Calculating Success: A Step-by-Step Guide to HSE Performance Measurement
25 min readHealth, Safety, and Environment (HSE) performance is a critical aspect of any organization, particularly within high-risk industries like Engineering, Procurement, and Construction (EPC). Effective HSE practices not only protect employees and the environment but also contribute to project success, cost efficiency, and positive stakeholder relationships. This comprehensive guide delves into the world of HSE performance, exploring key metrics, calculation methods, and strategies for achieving continuous improvement.
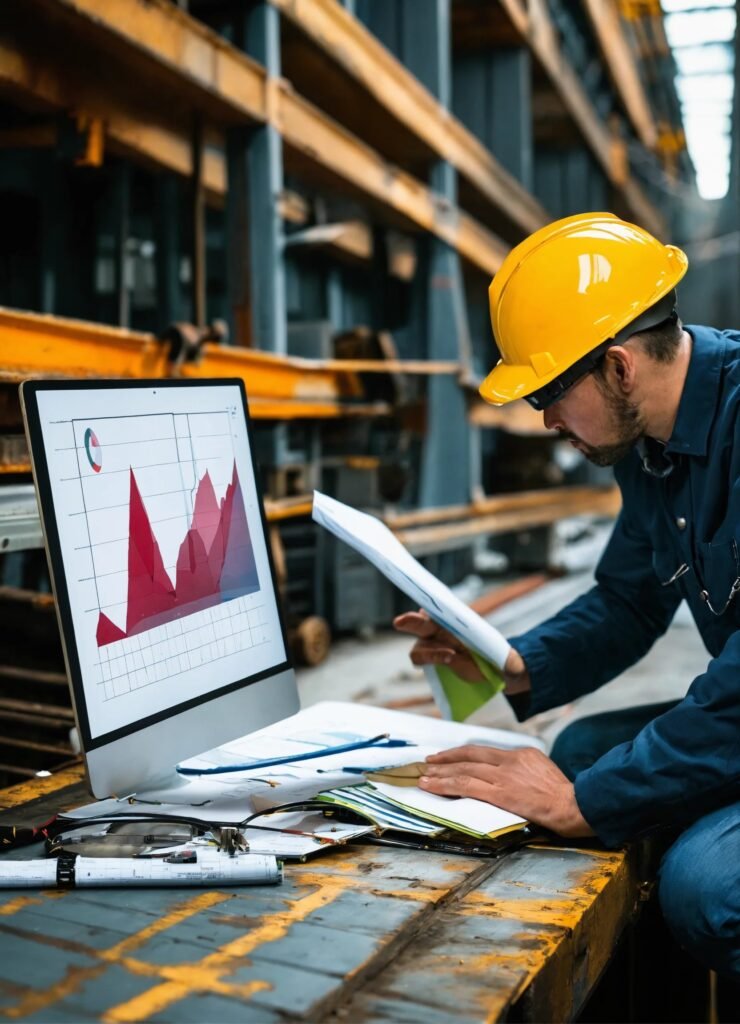
Introduction to Health, Safety, and Environmental (HSE) Performance
As an HSE professional, I’m acutely aware that Health, Safety, and Environmental performance is at the core of responsible business operation. Ensuring the well-being of employees, protecting the environment, and maintaining safe workspaces — these are not just regulatory requirements, they are moral imperatives and critical components of business success. Effective HSE performance measurement is indispensable in this pursuit, acting as a barometer for assessing risks, improving processes, and safeguarding resources.
When I speak of HSE, I refer to a comprehensive strategy encompassing three key pillars: health, which addresses occupational illness and promotes well-being; safety, which involves preventing accidents and injuries; and environmental, which focuses on minimizing the impact of operations on the natural world. Each pillar cannot stand in isolation they are intertwined elements that together constitute a robust HSE framework.
In monitoring HSE performance, I’ve found it’s essential to:
- Establish clear metrics and objectives based on corporate goals and compliance requirements.
- Implement tracking and reporting systems to measure progress and identify trends.
- Engage in regular audits and reviews to ensure continuous improvement.
Moreover, as we explore these aspects, it’s crucial to employ relevant indicators that are measurable and understandable to all stakeholders. From leading measures, like safety training compliance rates, to lagging indicators, such as incident frequency rates, each data point informs our strategy and actions.
In the forthcoming sections, I’ll be taking a step-by-step approach to measuring HSE performance — identifying the right metrics, gathering data, and analyzing it to make informed decisions. With this guide, you’ll be better equipped to calculate the success of your HSE initiatives, and in turn, safeguard the well-being of your workforce and the environment. Also Read: key-risk-indicators-kris-and-its-the-relationship-to-key-performance-indicators-kpis
Understanding HSE Key Performance Indicators (KPIs)
When I approach the topic of Health, Safety, and Environment (HSE) Key Performance Indicators (KPIs), I perceive them as essential metrics that help quantify the effectiveness of an organization’s health, safety, and environmental management systems. These KPIs enable me to measure and track progress, identifying areas that require improvement and celebrating successes where targets are met or exceeded.
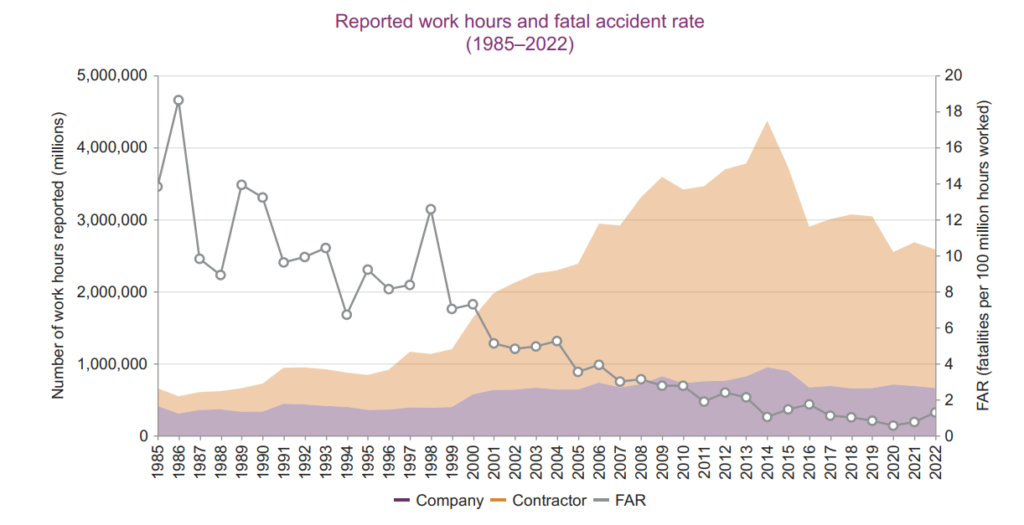
To ensure clarity and alignment with business objectives, I typically categorize HSE KPIs into lagging and leading indicators. Lagging indicators refer to historical data, which provide insight into the incidents that have already occurred, such as:
- Number of recordable incidents
- Lost time injury frequency rate
- Environmental spills volume
Conversely, leading indicators are predictive measures, offering me the ability to foresee and mitigate risks before they result in incidents. Some examples of leading indicators include:
- Number of safety audits completed
- Training hours per employee
- Equipment maintenance schedule adherence
For these KPIs to be effective tools in driving HSE performance, I ensure they are SMART: Specific, Measurable, Achievable, Relevant, and Time-bound. Additionally, I establish a process for regular review and adjustment of these KPIs, as this fosters continuous improvement and reflects the dynamic nature of the work environment.
In my practice, a crucial aspect of utilizing HSE KPIs is employee engagement. It’s vital that all members of the organization understand and recognize the significance of these indicators in promoting a safe and healthy workplace.
By diligently tracking and analyzing HSE KPIs, I can facilitate informed decision-making and strategic planning, ultimately leading to a safer work environment and sustainable operations.
Also Read: HSE-key-performance-indicators-need-to-be-tracked
Setting the Stage: The Importance of HSE in Driving Safety Forward
When I consider the critical elements that contribute to the success of any industry, Health, Safety, and Environment (HSE) management invariably stands out. It’s the backbone of operational integrity and plays a pivotal role in ensuring that enterprises aren’t just compliant, but are also safeguarding their most valuable asset—their workforce. I regard HSE not as a peripheral concern but as central to driving safety forward. It’s about instilling a culture of continuous improvement and risk management that prioritizes the well-being of employees and the environment.
The importance of a robust HSE system is twofold. Firstly, it acts as a preventive measure. By identifying potential hazards and implementing controls, we significantly reduce the potential for accidents. This is not only vital for the health and safety of individuals but also for the sustainability of the business. Secondly, HSE practices are key to legal compliance. The consequences of neglecting these can range from hefty fines to severe reputational damage—impediments that no business can afford in today’s competitive environment.
In my role, I’ve found that effective HSE management demands diligent performance measurement. Like any other business function, HSE requires the same rigor in terms of goals setting, monitoring, and evaluation. Adequate performance indicators, derived from data captured in incident reporting, risk assessments, and audits, are imperative to understand the current safety climate, drive improvements, and make informed decisions.
This synergistic blend of compliance, safety culture, and performance metrics isn’t just about mitigating risks—it’s about proactively shaping an environment where safety is inherent in every activity. As we venture further into this guide, we’ll unpack the step-by-step process of measuring HSE performance, understanding its intricacies, and using the insights gained to elevate our safety standards to unprecedented levels.
KPI #1: Incident Frequency Rate – Tracking and Analysis

When I aim to measure the effectiveness of health, safety, and environmental (HSE) performance within an organization, one of the key performance indicators (KPIs) I monitor closely is the Incident Frequency Rate (IFR). This metric provides insights into the frequency of safety incidents that occur over a standard amount of exposure hours, typically measured per one million work hours. To calculate the IFR, I follow these steps:
- Determine the number of recordable incidents that have occurred within the set period.
- Accumulate the total number of hours worked by all employees during the same period.
- Divide the total number of incidents by the total number of hours worked.
- Multiply the result by one million to normalize the data.
For example, if there were 5 incidents over 500,000 work hours, the IFR would be:
(5 incidents / 500,000 hours) x 1,000,000 = 10 incidents per million hours worked.
I analyze this data by comparing it to historical performance, industry standards, and internal targets. This comparison helps identify trends, predict potential future incidents, and devise strategies for improvement. I find it crucial to track how the IFR fluctuates over time to determine the effectiveness of safety initiatives and training programs.
Additionally, segmenting the data by department, job function, or location allows for a more granular analysis which can uncover specific areas with higher risks. This tailored approach enables me to address these risks with targeted actions, fostering a safer work environment.
By regularly reviewing and analyzing the Incident Frequency Rate, I am equipped to make informed decisions that promote a culture of safety and continuous improvement within the organization.
KPI #2: Severity Rate – Assessing the Impact of Workplace Injuries
When I examine the efficacy of Health, Safety, and Environment (HSE) initiatives, understanding the extent of injuries is crucial. The Severity Rate serves as a key performance indicator that provides insight into the gravity of workplace accidents. This metric helps me gauge not just the frequency of incidents, but also their impact on operations and personnel.
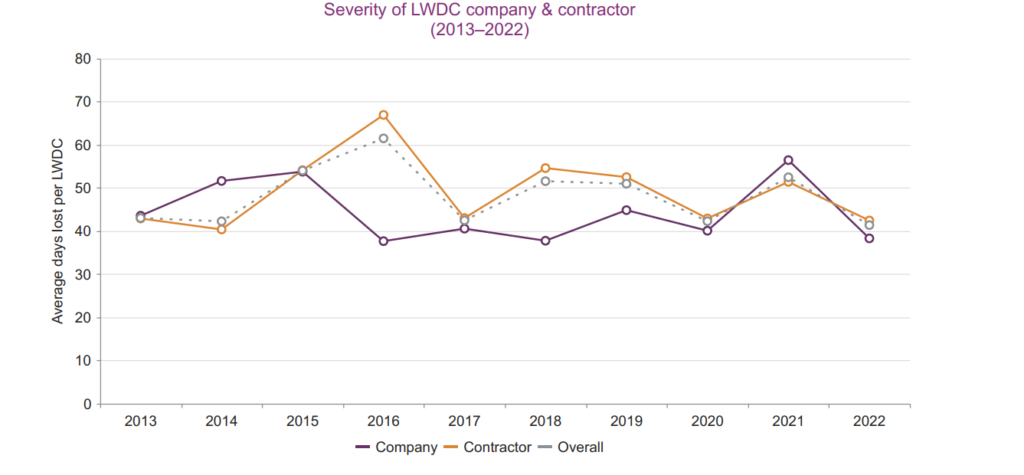
To calculate the Severity Rate, I follow these steps:
- Obtain the total number of lost days: This figure represents the sum of days employees were unable to work due to workplace injuries.
- Identify the total hours worked: I gather data on the collective number of hours all employees worked during the same period.
- Use a standard base number: Typically, I use 200,000, which corresponds to 100 employees working 40 hours a week for 50 weeks.
The formula to ascertain the Severity Rate is as follows:
Severity Rate = (Total number of lost days due to injuries\Total hours worked) times 200,000
Interpreting the Severity Rate offers me a clear picture of the aftermath of incidents, enabling me to make informed decisions about needed improvements in safety protocols and training programs. A higher Severity Rate indicates more severe outcomes from injuries and signals an urgent need for intervention.
In pursuit of lowering this KPI, I focus on:
- Enhanced training: Education on safe practices reduces the risk of severe accidents.
- Incident response plans: Effective strategies for immediate response can limit injury repercussions.
- Investment in safety equipment: Protective gear and safety systems are crucial for injury prevention.
By keeping a close eye on the Severity Rate, I ensure a proactive approach to minimizing the impacts of workplace injuries, thereby safeguarding employees and maintaining efficient operations.
KPI #3: Near Miss Reports – A Proactive Approach to Safety
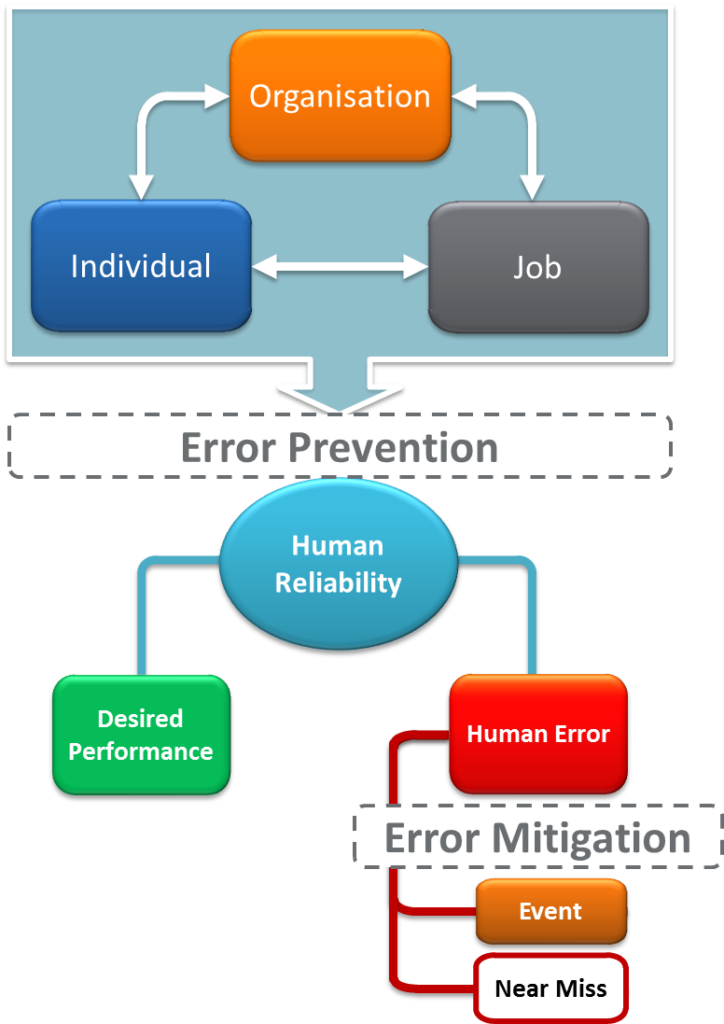
In my experience managing health, safety, and environmental (HSE) performance, I’ve learned the importance of tracking near-miss reports. Near-miss incidents are events that could have resulted in injury, illness, or property damage but didn’t—this time. I stress to my team that these incidents provide a crucial preview of potential disasters and an opportunity for proactive improvement.
When I calculate this key performance indicator (KPI), I focus on several aspects:
- Frequency of Reporting: A higher number of near-miss reports often indicates a strong safety culture where employees are vigilant and encouraged to share potential risks.
- Report Follow-up: It’s not enough to just record near misses; I ensure there’s a system for investigating and addressing the root causes.
- Trend Analysis: By analyzing near miss trends over time, I identify patterns that might be indicative of larger systemic issues.
Learn : Reporting Near-Misses
Here are the steps I follow to measure this KPI effectively:
- Data Collection: Every near miss is documented in detail, including the time, location, and potential consequences if the event had escalated.
- Incident Review: A cross-functional team reviews each report to decipher the underlying factors.
- Action Plan Implementation: Based on our findings, we develop and implement corrective actions to prevent recurrence.
- Communication: We disseminate lessons learned from near miss incidents company-wide to raise awareness and promote a preventive mindset.
- Performance Review: I regularly review this KPI with stakeholders to assess whether our interventions are effective in reducing risks and if further improvements are required.
I’ve found that a robust near miss reporting and response system not only enhances safety but also fosters a culture where employees are actively engaged in creating a safer workplace. Engaging with near miss data empowers us to mitigate hazards before they result in actual harm, making it a vital component of comprehensive HSE performance measurement.
KPI #4: Lost Time Injury Frequency Rate – Calculating Downtime
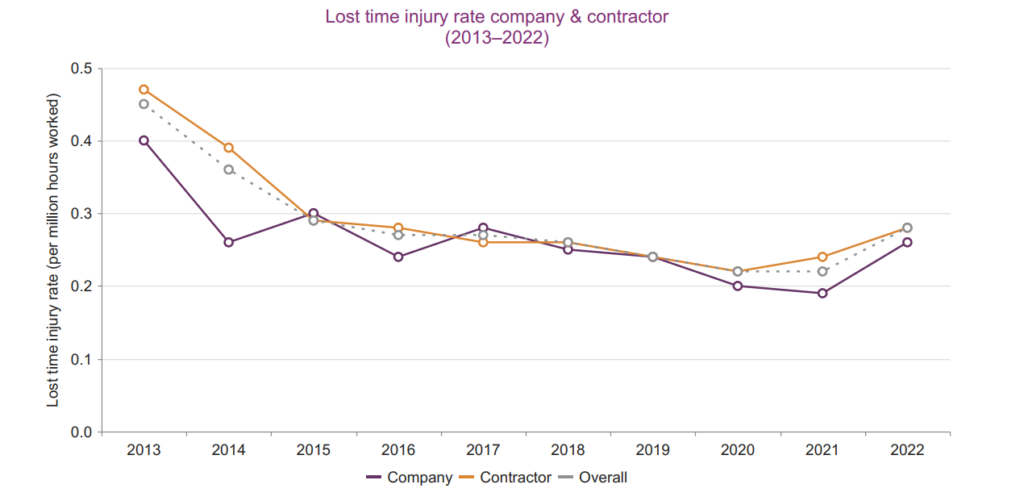
When evaluating health, safety, and environmental (HSE) performance, understanding the Lost Time Injury Frequency Rate (LTIFR) is critical. As a professional in the field, I recognize that LTIFR offers insight into the safety culture and effectiveness of safety protocols within an organization. Calculating it isn’t just a box-checking exercise—it directly correlates to the well-being of the workforce and, ultimately, to operational efficiency.
To compute the LTIFR, I follow a standardized equation:
LTIFR = Number of lost time injuries times 1,000,000 \Total hours worked by all employees during the period being measured
This rate is essential for a few reasons:
- Contextualizing Injuries: It puts the number of injuries into perspective relative to the size and scope of operations. Smaller companies have different scales compared to larger ones, and LTIFR helps normalize this aspect.
- Benchmarking: It allows me to compare my organization’s performance with industry standards or against past performance. Monitoring trends over time can indicate if improvements are happening.
- Prioritizing Safety: A higher LTIFR could ring alarm bells, suggesting that I need to reevaluate our safety protocols. Conversely, a lower LTIFR is often indicative of a stronger safety culture.
Some challenges in calculating LTIFR include ensuring that all lost time injuries are reported and accounted for, and that all hours worked are meticulously recorded. Misreporting or underreporting can skew the rate, making it less useful for making informed decisions.
In essence, LTIFR not only calculates downtime due to injuries but also serves as a proactive measure for continuous improvement in HSE practices. As a professional, it’s my duty to ensure the accuracy and consistency of this KPI to safeguard the health of our employees and organizational success.
KPI #5: Employee Safety Training Completion Rates
When evaluating Health, Safety, and Environment (HSE) performance, I pay close attention to the completion rates of employee safety training. This key performance indicator (KPI) offers a clear gauge of our proactive commitment to workplace safety and staff development.
In tracking this, I begin by establishing a baseline: what percentage of my workforce is currently trained? From there, I set a target completion rate that aligns with regulatory requirements and internal safety goals. This helps ensure that my team isn’t just compliant, but also possesses the knowledge to maintain a safe working environment.
To evaluate progress:
- I monitor the number of employees who have completed the mandatory safety training against the total number that requires it.
- I track the completion rates on a departmental level to identify areas that may need additional focus or resources.
- I consider the complexity and time required for each training module, adjusting my expectations and timelines accordingly.
I understand that high completion rates often translate to a safer workplace, making this a vital KPI to measure regularly. I use a combination of learning management systems and manual tracking to stay on top of this data. By fostering a culture of continuous education and prioritizing the safety training completion rates, I am building a foundation that not only protects our employees but also enhances our overall HSE performance. ( Read:hse-training-importance-for-employees-in-all-industries/)
KPI #6: Compliance with Safety Procedures
In evaluating Health, Safety, and Environmental (HSE) performance, I cannot overstate the importance of compliance with safety procedures. This key performance indicator (KPI) is critical because it directly impacts the well-being of employees and the overall safety culture within an organization.
To assess compliance, I usually begin with a comprehensive review of our safety protocols against regulatory standards and best practices. This includes an evaluation of both adherence to policies such as wearing personal protective equipment (PPE) and participation in safety training sessions.
I employ various methods to measure compliance, such as:
- Safety Audits: Regular audits help me pinpoint areas where safety procedures may be neglected or misunderstood. I meticulously record audit findings and compare them against previous results to track improvement or decline.
- Incident Reports: Each incident reported provides insights into potential breaches in our safety protocols. I analyse the nature and frequency of these incidents to understand where additional training or resources may be needed.
- Employee Feedback: Surveys and safety meetings serve as platforms for employees to voice concerns or suggest improvements regarding workplace safety.
- Training Attendance and Completion Rates: These metrics give me a quantitative measure of engagement with safety education efforts.
Moreover, I make sure to validate our safety procedures’ effectiveness through leading indicators, such as near-miss reports, which can act as a precursor to potential compliance issues.
In adherence to the Post-tag sitemap and other regulatory requirements, I ensure that all data on compliance with safety procedures is archived for future reference and accessibility.
Maintaining an effective safety record is non-negotiable for me, and this KPI serves as a barometer for our organization’s commitment to providing a safe and healthy work environment.
KPI #7: Environmental Impact Assessments
As a health, safety, and environmental (HSE) professional, I place great emphasis on Environmental Impact Assessments (EIAs) as a Key Performance Indicator (KPI). Understanding the significance of EIAs involves recognizing their role in informing decision-makers about the potential environmental effects of proposed projects before they proceed. This foresight is crucial in identifying opportunities for avoiding, minimizing, or mitigating adverse impacts while enhancing the positive ones.
When conducting EIAs, I follow a structured process that typically includes:
- Screening to determine whether a project requires a full or partial assessment
- Scoping to identify which potential impacts are relevant to assess
- Impact Analysis to predict the magnitude and significance of each impact
- Mitigation to propose measures to prevent, reduce or compensate for adverse impacts
- Reporting to document the findings and present them to decision-makers
Each of these steps requires careful data collection and analysis to ensure the accuracy and reliability of the findings. When measuring HSE performance through the lens of EIAs, I consider the following elements:
- The comprehensiveness of the EIA: Does the assessment adequately cover all necessary environmental factors?
- Stakeholder Engagement: Have stakeholders been involved effectively throughout the process?
- Mitigative Strategies: How effectively are the proposed mitigation measures expected to address the identified impacts?
- Regulatory Compliance: Does the EIA comply with all relevant local, national, and international environmental laws and regulations?
- Post-Project Monitoring: Are there plans for ongoing monitoring to ensure that mitigation strategies are effectively implemented?
By systematically analyzing these elements, I am able to incorporate feedback and continually improve the EIA process. Tracking the outcome and effectiveness of EIAs as a KPI is vital for ensuring that the projects I oversee not only meet regulatory requirements but also align with best practices for sustainable development. Hence, EIAs are not only a measure of compliance but also an indicator of our commitment to responsible stewardship of the environment.
KPI #8: Emergency Response Times
When I examine the Key Performance Indicator (KPI) for Emergency Response Times, it’s crucial to understand how vital this metric is in assessing our Health, Safety, and Environment (HSE) performance. Timely response during an emergency can mean the difference between minor and major impacts on health, safety, and the environment.
To measure this KPI effectively, I follow these steps:
- Set a Benchmark: I first establish a company standard or use national standards for acceptable response times to various emergencies. This benchmark serves as my guide to gauging performance.
- Define Emergencies: Not all incidents require the same level of response. I categorize emergencies (e.g., medical, fire, chemical spill) to ensure clarity when measuring times.
- Record Data: During an incident, I ensure that precise times are documented from the moment an emergency is reported to the point when the response team arrives and when the situation is under control.
- Analyze Trends: Looking at data over a period, I seek trends. Are we improving, or is there a pattern of delay? This analysis helps identify areas for potential improvement.
- Conduct Drills: Regular emergency drills are conducted, and response times are rigorously documented. Drills help in identifying areas where the response can be expedited.
- Implement Improvements: Based on drill outcomes and real incident analysis, I look for ways to reduce response times, which might include additional training, streamlining processes, or upgrading equipment.
- Report and Review: This KPI is then reported to management and teams regularly. Open discussions about performance and improvements are encouraged to foster a culture of continuous improvement.
Understanding and improving Emergency Response Times not only enhances the safety of personnel but also protects the environment and community at large. Therefore, I maintain a vigilant approach to measuring and improving this essential KPI.
KPI #9: Safety Audits and Inspections Regularity
In the realm of Health, Safety, and Environment (HSE) management, I recognize that proactive measures are as critical as reactive ones. To this end, regularity in conducting safety audits and inspections stands out as a Key Performance Indicator (KPI) that I can ill afford to overlook. These audits are not just about compliance, but about ensuring consistent application of safety protocols and identifying areas for improvement.
- Preparation and Planning: I prioritize setting a schedule for regular safety audits and inspections, integrating them into the company’s calendar.
- Execution: Carrying out these inspections diligently, I ensure that they cover all areas of operation, from the shop floor to the executive offices.
- Consistency: By maintaining a consistent frequency of safety audits, I help to establish a safety culture within the organization.
- Adaptability: I am vigilant in adjusting the frequency of audits based on factors such as changes in operations, recent incidents, or introduction of new regulations.
- Documentation: Clear record-keeping of all safety audits is essential, as it not only provides a historical account but also helps in tracking progress over time.
- Stakeholder Involvement: I involve various stakeholders in the audit process, which includes workers, management, and occasionally external auditors.
- Continuous Improvement: The insights gained from regular safety audits are instrumental for me in refining safety protocols and training programs.
Assessing the regularity and thoroughness of safety audits and inspections allows me to gauge the effectiveness of the HSE management system in place. I view this KPI as a compass guiding continual improvement efforts, ensuring that safety remains not just a static protocol but a dynamic process that adapts to the evolving workspace. Regular safety audits contribute to a safer work environment, better employee morale, and as a result, enhanced overall performance.
KPI #10: Employee Safety Engagement and Feedback
I consider Employee Safety Engagement and Feedback as the tenth key performance indicator in assessing Health, Safety, and Environment (HSE) success in the workplace. Effective safety engagement involves not only adherence to protocols but also active participation and input from the workforce regarding safety measures.
When I measure this KPI, I focus on:
- Safety Meetings and Training Participation: Tracking attendance and involvement in safety-related meetings and training sessions provides a quantitative look at engagement levels. It’s essential to ensure these sessions are both impactful and well-attended.
- Safety Suggestions Implementations: I consider the number of suggestions made by employees and how many of those suggestions have been implemented. A high rate of implementation indicates that the company takes employee feedback seriously and that workers are actively contributing to safety improvements.
- Incident Reporting: This involves monitoring the frequency and quality of safety incident reports submitted by employees. A high reporting rate can point to a strong culture of safety vigilance and participation. Conversely, low reporting may indicate a need for improved communication or trust building.
- Employee Surveys and Interviews: I periodically distribute surveys and conduct interviews to gauge the staff’s perception of safety in the workplace. This qualitative data helps me understand the effectiveness of safety communications and the level of staff engagement.
- Feedback System Responsiveness: A responsive feedback system is vital. I examine how quickly and effectively the company responds to employee safety concerns and feedback, as this responsiveness is indicative of engagement levels.
By monitoring these aspects, I can get a well-rounded picture of how engaged employees are in safety initiatives and how open and effective the feedback loop is between staff and management. This indicator not only helps to fine-tune safety policies but also fosters a culture where safety is a shared responsibility.
Leveraging Technology to Monitor and Improve HSE KPIs
As a professional in the field of Health, Safety, and Environment (HSE), I’m keenly aware of the pivotal role technology plays in enhancing our ability to monitor and improve HSE KPIs (Key Performance Indicators). The advancements in software and analytical tools have revolutionized the way HSE metrics are tracked, analyzed, and acted upon.
At the heart of this technological revolution is the ability to collect real-time data. I’ve experienced how wearable technology can send immediate alerts if an employee is exposed to hazardous conditions, thus preventing potential incidents. Moreover, using mobile applications, team members can report near-misses and safety observations on the go, ensuring that this vital data is captured and available for analysis.
Another key benefit of using technology is the capacity to centralize HSE data. Employing a comprehensive HSE management system allows for the integration of data from various sources. This helps me, and my colleagues, to have a holistic view of our HSE performance, facilitating more informed decision-making.
I’ve also found that advanced analytics capabilities are instrumental in identifying trends and predictive insights. For instance, AI-powered analytics can highlight areas of risk that might have gone unnoticed, allowing us to proactively implement corrective actions before an incident occurs.
Furthermore, the use of online dashboards to visualize HSE KPIs has empowered me to communicate the performance effectively to all stakeholders. These dashboards provide an at-a-glance overview of how we’re tracking against our HSE goals, and can be personalized to suit the unique needs of each stakeholder.
- The integration of Geographic Information Systems (GIS) for location tracking and incident mapping.
- Adoption of cloud computing for better data accessibility and collaboration among teams dispersed geographically.
- Implementation of Internet of Things (IoT) devices for monitoring environmental conditions, such as air quality or noise levels.
Incorporating these technological solutions has not only streamlined the way I monitor and report on HSE KPIs but has also led to tangible improvements in our overall HSE performance.
Artificial Intelligence as Your Safety Net: AI Innovations for a Safer Work Environment
Benchmarking and Setting Realistic HSE Goals
As I delve into the intricacies of Health, Safety, and Environment (HSE) performance measurement, I understand the critical role of benchmarking and goal-setting within this framework. By analyzing leading and lagging indicators, I recognize that benchmarking is more than a comparison game; it’s a strategic approach to elevate an organization’s HSE standards.
To commence benchmarking, I first review historical data and identify trends that highlight areas for improvement. I compare our company’s performance against industry averages, best practice standards, and past internal achievements to set a realistic yet challenging baseline. This comprehensive assessment encompasses performance metrics such as incident rates, audit scores, and regulatory compliance statuses.
Here’s how I systematically approach the benchmarking and goal-setting process:
- Identify industry standards and regulatory requirements to ensure our benchmarks align with legal and best practice expectations.
- Analyze internal historical data to assess our past performance, gathering insights to ascertain progress over time.
- Engage with stakeholders to gather diverse perspectives on realistic and achievable HSE objectives.
- Prioritize areas of improvement that have the most significant impact on health, safety, and the environment.
- Set SMART (Specific, Measurable, Achievable, Relevant, Time-bound) goals that drive continual improvement without setting unattainable standards.
Each goal is periodically reviewed to adapt to any changes within the business or the industry. I acknowledge that HSE landscapes are dynamic, and flexibility is vital in responding to emergent risks and opportunities efficiently. By firmly embedding benchmarking and tailored goal setting within our HSE strategy, I facilitate an environment of constant learning and improvement, something that is indispensable in the realm of HSE performance evaluation.
Analyzing the Data: Turning KPIs into Actionable Insights
Once I have identified and tracked the relevant Health, Safety, and Environment (HSE) Key Performance Indicators (KPIs), the next crucial step in my performance measurement is to analyze the data. This is about transforming numbers into meaningful narratives that inform decision-making and inspire effective action.
When analyzing KPIs, I employ a structured approach:
- Identify trends and patterns: I look for consistent issues or improvements over time. Is there a particular area showing repeated safety incidents? Recognizing trends allows me to pinpoint areas for improvement or strategies that are working well.
- Benchmark against industry standards: How does my performance stack up against industry norms or competitors? Benchmarking puts my data into context and can highlight where I’m ahead or behind the curve.
- Evaluate the root cause: It’s imperative not to stop at the ‘what’ but delve into the ‘why.’ I examine underlying factors contributing to the KPI results. This might involve discussions with staff, reviewing processes, or inspecting equipment.
- Prioritize issues based on impact: Not all findings warrant the same level of attention. I prioritize based on the potential impact on employee well being, environmental compliance, or the bottom line.
- Communicate findings: I share insights with stakeholders in a clear, concise manner, emphasizing both successes and areas needing attention.
- Develop an action plan: With insights in hand, I draft a plan to address the issues. This might involve revising protocols, introducing new training programs, or updating equipment.
- Set measurable targets: For accountability, I establish clear, attainable targets for improvement, ensuring they are SMART (Specific, Measurable, Achievable, Relevant, Time-bound).
- Monitor progress and adjust as necessary: Ongoing evaluation of the action plan is vital. If something isn’t working, I’m flexible enough to tweak my approach.
By turning HSE KPIs into actionable insights, I can make informed decisions that not only improve performance but also foster a safer, more sustainable work environment. This analytical process is cyclical and ever-evolving, reflecting the dynamic nature of HSE management.
Case Studies: Success Stories of Effective HSE KPI Implementation
In my career as an HSE professional, I’ve come across several case studies that epitomize the successful implementation of Health, Safety, and Environment (HSE) Key Performance Indicators (KPIs). These stories not only highlight the strategic benefits of KPIs but also underscore how companies can foster a culture of continuous improvement and safety excellence.
One such success story involves a global petrochemical company that faced frequent safety incidents. The introduction of targeted HSE KPIs like Lost Time Injury Frequency (LTIF) and Process Safety Events (PSE) led to a 50% reduction in reportable accidents within two years. By rigorously monitoring and analyzing these indicators, the company was able to identify root causes and implement corrective actions, demonstrating the profound impact of precise HSE KPIs on operational safety.
Another marked success comes from a manufacturing firm that introduced a comprehensive HSE dashboard encompassing metrics such as Near near-miss frequency and Safety Training Completion rates. This initiative resulted in enhanced employee engagement in safety programs and a 70% decrease in near misses, underscoring the role that well-communicated and regularly updated KPIs play in heightening awareness and preventative measures.
Lastly, an environmental consultancy I collaborated with adopted sustainability-focused KPIs, including energy consumption and waste reduction percentages. These KPIs were embedded in their corporate objectives, leading to not only improved environmental performance but also substantial cost savings and positive stakeholder feedback.
Each of these examples stands testament to the fact that carefully selected and implemented HSE KPIs can drive significant improvements, mitigating risk and leading businesses towards a sustainable future, all while authentically encapsulating the spirit of the “Calculation Success” narrative.
Challenges in KPI Measurement and How to Overcome Them
As someone deeply invested in Health, Safety, and Environmental (HSE) performance, I understand that Key Performance Indicators (KPIs) are our benchmarks for tracking and improving safety standards. However, accurately measuring KPIs comes with its challenges:
- Data Quality and Consistency: One of the foremost problems I face is ensuring that the data I use is accurate, reliable, and collected consistently. Inconsistent data can lead to incorrect analyses. I’ve found that standardizing data collection processes and training staff on their importance can mitigate this issue. It’s crucial to use consistent methods and tools to collect data so that it can be compared over time.
- Setting Realistic and Relevant KPIs: Sometimes, I’ve observed a tendency to set KPIs that are either too ambitious or not aligned with the actual goals of the organization. To overcome this, KPIs must be set through a collaborative process involving stakeholders who understand the practical aspects of the HSE domain. The SMART criteria (Specific, Measurable, Achievable, Relevant, Time-bound) have served as a helpful guide.
- Overcoming Siloed Information: Different departments sometimes hold on to data without sharing it, making it difficult to get a comprehensive view of HSE performance. Breaking down these silos, perhaps through integrated software systems or inter-departmental meetings, is a strategy I have employed with success.
- Adapting to Changing Regulations: Regulatory changes can mean that KPIs need to be adapted. Staying abreast of changes and being agile is essential. I ensure that a part of the strategy includes regular reviews of regulations.
- Employee Engagement: Lastly, without the active participation of the workforce in safety initiatives, KPI measurement will reflect an incomplete picture. Thus, cultivating a culture of safety and involving employees at every level in safety discussions and feedback loops is pivotal. A shared sense of responsibility and participation can significantly impact the accuracy of KPI measurement.
In my journey, bridging the gap between KPI measurement challenges and mitigating strategies has underscored the dynamic nature of HSE management. Regular review and adaptation of strategies are as important as the KPIs themselves.
Future Trends in HSE Performance Metrics
In the rapidly evolving field of Health, Safety, and Environment (HSE), I continually adapt to integrate the most current trends in performance measurement. Here’s a glimpse of what the future may hold:
- Enhanced Data Analytics: I predict a significant shift towards advanced data analytics in HSE performance metrics. The integration of predictive analytics and AI will enable us to anticipate and mitigate risks before they manifest, providing a proactive rather than reactive approach to HSE management.
- Real-time Monitoring: With the Internet of Things (IoT) becoming more prevalent, I see the potential for real-time HSE monitoring to become standard practice. Sensors could provide instant data on various parameters, such as exposure levels to hazardous substances or the occurrence of near-misses.
- Worker Engagement Metrics: Future metrics are likely to include a focus on worker engagement and behavior. By measuring aspects like safety culture, reporting rates, and employee feedback, I can gain a more comprehensive understanding of HSE performance.
- Sustainability and Environmental Stewardship: As corporate responsibility towards the environment gets increased attention, I must expand our metrics to include sustainability indicators such as carbon footprint, waste reduction, and resource conservation performance.
- Integration with Business Intelligence: I anticipate that HSE metrics will become more intertwined with overall business intelligence systems, contributing to strategic decision-making and optimizing business performance while ensuring safety and environmental compliance.
- Dynamic Risk Profiling: With the assistance of machine learning, I’m looking at developing dynamic risk profiles that can update in real-time based on a multitude of factors, such as operational changes or external environmental conditions.
The challenge lies in aligning these future trends with the fundamental goal of HSE: to reduce risk and enhance the safety and wellbeing of the workforce and environment. As I continue to refine HSE performance measurement, these forward-looking metrics will inevitably shape a more predictive, responsive, and integrated approach to health and safety.
Conclusion: Making a Commitment to Continuous HSE Improvement
As I reflect on the intricate process of measuring Health, Safety, and Environmental (HSE) performance, I am reminded of the profound responsibility I carry to ensure the well-being of not just employees, but also the community and environment influenced by my organization’s operations. Calculating success in HSE isn’t merely about meeting benchmarks or surpassing competitors; it’s about making an enduring commitment to continuous improvement.
Achieving excellence in HSE is a dynamic, never-ending journey. It’s critical for me to stay informed about the latest best practices, technological advances, and regulatory changes. My strategy involves:
- Regularly reviewing and updating HSE policies and procedures.
- Establishing clear, realistic, and incrementally challenging goals.
- Engaging employees at all levels for their insights and participation in safety culture.
- Implementing robust training programs that go beyond compliance and encourage proactive safety behavior.
I rely on a systematic approach to performance measurement that leverages data analytics, ensuring I can identify areas for enhancement swiftly and accurately. The integration of leading and lagging indicators provides a comprehensive picture of HSE performance, allowing me to anticipate potential issues and address them proactively.
Moreover, I’ve learned the importance of transparency in my journey towards HSE excellence. Sharing successes and setbacks with stakeholders not only fosters trust but also cultivates an environment where continuous improvement is a shared objective.
In conclusion, the commitment I have made to continual HSE improvement is not just a professional obligation—it’s a moral imperative. It’s about safeguarding the future, protecting lives, and preserving the world we live in. I am devoted to this cause and will persistently seek ways to enhance HSE performance, for the benefit of all.
Download many safety resources at safetybagresources