shall maintain a file of completed Waste Manifests in their respective HSE Department and made available when required.
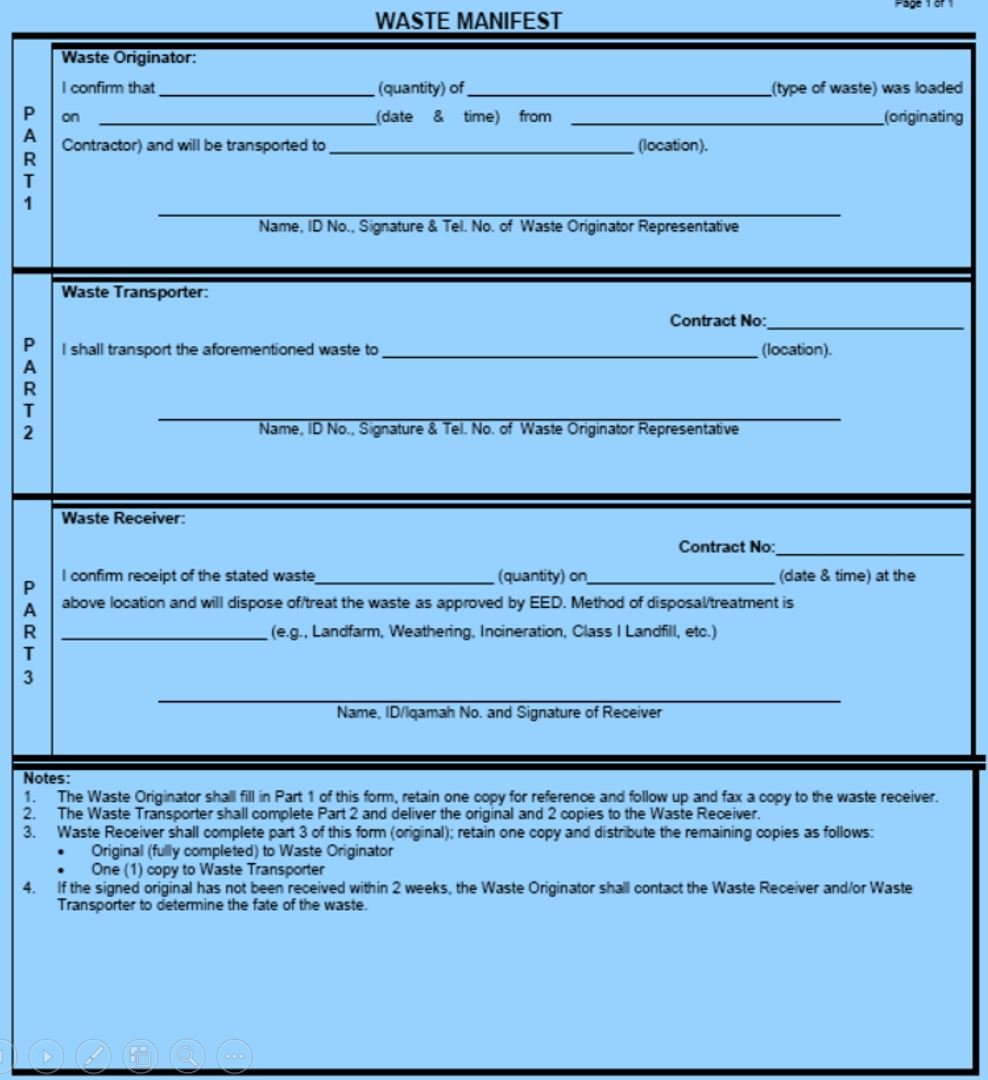
7- Surface Discharge
- All wastewater discharged to a local water body will meet the liquid effluent standards.
- The volume and concentration of the waste stream will be reviewed relative to the quality and capacity of the receiving water body to ensure that the disposal stream can be adequately absorbed into the receiving stream.
8- Reclaiming/Reuse
- All wastes will be reviewed to maximize the reclamation or recovery of materials through on-site processes or with outside Vendors and Suppliers.
- After all reclamation options have been investigated, reuse of the materials will be evaluated. Reuse may be in the same, alternate or downgraded service.
9- Waste Handling and monitoring
- Any worker or Subcontractor employee who handles any type of waste will use Personal Protective Equipment (PPE) appropriate to the type of waste involved as per the Risk and Hazard Assessment.
- The Contractor’s Construction Manager is responsible for assuring proper assessment, monitoring and handling of the waste generated on the construction project.
52 thoughts on “Waste Management: Procedures and Disposal Options”