General Elements of OH&S Program
20 min readA health and safety program is a definite plan of action designed to prevent incidents and occupational diseases. Some form of a program is required under occupational health and safety legislation. A health and safety program must include the elements required by the health and safety legislation as a minimum.
This article reviews the general elements of an OH&S program. In all cases, contact the OH&S authorities in your jurisdiction for specific requirements.
Because organizations differ, a program developed for one organization cannot necessarily meet the needs of another. Always customize the OH&S program to match the requirements and needs of your workplace.
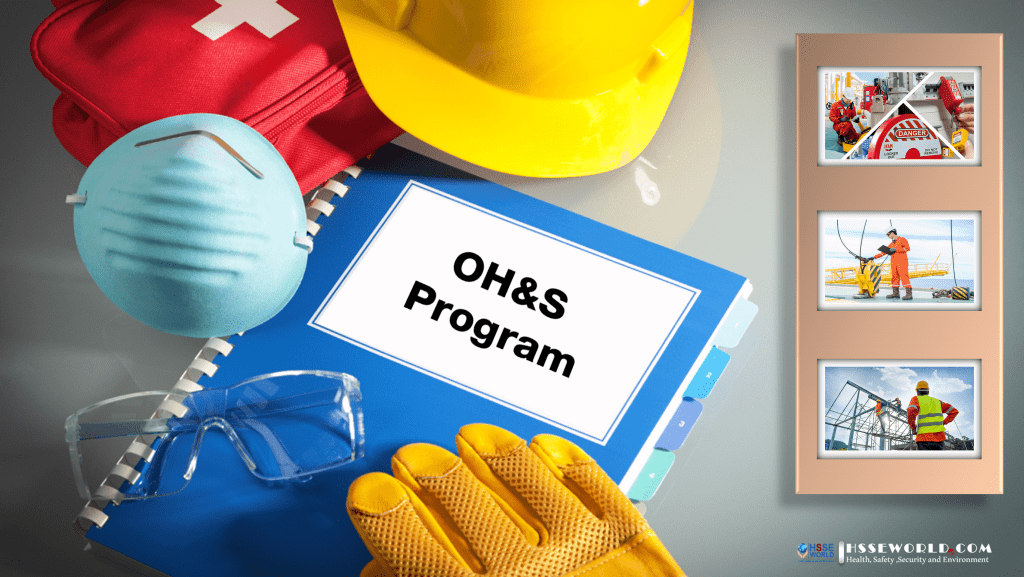
Policy statement
An organization’s occupational health and safety policy is a statement of principles and general rules that guides action. Senior (or top) management must be committed to ensuring that the policy is carried out with no exceptions. The health and safety policy should have the same importance as the other policies of the organization.
The policy statement can be brief, but it should mention:
- Management’s commitment to protecting and promoting the safety and health of workers, and preventing injuries and illnesses.
- The objectives of the program.
- The organization’s health and safety philosophy.
- Who is accountable for the health and safety programs.
- The general responsibilities of all managers and workers.
- That health and safety shall not be sacrificed for convenience or expediency.
- That unacceptable performance of health and safety duties will not be tolerated.
The policy should be:
- Stated in clear terms.
- Signed by the current President or Chief Executive Officer.
- Kept up-to-date.
- Communicated to each worker.
- Followed for all work activities.
The following is an example of an occupational health and safety policy statement:
ABC Transport
To all employees January 1, 2021
At ABC Transport the safety and health of our workers comes first. Management is committed to doing everything possible to prevent injuries, to promote prevention, and to maintain a safe and healthy environment.
To this end:
1) all supervisors are responsible for ensuring that their workers are trained in approved safe work procedures and to ensure that workers follow safe work procedures and all related regulations;
2) all personnel are required to support the OH&S program and make safety and health a part of their daily routine and to ensure that they are following safe work procedures and relevant regulations;
3) all personnel will be held accountable for implementing this program; and
4) all relevant laws and regulations are incorporated in our program as minimum standards
Signed by President
What are the program elements?
While organizations will have different needs and scope for specific elements required in their health and safety program, the following basic items should be considered in each case:
- Individual responsibility.
- The establishment and role of the health and safety committee or representative.
- Applicable health and safety legislation requirements, and organizational health and safety rules.
- Safe work procedures.
- Worker orientation.
- Training and education.
- Workplace inspections.
- Hazard identification, assessment, and control
- Reporting and investigating incidents.
- Emergency planning.
- Medical and first aid.
- Health and safety promotion, including psychological health and prevention of harassment and violence.
- Workplace-specific items.
- Review of the health and safety program.
What are individual OH&S responsibilities?
Health and safety are the joint responsibility of management and workers. Managers and supervisors are accountable for non-compliance to health and safety legislation.
Responsibility may be defined as an individual’s obligation to carry out assigned duties. Authority implies the right to make decisions and the power to direct others. Responsibility and authority can be delegated to others, giving them the right to act for others, such as supervisors. It is important to note that, while some responsibilities can be delegated, the supervisor remains accountable for seeing that they are carried out.
Individual responsibilities apply to every worker in the workplace, including the President or Chief Executive Officer. Stating these responsibilities means that all workers will then know exactly what is expected in health and safety terms.
To fulfill their individual responsibilities, the people must:
- Know what these responsibilities are (communication required).
- Have sufficient authority to carry them out (organizational issue).
- Have the required ability and competence (such as those acquired through education, training, or certification).
Once all these criteria have been met, safety performance can be assessed by each individual’s supervisor on an equal basis with other key job elements. Health and safety is not just an extra part of a worker’s job: it is an integral, full-time component of each individual’s responsibilities.
What are examples of the responsibilities of workers?
Examples of responsibilities of workers include:
- Using personal protection and safety equipment as required by the employer.
- Following safe work procedures.
- Knowing and complying with all regulations.
- Reporting any injury or illness immediately to the supervisor or manager.
- Reporting unsafe acts and unsafe conditions to the supervisor or manager..
- Participating in the health and safety committees or as the representative.
What are examples of the responsibilities of supervisors?
Examples of responsibilities of first-line supervisors include:
- Instructing workers to follow safe work practices.
- Enforcing health and safety regulations.
- Correcting unsafe acts and unsafe conditions.
- Ensuring that only authorized or adequately trained workers perform tasks or operate the equipment.
- Reporting and investigating all incidents.
- Inspecting the areas they have control over and taking remedial action to minimize or eliminate hazards.
- Ensuring equipment is properly maintained.
- Promoting safety awareness in workers.
What are examples of the responsibilities of management?
Examples of responsibilities of management include:
- Providing a safe and healthful workplace.
- Establishing and maintaining a health and safety program.
- Ensuring workers are educated, trained, or certified, as required.
- Reporting incidents and cases of occupational disease to the appropriate authority.
- Providing medical and first aid facilities.
- Ensuring personal protective equipment is available and maintained.
- Providing workers with health and safety information.
- Supporting supervisors in their health and safety activities.
- Evaluating health and safety performance of supervisors.
- Ensuring the health and safety program is reviewed at defined intervals.
- Ensuring any changes necessary as the result of this review are implemented.
What are examples of responsibilities of safety coordinators?
Examples of responsibilities of safety coordinators include:
- Advising all workers on health and safety matters.
- Coordinating interdepartmental health and safety activities.
- Collecting and analyzing health and safety statistics.
- Providing health and safety education and training.
- Conducting research on special problems.
- Attending health and safety committee meetings as a resource person.
- Resolving reported health and safety issues.
- Ensuring the timely implementation of corrective and preventive actions with supervisors and management.
What is the purpose of a health and safety committee?
An effective safety program needs the cooperative involvement of all workers. A health and safety committee is a forum for the collaborative involvement of employees representing both labor and management. Such committees are legal requirements for organizations of a specified minimum size in all Canadian jurisdictions. When a committee may not be required, a worker representative may be appointed. The responsibilities of members of the committee or representative are detailed in the health and safety legislation across Canada.
A health and safety committee brings together workers’ in-depth, practical knowledge of specific jobs and management’s overall overview of job interrelationships, general company policies, and procedures.
The employer must establish a committee that is organized and operates in compliance with the law, is effective, involves the widest range of workers and management, and provides resources (e.g., time, money, meeting rooms) so the committee can do its work. To function properly, the committee needs an appropriate structure, a clear statement of purpose and duties, and standard procedures for meetings. The committee does this by establishing terms of reference and the employer provides support by allocating adequate resources.
Common terms of reference include:
- Stating senior management’s commitment to respond to the committee’s recommendations.
- Defining how long a person will serve on the committee (if not specified by legislation).
- Establishing how a committee member will be chosen.
- Establishing how often a committee will meet, conduct inspections, etc.
- How the employer will respond to the committee’s recommendations.
Each organization should set up its own terms of reference. More information is available in the health and safety committee documents listed below:
- Joint Health and Safety Committee – What is a Joint Health and Safety Committee?
- Joint Health and Safety Committee – Creation
- Joint Health and Safety Committee – Effective and Efficient
- Joint Health and Safety Committee – Measuring Effectiveness
- Joint Health and Safety Committee – Structure
The health and safety committee members should be active participants in consulting, developing, implementing, and monitoring all phases of the health and safety program.
Why are safe work procedures established?
Government health and safety regulations represent minimum requirements. In almost all cases, organizations will exceed these regulations with rules or procedures that are specific to the organization, the work being done, the equipment used, etc.
We need rules – to protect the health and safety of workers – but there are dangers in having either too few or too many rules. Too few rules may be interpreted as a sign that health and safety are not important, or that common sense is all that is required to achieve them. Too many rules may be seen as not treating workers as thinking adults and makes enforcement of all rules less likely. Following are some guidelines for establishing rules:
- Rules should be specific to health safety concerns in the workplace.
- The health and safety committee should participate in their formulation.
- Rules should be stated in clearly understandable terms.
- Rules are best stated in positive terms (“workers shall” not “workers shall not”).
- The reasons for the rule should be explained.
- Rules must be enforceable since disregard for one rule will lead to disregard for others.
- Rules should be available to all workers in written form, in the languages of communication of workers.
- Rules should be periodically reviewed to evaluate the effectiveness and to make changes for improved effectiveness.
Compliance with health and safety rules should be considered a condition of employment. Rules must be explained to new workers when they start work or if they are transferred or retrained. After a suitable interval, these workers should be briefed to ensure they understand the rules applicable to their work.
The employer must establish procedures for dealing with repeat rule violators. Supervisors are responsible for correcting unsafe acts, such as a breach of rules, and they must be supported in this duty. Points that should be considered in establishing procedures on this issue are:
- Ensure that workers are aware of the rule.
- Ensure that workers are not encouraged, coerced, or forced to disregard the rule by fellow workers.
- All rules are to be followed.
- All violations will be managed.
- Action is taken promptly. The role of discipline is that of education, not punishment.
- While having guidelines for penalties for the first offense or infractions may be desirable, some flexibility is required when applying the guidelines since each case will vary in its circumstances.
- Action is done confidentially, consistently, and recorded.
How do you establish safe work procedures?
Safe work procedures are the safest way of doing a job, job instruction, monitoring performance, and incident investigation.
Job safety analysis (JSA), also known as “job hazard analysis”, is the first step in developing the correct procedure. In this analysis, each task of a specific job is examined to identify hazards and to determine the safest way to do the job. Job safety analysis involves the following steps:
1. Select the job.
2. Break down the job into a sequence of steps.
3. Identify the hazards.
4. Define preventive measures.
The analysis should be conducted on all critical tasks or jobs as a first priority. Critical jobs include:
- Those where frequent incidents and injuries occur.
- Those where severe incidents and injuries occur.
- Those with a potential for injuries.
- New or modified jobs.
- Infrequently performed jobs, such as maintenance.
Job safety analysis is generally carried out by observing a worker doing the job. Members of the joint health and safety committee should participate in this process. The reason for the exercise must be clearly explained to the worker, emphasizing that the job, not the individual, is being studied. Another approach, useful in the analysis of infrequently performed or new jobs, is group discussion.
A work procedure may consist of more than one specific task. In such cases, each separate task should be analyzed to complete a job safety analysis for that procedure. The final version of the safe work procedure should be presented in a narrative style format that outlines the correct way to do the job in a step-by-step outline. The steps are described in positive terms, pointing out the reasons why they are to be done in this way. Reference may be made to applicable rules and regulations and to the personal protective equipment required if any. Workers who carry out the tasks should be consulted in developing the procedure.( learn more: steps-to-conducting-an-effective-job-safety-analysis-jsa/)
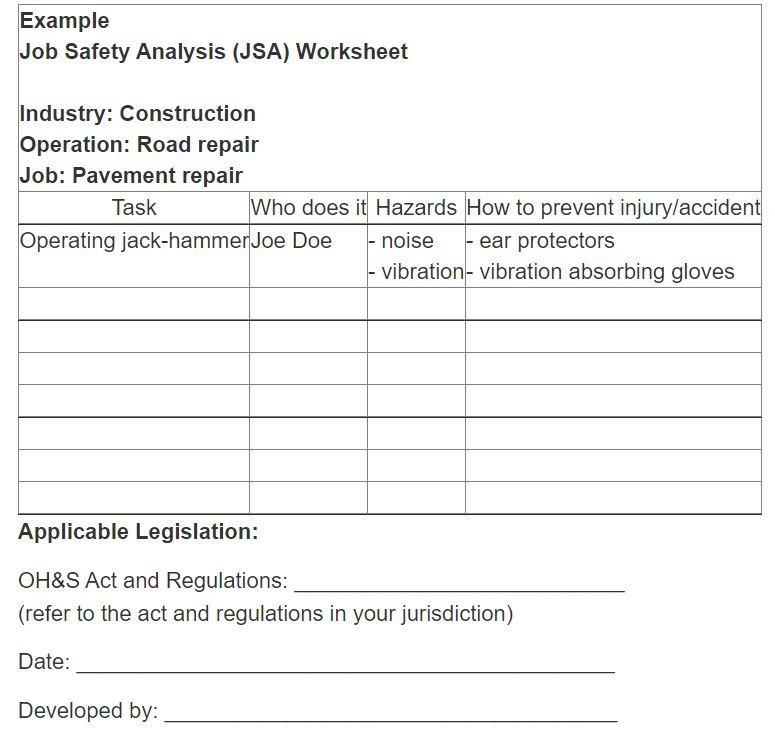
Why is worker orientation important?
Health and safety education should start with worker orientation when a worker joins the organization or is transferred to a new job. It has been found that inexperienced workers, in general, are involved in incidents at a higher rate than others. While experience can only be gained through time, both health and safety education and job skills training can be used to improve this record. Orientation sessions normally cover such items as an explanation of the function of the work unit, organizational relationships, administrative arrangements, and various policies and rules.
Items related to health and safety that should be included are:
- Emergency procedures, including evacuation and first aid.
- Location of first aid stations.
- Health and safety responsibilities, including those specified by legislation.
- Reporting of injuries, unsafe conditions, and acts.
- Use of personal protective equipment.
- Rights to know about the hazards of their work, to participate, and to refuse hazardous work.
- Hazards present at the workplace, including those outside own work area.
- Reasons for each health and safety rule.
- Any human resources, employment standards, and health and safety-related policies and procedures along with specific procedures ( e.g., absence reporting, hazard reporting, reporting injury or illness, etc.)
- Support (e.g., who to call when there is an emergency, technical issues, etc.)
Security protocols (e.g., how to access workplace premises, after-hour access, etc.) A new employee can be expected to absorb only a certain amount of information in the first few days. Be sure to pace the training to ensure all of the information or skills are learned. Other tips include providing written information that outlines the points covered in the orientation sessions. It also serves as a checklist for the person conducting the orientation. A buddy or mentor system is useful. This system allows for on-the-job reinforcement of the information presented to the new employee. This process also promotes the safety awareness of the experienced workers who are the “buddies”.
All workers, but especially new, inexperienced, or transferred workers, should be encouraged to ask questions at any time when doubt exists as to correct procedures or their ability to do the task safely. The orientation should address:
- What are the hazards of the job?
- When is job safety training available?
- What safety equipment do I need to do my job?
- Do I need to wear personal protective equipment (PPE)? Will I receive training on how to use the PPE?
- What do I do in case of fire or another emergency?
- Where do I find fire extinguishers, first aid kits, first aid rooms, and emergency assistance?
- What are my responsibilities regarding health and safety?
- If I notice something wrong, to whom should I report?
- Who is responsible for answering safety-related questions?
- What do I do if I get injured or have an incident?
Soon after the orientation sessions, employees should be assessed on their understanding of the items discussed. In this way, both the quality of training and the level of understanding can be evaluated. Continue with education and training throughout their employment, as needed.
(Read more about : New-worker-orientation-safety-orientation-checklist/ )
How do you design an education or training program?
The objective of education and training is to instruct recipients about health and safety procedures or specific job practices and to raise awareness or skill levels to an acceptable standard.
Occasions, when worker education or training may be required, are:
- Beginning of employment.
- Reassignment or transfer to a new job.
- Introduction of new equipment, processes, or procedures.
- Refresher, annual, or periodic education and training to ensure skills and knowledge.
- When there is a change to the legislative requirements.
- Inadequate performance.
Safety Standards, Occupational Health, and Safety Training, also outlines suggested training for supervisors. The standard states that a supervisor “should be competent (i.e., have adequate knowledge, training, and experience) on all processes and tasks over which he or she is exercising authority. Organizations should define what constitutes an acceptable combination of knowledge, training, and experience in relation to the supervision of others performing tasks.” Topics that may be included in supervisor training include:
- Roles and responsibilities – legal and corporate.
- Internal responsibility system.
- Hazard identification, hazard control, and risk assessment.
- Emergency procedures.
- Incident investigation.
- Conducting planned inspections.
- Auditing skills.
- Training.
- Planned task observation.
- Communication skills.
- Motivation and discipline.
- Managing workers.
- Off-the-job safety.
- Problem-solving skills.
- First aid.
- Workplace Hazardous Materials Information System (WHMIS)/chemical safety.
- Industrial hygiene and medical surveillance programs.
- Duty to accommodate.
When providing training, an instructor should:
- Receive training in how to instruct.
- Prepare an orderly plan for instruction.
- Explain the reasons why each step must be done in a certain way.
All instructors should:
- Plan the session beforehand, break the job down into steps, and have training aids available.
- Explain what is to be done.
- Describe all the hazards and protective measures.
- Demonstrate each step, stress key points, and answer any questions.
- Have the worker carry out each step, correct errors, and compliment the good performance.
- Check frequently after the worker is working independently to ensure correct performance.
Documented correct work procedures are very important in job skills training.
What are workplace inspections?
Workplace inspections help to identify existing hazards so that appropriate corrective action can be taken. Health and safety legislation requires workplace inspections as a proactive action to ensure workplace health and safety.
The frequency of planned formal inspections may be set out in legislation. Records of previous incidents and the potential for incidents are factors to be included when determining if more frequent inspections are needed.
Supervisors are responsible for conducting their own inspections (for the areas they are responsible for) and for taking action on unsafe conditions and acts as they are reported or encountered.
General inspections may be conducted by health and safety committee members or representatives, especially if they have received training or certification. Other criteria for selecting the inspection team are:
- Knowledge of regulations and procedures.
- Knowledge of the hazards in the workplace.
- Experience with work processes involved.
Pre-planning any inspection is always worthwhile. Documents, such as previous inspections, incident investigations, maintenance reports, and committee minutes, should be consulted. If a checklist is to be used, it should be reviewed and changed to meet the specific needs of the workplace.
Checklists are useful aids in that they help ensure that no items are overlooked in an inspection. One type of checklist is the “critical parts inventory”. This inventory itemizes parts and items that may result in an incident if they fail. While many ready-made checklists are available in safety literature, it is best to adapt these to your workplace. The health and safety committee should participate in the preparation of these tailor-made checklists.
Sample of inspection Checklist

During the actual inspection, both work conditions and procedures should be observed. If a hazard poses an immediate threat is discovered, preventive action must be taken right away, not after the inspection. Notes are made, specifying details of the hazard, including its exact location. When completing the inspection report, it is a good idea to classify each hazard by degree of possible consequences (for example A = major, B = serious, C = minor). In this way, priorities for remedial action can be established.
( you can download 22-safety-inspection-checklists/ )
Workplace Inspection Report
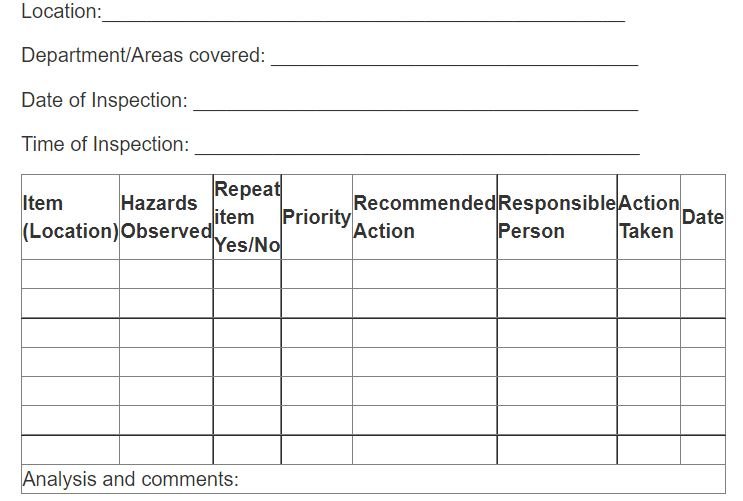
Priority Codes: A – do immediately; B – do within 3 days; C – do within 2 weeks; D – other
Inspections serve a useful purpose only if remedial action is taken to correct shortcomings. Causes, not symptoms alone, must be rectified. Corrective action should be taken immediately, emphasizing engineering controls, management failures, or the need for worker education, whatever applies.
What should you report and investigate when an incident occurs?
Occupational health and safety legislation in all Canadian jurisdictions requires that specific injuries and certain categories of incidents must be reported. There may be minimum legal requirements for their investigation. Many organizations investigate other events (e.g., where damage did not involve injuries) and “near misses.” The health and safety program should specify:
- What is to be reported.
- To whom it will be reported.
- How it is reported.
- Which incidents are investigated?
- Who will investigate them?
- What forms are used.
- What education and training investigators will receive.
- What records are to be kept.
- What summaries and statistics are to be developed.
- How often reports are prepared.
Incidents are investigated so that measures can be taken to prevent a recurrence of similar events. The investigation represents an “after-the-fact” response for any particular mishap. However, a thorough investigation may uncover hazards or problems that can be eliminated “before the fact” for the future. After causes have been determined, prompt follow-up action is required to achieve the purpose of the investigation.
Please note: The term incident is used in some situations and jurisdictions to cover both an “accident” and “incident”. It is argued that the word “accident” implies that the event was related to fate or chance. When the root cause is determined, it is usually found that many events were predictable and could have been prevented if the right actions were taken – making the event not one of fate or chance (thus, the word incident is used). For simplicity, we use the term incident to mean all of the above events.
( learn more :accident-incident-prevention-techniques-2nd-edition/)
What are emergency procedures and how are they established?
Emergency procedures are plans for dealing with emergencies such as fires, explosions, major releases of hazardous materials, violent occurrences, or natural hazards. When such events occur, the urgent need for rapid decisions, shortage of time, lack of resources, and trained personnel can lead to chaos.
The objective of the plan is to prevent or minimize fatalities, injuries, and damage. The organization and procedures for handling these sudden and unexpected situations must be clearly defined.
The development of the plan follows a logical sequence.
- Compile a list of possible hazards or scenarios (for example fires, explosions, floods).
- Identify the possible major consequences of each (for example casualties, damage).
- Determine the required countermeasures (for example evacuation, rescue, firefighting).
- Inventory the resources needed to carry out the planned actions (for example medical supplies, rescue equipment, training personnel).
- Based on these considerations, establish the necessary emergency organization and procedures.
Communication, training, and periodic drills are required to ensure adequate performance when the plan must be implemented.
How do you establish first aid programs?
First aid is generally prescribed under health and safety legislation or workers’ compensation legislation. The OSH program must include the following information:
- Location of first aid stations or medical facilities, and any required supplies or equipment.
- Identification of first aid attendants.
- Identification of other staff trained in first aid.
- Policy on pre-employment and follow-up medical examinations.
- Procedures for transporting injured workers to outside medical facilities.
- Provision of first aid training.
- Procedure for recording injuries and illnesses.
A policy on return to work after a lost-time accident might appropriately be included in this section of the program.
In general, if injured workers are offered alternative employment:
- The work should be suitable and productive.
- The worker’s physician must agree that such employment will not harm the worker or slow down the recovery.
- The worker will pose no threat to other workers.
- The policy is applied to off-the-job injuries as well.
Under no circumstances should the reduction of severity ratings be a reason for initiating a “modified work” program.
How do you prevent violence and harassment in the workplace?
All jurisdictions have legislation specific to harassment and violence (note that the legislation in the Yukon will be in force in September 2021).
All jurisdictions specify elements required in harassment and violence prevention policies and programs. While there are variations between jurisdictions, there are many common elements such as:
- Defining violence and harassment. Some definitions include bullying formally
- Conducting a workplace assessment (a hazard identification and risk assessment) specific to harassment or violence
- Developing and implement preventative measures
- Developing a policy and program, implement the program, and corresponding procedures for reporting an incident
- Developing a reporting and resolution process, including how to report an incident or occurrence
- Providing worker instruction, education, or training
- Determining procedures to ensure confidentiality and privacy
- Listing supports that are available (internally, externally)
- Requiring record keeping
- Using continual review and improvement processes to update the policy and programs
- Reporting to the jurisdiction, as necessary
- Including additional requirements for situations such as family (domestic) violence, or working late-night hours in retail, gas stations, convenience stores, etc.
How do you promote worker involvement in health and safety programs?
Once the health and safety program has been set in place and the program appears to be running smoothly, the effort is still required to maintain compliance, enthusiasm, and interest.
Safety awareness can be enhanced by:
- The setting of realistic goals and monitoring progress.
- Distribution of all pertinent information.
- Incorporating safe work outcomes into performance appraisals or job reviews.
- Individual recognition for superior performance.
- Continuing education and training, including general meetings, tailgate talks, and one-on-one coaching.
Should workplace-specific items be included in occupational health and safety programs?
The elements of OH&S programs discussed so far apply to all general health and safety programs. In addition, specific items may be needed to address workplace-specific activities. Examples of such items are:
- Workplace Hazardous Materials Information System (WHMIS).
- Lockout procedures.
- Confined space procedures.
- Hot-work permits.
- Working at heights.
- Material handling rules.
- Plant maintenance.
- Fire safeguards.
- Vehicle safety rules.
- Off-the-job safety.
- Working alone guidelines.
- Personal protective equipment requirements.
- Engineering standards.
- Purchasing standards.
- Preventive maintenance.
How do you implement occupational health and safety programs?
A good health and safety program provides a clear set of guidelines for activities that, when followed, will reduce incidents and cases of occupational disease. The key to success is the manner in which the program is implemented and maintained.
Senior management must demonstrate commitment and support the program by:
- Providing resources such as time, money, and personnel.
- Ensuring that workers receive training or certification as required.
- Making all applicable health and safety information available to all workers.
- Including health and safety performance as part of employee performances appraisals at all levels.
- Attending health and safety meetings.
The program must be communicated to all workers. Special emphasis should be given to new workers, newly appointed supervisors, and new members of the joint health and safety committee. Revisions to policies and procedures should be publicized. The program should be available in a single written document. However, if separate policies or procedures have been developed for various elements, such as incident investigation procedures or preventing harassment and violence, their use should be referred to in the main document.
How is the effectiveness of OH&S programs evaluated?
Incident frequency and severity rates are often used, but they are not always the only measures to use for evaluating the effectiveness of a health and safety program. Cases of occupational disease are often under-reported in these statistics. The emphasis is usually on injury-producing incidents, not all events. Since incidents may be rare events, in some organizations the basis for comparison may be limited.
It is desirable to use an audit as a before-the-fact measure of the effectiveness of an OH&S program. An audit uses a checklist in which each element is subdivided into a series of questions. Each question is given a weighting factor depending on its importance. Records, observations, interviews, and questionnaires are used to evaluate performance for each sub-element.
A number of audit systems are available.
Annual audits appear to be more common, but reviewing critical elements in the program more frequently may be advisable. The audit team, which should include representation from the joint health and safety committee, must receive the appropriate training in audit procedures.
The audit identifies weaknesses in the health and safety program. Establish a procedure to ensure prompt follow-up on deficiencies. This procedure should include target dates for remedial action and checks to confirm completion.