Controlling Hazardous Fume and Gases during Welding.
Welding fumes are a complex mixture of metallic oxides, silicates, and fluorides. Fumes are formed when a metal is heated above its boiling point and its vapors condense into very fine, particles (solid particulates). Welding fumes generally contain particles from the electrode and the material being welded.

Can the composition of welding fumes vary?
Yes, welding fumes contain oxides of the metals in the material being welded.
- Fluxes containing silica or fluoride produce amorphous silica, metallic silicates, and fluoride fumes.
- Fumes from mild steel welding contain mostly iron with small amounts of additive metals (chromium, nickel, manganese, molybdenum, vanadium, titanium, cobalt, copper, etc.).
- Stainless steels have larger amounts of chromium or nickel in the fume and lesser amounts of iron.
- Nickel alloys have much more nickel in the fume and very little iron.
How do coatings change the composition of welding fumes?
Vapors or fumes can come from coatings and residues on the metal being welded. Some ingredients in coatings can have toxic effects. These ingredients include:
- metalworking fluids, oils, and rust inhibitors
- zinc on galvanized steel (vaporizes to produce zinc oxide fume)
- cadmium plating
- vapors from paints and solvents
- lead oxide primer paints
- some plastic coatings
- Metal Coatings – A Source of Hazardous Fumes
How do I remove the coatings?
- Remove coatings from the weld area to minimize the fume. The removal of the coating will also improve weld quality.
- Use stripping products to remove coatings. Make sure to remove any residues before welding.
- Use wet slurry vacuum removal techniques for removing very toxic coatings.
- Do not grind coatings. Grinding dust may be toxic.
What are the factors that affect worker exposure to welding fumes?
- Type of welding process.
- Composition of welding rod.
- Filler metals and the base metal used.
- Type of coatings present.
- Location (an open area or confined space).
- Type of ventilation controls (mechanical or local).
- Work practices of the welder (e.g. remove coatings, clean surfaces, stay upwind when welding in open or outdoor).
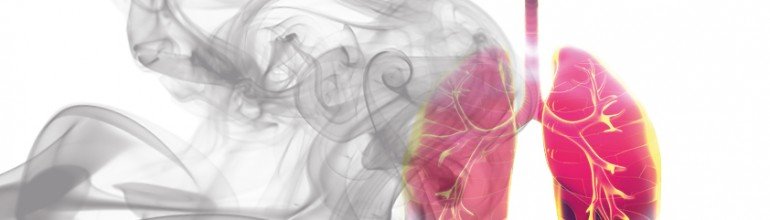
What are the welding gases?
Welding gases are gases used or produced during welding and cutting processes like shielding gases or gases produced by the decomposition of fluxes or from the interaction of ultraviolet light or high temperatures with gases or vapors in the air.
What are the examples of welding gases?
Gases used in welding and cutting processes include:
- shielding gases such as carbon dioxide, argon, helium, etc.
- fuel gases such as acetylene, propane, butane, etc.
- oxygen, used with fuel gases and also in small amounts in some shielding gas mixtures
Gases produced from welding and cutting processes include:
- carbon dioxide from the decomposition of fluxes
- carbon monoxide from the breakdown of carbon dioxide shielding gas in arc welding.
- ozone from the interaction of electric arc with atmospheric oxygen
- nitrogen oxides from the heating of atmospheric oxygen and nitrogen
- hydrogen chloride and phosgene produced by the reaction between ultraviolet light and the vapors from chlorinated hydrocarbon degreasing solvents (e.g., trichloroethylene, TCE).
(Learn More about: Welding gases & fumes Exposure)
Gases are also produced from the thermal breakdown of coatings:
- Polyurethane coatings can produce hydrogen cyanide, formaldehyde, carbon dioxide, carbon monoxide, oxides of nitrogen, and isocyanate vapors.
- Epoxy coatings can produce carbon dioxide and carbon monoxide.
- Vinyl paints can produce hydrogen chloride.
- Phosphate rust-inhibiting paints can release phosphine during welding processes.
- Minimizing exposure to degreasing solvent vapors.
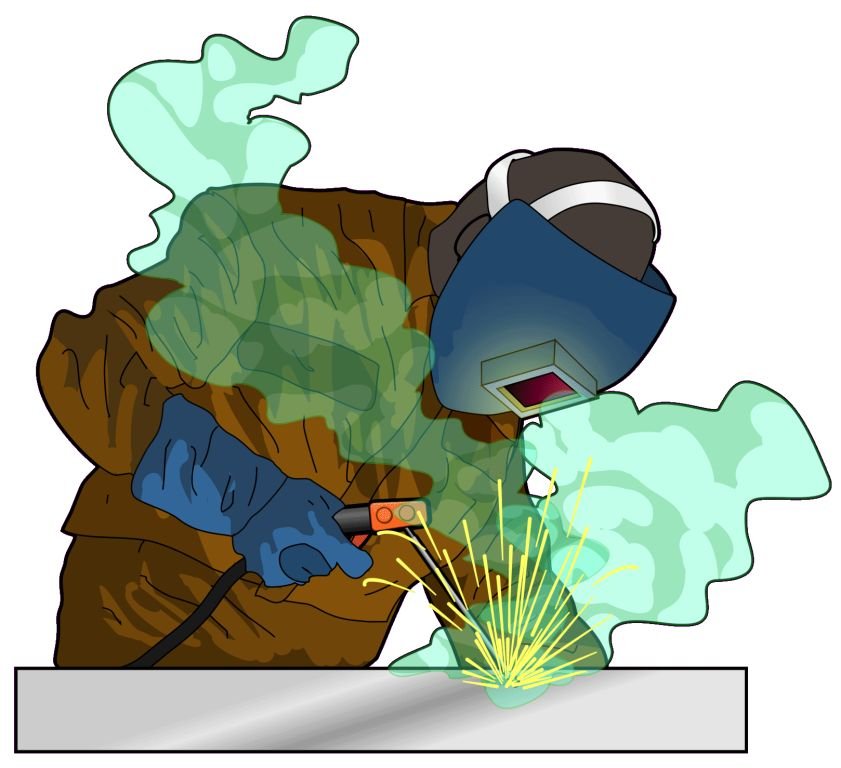
How can I prevent exposure to welding gases?
It is important to follow the manufacturer’s instructions, safety data sheets (SDSs), and safety protocols to minimize the hazards of welding gases.
- Use substitute materials such as water-based cleaners or high flash point solvents.
- Cover the degreaser baths or containers.
- Do not weld on surfaces that are still wet with a degreasing solvent.
- Do not weld near degreasing baths.
- Do not use chlorinated hydrocarbon degreasers.
- Have adequate ventilation in a workplace to prevent the displacement or enrichment of oxygen and to prevent the accumulation of flammable atmospheres.
- Use local exhaust ventilation systems to remove fume and gases from the welder’s breathing zone.
- Wear appropriate respiratory protective equipment. Respiratory protective equipment should not be used to replace the use of mechanical ventilation.
- Welders should understand the hazards of the materials they are working with. OSHA’s Hazard Communication Standard requires employers to provide information and training for workers on hazardous materials in the workplace.
- Welding surfaces should be cleaned of any coating that could potentially create toxic exposure, such as solvent residue and paint.
- Workers should position themselves to avoid breathing welding fume and gases. For example, workers should stay upwind when welding in open or outdoor environments.
- General ventilation, the natural or forced movement of fresh air, can reduce fume and gas levels in the work area. Welding outdoors or in open workspaces does not guarantee adequate ventilation. In work areas without ventilation and exhaust systems, welders should use natural drafts along with proper positioning to keep fume and gases away from themselves and other workers.
- Local exhaust ventilation systems can be used to remove fume and gases from the welder’s breathing zone. Keep fume hoods, fume extractor guns and vacuum nozzles close to the plume source to remove the maximum amount of fume and gases. Portable or flexible exhaust systems can be positioned so that fume and gases are drawn away from the welder. Keep exhaust ports away from other workers.
- Consider substituting a lower fume-generating or less toxic welding type or consumable.
- Do not weld in confined spaces without ventilation. Refer to applicable OSHA regulations (see list below).
- Respiratory protection may be required if work practices and ventilation do not reduce exposures to safe levels.
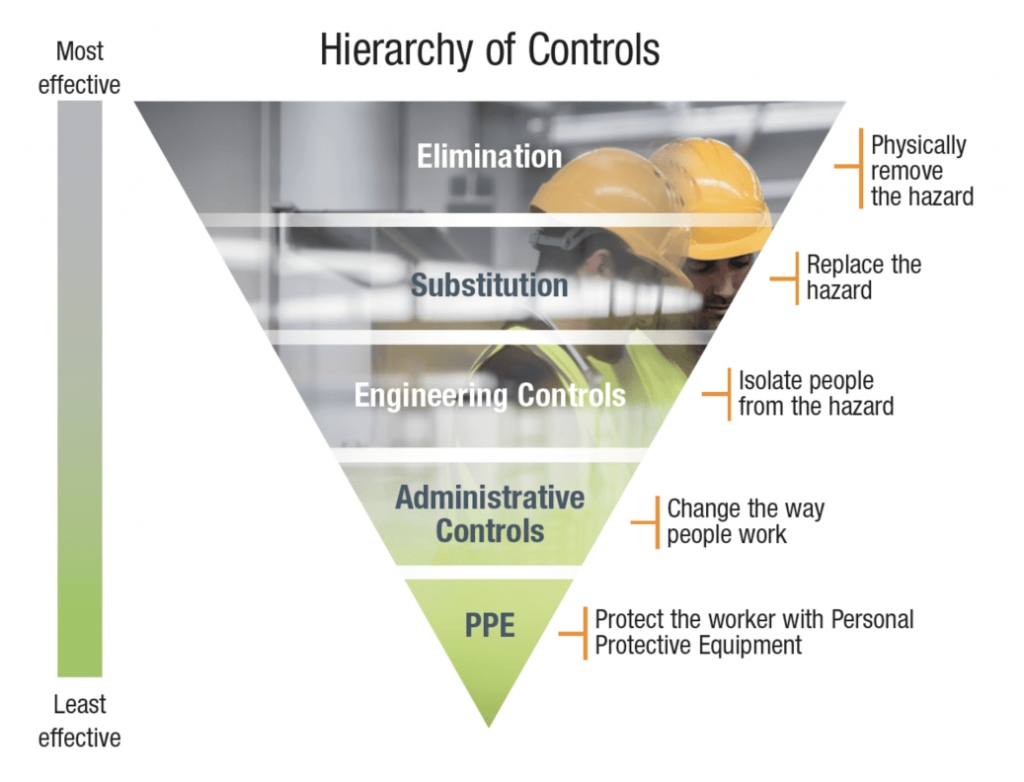
OSHA standards applicable to welding
• Welding, Cutting & Brazing—29 CFR 1910 Subpart Q.
• Welding & Cutting—29 CFR 1926 Subpart J.
• Welding, Cutting & Heating—29 CFR 1915 Subpart D.
• Permit-required confined spaces—29 CFR 1910.146.
• Confined & Enclosed Spaces & Other Dangerous Atmospheres in Shipyard Employment—29 CFR 1915 Subpart B.
• Hazard Communication—29 CFR 1910.1200.
• Respiratory Protection—29 CFR 1910.134.
• Air Contaminants—29 CFR 1910.1000 (general industry), 29 CFR 1915.1000 (shipyards), 29 CFR 1926.55 (construction) .