Free Guidelines for Working with Electricity-Ground Fault Circuit Protection
20 min readElectrical hazards represent a serious, widespread occupational danger; practically all members of the workforce are exposed to electrical energy during the performance of their daily duties, and electrocutions occur to workers in various job categories. Many workers are unaware of the potential electrical hazards present in their work environment, which makes them more vulnerable to the danger of electrocution. According to the National Electrical Code, a “ground fault” is a conducting connection (whether intentional or accidental) between any electric conductor and any conducting material that is grounded or that may become grounded. Electricity always wants to find a path to the ground. In a ground fault, electricity has found a path to the ground, but it is a path the electricity was never intended to be on, such as through a person’s body. Because of this potential for shock, GFCI protection is used to protect human life. in this article you will be familiar with ground fault circuit protection devices and hot dose it works.
Also Read: E-Books: Working with Electricity Electrical Accidents Guide for Electrical Workers
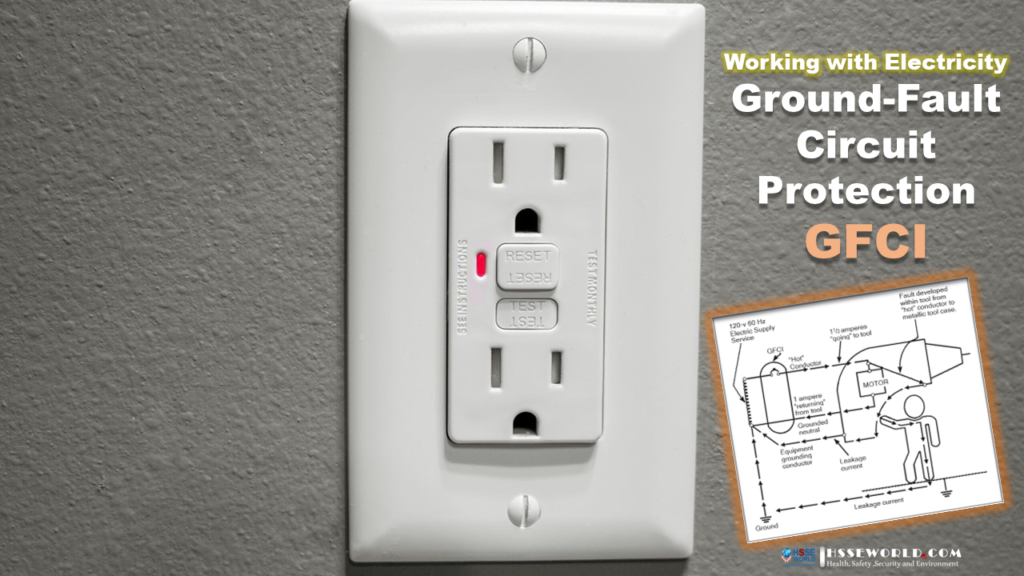
Circuit Protection Devices
Circuit protection devices are designed to automatically limit or shut off the flow of electricity in the event of a ground fault, overload, or short circuit in the wiring system. Fuses, circuit breakers, and ground-fault circuit interrupters are three well-known examples of such devices.
Fuses and circuit breakers are over-current devices that are placed in circuits to monitor the amount of current that the circuit will carry. They automatically open or break the circuit when the amount of current flow becomes excessive and therefore unsafe. Fuses are designed to melt when too much current flows through them. Circuit breakers, on the other hand, are designed to trip open the circuit by electromechanical means. Fuses and circuit breakers are intended primarily for the protection of conductors and equipment. They prevent overheating of wires and components that might otherwise create hazards for operators. They also open the circuit under certain hazardous ground-fault conditions.
The ground fault circuit interrupter, or GFCI, is designed to shut off electric power within as little as one-fortieth of a second. It works by comparing the amount of current going to electric equipment against the amount of current returning from the equipment along the circuit conductors. If the current difference exceeds 6 milliamperes, the GFCI interrupts the current quickly enough to prevent electrocution. The GFCI is used in high-risk areas such as wet locations and construction sites.
Also Read: Photo of the day: Arc-Fault Circuit Interrupters (AFCI)
The GFCI contains a special sensor that monitors the strength of the magnetic field around each wire in the circuit when current is flowing. The magnetic field around a wire is directly proportional to the amount of current flow, thus the circuitry can accurately translate the magnetic information into the current flow.
If the current flowing in the black (ungrounded) wire is within 5 (± 1) milliamperes of the current flowing in the white (grounded) wire at any given instant, the circuitry considers the situation normal. All the current is flowing in the normal path. If, however, the current flow in the two wires differs by more than 5 milliamperes, the GFCI will quickly open the circuit. This is illustrated in Figure 1.


How the GFCI Protects People
(By Opening the Circuit When Current Flows Through a Ground-Fault Path)
Note: the GFCI will open the circuit if 5 milliamperes or more of current returns to the service entrance by any path other than the intended white (grounded) conductor. If the equipment grounding conductor is properly installed and maintained, this will happen as soon as the faulty tool is plugged in. If by chance this grounding conductor is not intact and of the low impedance, the GFCI may not trip out until a person provides a path. In this case, the person will receive a shock, but the GFCI should trip out so quickly that the shock will not be harmful.
Safe Work Practices
Employees and others working with electric equipment need to use safe work practices. These include de-energizing electric equipment before inspecting or making repairs, using electric tools that are in good repair, using good judgment when working near energized lines, and using appropriate protective equipment. Electrical safety-related work practice requirements are contained in Subpart S of 29 CFR Part 1910, in sections 1910.331–1910.335.
Training
To ensure that they use safe work practices, employees must be aware of the electrical hazards to which they will be exposed. Employees must be trained in safety-related work practices as well as any other procedures necessary for safety from electrical hazards.
REad: E-Books: Electrical Safety of Low Voltage Systems
Polarity of Connections
- No grounded conductor may be attached to any terminal or lead so as to reverse designated polarity.
- A grounding terminal or grounding-type device on a receptacle, cord connector, or attachment plug may not be used for purposes other than grounding.
The above two subparagraphs dealing with the polarity of connections and the use of grounding terminals and devices address one potentially dangerous aspect of alternating current: many pieces of equipment will operate properly even though the supply wires are not connected in the order designated by design or the manufacturer. Improper connection of these conductors is most prevalent on the smaller branch circuit typically associated with standard 120-volt receptacle outlets, lighting fixtures, and cord- and plug-connected equipment. When plugs, receptacles, and connectors are used in an electrical branch circuit, the correct polarity between the ungrounded (hot) conductor, the grounded (neutral) conductor and the grounding conductor must be maintained. Reversed polarity is a condition when the identified circuit conductor (the grounded conductor or neutral) is incorrectly connected to the ungrounded or hot terminal of a plug, receptacle or another type of connector. Correct polarity is achieved when the grounded conductor is connected to the corresponding grounded terminal and the ungrounded conductor is connected to the corresponding ungrounded terminal. The reverse of the designated polarity is prohibited. Figure 5 illustrates a duplex receptacle correctly wired. Terminals are designated and identified to avoid confusion. An easy way to remember the correct polarity is “white to light”—the white (grounded) wire should be connected to the light or nickel-colored terminal; “black to brass”—the black or multi-colored (ungrounded) wire should be connected to the brass terminal; and “green to green”—the green or bare (grounding) wire should be connected to the green hexagonal head terminal screw


Duplex Receptacle Correctly Wired to Designated Terminals
Deenergizing Electrical Equipment. The accidental or unexpected sudden starting of electrical equipment can cause severe injury or death. Before any inspections or repairs are made—even on low-voltage circuits—the current must be turned off at the switch box and the switch padlocked in the “off” position. At the same time, the switch or controls of the machine or other equipment being locked out of service must be securely tagged to show which equipment or circuits are being worked on.
Maintenance employees should be qualified electricians who have been well-instructed in lockout procedures. No two locks should be alike; each key should fit only one lock, and only one key should be issued to each maintenance employee. If more than one employee is repairing a piece of equipment, each should lock out the switch with his or her own lock and never permit anyone else to remove it. The maintenance worker should at all times be certain that he or she is not exposing other employees to danger.
Overhead Lines
If work is to be performed near overhead power lines, the lines must be de-energized and grounded by the owner or operator of the lines, or other protective measures must be provided before work is started. Protective measures (such as guarding or insulating the lines) must be designed to prevent employees from contacting the lines.
Unqualified employees and mechanical equipment must stay at least 10 feet (3.05 meters) away from overhead power lines. If the voltage is more than 50,000 volts, the clearance must be increased by 4 inches (10 centimeters) for each additional 10,000 volts.
When mechanical equipment is being operated near overhead lines, employees standing on the ground may not contact the equipment unless it is located so that the required clearance cannot be violated even at the maximum reach of the equipment.
Protective Equipment. Employees whose occupations require them to work directly with electricity must use the personal protective equipment required for the jobs they perform. This equipment may consist of rubber-insulating gloves, hoods, sleeves, matting, blankets, line hoses, and industrial protective helmets.
Tools. To maximize his or her own safety, an employee should always use tools that work properly. Tools must be inspected before use, and those found questionable, removed from service, and properly tagged. Tools and other equipment should be regularly maintained. Inadequate maintenance can cause equipment to deteriorate, resulting in an unsafe conditions. Tools that are used by employees to handle energized conductors must be designed and constructed to withstand the voltages and stresses to which they are exposed.
Good Judgment. Perhaps the single most successful defense against electrical accidents is the continuous exercising of good judgment or common sense. All employees should be thoroughly familiar with the safety procedures for their particular jobs. When work is performed on electrical equipment, for example, some basic procedures are:
- Have the equipment de-energized.
- Ensure that the equipment remains de-energized by using some type of lockout and tag procedure.
- Use insulating protective equipment.
- Keep a safe distance from energized parts.
Protection is generally available as a GFCI/circuit breaker or GFCI receptacle. The breaker has a ground fault-sensing circuit breaker body. The same breaker or interrupting mechanism is used for both ground faults and overloads. GFCI receptacles are located at the point of use; the receptacle opens the circuit.
Also, Read: Photo of the day: Overhead powerline safety
Insulation and Grounding Deficiencies
Insulation and grounding are two recognized means of preventing injury during electrical equipment operation.
Conductor insulation may be provided by placing nonconductive material such as plastic around the conductor. Grounding may be achieved through the use of a direct connection to a known ground such as a metal cold water pipe.
Consider, for example, the metal housing or enclosure around a motor or the metal box in which electrical switches, circuit breakers, and controls are placed. Such enclosures protect the equipment from dirt and moisture and prevent accidental contact with exposed wiring; however, there is a hazard associated with housings and enclosures. A malfunction within the equipment—such as deteriorated insulation—may create an electric shock hazard. Many metal enclosures are connected to the ground to eliminate the hazard. If an energized wire contacts a grounded enclosure, a ground fault results, which normally will trip a circuit breaker, blow a fuse or trip a GFCI. Metal enclosures and containers are usually ground- ed by connecting them with a wire going to the ground. This wire is called an equipment grounding conductor. Most portable electric tools and appliances are grounded by this means. There is one disadvantage to grounding: a break in the grounding system may occur without the user’s knowledge, thus producing an unsuspected hazard.
Insulation may be damaged by hard usage on the job or by aging. If this damage causes the conductors to become exposed, the hazards of shocks, burns, and fire will exist. Double insulation may be used as additional protection on the live parts of a tool, but double insulation does not provide protection against defective cords and plugs or against heavy moisture conditions.
The use of a ground-fault circuit interrupter is one method used to overcome grounding and insulation deficiencies.
GFCI Operation Principle
In most cases, insulation and grounding are used to prevent injury from electrical wiring systems or equipment. However, there are instances when these recognized methods do not provide the degree of protection required. To help appreciate this, let’s consider a few examples of where ground fault circuit interrupters would provide additional protection.
Many portable hand tools, such as electric drills, are now manufactured with non-metallic cases. If approved, we refer to such tools as double insulated. Although this design method assists in reducing the risk of grounding deficiencies, a shock hazard can still exist. In many cases, people must use such electrical equipment where there is considerable moisture or wetness. Although the person is insulated from the electrical wiring and components, there is still the possibility that water can enter the tool housing. Ordinary water is a conductor of electricity. Therefore, if the water contacts energized parts, a path will be provided from inside the housing to the outside, bypassing the double insulation. When a person holding a hand tool under these conditions touches another conductive surface in the work environment, an electric shock will result.
Double-insulated equipment or equipment with nonmetallic housings that do not require grounding under the National Electrical Code is frequently used around sinks or in situations where the equipment could be dropped into water. Frequently, the initial human response is to grab the equipment. If a person’s hand is placed in the water and another portion of their body is in contact with a conductive surface, a serious or deadly electric shock can occur.
In construction work and regular factory maintenance work, it is frequently necessary to use extension cord sets with portable equipment. These cords are regularly exposed to physical damage. Although safe work procedures require adequate protection, it is not possible to prevent all damage. Frequently, the damage is only to the insulation, exposing energized conductors. It is not unusual for a person to handle the cord often with the possibility of contacting the exposed wires while holding a metal case tool or while in contact with other conductive surfaces. The amount of current which flows under such conditions will be enough to cause serious human response. This can result in falls or other physical injuries and in many cases death.
Since neither insulation (double insulation) nor grounding can provide protection under these conditions, it is necessary to use other protective measures. One acceptable method is a ground-fault circuit interrupter, commonly referred to as a GFCI. See Figure 3.


Ground-Fault Circuit Interrupter
GFCI monitors the difference in current flowing into the energized and out to the grounded neutral conductors. The difference (1/2 ampere in this case) will flow back through any available path, such as the equipment grounding conductor, and through a person holding the tool if the person is in contact with a grounded object.
Many employees are not fully aware of the hazards involved in using electric tools. Employees have received shocks from the equipment they were using, but continued using them and were subsequently electrocuted. The majority of such electrocutions are caused by a malfunction of a part of the equipment grounding conductor. Frequently, for example, a defect in the grounding conductor, such as a break, allows it to come into direct contact with the ungrounded conductor. An equipment grounding conductor alone cannot provide complete protection under all circumstances. If a fault current of about three or four times the rating of the circuit breaker occurs during the use of the tool, sufficient fault current may flow through the person holding the tool and cause electrocution before the circuit breaker could open.
Most fatal fault currents through people will never trip the circuit breakers. As noted earlier, double digit milliamps kill people; however, a circuit panel circuit breaker will not trip until its rated value is exceeded. People can never rely on circuit breakers to protect them from electrocution. Standard circuit breakers are only for equipment and fire protection.
Since grounding conductors are, in many cases, not adequately maintained, equipment grounding regulations alone are
inadequate to provide the necessary protection. Accordingly, there is a need to supplement the existing equipment grounding conductor requirements to protect employees from ground fault accidents resulting in injuries and fatalities.
The GFCI will not protect the employee from line-to-line contact hazards (such as a person holding two energized wires or an energized and a neutral wire in each hand). It does provide protection against the most common form of electrical shock hazard—the ground fault. It also provides protection against fires, overheating, and destruction of insulation on wiring.
Flexible Electrical Cords—Another Reason for Added Protection
With the wide use of portable tools, the use of flexible cords often becomes necessary. Hazards are created when cords, cord connectors, receptacles, and cord- and plug-connected equipment are improperly used and maintained or are used in a hazardous environment (such as around water).
Generally, flexible cords are more vulnerable to damage than is fixed wiring. Flexible cords must be so connected to devices and to fittings to prevent tension at joints and terminal screws. Because a cord is exposed, flexible and unsecured, joints and terminals become more vulnerable. Flexible cord conductors are finely stranded for flexibility, but the strands of one conductor may loosen from under terminal screws and touch another conductor, especially if the cord is subjected to stress or strain.
A flexible cord may be damaged by normal activities, by the door or window edges, by staples or fastenings, by abrasion from adjacent materials, by high temperature, or by aging. If the electrical conductors become exposed, there is a danger of shocks, burns, or fire.
When a cord connector is wet, hazardous leakage can occur to the equipment grounding conductor and to humans who pick up that connector if they also provide a path to the ground. Such leakage is not limited to the face of the connector but also develops at any wetted portion of it.
When the leakage current of tools is below 1 ampere and the grounding conductor has a low resistance, no shock should be perceived. Should the resistance of the equipment grounding conductor increase, the current through the body will also increase; thus, if the resistance of the equipment grounding conductor is significantly greater than 1 ohm, tools with even small leakages become hazardous.
GFCIs can be used successfully to reduce electrical hazards on construction sites. Tripping of GFCIs—interruption of current flow—is sometimes caused by wet connectors and tools. It is good practice to limit the exposure of connectors and tools to excessive moisture by using watertight or sealable connectors. Providing more GFCIs or shorter circuits can prevent tripping caused by cumulative leakage from several tools or by leakages from extremely long circuits.
Discussion of the OSHA Standard
Following is a discussion of the major aspects of OSHA standard 29 CFR 1926.404(b)(1) for GFCIs. Employers are required by the standard to use either ground-fault circuit interrupters as specified in paragraph (b)(1)(ii) or an assured equipment grounding conductor program as specified in paragraph (b)(1)(iii), to protect employees on construction sites. These requirements are in addition to any other requirements for equipment grounding conductors. Each method is dis- cussed separately.
Ground-Fault Circuit Interrupters
The employer must provide GFCI protection for all 120-volt, 15- and 20-ampere, single-phase receptacles on construction sites that are not a part of the permanent wiring of the building or structure and which are in use by employees. As noted, this protection is required in addition to, not in lieu of, the equipment grounding conductor requirements of 29 CFR 1926.
The GFCIs used must be approved, as that term is defined by OSHA. Various types of approved GFCIs suitable for use on construction sites are available, including circuit-breaker, receptacle, and portable types. Most of today’s approved GFCIs have trip levels of 5 milliamperes ± 1 milliampere. Portable GFCIs are acceptable if they are connected to the receptacle outlet in use.
On generators where the supply wires are not required to be grounded and are in fact not grounded, the return path for a ground-fault current to flow is not completed, and the hazard that a GFCI would protect against is not present.
Consequently, the rule does not require the use of GFCIs on portable or vehicle-mounted generators of 5 kilowatts capacity or less if the output is a two-wire, single-phase system and their circuit conductors are insulated from the generator
frame and all other grounded surfaces. It should be noted that receptacles on all small portable generators are not exempt from the GFCI requirements. The standard clearly states that receptacles on such generators must have the circuit conductors insulated from the generator frames and all grounded surfaces to be exempt.
Assured Equipment Grounding Conductor Program
If the employer selects this option, the employer must provide an assured equipment grounding conductor program covering all cord sets, receptacles that are not a part of the permanent wiring of the building or structure, and equipment connected by cord and plug that is available for use by employees. Though it is not required to be posted, a written procedure for the program must be kept at the job site and made available to the Occupational Safety and Health Division and any affected employee.
The employer must designate one or more competent people to implement the program. A competent person is defined in 29 CFR 1926.32(f) as one who is capable of identifying existing and predictable hazards in the surroundings or working conditions that are unsanitary, hazardous or dangerous to employees, and who has the authorization to take prompt corrective measures to eliminate them. This person may be the employer, an employee of the employer, or another person.
Inspections
Equipment, except cord sets and receptacles that are fixed and not exposed to damage, must be inspected for visible damage or defects before each day’s use. Examples of possible damage would be deformed or missing pins, insulation damage, or indications of possible internal damage. Any equipment found to be damaged or defective may not be made available for use or used by employees.
Periodic Tests
Two tests are required to be performed to ensure the safe condition of the equipment grounding conductor. The first test is a continuity test—the equipment grounding conductor must be electrically continuous. This test is required to be performed on all cord sets, receptacles that are not a part of the permanent wiring of the building or structure, and cord- and plug-connected equipment that is required to be grounded. It may be performed by an ohmmeter for cord sets and cord- and plug-connected equipment and by a receptacle tester for receptacles or by any other testing device that can ascertain electrical continuity.
In addition to the continuity test, a test must be performed on receptacles and attachment caps, and plugs to ascertain that the equipment grounding conductor is connected to its proper terminal. This test can be performed with the same equipment used to perform the first test.
Both of these tests are required to be performed: (1) before first use, (2) after any repairs, (3) after damage can be reasonably suspected to have occurred and (4) at three-month intervals. For cord sets and receptacles that are fixed and not exposed to damage that rough handling or abuse is most likely to cause, the testing frequency may be reduced to once every six months. The basis for the different testing intervals is that this latter type of equipment, once it is in place, is not subject to the same abuse, and the hazards thereby created, as equipment that is constantly moved around on construction sites. Cord sets that we would consider fixed would only be those which, once they are put in place, remain stationary and not those cord sets that are being constantly moved around on construction sites.
Recording of Testing
The testing must be recorded. To record the tests, color coding, logs, or other effective means may be used. The record must indicate which equipment passed the test and the date it was tested or the interval for which it was tested. Any equipment that fails to pass the required tests may not be made available for use by employees until the defect has been repaired and the equipment successfully retested.
The NEC also requires GFCI protection for residential bathrooms and outdoor receptacles, construction sites, and electrical equipment on swimming pools (and between 10 and 15 feet of pools and in underwater lighting). In addition, any other place where a hazardous condition might develop should have GFCI protection.
Specific Standard Requirements
All 120-volt, single-phase, 15- and 20-ampere receptacle outlets on construction sites that are not a part of the permanent wiring of the building or structure and which are in use by employees must have approved GFCIs for the protection of personnel. Receptacles on a two-wire, single-phase portable or vehicle-mounted generator rated not more than 5 kilowatts, where the circuit conductors of the generator are insulated from the generator frame and all other grounded surfaces, need
not be protected with ground fault circuit interrupters. The employer must establish and implement an assured equipment grounding conductor program on construction sites covering all cord sets, receptacles that are not a part of the permanent wiring of the building or structure, and equipment connected by cord and plug that is available for use or used by employees. This program must comply with the following minimum requirements:
- A written description of the program, including the specific procedures adopted by the employer, must be available at the job site for inspection and copying by OSHA and by any affected employee.
- The employer must designate one or more competent people (as defined by OSHA) to implement the program.
- Each cord set, attachment cap, plug and receptacle of cord sets, and any equipment connected by cord and plug, except cord sets and receptacles that are fixed and are not exposed to damage, must be visually inspected before each day’s use for external defects, such as deformed or missing pins or insulation damage, and for indication of possible internal damage. Equipment found damaged or defective may not be used until repaired.
- The following tests must be performed on all cord sets, receptacles that are not a part of the permanent wiring of the building or structure, and cord and plug-connected equipment required to be grounded:
- All equipment grounding conductors must be tested for continuity and must be electrically continuous.
- Each receptacle and attachment cap or plug must be tested for correct attachment of the equipment grounding conductor. The equipment grounding conductor must be connected to its proper terminal.
- All required tests must be performed:
- Before first useBefore equipment is returned to service following any repairsBefore equipment is used after any incident that can be reasonably suspected to have caused damage (for example, when a cord set is run over) and
- At intervals, not to exceed three months, except that cord sets and receptacles that are fixed and not exposed to damage must be tested at intervals not exceeding six months
- The employer may not make available or permit the use by employees of any equipment that has not met these requirements.
- Tests performed as required must be recorded. This test record must identify each receptacle, cord set, and cord- and plug-connected equipment that passed the test and must indicate the last date it was tested or the interval for which it was tested. This record must be kept by means of logs, color coding, or other effective means and must be maintained until replaced by a more current record. The record must be made available on the job site for inspection by the Occupational Safety and Health Division and by any affected employee.
Program Evaluation
In evaluating an assured equipment grounding conductor program method of ground-fault protection, at least the items listed below must be considered. All of these items are necessary for an effective assured equipment grounding conductor program, and the weakness or absence of any specific item may make the program ineffective and unacceptable.
- The program must cover all cord sets, receptacles (not part of permanent wiring), and cord- and plug-connected equipment available for use by the employees.
- There must be a written description of the program, including specific details, present at the job site. This program must represent what is actually being carried out.
- A competent person or people must be responsible for implementing the program. One person may have the overall responsibility for the program and the actual cord and equipment testing and recording for several sites, while other competent persons may conduct daily visual inspections and remove questionable or unsafe equipment from service on each individual site.
- A competent person must conduct visual inspections and carry out procedures intended to prevent the use of damaged or defective tools.
- Appropriate test equipment and procedures must be used in conducting the continuity tests and the wiring attachment evaluations of the equipment grounding conductors on cords, plugs, and temporary receptacles.
- Appropriate test intervals must be established in accordance with the provisions of the standards and additional tests must be made following suspected damage before returning repaired cords or equipment to service and before the first use of a new cord or tool.
- Effective procedures or policies must be instituted to prevent the use of untested cords and equipment on the site.
- An effective method of recordkeeping and identification of equipment and test intervals must be established. The methods may range from detailed records to a simple color coding system with the code being included in the written program.
Also Read: Electrical Risk Assessments
For more safety Resources Please Visit Safetybagresources