Should You Use Plastic Labels or Metal Plates?
3 min readWe all know that the smallest details can have the biggest impact—and the way you label your products is one of those details.
A good label will provide a secure, reliable, and professional way for your products to be identified throughout their lifespan. It can improve the perceived quality of your product and even the reputation of your company. The wrong label will fall off or become unreadable—making product tracking impossible, inconveniencing your customers, and creating a time-consuming (and sometimes expensive) problem for you to solve.
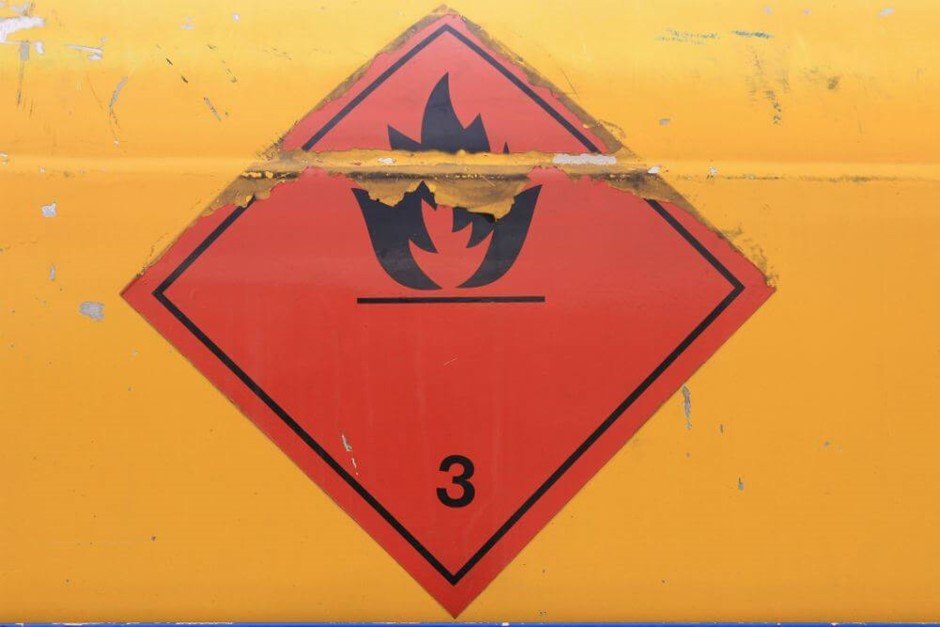
Choosing the Right Label
Simply opting for the most durable labeling you can find is often overkill, and an over-specified solution will quickly eat into your profit margins. The best way to choose effective labels is to consult with a specialist firm that understands the technical demands of your industry. There are many label manufacturers around the world, including Europe, United Kingdom, and North America. The most experienced label manufacturers are familiar with both metal plates and plastic labels, providing an expert opinion on which suits your needs best.
If you’re just beginning your research into labeling options, here is an overview of metal plates and plastic labels for use in industrial environments.
Metal plates
Metal plates (also known as nameplates, rating plates, or data plates) offer exceptional durability in an industrial environment. Their unparalleled tolerance for extreme temperatures, weathering, and exposure to chemicals (such as fuels and brake fluid) has made them a standard specification across many trades, including construction, aerospace, and automotive.
The Benefits
- Many industry specifications demand metal plates as standard
- Sub-surface printing is essentially permanent, resisting chemicals, abrasion, oils, and weathering
- Plates are exceptionally difficult to remove, especially if screwed or riveted into place
- A professional nameplate boosts the prestige and perceived quality of your product
- Metal plates have an unparalleled tolerance to high temperatures (up to 500°C, or 932°F)
- Cost-effective metals (like anodized aluminum) offer a competitive price point
The Drawbacks
- The overall cost of plates (materials, engraving, and affixing) is relatively high
- Colored inks are prone to fading in sunlight
- Plates are not indestructible and are vulnerable in certain environments (e.g. marine)
- The print has to be added at the point of manufacture for it to be permanent
- Engraved lettering can attract dirt and become hard to read over time or in certain lights
Plastic Labels
Plastic labels are growing in popularity, not least because of their cost-effectiveness when produced in bulk. As long as you choose the right material and adhesive combination, plastic labeling can still deliver excellent resistance to extreme temperatures, weathering, chemicals, and heavy handling.
The Benefits
- They are just as tough as metal plates for many applications and comparatively inexpensive
- Resistant to fluctuating temperatures (up to 388°C, or 730°F, for certain materials), weathering, chemicals, and frequent handling
- Quick and easy to apply
- Wipe-clean and easy to read long-term
- Flexibility for labeling lightly curved surfaces
- Durable color printing is possible, thanks to digital technology
- Versatile options for specific needs, such as RFID tags or tamper-evident labels
The Drawbacks
- Incorrectly specified adhesives may not tolerate moisture, weathering, or frequent handling
- Lower temperature limits than metal plates
- May not withstand repeated or long-term exposure to exceptionally harsh environments
Other Factors to Consider
Of course, the best material for your labels may not depend solely on the environment they will end up in. There are often other factors to consider, such as:
- Industry labeling regulations affecting your consumer (MILSpec, REACH, RoHS, etc.)
- Whether barcoding would be advantageous for traceability
- The surface your label will be attached to
- Security or anti-counterfeiting measures
- Whether you need to add data post-production, such as serial number or product codes (and whether you intend to outsource this or print or engrave it in-house).
To some extent, any of these requirements can be met by both metal and plastic labels. Depending on your exact application. However, you may find that the necessity of one particular feature makes either metal or plastic a better option for your labels.
Conclusion
With this information, you should have a better idea of the kind of labeling you’ll need for your purposes. But again, the simplest way to find a solution is to consult with a specialist, who will guarantee the most effective labels for the job.
1 thought on “Should You Use Plastic Labels or Metal Plates?”