Safe work site Activity for Traffic Management
Previously we spoke about safe work site design and examples of ways you can control worksite traffic risk from a sited design or layout perspective however Safe worksite practices can help reduce the risks to people working in or near worksite traffic. This article provides examples of safe practices for common vehicle-related worksite activities. These suggested control measures can help minimize the risks associated with vehicles at work sites.
As a person conducting a business or undertaking ( PCBU ), you will need to assess your individual situation to decide what controls measures will be the most effective and reasonably practicable for your situation. This may mean adopting a combination of control measures to manage the risk.
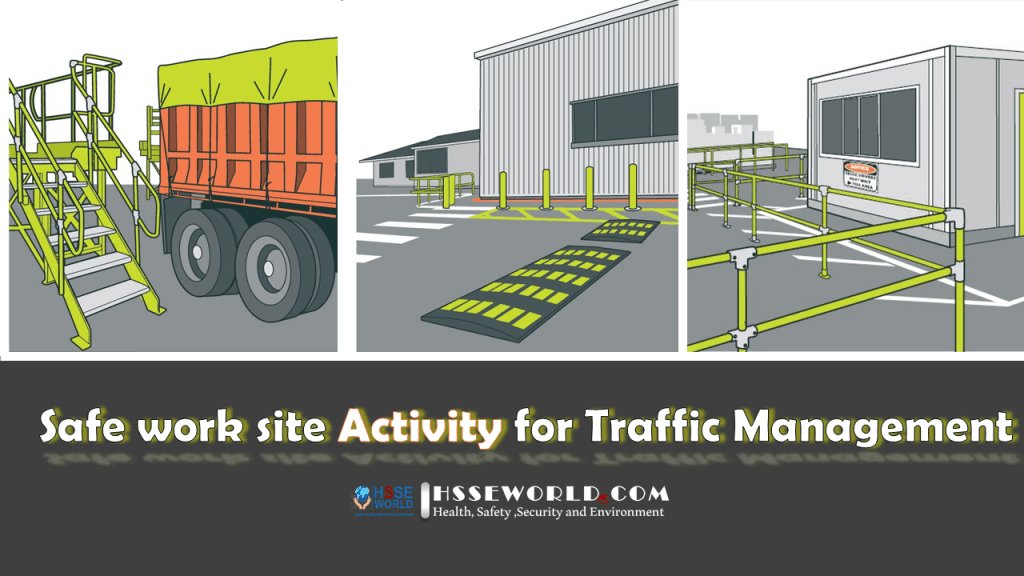
Speed
Reducing vehicle speed is an important part of worksite vehicle safety.
Set a maximum speed limit for your worksite:
- Speed limits should be based on the individual circumstances of your worksite but should remain within industry-accepted levels (for example, 10km/h in trucking yards and 30km/h on farms).
- To assess a suitable speed limit, consider the route layout and use. For example, lower speeds will be better where pedestrians are present or where forklifts and road-going vehicles share a traffic route.
- Speed limits need to be properly enforced and, where possible, consistent across the worksite.
- Consider consulting a suitably qualified person such as a traffic engineer, or traffic planner on what speed limits might be suitable for your worksite and the vehicles that operate there.
Speed control measures such as speed cushions (see Figure 1), chicanes, and rumble strips may also be useful for reducing speed. But you need to make sure they are not going to create new risks such as vehicle instability or limit visibility for drivers.
Consider installing speed-limiting devices on worksite vehicles where keeping vehicles and workers in separate areas are not reasonably practicable – especially for vehicles used inside warehouses or in close proximity to workers
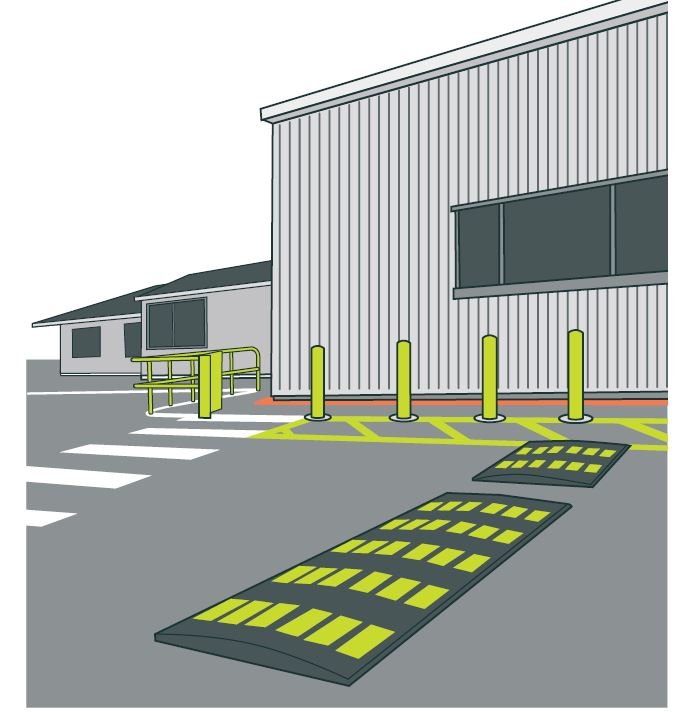
Reversing vehicles
The most effective way of reducing reversing incidents is to eliminate the need for reversing by:
- having a one-way drive-through loading and unloading system
- using multi-directional vehicles or vehicles with rotating cabins
- having designated turning areas that are separated from pedestrians and all other worksite activities.
Where these control measures are not reasonably practicable, you should consider:
- using devices like reversing sensors, reversing cameras, mirrors, rotating lights, or audible reversing alarms (make sure these are always kept clean and in working order)
- using a competent person to guide the reversing vehicle (see Spotting below)
- using radios and other communication systems
- providing a designated clearly marked, signposted, and well-lit reversing area with barriers around it to stop pedestrians from entering the area.
SPOTTING
The job of a spotter is to guide drivers when reversing and make sure reversing areas are free of pedestrians.
If you use a spotter, make sure:
- the spotter is always in visible contact with the driver and wearing high visibility clothing
- the spotter stands in a safe position throughout the reversing operation
- the spotter and driver both understand and agree on the standard spotting signs to be used.
In industries where vehicles can be very large (such as quarrying), radio contact should be used, with the spotter in a safe location away from the vehicle but still able to see what is happening.
Parking
Parking areas should be clearly signposted. There should be separate parking areas for commercial and private vehicles and designated areas where commercial vehicles can be loaded and unloaded.
When vehicles are parked, their parking brakes should always be applied.
Drivers should never leave a vehicle unattended without making sure the vehicle and the trailer are securely braked, the engine is off and the key to the vehicle has been removed.
Avoid parking smaller vehicles behind large ones or in areas where the driver does not have clear visibility of the smaller vehicle.
Parking areas should be on level ground so parked vehicles cannot roll away.
Where this is not possible consider:
- installing wheel stops in parking areas to stop vehicles from rolling away
- making sure the wheels of vehicles are pointed towards a safe stopping place like a curb or a wall so the vehicle or equipment does not accidentally roll away
- chocking the wheels of parked vehicles.
If loading docks are used, they should be built so that there is a slight downhill slope leading into the dock, to naturally keep the vehicle in the dock.
Coupling and uncoupling
Coupling and uncoupling should be done in a designated area that:
- is well lit
- has a firm and level surface
- has a surface suitable for the tare weight of the trailer and truck.
Trailer and tractor unit parking brakes should be used as appropriate.
Trailer swaps should be done in designated truck stop areas, away from busy roads, and with good lighting.
Loading and unloading
To minimize the risks to workers involved in loading and unloading vehicles, information should be provided on the nature of the load and how it should be properly loaded, secured, and unloaded. This information should accompany the load and be available to those involved in the loading, transportation, and unloading activities.
Loading and unloading areas should be:
- clear of traffic and workers not directly involved with loading or unloading
- well lit
- on level ground
- segregated from other work areas
- clear of overhead cables, pipes, or other obstructions
- protected from adverse weather where possible.
Where these conditions cannot be met, other control measures need to be considered (such as using temporary barriers if there is no room to unload away from other worksite activity).
When loading and unloading are taking place:
- one person should be in control of the loading zone (for example, the person operating the forklift, the stock room manager, site foreman, or spotter). Everybody involved in the loading or unloading activity should know who this person is before the activity starts.
- there should be clear operating procedures that are understood and always followed
- there should be a system in place to warn other vehicle drivers and workers that loading and unloading is in progress
- only workers directly involved with loading or unloading should be in the area
- warning devices such as lights, alarms, horns, cones and signage should be used.
You should have systems in place to stop vehicles from inadvertently moving
or being driven off during loading and unloading. For example:
- wheel chocks
- air brake isolation interlock devices
- vehicle or trailer restraints
- traffic lights on the loading bay
- dock locks.
Keys should be removed from the vehicle ignition and kept in a safe place (except for trucks that need the engine running for integrated cranes to operate).
( learn why the operator-dies-when-forklift-falls-off-loading-dock/)
Driver waiting areas
There should be a safe place where drivers can wait throughout loading and
unloading (see Figure 2). This location should:
- be far enough away to keep them safe
- be in a position where the driver can still see the loading or unloading of their vehicle
- be where the worker doing the loading can see them
- provide shelter from the weather and a place to sit.
Ideally, drivers should also have access to facilities such as toilets and somewhere to prepare a hot drink (accessed before or after loading or unloading).
There should be a clear system in place that tells drivers and all those involved with loading and unloading when it is safe for the driver to approach the vehicle, check the load, and drive away.
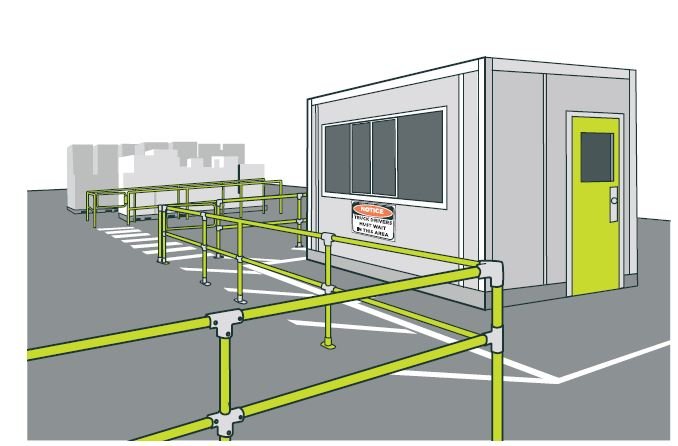
Loading and unloading shipping containers
Shipping containers should be placed in a location where they do not create dangers for those loading or unloading them, or for workers carrying out other activities at the same worksite:
- the proposed location should be on level ground with enough room to open the doors and provide safe access
- the proposed location should have enough space to operate vehicles in and around the shipping container and to set downloads outside of the shipping container
- the proposed area should be well lit.
Temporary barriers should be used to make sure only those involved in the loading or unloading of the shipping container can access the area.
Tipping
Tipping should be carried out on the level ground. Check there are no overhead obstacles, such as power lines. Make sure there are no unnecessary bystanders. Use temporary barriers and spotters if needed.
Tarping/load securing
Tarping and other forms of load securing can require working at height and manual handling of heavy equipment.
To eliminate the risks associated with working at height and manual handling, automated tarping devices are recommended.
Consider installing access platforms with barriers to stop falls where tarping must be done manually, or where the top of a load needs to be accessed for other reasons (see Figure 3).
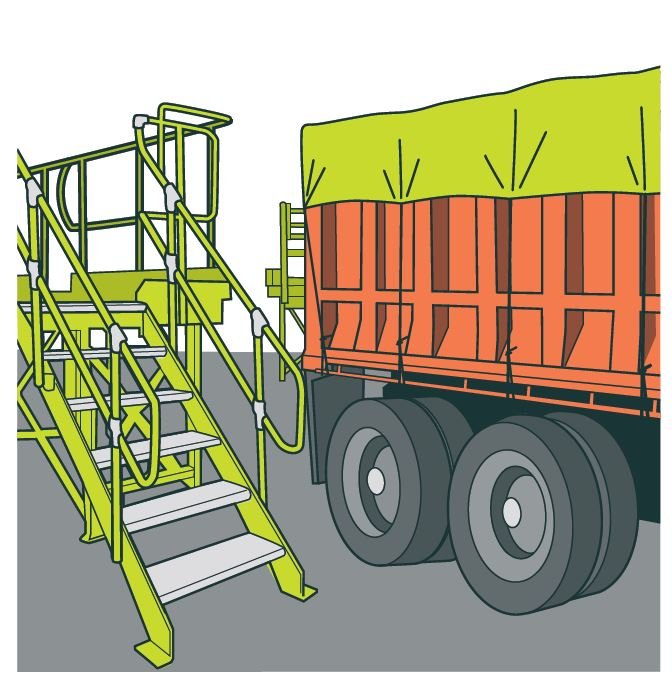
Queuing vehicles
At busy work sites, you may have several vehicles operating or arriving on-site at the same time. Having several vehicles operating on-site at the same time increases the chances of incidents happening.
To help manage the risks of queuing vehicles, you should:
- consider a queuing time slot system – use a gatehouse to control traffic time slots
- consider setting up separate areas for tarping, load securing, load splitting, maintenance and clean down to help reduce hold-ups
- make sure there is enough space between queuing vehicles, so they do not impact other traffic or block emergency exits
- make sure there is a safe system for communicating with drivers (such as telling them the expected wait times)
- make sure there is a safe access route for drivers if they need to exit their vehicle to access facilities or driver safe areas while waiting
- make sure queued vehicles are not parked over footpaths or blocking public roads
- consider the impacts of idling vehicles – make sure there is good ventilation to remove fumes and particulates, or have waiting vehicles turn their engines off if possible.