Eyewash and Emergency Shower Safety
10 min readSufficient and properly working emergency eyewash and shower devices in the workplace are vital for easing eye and skin injuries. However, this equipment is not a substitute for safety eyewear, face shields, protective clothing, or other personal protective gear designed to prevent employees’ exposure to chemical, physical, or biological agents.
According to the United States Bureau of Labor Statistics:
- 11,330 workers were afflicted by chemical exposures in 2019;
- 36,840 workers experienced exposure to harmful substances or environments, and 18,640 workers suffered eye injuries
In This article, you will learn the following :
- Types of emergency eyewash and shower equipment
- Maintaining flushing fluid standards
- Selecting the location and installing emergency wash equipment
- Treating eye injuries.
- Properly disposing of fluids.
- Chemical considerations
Also Read: A Guide to Eye Wash and Emergency Shower Stations
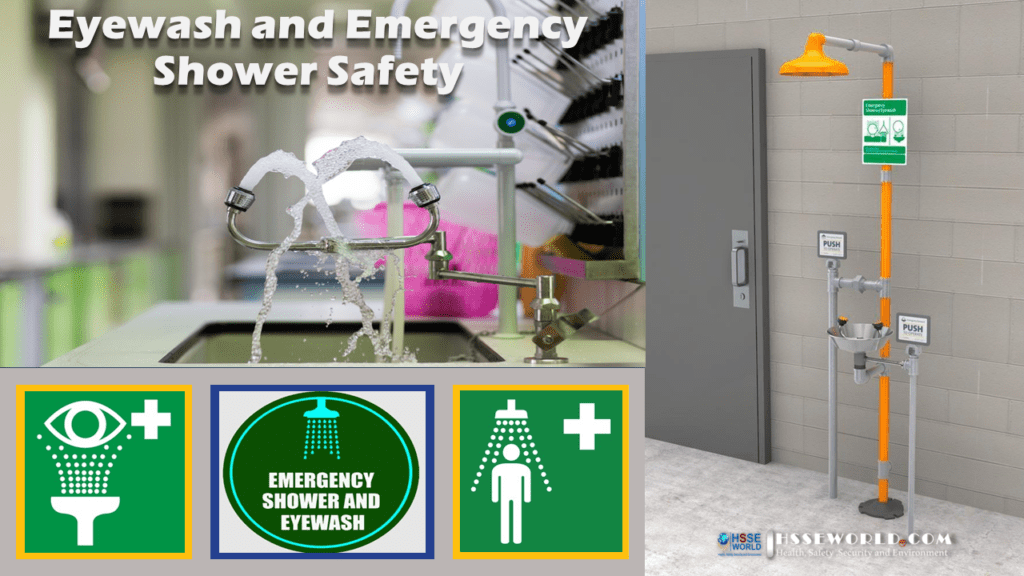
The Occupational Safety and Health Administration’s (OSHA) standard 29 CFR 1910.151(c) requires that employers provide quick-drenching emergency wash stations in areas where an employee may be exposed to harmful corrosive materials. The standard applies to human immunodeficiency virus and hepatitis B research laboratories or any workplace where splashing of solutions containing 0.1 percent or greater formaldehyde may occur.
While OSHA specifies where and when to use emergency wash stations, the American National Standards Institute (ANSI)/ International Safety Equipment Association (ISEA) explains how to use them. The ANSI/ISEA’s Z358.1 standard serves as a benchmark within the United States and internationally to help protect workers from eye injuries caused by caustic and corrosive substances.
The standard provides numerous eyewash guidelines, including:
- proper design of eyewash stations and showers;
- certification and testing procedures;
- performance and usage;
- maintenance of flushing equipment; and
- employee training.
Also Read: Emergency Eyewash Stations: What the Z358 Standard Means for Your Workplace
Types of Emergency Eyewash and Shower Equipment
The three primary types of first aid wash equipment include eyewash stations, eye/face wash equipment, and emergency showers.
Eyewash Stations
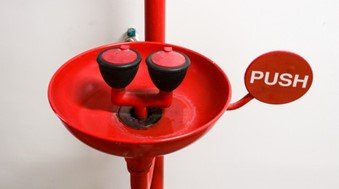
Eyewash stations are for splashes or spills where only the eyes are likely affected. Approved equipment must deliver at least 0.4 gallons per minute (GPM) of flushing fluid at 30 pounds per square inch (PSI) for 15 minutes.
The two primary types of emergency eyewash units that conform to OSHA and ANSI/ISEA standards are:
- Plumbed eyewash stations Plumbed eyewash stations permanently connect to and are designed to receive water or other flushing fluids from a remote source, such as the building’s plumbing or flushing fluid supply. Plumbed stations may be mounted to a fixed object, such as a wall or countertop, or a pipe stand referred to as a pedestal mount. Plumbed eyewashes may include a bowl that collects and directs fluid away from the eyewash user after use. To ensure that the flushing fluid flows freely and cleanly from a plumbed station, test the station once a week. Protect eyewash nozzles from airborne contaminants with an integrated cover. Plumbed eyewash stations may also include:
- Faucet-integrated or faucet- mounted eyewash stations -These eyewashes are found in many laboratories, clinics, and schools and attach to a sink’s faucet. This type of eyewash must comply with the ANSI/ ISEA standard of turning on within one second of activation.
- Portable stations Portable stations feature a self-contained tank of water or other fluid. They are practical in safety and rescue vehicles where no reliable plumbing or water source is available. They can also be permanently fixed in place. Types of portable eyewash stations include:
- Gravity-fed eye and face wash stations-These stations contain their own water or flushing fluid, which must be refilled after every use. The flushing fluid is pumped from a storage tank through drench nozzles and onto the eyes and face. These units may be temporarily installed on walls, tabletops, or other level surfaces. Follow the manufacturer’s instructions for checking fluid levels and cleanliness in the tank.
- Pressurized tank eyewash stations-These stations connect to drench nozzles or a hose. They are extra-portable and useful for immediate emergency operations in most environments. However, since they may not produce a strong or long enough shower to meet ANSI/ISEA standards, use them temporarily in emergencies before getting to a primary eyewash station.
- Personal eyewash units-These units are intended to supplement rather than replace ANSI/ISEA standard- compliant eyewashes. They are especially helpful as a first response before a person reaches the primary washing station or when a person is on the way to a medical facility. They are also helpful at outdoor worksites.
Also Read: Eye Protection’s 10 Key Facts
Eye/Face Wash Stations
Eye and face wash units are plumbed or self-contained devices designed to flush the operator’s eyes and face simultaneously by delivering a minimum of 3 GPM of fluid at 30 PSI for 15 minutes. Some eye/face wash equipment divides a central stream of flushing fluid into several smaller streams to provide a gentler rinse. Others use an aerated system to disperse the flushing fluid across the face to rinse off contaminants. Eye/face wash equipment may include:
- Hand-held drench hoses-These hoses, like showers, are supplemental devices connected to a water supply. They are used to irrigate the operator’s eyes, face, and sometimes, the body. To prevent contaminated water from entering a hose from a different source, employers should install a drench hose with a backflow preventer that meets local codes and ordinances.

Emergency Showers
Emergency showers are designed to deliver enough flushing fluid to cover the whole body. These devices require 20 GPM of flushing fluid at 30 PSI for 15 minutes. Most emergency showers include “modesty curtains” to encourage the affected person to remove contaminated clothing rapidly – a critical step after exposure to harmful materials.
Emergency showers may be mounted to a wall, floor, or ceiling. They may have a permanent plumbing connection to a source of flushing liquid or be self-contained, with flushing fluid that must be refilled or replaced after each use. Delivery of the flushing fluid may come from overhead, sides, or both, as long as the water pattern meets the following ANSI/ISEA minimum height, dimensional, and pressure requirements, including:
- delivery of a water pattern with a diameter of at least 20 to 60 inches;
- a minimum spray volume of 20 GPM for a minimum of 15 minutes;
- the ability to turn on in one second or less without requiring the operator to use the controls repeatedly to keep the shower on;
- hands-free operation;
- a shower head that is 82 to 96 inches from the floor; and
- an actuating valve or lever not more than 69 inches from the floor.
Maintaining Flushing Fluid Standards

Portable and plumbed stations that use tap water require more regular maintenance than portable, saline-solution stations. While flushing fluids can be any potable (drinking) water; preserved water; saline solution; or other medically acceptable solution, the ANSI Z358.1 recommends a preserved, buffered pH-balanced saline solution. As opposed to tap water, a saline solution is closer to human tears, causes less potential damage to delicate eye tissue, and decreases the buildup of contaminants, mildew, and sediment. It is critical to maintain the flushing fluid’s pH balance and to not allow bacterial growth.
ANSI/ISEA Z358.1 requires that plumbed flushing stations “be activated weekly for a period long enough to verify operation and ensure that flushing fluid is available.” It also states that portable equipment “be visually checked to determine if flushing fluid needs to be changed or supplemented.” Whether plumbed or portable, both types additionally need to be tested annually and maintained according to the manufacturer’s guidelines. A bacteriostatic additive can maintain this balance in self-contained eyewash units. In personal wash units, provide a sterile flushing fluid in a closed container that is only opened at the time of use.
To ensure eye and safety compliance, plumbed and portable wash units should be tested for the following:
• Flushing duration
Units should provide at least 15 minutes of hands-free flushing immediately and thoroughly after exposure, using an ample supply of clean fluid under low pressure. Longer times may be warranted for exposure to penetrating, corrosive materials.
• Fluid pressure
The fluid pressure must be at a velocity low enough not to injure the user: a minimum of 0.4 gallons (1.5 liters) per minute for eyewashes; 3 gallons (11.4 liters) per minute for eye or face washes; and 20 gallons (75.7 liters) per minute for showers. Closely regulate fluid pressure in eyewash stations to avoid damaging tender eye tissue.
• Fluid temperature
Eye, face, and shower wash stations should be kept tepid (60-100° F) to not damage eye or other body tissue. Plumbed units may need to be disconnected from the hot water pipe to keep the fluid from reaching extreme temperatures. Tepid fluid increases the chances that a victim can tolerate the required 15-minute wash. In some cases, warm water may compound a chemical reaction. Consult a professional about the optimum water temperature for a specific application.
Selecting the location and Installing Emergency Wash Equipment
choosing the right location for emergency wash stations is critical for increasing the affected person’s chances of a full recovery. The ANSI/ISEA standard requires placement of emergency wash stations within 10 seconds (about 55 feet) from the hazard.
The ANSI/ISEA standard also requires that wash areas remain on the same level as the hazard in a well-lit area marked as an emergency eyewash station. Also, avoid any location around corners, through closed doors, beyond a partition, or otherwise physically separated from the work environment. If strong caustics, acids, or any highly corrosive chemicals are used, install emergency eyewash stations adjacent to the hazard.
Follow these additional guidelines for emergency washing stations:
- Keep the path to the station unobstructed. An obstacle-free path is crucial since the vision of an injured worker is impaired. (The 2014 ANSI/ ISEA standard clarifies that a single step up into an enclosure where the wash is accessed is not considered an obstruction.)
- Install equipment near an emergency exit, so emergency-response personnel can more easily reach an exposed employee.
- Do not install emergency wash stations near electrical equipment.
- Install the equipment in a hazard-free area near a drainage system to prevent further contamination and excess water accumulation.
- Protect plumbed units from freezing by placing the unit on a wall adjoining a heated space, using electrical heat tracing, or other methods. Protect flushing fluid from freezing in self- contained eyewash units in cold environments by covering the units with heated blankets.
- Install equipment according to the manufacturer’s instructions.
- Install sinks or face washes 33 to 53 inches from the floor (measuring from the floor to the water flow0.
- Select eyewash equipment that can deliver fluid to both eyes at the same time.
- Install emergency equipment that can be operated hands-free.
- Install signage so a person can easily identify the washing equipment.
- Ensure the area surrounding the equipment is well-lighted.
- Install emergency showers so that the actuator handle is easily visible and reachable, about 5 feet from the ground. (In drench hose units or eyewashes, the actuator is usually built into the unit and can be installed facing outward for immediate use.)
- Mount the equipment at least 6 inches from the wall or obstructions.
- Install nozzle caps to keep foreign matter from accumulating in the nozzle area. Ensure that nozzle caps automatically separate from nozzles when users activate the equipment.
- Install equipment so it will activate in one second or less and so that the valve remains open without the operator having to use his or her hands to continue activating the equipment.
- Install equipment so that neither the pressure nor temperature of the delivered fluid will harm affected body parts. Install temperature control valves. Consider that the initial temperature of the flushing water will be the temperature of the piping system. Recirculation systems will keep the water temperature in the required range.
- Ensure that units deliver a sufficient spray pattern.
- Select corrosion-resistant eyewash and shower equipment and valves. Make sure your equipment and supply system piping parts and materials are compatible. If the equipment is not corrosion-resistant, paint or coat the equipment to withstand exposure to airborne contaminants.
- Inspect equipment every year and keep a record of all inspections and maintenance.
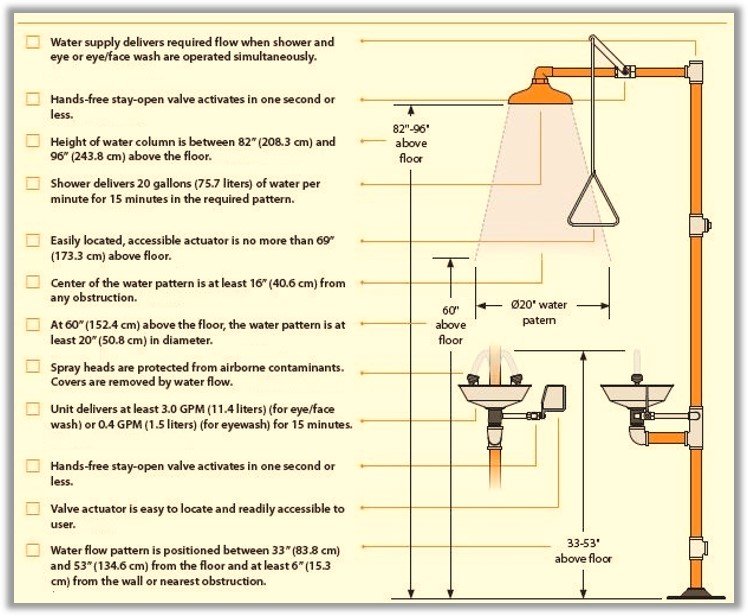
Treating Eye Injuries

When an eye injury occurs, have an ophthalmologist (eye physician and surgeon) or another medical doctor examine the eye as soon as possible. Although the injury may not look or feel serious, it could seriously damage the eyes. If an employee experiences blurred vision, partial loss of vision, double vision, or sharp pain in the eye after an incident, take the victim to an emergency room immediately and consult an ophthalmologist.
Properly Disposing of Fluids
Properly dispose of wastewater.
- Ensure that it does not pool or freeze where someone might slip.
- Do not allow it to enter a wastewater treatment system if the flushing fluid contains hazardous materials. In such cases, connect drain piping from the unit’s acid waste disposal system or a neutralizing tank. Never use neutralizing agents on the eyes or skin.
Chemical Considerations
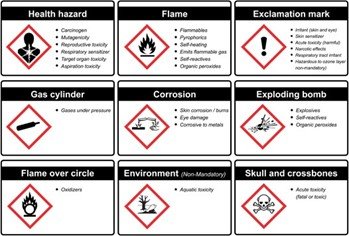
Some chemicals violently react when mixed with other substances and may endanger the handler or other people in the area. Conduct a job hazard analysis to decide which emergency equipment is needed. Keep a list of all hazardous substances at each job site and make safety data sheets readily available for each hazardous on-site chemical (as required by OSHA’s Hazard Communication Standard 29 CFR 1910.1200). With the help of a trained medical professional, establish first-aid procedures for chemical injuries and regularly review and update the procedures.
Also read:
Please visit our Safety Resources SAFETY BAG to have many Safety Resources
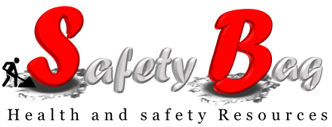