Guideline for Hazardous Locations
9 min readElectrical equipment can cause explosions in certain atmospheres. Equipment used in areas where explosive concentrations of dust or vapors may exist must be equipped with special wiring and other electrical components for safety purposes. Hazardous (classified) locations such as these might exist in aircraft hangars, gasoline stations, paint-finishing locations, or grain bins.
In North America, the most widely used hazardous location classification system is defined by the National Fire Protection Association (NFPA) Publication 70, National Electric Code® (NEC) in Articles 500 to 506. The type of hazardous substances that is or may be present in the air in quantities sufficient to produce explosive or ignitable mixtures is specified.

The NFPA establishes area classifications based on Classes, Divisions, and Zones that when combined delineate the hazardous conditions of a specific area. This classification method provides a description of the hazardous material that may be present, and the probability that it is present, so that the appropriate equipment may be selected and safe installation practices followed. The Occupational Safety and Health Administration (OSHA) has adopted these hazardous classifications from the NEC and they are defined in 29 Code of Federal Register (CFR) 1910.399.Definition of Hazardous Locations

Class I Locations
Class I locations are those in which flammable gases or vapors are or may be present in the air in quantities sufficient to produce explosive or ignitable mixtures. Class I locations are further subdivided into two Divisions and three Zones.
Class I, Division 1: There are three different situations that could exist to classify an area as a Class I, Division 1 location:
- Ignitable concentrations of flammable gases or vapors may exist under normal operating conditions.
- Ignitable concentrations of such gases or vapors may exist frequently because of repair or maintenance operations or because of leakage.
- Breakdown or faulty operation of equipment or processes might release ignitable concentrations of flammable gases or vapors and might also cause simultaneous failure of electric equipment.
Class I, Division 2: One of the following three situations must exist in order for an area to be considered a Class I, Division 2 location:
- Volatile flammable liquids or flammable gases are handled, processed or used, but the hazardous liquids, vapors or gases will normally be confined within closed containers or closed systems from which they can escape only in the event of accidental rupture or breakdown of such containers or systems, or as a result of abnormal operation of equipment.
- Ignitable concentrations of gases or vapors are normally prevented by positive mechanical ventilation, and which might become hazardous through failure or abnormal operations of the ventilating equipment.
- Adjacent to a Class I, Division 1 location, and to which ignitable concentrations of gases or vapors might occasionally be communicated unless such communication is prevented by adequate positive-pressure ventilation from a source of clean air, and effective safeguards against ventilation failure are provided.
Class I, Zone 0: One of the following two situations must exist in order for an area to be considered a Class I, Zone 0 location:
- Ignitable concentrations of flammable gases or vapors are present continuously.
- Ignitable concentrations of flammable gases or vapors are present for long periods of time.
Class I, Zone 1: One of the following four situations must exist in order for an area to be considered a Class I, Zone 1 location:
- Ignitable concentrations of flammable gases or vapors are likely to exist under normal operating conditions.
- Ignitable concentrations of flammable gases or vapors may exist frequently because of repair or maintenance operations or because of leakage.
- Equipment is operated or processes are carried on of such a nature that equipment breakdown or faulty operations could result in the release of ignitable concentrations of flammable gases or vapors and also cause simultaneous failure of electric equipment in a manner that would cause the electric equipment to become a source of ignition.
- A location that is adjacent to a Class I, Zone 0 location from which ignitable concentrations of vapors could be communicated unless the communication is prevented by adequate positive-pressure ventilation from a source of clean air and effective safeguards against ventilation failure are provided.
Class I, Zone 2: One of the following four situations must exist in order for an area to be considered a Class I, Zone 2 location:
- Ignitable concentrations of flammable gases or vapors are not likely to occur in normal operation and if they do occur will exist only for a short period.
- Volatile flammable liquids, flammable gases or flammable vapors are handled, processed or used, but in which the liquids, gases or vapors are normally confined within closed containers or closed systems from which they can escape only as a result of accidental rupture or breakdown of the containers or system or as the result of the abnormal operation of the equipment with which the liquids or gases are handled, processed or used.
- Ignitable concentrations of flammable gases or vapors normally are prevented by positive mechanical ventilation, but which may become hazardous as the result of failure or abnormal operation of the ventilation equipment.
- A location that is adjacent to a Class I, Zone 1 location, from which ignitable concentrations of flammable gases or vapors could be communicated, unless such communication is prevented by adequate positive-pressure ventilation from a source of clean air, and effective safeguards against ventilation failure are provided.
The table below provides a comparison between the “Class, Division” System and the “Zone” System:
Hazardous Material | Class, Division System | Zone System |
---|---|---|
Gases or Vapors | Division 1 | Zone 0 and Zone 1 |
Gases or Vapors | Division 2 | Zone 2 |
The frequency of occurrence determines the level of hazard for a location. The longer the material is present, the greater the risk:
Frequency of Occurrence | Class, Division System | Zone System |
---|---|---|
Continuous | Class 1, Division 1 | Zone 0 |
Intermittent Periodically | Class 1, Division 1 | Zone 1 |
Abnormal Conditions | Class 1, Division 2 | Zone 2 |
Class II Locations
Class II hazardous locations are areas where combustible dust, rather than gases or liquids, may be present in varying hazardous concentrations. Class II locations are further subdivided into two divisions.
Class II, Division 1: One of the following three situations must exist in order for an area to be considered a Class II, Division 1 location:
- Where combustible dust is present in the air under normal operating conditions in such a quantity as to produce explosive or ignitable mixtures. This could be on a continuous, intermittent, or periodic basis.
- Where an ignitable and/or explosive mixture could be produced if a mechanical failure or abnormal machinery operation occurs.
- Where electrically conductive dust in hazardous concentrations is present.
Class II, Division 2: One of the following two situations must exist in order for an area to be considered a Class II, Division 2 location:
- Combustible dust will not normally be in suspension in the air in quantities sufficient to produce explosive or ignitable mixtures, and dust accumulations will normally be insufficient to interfere with the normal operation of electric equipment or other apparatus, but combustible dust may be in suspension in the air as a result of infrequent malfunctioning of handling or processing equipment.
- Resulting combustible dust accumulations on, in or in the vicinity of the electric equipment may be sufficient to interfere with the safe dissipation of heat from electric equipment or maybe ignitable by abnormal operation or failure of electric equipment.
Class III Locations
Class III hazardous locations contain easily ignitable fibers or flyings, but the concentration of these fibers or flyings are not suspended in the air in such quantities that would produce ignitable mixtures. Class III locations are further subdivided into two divisions.
Class III, Division 1: Easily ignitable fibers or materials producing combustible flyings are handled, manufactured or used.
Class III, Division 2: Easily ignitable fibers are stored or handled, other than in the process of manufacture. Other Key Definitions
Explosion-proof apparatus: Apparatus enclosed in a case that is capable of withstanding an explosion of a specified gas or vapor that may occur within it and of preventing the ignition of a specified gas or vapor surrounding the enclosure by sparks, flashes or explosion of the gas or vapor within, and that operates at such an external temperature that it will not ignite a surrounding flammable atmosphere.
Intrinsically safe: An apparatus/equipment in which all the circuits in which any spark or thermal effect is incapable of causing ignition of a mixture of flammable or combustible material in the air under prescribed test conditions as described in ANSI/UL 913 Edition 8.
Insulated: Separated from other conducting surfaces by a dielectric (including air space) offering high resistance to the passage of current. Hazardous Groupings
In 29 CFR 1910.307(c)(2)(ii), OSHA requires all equipment used in a hazardous location to be marked with the class, group, and operating temperature or temperature range for which it is approved. However, OSHA does not provide a definition of group classifications in 29 CFR 1910.307 or 399. OSHA does provide a note under 29 CFR 1910.307(c)(1) that states:
NFPA 70, the National Electrical Code, lists or defines hazardous gases, vapors, and dust by “Groups” characterized by their ignitable or combustible properties.
To meet OSHA’s marking requirement, the marking must include the hazardous group the equipment is approved to operate in. The 2014 edition of the NEC defines these groups as:
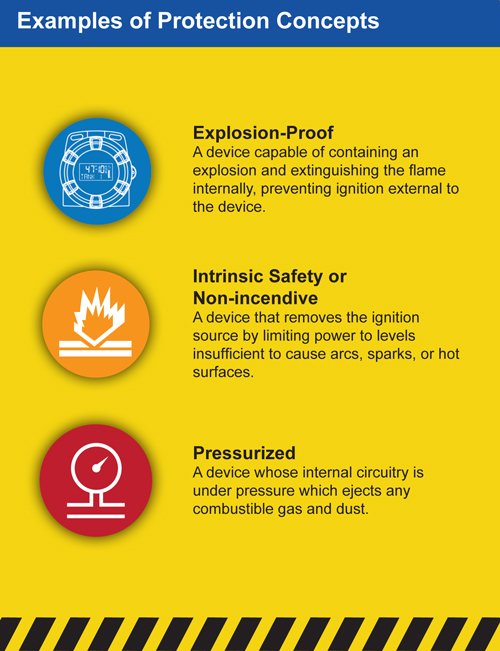
Group A: Acetylene – 497:3.3.5.1.1
Group B: Flammable gas, flammable liquid-produced vapor or combustible liquid-produced vapor mixed with air that may burn or explode, having either a maximum experimental safe gap (MESG) value less than or equal to 0.45mm or minimum igniting current ratio (MIC ratio) less than or equal to 0.40. Example: Hydrogen – 497:3.3.5.1.2.
Group C: Flammable gas, flammable liquid-produced vapor or combustible liquid-produced vapor mixed with air that may burn or explode, having either a maximum experimental safe gap (MESG) value greater than or equal to 0.45mm or less than 0.75mm, or minimum igniting current ratio (MIC ratio) greater than 0.40 and less than or equal to 0.80. Example: Ethylene – 497:3.3.5.1.3.
Group D: Flammable gas, flammable liquid-produced vapor or combustible liquid-produced vapor mixed with air that may burn or explode, having either a maximum experimental safe gap (MESG) value greater than or equal to 0.75mm or minimum igniting current ratio (MIC ratio) greater than 0.80. Example: Propane – 497:3.3.5.1.4.
Group E: Atmospheres containing combustible metal dust, including aluminum, magnesium, and their commercial alloys, or other combustible dust whose particle size, abrasiveness, and conductivity present similar hazards in the use of electrical equipment. Example: Metal dust – 499:3.3.4.1.
Group F: Atmospheres containing combustible carbonaceous dust that have more than 8% total entrapped volatiles (based on ASTM D3175-11) or that have been sensitized by other materials so that they present an explosion hazard. Examples: Coal, carbon black, charcoal, and coke dust – 499:3.3.4.2.
Group G: Atmospheres containing combustible dust not included in Groups E or F. Examples: Flour, grain, wood, plastic, and chemicals – 499:3.3.4.3.
Reading Hazardous Area Approval Labels
A device that has been certified by one of the aforementioned agencies will bear that agency’s mark so that the device purchaser and installer can know immediately that the particular device is approved for use in a hazardous area. All of the information about area classification, division and/or zone, equipment group, and temperature class is also provided on the equipment label. It may not be readily apparent how to make sense of it all, however. Below is an image of the product label from a Precision Digital product, the PD8 ProtEX-MAX, with all applicable agency approval information.
What may look like a jumble of letters and numbers is actually very specific and crucial information that is necessary for any hazardous area application. An installer or purchaser needs to be able to break down this code in order to properly vet the equipment being installed.

Commonly Asked Questions
Q: Can I use a piece of equipment approved for use in Division 1 hazardous location in Division 2 hazardous location?
A: Yes. If the equipment has been approved for use in Division 1 hazardous location, it can be used in Division 2 hazardous location, providing it is in the same class and group.
Q: Can equipment approved for a Class I hazardous location be used in Class II hazardous location?
A: No. Equipment used in Class I and Class II hazardous locations are made for different purposes. Equipment approved for Class I hazardous locations must contain an internal explosion, while Class II approved equipment must seal out dust. They are not interchangeable.
2 thoughts on “Guideline for Hazardous Locations”