Guideline for Process Safety Management Program with Free Training
Process Safety Management Progam Program ( PSM) guidelines for preventing or minimizing the consequences of catastrophic releases of toxic, reactive, flammable, or explosive chemicals. These releases may result in toxic, fire, or explosion hazards or injuries in the following industries: power generation, petrochemical, refining, and pulp and paper. Employees performing work at a location who are covered by Process Safety Management or Risk Management Plan standards must be trained in the requirements for the applicable portions of their plan. If a facility acquires chemicals in quantities that exceed the threshold for inclusion, the facility must implement a written Process Safety Management Program ( PSM ) and Risk Management Process (RMP )program. This article will outline the guides for PSM Program in addition Free download of Materials for Process Safety Management
Also Read: The Process and Benefits of Process Safety

PSM / RMP Program
The PSM/RMP program requires that each facility have an Emergency Response Program. Facilities must also coordinate response actions with local emergency planning and response agencies.
The following guidance applies to RMP Regulated Facilities only.
- Executive Summary
Include an Executive Summary with a brief description of the elements of the RMP program.
- Off-site Consequence Analysis
Evaluate one worst-case release scenario for each process involving highly hazardous chemicals over threshold quantities.
- Off-site Consequence Analysis Records
Complete and maintain a five-year accident history.
- Maintain descriptions, assumptions, and parameters for worst-case and alternative-case scenarios.
- Maintain rationale for the selection, controls, and effects of controls on the release rate and quantity records.
- Maintain the following data: quantity released, release rate, duration of release, methodology to determine endpoints, population data, and environmental receptor data.
The following guidance applies to all PSM Regulated Facilities and RMP Regulated Facilities where the distance of the worst-case release is greater than the nearest receptor, or the facility has had a catastrophic release in the past 5 years.
- Management System
The facility must develop a management system to oversee the PSM/RMP process. Assign a qualified person who is responsible for developing and implementing the PSM/RMP program. This person must also identify local regulations that are applicable to this procedure.
- Off-site Consequence Analysis
The facility must prepare an off-site consequence analysis that includes evaluations for worst-case and alternate-case scenarios. Select an appropriate air dispersion model based on the type of release. Base the quantity of the release and model parameters on regulatory requirements. Evaluate the off-site impact on the environment and population for each chemical. An outside consultant should assist with this complicated analysis.
- Process Safety Information
- Chemical information for all PSM/RMP processes must be comprehensive enough for an accurate assessment of the fire and explosion characteristics, reactivity hazards, safety and health hazards to workers, and the corrosion and erosion effects on the process equipment and monitoring tools. Assemble chemical information for the processes including toxicity reactivity, corrosivity, exposure limits, physical data, thermal and chemical stability, and hazardous effects. Specify the maximum intended inventory of the equipment.
- All process technology must include diagrams (see Sample Process Technology Diagram Below), established criteria for maximum inventory levels for process chemicals, process chemistry limits beyond which would be considered upset conditions, operating ranges, and a qualitative estimate of the consequences or results of deviation that could occur if operating beyond the established process limits.
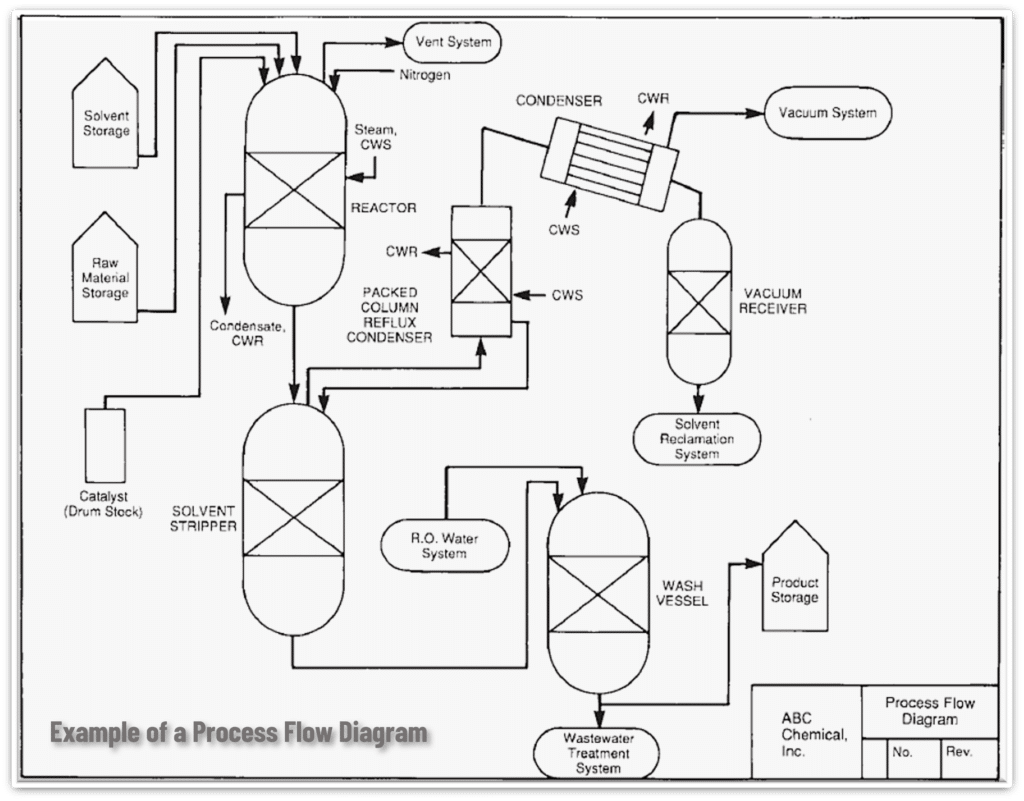
- All process equipment and interconnecting process flow lines should be illustrated in a block flow diagram (see Sample Block Flow Diagram Below), which shows flow rates, materials of construction, stream composition, temperatures, and pressures when necessary for clarity. Assemble the following diagrams: P&IDs, electrical classification, relief system, ventilation, and safety systems. Prepare design PH codes and standards, and material and energy balances.
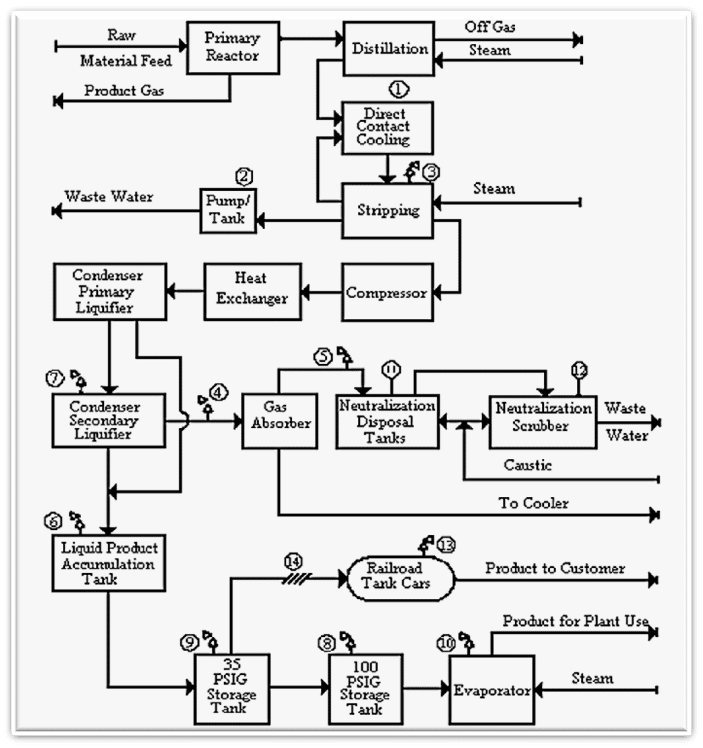
- Maintain all equipment specifications, codes, and standards for design and operation.
Process Hazard Analysis/Prevention Program
A process hazard analysis is an organized and systematic effort to identify and analyze the significance of potential hazards associated with the processing or handling of highly hazardous chemicals. Consider using an outside consultant to provide this complicated program. Perform a hazard analysis for a process initially, every 5 years, and before modifications.
Also Read: Photo of the day: Dangerous Goods Classes
Operating Procedures and Practices
Establish operating procedures for all affected processes, including tasks, data to record, operating conditions to maintain, samples to collect, and safety and health precautions to take. The operating procedures must address items such as pressure limits, temperature ranges, flow rates, an appropriate response to upset and alarm conditions, and start-up and shutdown procedures. Develop procedures for lockout/Tagout, process opening, confined space, and equipment inspections.
Employee Training
Develop training to help employees understand the nature and causes of the problems created by process operations and to increase employee awareness and reactions to the hazards of each process. Training must also include operating procedures, health and safety, emergency operations, and safe work practices. Provide refresher training at least every two years.
Mechanical Integrity
Develop a mechanical integrity program to ensure the integrity of process equipment. Include the identification of all equipment and instrumentation, written maintenance procedures, documentation of maintenance training, and documentation of inspections and testing.
Incident Investigation
- Each facility must develop in-house capabilities to investigate incidents that occur in the facility, including procedures for written investigations. See Incident Reporting and Investigation for guidelines.
- Each facility must maintain a five-year accident history of all accidental releases from covered processes. The reports must include: dates, duration of release, a chemical released, type of release, weather conditions, release impacts, factors of the release, responders, and changes made.
Contractor Participation
This section provides guidance for all Services personnel working at PSM or RMP-regulated facilities:
- The Facility Manager must review the safety performance records of contractors hired to work in and around processes that involve highly hazardous chemicals. It is important to ensure that contractors can complete specialized work without endangering the safety and health of employees at the plant. Develop written procedures that include training for contractors. Services personnel must comply with contractor pre-qualification requirements as requested by the Customer.
- Employees must complete training in the hazards of their jobs and safe work practices.
- Before employees begin work, the Customer must conduct required site training, including:
- site hazards, known potential fire, explosion, or toxic release hazards related to the site or work area,
- site emergency response plans, site work practices, and permits.
- The Customer must provide documentation of training for the site, including an outline of content, name, date, and test method. Each employee must be instructed in known potential fire, explosion, or toxic release hazards related to his or her job and potential hazards created by the Customer or other contractors at the Customer site or adjacent geographical areas.
- Employees must request process safety information, such as MOCs, process hazard information, and mechanical integrity information; PSM required operating standards, or procedures pertinent to their work on a customer site.
- Employees must follow safety rules, work practices, and customer rules at all times including during high-risk activities such as confined space entry, hot work, and security. Do not perform hot work without obtaining a hot work permit.
- Employees must advise the Customer contact of any hazard identified at the Customer’s work site.
- Report all accidents, events, near misses, and hazards to the Customer immediately. Investigate all incidents per –Incident Reporting and Investigation and any applicable Customer requirements.
Pre-Startup Safety
Ensure that all equipment meets safety and operating specifications before using a highly hazardous chemical in a process. Personnel must be properly trained before start-up, operation, and maintenance. Emergency procedures must be in place. Include a pre-startup review in the normal start-up operating procedure for each system. Develop written procedures for conducting a pre-startup safety review.
Also Read: Free Pre-Startup Safety Review Checklist (PSSR)
Non-routine Work Authorizations
Control non-routine work in process areas consistently. The work authorization procedures must reference and coordinate, as applicable, lockout/Tagout procedures, line-breaking procedures, confined space entry procedures, and hot work permits. Conduct this work in accordance with the following procedures:
Managing Change
Manage all modifications to equipment, procedures, raw materials, and processing conditions. Issue requirements in accordance with the specified procedure for Review of New/Modified Facilities and Equipment.
Trade Secrets
The Facility Manager must ensure that all information necessary to comply with the PSM program is available to personnel with no regard to possible trade secret status.
Employee Participation
Facility management must consult with employees regarding the development and implementation of the PSM program, including the assessment of hazards. Prepare a written employee participation plan. Employees must have access to information developed under the PSM Program.
Records
Maintain all records related to PSM/RMP-covered operations until the covered operation is no longer being conducted at the site. Records include:
- Written PSM/RMP plans
- Drawings and process maps
- On and Off-site consequence analysis
- Inventory documentation equipment-specific codes, standards, and specifications
- Accident history
Training
- All employees involved with highly hazardous chemicals must be trained to understand the safety and health hazards of the chemicals and processes in their work area. The training must comply with the Hazard Communication program.
- Additional training in operating procedures, safe work practices, emergency response and evacuation, and other areas pertinent to process safety and health must be covered in the facility’s training program.
- Provide initial and refresher training, in accordance with – EHS Training. Before beginning work at a customer site, service employees must receive training on the applicable portions of the Customer’s PSM/RMP plan.
Download Process Safety Management Training Material
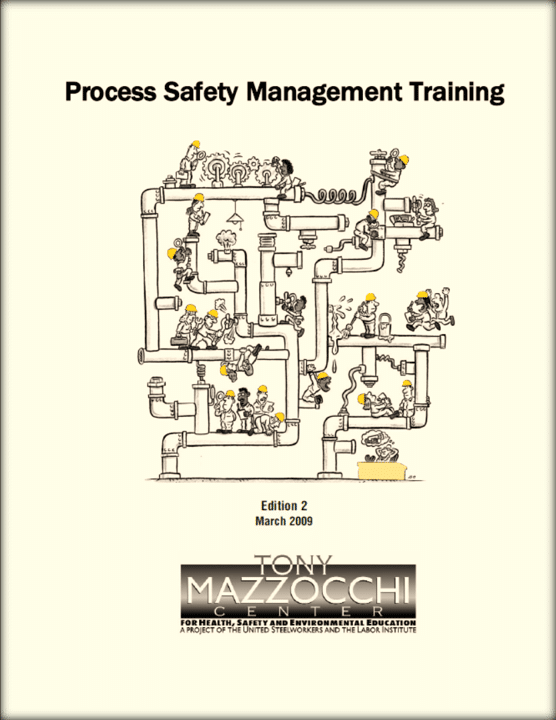
Auditing
- Review the PSM-required elements of the written plan every three years.
- Review the RMP-required elements of the written plan every five years.
- Review the elements of the PSM/RMP programs every two years as part of the EHS Power Self-Auditing Tool, Process Safety, and Air Quality – E Accidental Release Prevention (RMP) Modules. See Self-Auditing.
- Audit maintenance records related to PSM/RMP operations for the previous two years.
Also Read Process Safety Management (PSM) Compliance checklist
For more safety Resources Please Visit Safetybagresources