Guide for Working With Corrosive Substances and how to avoid it
13 min readEmployers must be aware of workplace hazards facing their employees and take appropriate action to minimize or eliminate exposure to these hazards. A Guide to Working with Corrosive Substances discusses precautions that can prevent serious health risks to workers due to exposure to corrosives. Corrosive chemicals are essential to many work processes; however, they can enter the body through ingestion, inhalation, or contact with the skin and eyes. Employee exposure to corrosives must be evaluated to determine the need for engineering and administrative controls as well as the need for personal protective equipment. The results from injuries can be severe and even fatal. Mists produced by liquids can result in lung damage if inhaled, serious burns or irritation can be the result of accidental contact with the skin or eyes, and lung and skin cancer have been linked to chromic acid. Additional threats to employees are posed by the ease with which many corrosive chemicals ignite, explode, or react with incompatible substances.
Also Read: Your steps to chemical safety
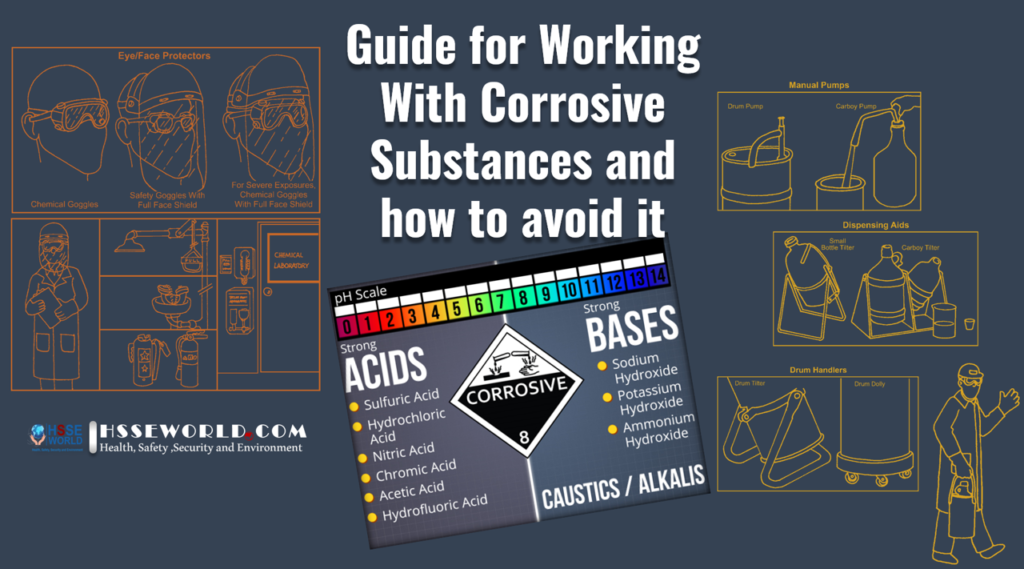
What Are Corrosives?
Information About Corrosives From the Department of Transportation
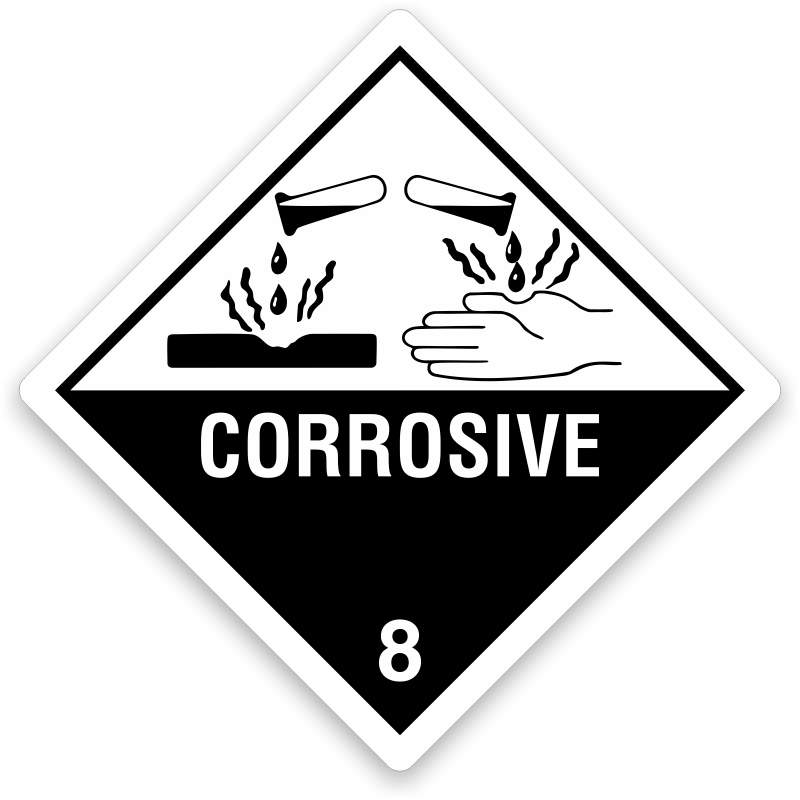
The U.S. Department of Transportation (DOT) regulations consider a corrosive material to be liquid or solid that causes visible destruction or irreversible alterations in human skin tissue at the site of contact, or in the case of leakage from its packaging, a liquid that has a severe corrosion rate on steel or aluminum. The DOT further develops this definition by offering the following:
- A material is considered to be corrosive if a liquid or solid causes full-thickness destruction of human skin at the site of contact within a specified period of time.
- A liquid is considered to have a severe corrosion rate if its corrosion rate exceeds 1/4 inch per year on steel [SAE 1020 (Society of Engineers)] or aluminum surfaces at a test temperature of 130°F when tested on both materials. (For additional information see 49 CFR 173.136 and § 173.137.
In most instances, corrosive materials may be identified by the label and/or placard (required by the DOT) shown in Figure 1
Also Read: Risk of Burns
Information About Corrosives From the Environmental Protection Agency
The Environmental Protection Agency (EPA), in regulating hazardous waste, uses pH as the criterion for determining if a substance is corrosive. Wastes with a pH of less than 2.0 or greater than 12.5 are considered to be corrosive.
The EPA defines corrosive wastes to include (1) aqueous waste exhibiting a pH of less than or equal to 2 or greater than or equal to 12.5 and (2) liquid waste capable of corroding steel at a rate greater than 1/4 inch per year. The EPA chose pH as one barometer of corrosivity because waste exhibiting low or high pH can cause harm to human tissue, promote the migration of toxic contaminants from other waste, react dangerously with other waste, and harm aquatic life. The EPA chose metal corrosion rate as its other barometer of corrosivity because waste capable of corroding metal can escape from the containers in which it is segregated and liberate other waste.
The percent of acidity/alkalinity provides an indication of the capacity of a waste to resist a change in pH. That measurement aids in the assessment of the hazard presented by a waste over the long term. However, it adds little to the assessment of the hazard posed by the waste during transportation, storage, and initial disposal. Furthermore, because the capacity of waste to retain low or high pH is as much a function of its disposal or storage environment as of its percent of acidity/alkalinity, there is no scientifically valid basis upon which to establish hazardous threshold levels of percent of acidity/alkalinity. (For additional information see 40 CFR 261.22.)
All corrosive materials and solutions have the EPA Hazardous Waste Number D002. The following are some of the more commonly used corrosives:
- Acetic Acid
- Ammonium Hydroxide
- Chromic Acid
- Hydrobromic Acid
- Hydrochloric Acid
- Hydrofluoric Acid
- Nitric Acid
- Oleum
- Perchloric Acid
- Phosphoric Acid
- Potassium Hydroxide
- Sodium Hydroxide
- Sulfuric Acid
Hazard Communication Standard Definition of Skin Corrosion
The Hazard Communication Standard (HCS) is now aligned with the Globally Harmonized System of Classification and Labeling of Chemicals (GHS). This update to the Hazard Communication Standard (HCS) will provide a common and coherent approach to classifying chemicals and communicating hazard information on labels and safety data sheets.
Chemical manufacturers and importers are required to determine the hazards of the chemicals they produce or import. Hazard classification under the new, updated 2012 Hazard Communication Standard provides specific criteria to address health and physical hazards as well as the classification of chemical mixtures. There is no requirement to test the chemical to determine how to classify its hazards. Appendix A to 29 CFR 1910.1200 shall be consulted for the classification of health hazards.
The definition of “skin corrosion” can be found in Appendix A of 29 CFR 1910.1200, the Hazard Communication standard.
“Skin corrosion is the production of irreversible damage to the skin; namely, visible necrosis through the epidermis and into the dermis, following the application of a test substance for up to 4 hours. Corrosive reactions are typified by ulcers, bleeding, bloody scabs, and, by the end of observation at 14 days, discoloration due to blanching of the skin, complete areas of alopecia, and scars. Histopathology should be considered to evaluate questionable lesions.”

Also Read:Chemical Risk Assessment form
Acids and bases are a part of the classification of corrosives and are chemicals that pose especially severe risks if personal contact is made with them. An important first step in understanding the effects of acids and bases is clearly distinguishing the two terms. Acids are those substances that yield hydrogen ions (H+) in an aqueous solution. Basic substances yield hydroxide ions (OH–) in an aqueous solution. When acids and bases are mixed they neutralize each other, producing salts. The resultant solution has a salty taste and none of the properties of either acids or bases.
Bases are also known as alkalis, caustics, or hydroxides. As previously noted, both acids and bases are included in a broader group of materials known as corrosives. As shown by the scale in Table 2 acidity and alkalinity are measured on a pH scale. The pH value of a solution determines its acidity or alkalinity (basicity).
What is pH?
The pH of a chemical is one of the physical properties that may be an indicator of a potential hazard. The pH scale runs from 0 to 14. Substances with a pH of less than 7 are said to be acidic. Vinegar has a pH of 3.5. Human skin has a pH of
4.5 to 6. If the substance has a pH of more than 7, it is basic. Wet cement and lye have a pH of 12 to 13. A neutral substance has a pH of 7. Pure water is a pH of 7. A pH of 0 is the strongest acid. A pH of 14 is the strongest base. The pH scale is logarithmic. For every whole number increase or decrease, the pH changes 10-fold! The pH of wet cement is one 1 billion times higher than the pH of the skin.

Other distinguishing characteristics between acids and bases include distinctions made by effects. Acids are chemical compounds that exhibit a sharp, sour taste in water solution. (Of course, you should never actually taste an acid to verify its effect.) Acids have corrosive action on metals and turn certain blue vegetable dyes red. An acid will turn blue litmus paper red.
Bases are chemicals that in solution are soapy, slippery to the touch, and turn red vegetable dyes blue. Red litmus paper is turned blue by a base.
Other distinguishing characteristics between acids and bases include distinctions made by effects. Acids are chemical compounds that exhibit a sharp, sour taste in water solution. (Of course, you should never actually taste an acid to verify its effect.) Acids have corrosive action on metals and turn certain blue vegetable dyes red. An acid will turn blue litmus paper red.
Bases are chemicals that in solution are soapy, slippery to the touch, and turn red vegetable dyes blue. Red litmus paper is turned blue by a base.
What Regulations Protect Us Against Corrosives?
The U.S. Department of Transportation
Specific Department of Transportation (DOT) regulations regarding corrosives are in the Code of Federal Regulations (49 CFR). Among DOT regulations are requirements for the packaging and loading of corrosives and guidelines for accidents where corrosives are involved (including the subject of leaking cargo tanks).
Regarding packaging, DOT requirements for corrosives cover the outage. The expansion traits of the liquid and the maximum increase of temperature to which it will be subjected in transit determine the proper vacant space (outage or ullage) in the package. (As a general rule, sufficient outage must be provided so that the packaging will not be liquid full at 130° F for packages of less than 110 gallons, and for tank cars not less than 2 percent of the total volume). DOT regulations also apply to the methods of closing and cushioning packaging and the types of containers that may be used for corrosives.
The following summary of DOT regulations offers general guidance regarding the loading of corrosive liquids: In general, individual carboys and frangible containers [containers capable of being broken] of corrosive liquids,
including charged electric storage batteries, when loaded by hand, must be individually loaded into and unloaded from
any motor vehicle in which they are to be transported. All reasonable precautions must be taken to prevent the dropping of any such containers or batteries containing corrosive liquids. No such container or battery may be loaded into a motor vehicle having an uneven floor surface. It shall be permissible to load corrosive liquids, more than one tier high above any floor only if such carboys or other containers are boxed or crated, or are in barrels or kegs.
No carboy or other container of nitric acid shall be loaded above any container containing any other kind of material.
The loading of carboys or other containers of nitric acid shall be limited in height to two tiers.
How Do Corrosives Harm Us and How Can We Protect Ourselves?
How Corrosives Harm Us
Most commonly, the eyes, skin, and respiratory system are the parts of the body affected by corrosive chemicals. Causes could include:
- splashes during pouring
- splashes from mixing, diluting, and chemical reactions
- spills while carrying containers and from leaking containers
- vapors from open or leaking containers
Both acidic (pH < 4) and alkaline (pH >10) solutions are capable of inducing a chemical burn. The severity is dependent primarily upon the concentration of the chemical and the duration of contact.
With respect to the severity of chemical burns from acids and alkalis, burns from alkalis tend to be the more severe. An alkali in contact with human tissue may form an albuminate (clot or mass) and, with natural fats, forms soaps. Tissue is gelatinized to form soluble compounds resulting in deep and painful destruction.
Acids tend to harden the skin, and most of them produce pain at the site of contact. Thus, they often give a quicker warning of injury than do alkalis. First aid includes immediate irrigation with plain water for at least 15 minutes.
In addition, mists produced by corrosive liquids can result in lung damage if inhaled. Routine or accidental contact of corrosives with the skin or eyes can result in serious burns and irritation. Some acid mists, such as sulfuric, can corrode teeth over an extended period of time. Chromic acid is particularly dangerous and has been linked to lung and skin cancer.
Also Read: Hazardous Chemical Storage
How We Can Protect Ourselves—Evaluating the Workplace
Corrosive substances that present potential problems should be studied in detail to determine the nature and seriousness of the problems they present. A large part of this evaluation should consist of air sampling conducted by an industrial hygienist or a person trained in air sampling techniques. The possibility of exposing employees to corrosives should be evaluated to determine the need for controls and personal protective equipment.
Acids commonly found in industries include:
- Acetic
- Chromic
- Formic
- Hydrochloric Acid
- Nitric
- oxalic
- Perchloric
- picric
- Phosphoric
- sulfuric
Industrial processes that use acids include:
- metal cleaning, pickling, and etching
- electrolysis
- electroplating
- battery making
- paper making
- chemical syntheses
Alkalis commonly found in industries include:
- ammonium hydroxide
- barium hydroxide
- calcium chloride
- calcium oxide (quicklime)
- calcium sulfide
- potassium hydroxide
- sodium carbonate (soda ash)
- sodium hydroxide (lye or caustic soda)
- sodium sulfide
Tests and Training for Employees Who Work Near Corrosives
Recommended tests for employees exposed to corrosives include pulmonary function tests, particularly forced vital capacity (FVC) and forced expiratory volume for one second (FEV1) and their ratio (FEV1/FVC) on a scheduled basis.
Employees should be advised of the health hazards posed by the particular corrosives with which they work. They should be instructed in the proper procedures for handling, transporting, and storing corrosives.
Training in the use of personal protective equipment, the operation of engineering controls, and the location and proper use of eyewashes and safety showers should also be required.
Engineering and Administrative Controls
Engineering and administrative controls can be used to reduce employee exposure to corrosive mists or dust in the air and to lessen the hazard of direct contact with corrosives on the skin and eyes.

Engineering controls include:
- local exhaust ventilation (hoods or process enclosures)
- dilution ventilation
- a combination of the above
Administrative controls include:
- eliminating the use of a particular corrosive
- replacing one corrosive with a less toxic one
- instituting procedures to reduce accidents associated with the handling, transporting, and storing of corrosives
- limiting employees’ exposure time to vapors, mists, and dust
One example of administrative control is a precaution to be taken when acids and water are mixed. The acids should always be poured into the water, never the opposite. This lessens the danger of acid being splashed and of spattering from its contact with the water.
Figure 2 depicts apparatus designed for handling corrosive liquids.
also, Read: Hazardous Chemical Storage
Personal Protective Equipment
When engineering and administrative controls have failed to prevent or limit employees’ exposures, personal protective equipment should be used. Depending on the use of corrosives, the following types of equipment may be required:
- gloves and aprons for handling corrosive
- eye and face protection against splashes
- respirators for emergency or short-term use where high concentrations of corrosives are present in the air
- protective shoe coverings
Emergency Wash Facilities
Additionally, emergency wash, routine washing facilities, and overhead showers should be present in each department or work area where corrosives are used. The OSHA requirements for emergency eyewashes and showers, found at 29 CFR 1910.151(c), specify that “where the eyes or body of any person may be exposed to injurious corrosive materials, suitable facilities for quick drenching or flushing of the eyes and body shall be provided within the work area for immediate emergency use.”
While not having the force of a regulation under the OSH Act, the current ANSI standard addressing emergency eye-wash and shower equipment (ANSI/ISEA Z358.1-2009) provides guidance for suitable eyewash and shower equipment. ANSI’s standard also provides detail with respect to the location, installation, nature, and maintenance of eyewash and shower equipment.
Employers may also reference other recognized medical, technical, and industrial hygiene sources when determining whether the eyewash or shower facilities are suitable given the circumstances of a particular worksite.
Table 2 summarizes the requirements for eyewash and safety showers in accordance with the standards of the American National Standards Institute (ANSI/ISEA Z358.1-2009).
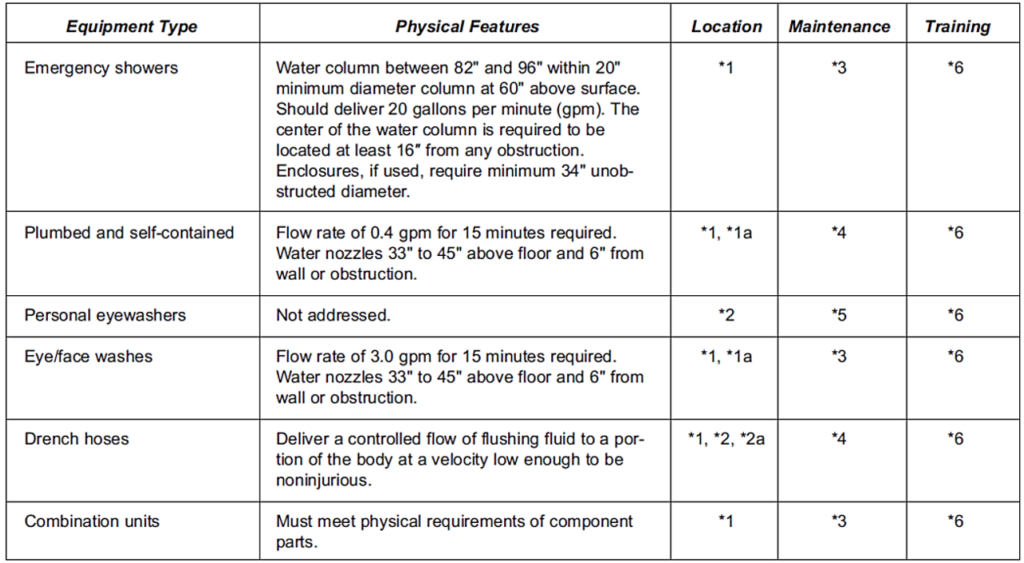
*(1) Accessible within 10 seconds, located on the same level as a hazard, and path of travel free from obstructions.
*(1a) For strong acids or strong caustics, located immediately adjacent to the hazard.
*(2) Not specified but recommended to be placed in the vicinity of potentially hazardous area.
*(2a) A drench hose may be considered an eyewash or eye/face wash if the device meets the performance requirements of Section 5 and/or Section 6.
*(3) Activated weekly to flush lines and verify operation.
*(4) Plumbed units activated weekly to flush lines and verify operation; self-contained units in accordance with manufacturer’s instructions.
*(5) Inspected and maintained in accordance with manufacturers’ instructions.
*(6) Required for all employees who might be exposed to a chemical splash.
Figure 3 provides examples of personal protective equipment, emergency wash facilities, emergency alerting equipment, and fire suppression equipment

Personal Protective Equipment and Facilities Checklist
In the checklist below, each item should be answered “yes.” Are protective measures in place that:
- Prevent skin, eye, and mucous membrane contact?
- Provide personal protective equipment for body, feet, head, hand/arm, and eye/face where needed?
- Provide properly maintained eyewash/safety showers for emergency use?
- Ensure that workers are adequately informed and trained as to precautions and controls?
- Provide and require the use of personal hygiene facilities at the conclusion of the work shift, prior to breaks and meals?
- Maintain corrosives in closed systems where possible?
- Ensure the avoidance of contact between corrosives and other incompatible substances?
- Provide for labeling on all containers as to their content?
- Provide ventilation, especially if corrosive gases or dusts are present?
- Provide fire preventive and protective measures if contact with corrosives causes a fire risk?
- Determine what risks from corrosives might be generated from normal and abnormal circumstances before a new process is introduced?
- Ensure that acids are stored in fire-resistant buildings with acid-resistant floors?
- Provide storage areas with secondary containment and proper drainage?
- Provide acid-resistant electrical installations in storage areas?
- Protect glass and plastic containers against impact?
- Ensure that all containers are stored off the floor, to facilitate flushing?
- Require dispensing from larger containers with carboy tilters and/or pumps?
Also Read Process Safety Management (PSM) Compliance checklist
For more safety Resources Please Visit Safetybagresources