Occupational safety and health management systems
What are occupational safety and health management systems and why do companies implement them?
Contents
- Introduction
- What are occupational safety and health management systems?
- The relationship between occupational safety and health management systems and legislation and governmental policies
- The importance of standardisation
- 5 Processes of continuous improvement
- Reasons for implementing an occupational safety and health management system
- The option of certification
- The impact of occupational safety and health management on OSH performance
- The main factors for success or failure of OSH management systems
- Challenges for the future development of OSH management systems
Introduction
In company practice and in governmental legislation, it is increasingly acknowledged that occupational safety and health (OSH) management should be performed systematically and continually. Implementing an OSH Management System (OSH MS) is the major strategy to achieve this.
What are occupational safety and health management systems?
Occupational safety and health (OSH) problems were initially perceived as mainly technical problems that required technical solutions. Later, organisational issues were recognised as being important, and more recently, human factors, behavioural and organisational culture issues have been identified as being important.
The increasing awareness of problems and solutions has been mirrored by the development of management practices. Initially, management of OSH focused on technical inspections, with the later inclusion of organisational, human factors and behavioural issues. Today, it is broadly acknowledged that all these factors are important and the management of OSH requires an integrated approach.
OSH MS combine occupational safety and health with management and ‘system thinking’. In ‘system thinking’, entities such as organisations or departments are considered as ‘systems’ which comprise a range of ‘elements’ (e.g. risk assessment and OSH competence). The ‘whole (the system) is more than the sum of its parts (the elements)’ and the interactions between the elements are just as important as the elements per sé.
The five basic characteristics of any occupational safety and health managements systems are:
- It includes all components of OSH that are relevant to the members of the organisation and the business process.
- In principle, its functions are: (1) to increase the effectiveness of OSH management; (2) to guarantee compliance with existing legislation; and (3) to improve OSH performance. The OSH MS objectives are to be defined by the organisation and may include ethical, economic, legal and organisational goals. Not all OSH MS have similar objectives.
- It is a holistic approach, specifying and requiring implementation of a series of elements and (positive) interactions between them.
- It has provisions for system maintenance and continuity. The functioning of an OHS MS is evaluated on a regular basis (through OSH audits). A periodic review of its objectives and effectiveness is necessary to ensure continuous improvement.
- Its outputs (OSH performance) are important to the evaluation of the management system.
OSH MS help deal with complex issues, such as the ‘changing world of work’ the dynamics within organisations, and the interactions between management and employees. They lead to a better understanding of processes, problems and possible solutions, and enable the implementation of measures to reduce hazards and control risks.
The relationship between occupational safety and health management systems and legislation and governmental policies
Regulatory requirements now include a systematic management approach to control occupational hazards. The most prominent example is the EU framework directive from 1989. Although it does not require companies to have a OSH management system, it does require them to have a range of elements of the system (i.e. management and workers involvement, a risk assessment and control process, and OSH Competence). Within the EU, having a specific (process) safety management system in place is a legal requirement for the chemical process industries that deal with major hazards (the post-Seveso Directive).
Throughout various countries, government policies have supported the implementation of OSH management system. These include the exemption from regular screening inspections in Denmark[7] and the promotion of voluntary management systems in the UK[8]. Similar developments have taken place outside the EU. For example, OSH MS are embedded in the USA’s OSHA’s Voluntary Protection Programm.
The importance of standardization
In the 1990’s standardised approaches for OSH MS were developed that made use of the experiences with Total Quality Management, specifically those with Quality Management Systems according to the ISO 9000 standard.
Following these developments, and after fierce debates. OSH management system standards were developed. The main standard being OHSAS 18001 (note that the standard uses the term OHS while in this article the term OSH is used (first version 1999, updated in 2007). In 2001, the International Labour Organisation (ILO) also published OSH MS Guidelines.
The OHSAS method is based on the ‘Deming cycle’, which consists of an iterative process of four steps, known as ‘Plan, Do, Check and Act (PDCA)’. The involvement of top management in all steps of the process is essential for an effective management system. Risk assessment is the most important in the ‘Plan’ stage. The participation of employees with relevant skills and competences, and available resources is critical for ‘Do’. Performance measures and corrective and preventive action are the essence of ‘Check’, while ‘Act’ centres around the management review, taking into account OSH performance measures. An overview of the four steps and the elements of OHSAS is shown in table 1.
Table 1: The ‘Plan, Do, Check and Act’ steps, and the main
Processes of continuous improvement
An important feature of OSH MS is the process of continuous (or continual) improvement.Any OSH MS implies an iterative process, with each cycle in the process aiming to contribute to OSH improvement. This is illustrated in Figure 1 of the OHSAS model taken from the OHSAS 18001 standard.
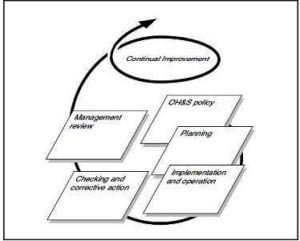
Figure 1: The OHSAS model: OHS management as an iterative process for continual improvement
The idea of continuous improvement (stemming from the ‘PDCA’ cycle) is challenging and promising. However, in practice it is often not easy to achieve continuous improvement in OSH performance
One reason is that it presupposes a stable or constant work environment. If no new risks are introduced and the existing risk control measures are always functioning well, further improvement will contribute to an overall improvement in OSH. However, in everyday practice, organisations are dynamic and evolving. Reorganisation within the company and the introduction of new technologies and ways of working may imply drastic changes. People may leave the organisation and may not be replaced – perhaps with them relevant OSH knowledge disappears. Such developments may alter the process of continuous improvement to a process of ‘trying to keep up with changes’.
The second reason is that the process of continuous improvement presupposes a process of organisational leaning (with respect to OSH management). Such organisational learning processes are possible, but are not an automatic result of implementing an OSH MS. For an interesting analysis of the process of continuous improvement and learning.
Reasons for implementing an occupational safety and health management system
There are several reasons why organisations might want to implement an OSH MS. The main reasons are:
- to systemise OSH Management;
- to optimise prevention;
- to improve OSH performance;
- to reduce possible future liabilities;
- to assure compliance with legislative requirements;
- to create organisational benefits, whether economic or other;
- to show that the organisation cares for its employees and is a good employer;
- to benefit from regular external feedback from third party auditors;
- to reduce the likelihood of inspection by the labour inspectorate;
- to demonstrate to customers and external stakeholders that an OSH MS is in place;
- to be transparent about the company’s corporate social responsibilities.
The option of certification
The ISO management standards imply the option of third party certification. Third party certification means that an independent and competent agency (e.g. DNV, Lloyds, BVQI, etc.) confirms after a dedicated audit that there can be ‘justified confidence’ that the management system is functioning well, and that the organisation complies with all relevant requirements. Such agencies evaluate the ‘system of plans and words’ (in the OSH Management Handbook), as well as the ‘system of associated practices’ in the organisation. Where these two ‘systems’ do not correspond, the practices should be considered more important than the paper work, as these determine the occupational safety and health performance.
Having a certified occupational safety and health management system in place is increasingly becoming a business-to-business requirement. Since the early 1990’s, this development has also raised the issue of integrated Management systems, wherein OSH MS are integrated with quality and/or environmental management systems, and business processes. According to a survey carried out by the British Standardisation Institute at the end of 2009, more than 56,200 companies were certified worldwide as having an OSH management system, of which more than 8,200 were in the EU.
The certification regimes associated with OSH MS have been criticised, e.g. for increasing the cost to businesses and for becoming an ‘aim in themselves’ for failures in the broader certification regimeand in the associated market mechanisms, and for problems with the quality of the essential auditing process.
Certification can be attractive for companies, especially as it demonstrates to customers and the labour inspectorate that they are addressing occupational safety and health issues continuously and systematically. However, the certification process can become an ‘aim in itself’, when ‘having the certificate’ becomes more important than the improvements in OSH performance. Therefore, several companies choose to implement a ‘certifiable management system’, but refrain from certification. They then enjoy the benefits of a good and auditable OSH management system, while avoiding the danger of the certification process becoming a ’means to an end’.
The impact of occupational safety and health management on OSH performance
An occupational safety and health management system influences the occupational safety and health performance of the organisation. A management system only functions adequately when there is a continuous and systemic control of all activities and influences relevant to OSH.
Beneficial effects on health and safety performance can be expected in the short-term from improvements during the implementation process (when the management system is put in place), and in the long-term from the potential of the continuous improvement process over time.
Nevertheless, there are debates as to whether OHS MS have a positive effect on health and safety or not. On the one hand, proponents almost take it for granted that an occupational safety and health management system will automatically lead to better health and safety performance, as is suggested in the OHSAS Standard. On the other hand, critics have used words, such as “scam”, “fraud”, “bureaucracy” and “paper tigers”, to describe management systems and pointed out that workers lose influence. In reality, the impact of OSH MS is depending on several contextual factors and therefore ambiguous.
It is well established that occupational safety and health management system can be a valuable method for the improvement of health and safety. Whilst OSH MS can be used as a tool for management, how that tool is used depends primarily on the management’s ambitions (the OSH objectives). These ambitions can range from ‘having the certificate’ to becoming ‘world class in health and safety’. OSH MS can also be regarded as an enabling methodology which can be used to serve different purposes, and can be associated with different contents, depending on the company and its ambitions, culture and history.
OSH MS imply an on-going ‘PDCA’ process, but planning and the associated paper work is often easier to accomplish compared to the rest of the cycle. Especially after reorganisations the paper work remains intact, but practices and responsibilities may have changed, leading to the danger that occupational safety and health management system become just a paper exercise.
The changes to the way a business operates, societal developments, shifting priorities and risk perceptions of internal and external stakeholders, influences the functioning of OSH MS over time. Occupational safety and health management system also require continuous interpretation, adaptation, anticipation and monitoring, e.g. with regard to newly emerging risks, such as psychosocial risks or those stemming from nanotechnology. Therefore, the functioning of OSH MS is always dynamic and complex, and sometimes implies uncertainties, and ambiguities.
Despite the concept of ‘management system’ suggesting that it is an issue for management only, worker participation in OHS MS is regarded as essential.
In summary, the ambition to improve OSH substantially, the commitment of management, the participation of workers and the continual adaptation to changing circumstances are essential for effective OSH MSs. This has implications for the scientific evaluation of the effectiveness of occupational health and safety management system. It is not useful to prove once and for all that OHS MS are beneficial for managing health and safety, when such contextual factors are not taken into account. An OHS MS cannot be evaluated as a simple mono-causal intervention, or as if it was independent of its dynamic internal and external environment. Therefore, it is hardly surprising that the positive effects of an OSH MS on health and safety performance have been difficult to demonstrate in systematic reviews that do not take account of such factors.
The main factors for success or failure of OHS management systems
Occupational health and safety management system are a valuable approach, but their effectiveness is influenced by a range of internal and external factors. Several of these factors have already been mentioned above.Table 2 summaries the factors critical to the functioning and usefulness of OSH management system
Table 2: Factors contributing and hindering the effectiveness of OSH MS
Challenges for the future development of OSH management systems
As we have described, OSH management system do not function as independent systems, but are impacted on by a range of internal and external factors. The compatibility with a changing external environment and the development of an internal context that is supportive to OSH suggests that the main challenges for the future development of occupational health and safety management system are:
- to make OSH MS better suited to the ‘changing world of work’, where production is increasingly outsourced and risks can be easily shifted to partners in the supply chain, or to contingency workers.
- to develop OSH MS that contribute explicitly to organisational strategy and business goals, as well as deliver OSH benefits. In this respect, the growing attention to corporate social responsibility forms an opportunity to develop innovative OSH MS and OSH strategies
- to factor business ethics and organisational learning processes into the design and functioning of OSH MS. This implies additional dimensions, such as business ethics and value management.
- to develop useful and practical sets of performance indicators in order to monitor and steer the development of OSH MS and OSH performance.