Calibration Gases and What You Should Know About Using them
4 min readWhen you’re working with gases or in confined spaces where the atmosphere may contain harmful gases, having an accurate gas detector is essential. Without it, workers may be at risk of illness and injury without even realizing it. But to do its job properly, the detector must be well-calibrated. Gas detectors are meant to save lives, but when they are inaccurate or incorrectly calibrated, they can become a serious risk.
Calibration gases are the unsung heroes of gas detection. But what are they, exactly? How do you use them? What specific things do you need to consider before using them? Before you set off to test your detectors, let’s take a closer look at calibration and get some answers to these questions.
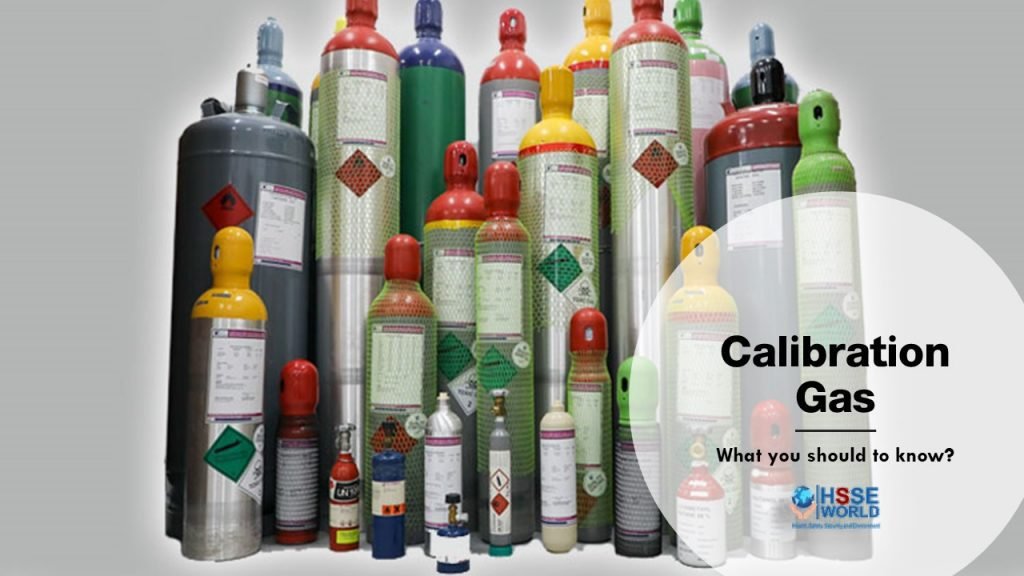
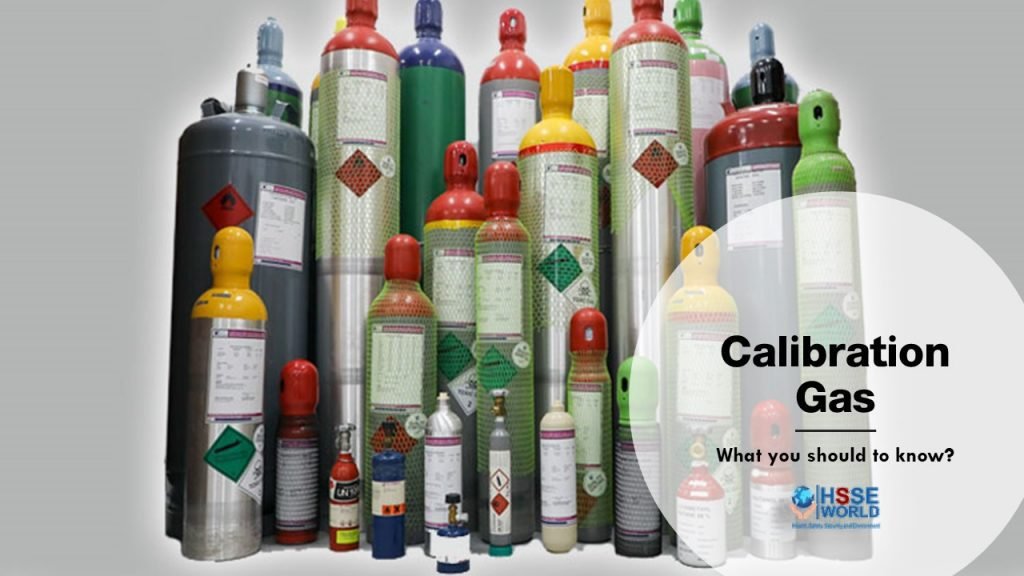
What Are Calibration Gases?
Simply put, calibration gases are used to calibrate gas detectors and ensure their proper functioning.
The only way to confirm that a gas detector is accurate is to test it with a known concentration of gas that is, a calibration gas. By exposing the detector to a confirmed concentration of a particular gas, users can determine whether the sensors respond accurately or provide an erroneous reading. They can also test whether the device alarms are working as they should.
Where Are Calibration Gases Used?
Gas detectors are used in nearly every safety application, which means that calibration gases are also required. Some common applications include:
- Pulp and paper mills
- Refineries
- Petrochemical plants
- Pharmaceutical facilities
- City governments
- Any confined space work
When to Use Calibration Gases
Calibration gases are necessary any time a calibration test or full calibration is being performed. While there is no hard and fast rule as to when a device must be calibrated, OSHA lays out some best practices that should be followed:
- A functional test (also known as a bump test) or full calibration should be performed each day before using a direct-reading portable gas monitor
- A full calibration must be carried out on any instrument that fails the functional test
- Calibration should be conducted more frequently if environmental conditions could affect device performance (e.g. sensor poisons, high gas concentrations, extreme temperature, mechanical shock, or stress) are suspected to be present
If ever in doubt, conduct a full calibration. By exposing the detector to a known concentration calibration gas, you can confirm the accuracy of the reading and the proper functioning of the alarm.
Employers that fail to regularly test and document instrument performance are vulnerable to regulatory fines and the occurrence of serious and preventable workplace accidents.
(Read more:what-is-meaning-of-LEL-UEL-PID/)
Calibration Is Only as Accurate as the Test Gas
It goes without saying that the results can be disastrous if calibration is conducted incorrectly or if the gas is not appropriate for the instrument being tested. OSHA recommends using the calibration gases available through the Agency Expendable Supplies Program for the specific instrument you are using. But no matter where your gas comes from, be sure to ask your supplier for a traceable certificate of analysis for every single cylinder you get.
It’s critical to ensure the expiration date marked on the cylinder has not passed. The concentration of a calibration gas-only remains stable for a limited time, particularly with reactive gases like hydrogen sulfide and chlorine. For this reason, gas past its expiration date cannot be confirmed accurately and should never be used.
When testing a device with multiple sensors, take care to confirm that you have the proper gas mix. Sometimes, mixes can adversely affect other sensors on the instrument, calling all your test results into question. It’s also a good idea to ask the supplier for a certificate of analysis for every test gas cylinder. You want to be sure that what they say is in the cylinder really is there.
This might seem like a lot of fuss. But when it comes to your test gas, it’s best not to take any chances.
Testing Tips
No matter how careful you are, sometimes things get overlooked. And when you’re dealing with potentially harmful gases and the safety of workers, that’s not such a good thing.
Review these helpful reminders to make sure your gas testing is as comprehensive as it can be.
- Always make sure your device is zeroed in fresh air (like an office environment)
- Perform a calibration check each day before the gas detector is used
- Full calibrations should be done at least monthly
- Verify the values the instrument uses to ensure sensor readings match the concentrations listed on the calibration gas cylinder label (the wrong concentration gas can produce inaccurate readings)
- Use the correct regulators and fittings to supply calibration gas to an instrument, as incorrect flows can produce inaccurate readings
If you’re at all uncertain about a step in the calibration process or how to determine whether the gas you’re using is the right one, don’t hesitate to get a second opinion from someone knowledgeable or speak to the instrument’s manufacturer.
Conclusion
When it comes to working with gas detectors, calibration can save your life. Be sure to follow all of the best practices when calibrating your devices and never take your calibration gas for granted.
(Read more:calibration-procedure-of-portable-gas-detectors)
1 thought on “Calibration Gases and What You Should Know About Using them”