Improving Safety Culture: A Multipronged Strategy Using the Safety Pyramid Model
7 min readWorkplace safety encompasses practices, protocols, and procedures implemented to ensure employees’ well-being. A robust safety culture prioritizes hazard identification and risk assessment.
Key aspects of workplace safety include:
- Regulatory Compliance: Adherence to OSHA and other regulatory bodies
- Training Programs: Regular safety training and awareness campaigns
- Personal Protective Equipment (PPE): Proper usage and availability
- Incident Reporting: Efficient incident and near-miss reporting mechanisms
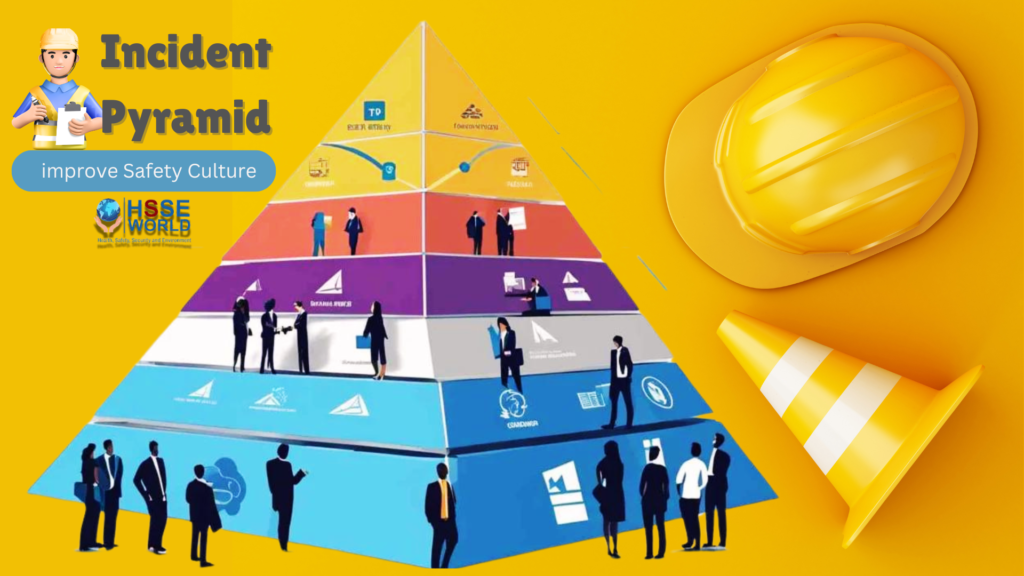
A strong focus on safety reduces accident rates, increases productivity, and boosts employee morale. Effective safety management benefits organizations by mitigating potential risks and liabilities.
Understanding Herbert Henrich’s Safety Pyramid
Herbert Henrich’s Safety Pyramid, also known as the “Heinrich Triangle,” is a crucial concept in occupational safety. Derived from extensive studies, it visualizes the relationship between incidents of varying severity.

- Top of the Pyramid: Represents major accidents causing serious injury or fatality.
- Middle Tier: Accounts for minor injuries needing medical attention.
- Base Level: Comprises near misses or unsafe acts without resulting injuries.
The model suggests:
- Proactive Measures: Emphasizes preventive actions at the base level.
- Incident Ratio: For every major accident, there are numerous minor injuries and near misses.
Read: What Is The Difference Between Incidents and Accidents?
The Evolution and Relevance of the Safety Pyramid in Modern Workplaces
The Safety Pyramid, introduced by Herbert William Heinrich, elucidates the relationship between minor incidents and major accidents. The foundational aspect comprises numerous near-misses and minor occurrences that precede severe accidents.
Historical Development
- Early 20th Century: Heinrich’s model proposed a 300-29-1 ratio.
- 1970s: Updates to capture workplace transformation.
- 21st Century: Emphasis on higher accuracy and preventive measures.
Modern Application
- Data-Driven Insights: Enhanced data collection and analysis methods.
- Integrated Technology: Automation and real-time monitoring improve safety practices.
- Behavioral Safety: Focus on proactive, behavior-based safety interventions.
“Understanding the pyramid’s evolution helps organizations to refine their strategies and prevent accidents effectively.”
How to Interpret the Different Levels of Henrich’s Safety Pyramid
Henrich’s Safety Pyramid illustrates the hierarchical relationship between incidents of varying severity.
- Unsafe Acts: The foundation, representing numerous unsafe acts leading to minor or no injury.
- Near Misses: Fewer than unsafe acts, near misses indicate potential for accidents without resulting in harm.
- Minor Injuries: Reflects incidents causing minor injuries. It’s crucial to investigate to prevent severe consequences.
- Serious Injuries: Fewer occurrences but indicative of significant safety system flaws.
- Fatalities: The apex, rare but devastating. Each level must be analyzed to mitigate risks effectively.
Read: Photo of the day: Unsafe Conditions
Identifying and Addressing Near Misses: The First Line of Defense
Identifying near misses is critical. Employees should be encouraged to report incidents that almost caused harm. Effective strategies include:
- Clear Reporting Channels:
- Provide anonymous reporting options.
- Ensure accessibility and ease of use.
- Routine Training:
- Conduct regular workshops.
- Emphasize the significance of near misses.
- Data Analysis:
- Use software for trend analysis.
- Identify potential hazards proactively.
- Feedback Loop:
- Inform employees about actions taken.
- Reinforce the importance of their contributions.
A proactive approach to near misses strengthens safety culture and preempts accidents, ensuring a safer workplace environment.
Read: Close calls and Near misses incidents
Transforming Small Incidents into Learning Opportunities
Organizations can harness the lessons inherent in minor incidents. These events, often overlooked, hold significant potential for improvement.
- Encourage Reporting: A culture that promotes reporting small incidents leads to a vast pool of data.
- Analysis: Thorough analysis can identify underlying causes.
- Training Programs: Use findings to inform and update training programs.
- Communication: Share insights and solutions across the organization.
- Feedback Loop: Create a feedback mechanism to ensure continuous improvement.
By addressing small incidents, companies can prevent more significant issues and instill a proactive safety culture. Every minor slip, trip, or error becomes a stepping stone towards a safer working environment.
Read: Accident-Incident Investigation Technique guideline
Strategies to Minimize Minor Injuries and Prevent Serious Accidents
- Regular Safety Training
- Continuous education on safety practices.
- Mandatory workshops and refresher courses.
- Enhanced Risk Assessments
- Conduct frequent risk evaluations.
- Involve multiple departments in the risk assessment process.
- Safety Audits
- Implement periodic safety audits.
- Review and update safety protocols regularly.
- Use of Protective Equipment
- Ensure availability and proper use of PPE.
- Regularly inspect and maintain safety gear.
- Clear Communication Channels
- Establish clear reporting procedures.
- Encourage open dialogue about safety concerns.
- Employee Involvement
- Encourage employee participation in safety committees.
- Reward proactive safety behavior.
- Technology Integration
- Use safety management software.
- Monitor compliance through digital tools.
Download: photo-of-the-day-tracking-near-miss-incidents/
Building a Proactive Safety Culture: Key Steps and Best Practices

Implementing a proactive safety culture requires systematic actions and consistent involvement. Steps to build this culture include:
- Leadership Commitment:
- Ensure top management visibly supports safety initiatives.
- Allocate necessary resources for safety programs.
- Employee Engagement:
- Encourage employee participation in safety meetings.
- Recognize and reward safety contributions.
- Continuous Training:
- Conduct regular safety training and refreshers.
- Use scenario-based learning for effective engagement.
- Incident Reporting System:
- Establish a non-punitive reporting mechanism.
- Analyze reports to identify potential hazards.
- Regular Audits and Inspections:
- Perform periodic safety audits.
- Implement corrective actions promptly.
Developing these practices fosters a culture that prioritizes safety at every organizational level.
Integrating Technology and Data Analytics for Enhanced Safety Management
Leveraging technology and data analytics transforms safety management. Key technologies include:

- Internet of Things (IoT): Sensors monitor equipment and environmental conditions, providing real-time alerts.
- Machine Learning Algorithms: Predictive analytics identify potential hazards before incidents occur.
- Cloud Solutions: Centralize data storage, ensuring easy access and collaboration.
- Mobile Applications: Facilitate immediate incident reporting and safety audits.
Additionally, data analytics:
- Identifies risk patterns.
- Tracks safety compliance.
- Enhances incident investigation.
Investing in these technologies leads to data-driven decision-making, optimizing resource allocation and improving overall safety culture.
Case Studies: Successful Implementation of Henrich’s Safety Principles
Case Study 1: Manufacturing Sector
A leading automotive manufacturer significantly reduced incident rates by implementing Henrich’s principles:
- Hazard Identification: Conducted monthly safety audits.
- Employee Training: Mandatory safety training sessions.
- Near-Miss Reporting: Established a zero-tolerance policy for not reporting near-misses.
Case Study 2: Healthcare
A hospital improved patient safety through:
- Root Cause Analysis: Comprehensive reviews of medical errors.
- Safety Protocols: Stringent adherence to safety checklists.
- Staff Accountability: Encouraged accountability through transparent reporting.
Case Study 3: Construction Industry
A construction firm achieved remarkable safety standards by:
- Risk Assessments: Daily risk assessment meetings.
- PPE Use: Strict enforcement of Personal Protective Equipment.
- Behavioral Observations: Regular observations to reinforce safe practices.
Training and Engaging Employees in Safety Protocols
Regular training sessions should be conducted to keep employees updated on safety protocols. Interactive workshops can promote active participation.
- Monthly Safety Drills: Practice emergency responses.
- Workshops and Seminars: Facilitate discussions on safety practices.
- Online Training Modules: Provide flexible learning options.
- Feedback Mechanisms: Encourage employee input on safety measures.
Effective communication channels must be established to disseminate safety updates swiftly. Leadership should lead by example, consistently observing safety guidelines.
“Engagement in safety protocols is critical for maintaining a robust safety culture. Continuous learning and active involvement foster a safer work environment.”
Measuring the Effectiveness of Safety Interventions
Accurately assessing the effectiveness of safety interventions necessitates a structured approach. Key performance indicators (KPIs) should include:
- Incident Rates: Tracking the frequency and severity of incidents before and after interventions.
- Safety Audits: Regular audits to ensure compliance with safety protocols.
- Employee Feedback: Surveys and feedback mechanisms to understand employee perceptions of safety.
- Training Outcomes: Evaluating the impact of safety training programs through competency tests.
Statistical analysis of these metrics provides a comprehensive view of intervention efficacy. Continuously refining these metrics ensures they remain aligned with evolving safety objectives.
Read: Calculating Success: A Step-by-Step Guide to HSE Performance Measurement
Continuous Improvement: Adapting and Evolving Safety Strategies
Continuous improvement is paramount to effective safety strategies. Organizations must regularly assess and refine their practices to keep pace with changing environments.
- Regular Audits: Conduct frequent safety audits to identify new risks.
- Employee Feedback: Implement systems to capture and act on employee safety suggestions.
- Training Programs: Update training materials to reflect the latest safety protocols.
- Technology Integration: Utilize advanced technologies like AI to predict potential hazards.
- Policy Reviews: Periodically review and revise safety policies for relevance.
“Adaptability is key to maintaining a proactive safety culture.”
These methods ensure that safety measures evolve continuously.
Conclusion: The Future of Workplace Safety and the Role of Leadership
The future of workplace safety hinges significantly on active and committed leadership. Leaders set the tone for safety cultures and are paramount in cascading safety values throughout the organization.
- Leadership Commitment: Leaders must consistently prioritize safety above productivity metrics.
- Communication: Open lines of communication regarding safety policies and practices.
- Training and Education: Leaders should invest in ongoing training programs.
- Accountability: Implement systems to hold all employees accountable for safety.
- Innovation: Embrace technology and data analytics to anticipate and mitigate risks.
Organizations can significantly reduce incidents and enhance overall workplace well-being through strategic leadership and a robust safety culture.
you can have more safety resources here