Hydrogen Sulfide New Regulations
3 min readHydrogen sulfide (H2S) regulations have gotten an overhaul for 2017. These regulatory changes are a top priority that need to be addressed in order to keep workers safe.If your business strives for excellence in safety, these are policies that belong on the front burner. Keep reading to find out what you need to know.
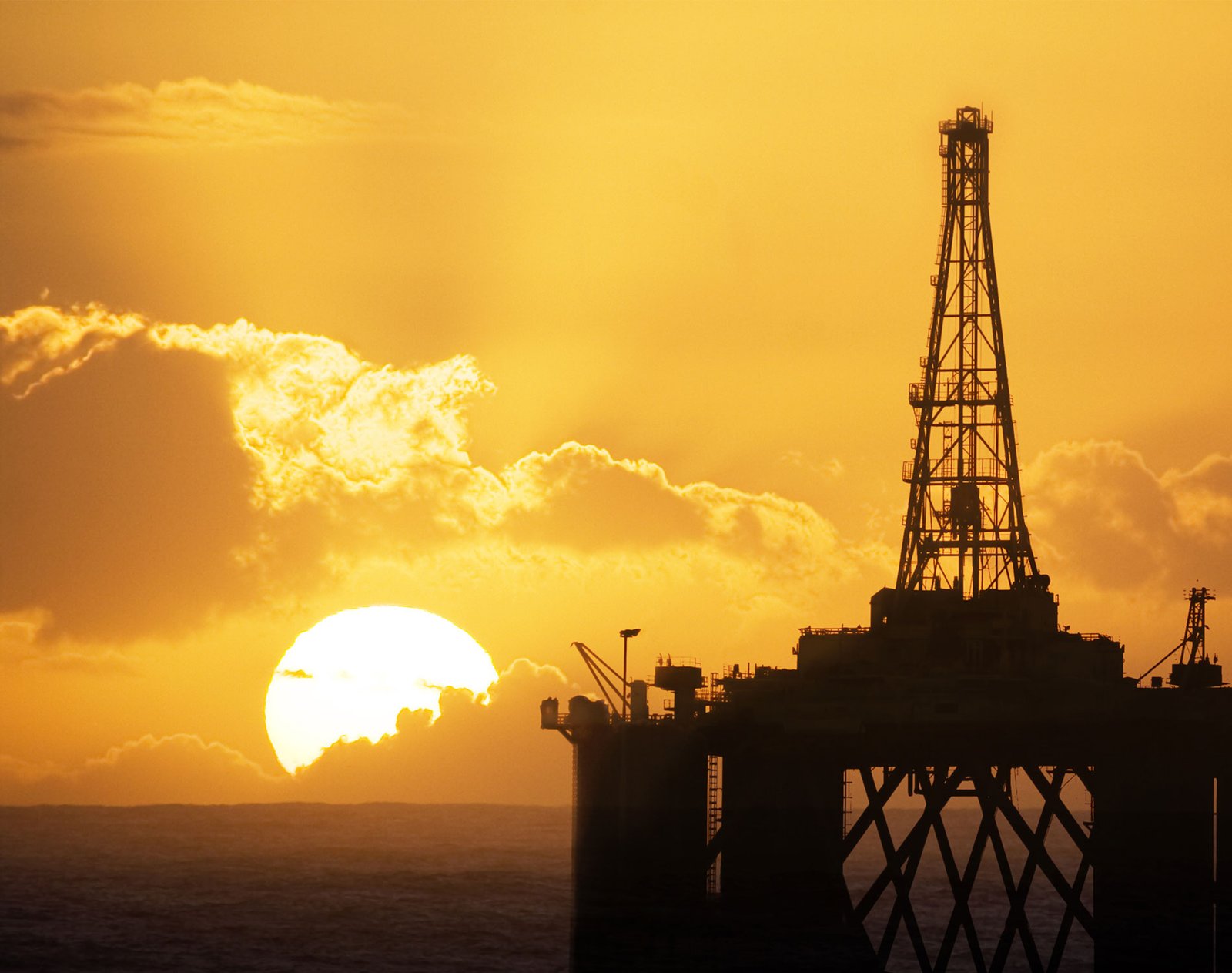
Eliminating Confusion
Previous standards used terminology that some found a bit challenging to interpret. Combined with regulations that caused some head scratching of their own (the line between what was mandatory and what was advisory was often blurred), this caused a lot of needless difficulty and may have put workers at risk.
The 2017 updated performance standard clarifies many of the requirements, ensuring that employers and safety professionals know exactly what they need to do to keep workers safe.
The Update in a Nutshell
A few features stand out in the 2017 regulations. These specify, broadly, that:
- Workers must have a demonstrated competency of H2S knowledge, training, and equipment
- Workers require a minimum of 34 hours of H2S training and annual refresher training
- Employers must provide respiratory protection (of appropriate type and size) to all workers and visitors on a site where H2S is used
Revised Exposure Limits
The new standard places limits on the safe exposure to certain chemicals, including hydrogen sulfide.
Limits for H2S as well as poisons (such as carbon monoxide), asphyxiates (including carbon dioxide), and volatile organic compounds (VOCs) such as heptane, hexane, octane, pentane, and propane must be carefully monitored and controlled. Chemical manufacturers and chemical product importers must also evaluate the chemicals produced in their workplaces.
Getting Ready for Inspections
Regulatory inspections are a challenge for any business, and although they might mean a halt or a slow-down to production, that should be anticipated and treated as an important part of your operations. But there are steps you can take to prepare yourself. One of the most important ones is working with an industry expert who is knowledgeable about the new standards. They will help you improve your processes, implement the right controls and best practices, and prepare your business to meet the updated standards.
Another important step is working with standard-compliant programs to meet the training requirements. Developing an ongoing relationship with a training firm will help ensure continuity between your initial training and your annual refresher training.
All of your efforts won’t help make the inspections go smoothly if you don’t have proof handy. Ensure that your record-keeping practices are adequate and consider upgrading to a digital or cloud-based system that will allow easy retrieval of the compliance documentation.
Important Steps
Employers must take a variety of factors into consideration, including chemical hazard identification, potential contact points with hazardous chemicals, and the adequacy of PPE for combating hazardous chemical exposure. Working with an expert will give you the peace of mind of knowing that you are compliant and doing what you need to keep your workers safe from harm.