Free Travel Safety Tips and Ergonomic Solutions for Baggage Handling
7 min readAirline employees handle customer baggage at several points between customer departure and arrival. At each point, the weight of the luggage, awkward body postures assumed while lifting, the repetition of lifting, and fast work pace combine to create potentially serious ergonomic hazards. These hazards have caused a higher rate of Occupational Safety and Health Administration (OSHA)-recordable lost work days in these operations. According to the Bureau of Labor Statistics data for Texas, in 2009 there were 600 injuries reported as a result of some type of overexertion when handling luggage. The median number of days away from work for these types of injuries is 10. This safety Article describes common hazards and possible solutions for baggage handling.
Also Read: Photo of the day: Conveyors Safety Tips

BAGGAGE CHECK-IN
Agents receive bags from passengers at a baggage check-in point. The bags are usually weighed on a scale and tagged for the destination. The agent then lifts the bags and places them on a conveyor for transport to the baggage sorting area.
TRANSFERRING BAGGAGE TO THE MAIN CONVEYOR
Potential Hazards:
- Tagging and lifting bags while bent over (Fig. 1).
- Reaching with extended arms to lift and carry the baggage (Fig. 2).
- Twist the torso while transferring the baggage to the main conveyor, often several feet behind the counter (Fig. 3a).
- Performing the same lifting and twisting motions repeatedly throughout the shift (Fig.3b).
- Lifting excessively heavy and/or awkward bags (Fig. 4).
Possible Solutions:
- Educate employees in proper lifting techniques (Fig. 5) to keep baggage close to the body and near its center.
- To minimize bending to lift baggage, raise the height of the scales where the passengers place their baggage.
- To minimize lifting, tag baggage while on the scale, rather than lifting it to a temporary position on the floor and then lifting it again to the main conveyor.
- Tag excessively heavy baggage. All baggage tagged “heavy” should be handled by two or more people and/or with a lifting aid (e.g. hand truck or dolly).
- Use a rotation scheme to rotate employees out of this task which is particularly stressful. Rotating will reduce the amount of lifting and twisting each employee performs.
Also Read: Stress is a serious workplace hazard












STANDING
Potential Hazards:
- Standing on hard floors.
- Standing for long periods of time.
Possible Solutions:
- A footrest four to six inches from the floor will allow the employee to alternate the leg that supports the majority of his/her weight.
- Provide anti-fatigue mats to employees who must stand for extended periods of time.
- Provide sit/stand stools to allow employees to alter posture while working behind the counter (Fig. 6)
Automated Solution:
Some airlines have eliminated most lifting and standing hazards in baggage receiving by installing short “collection” conveyors to carry baggage to the main conveyor (Fig. 7).
- The passenger places luggage on the front end of a short collection conveyor leading to the main conveyor (Fig. 8). The front end of the short conveyor also functions as a scale. After measuring the weight, the agent activates the short conveyor to bring the bag to a position next to the agent, where it is tagged. Activating the conveyor again carries the bag to the main conveyor which takes it to the bag sorting area.
- The collection conveyor is low to the floor, so the employees can safely step on and over to get to their workstations. The employees never have to worry about stepping on a moving conveyor, because the conveyor is stationary when it is not being used.
- Where a belt conveyor is not practical, a series of rollers (“roller conveyor”) may be used. Although the employee must pull the luggage along the rollers, with proper training this will minimize the lifting and twisting.
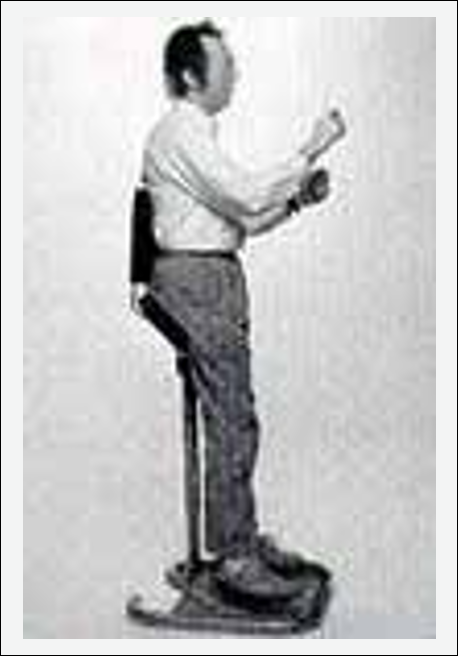
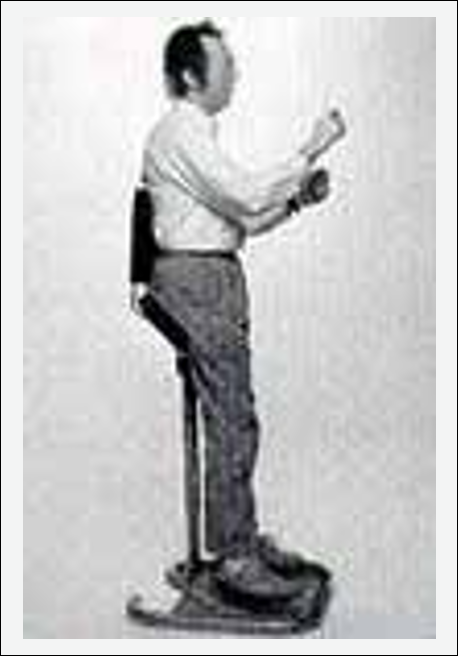




Also Read: Marking and Identification of Lifting Accessories
FROM BAGGAGE CART TO SORTING CONVEYOR
Employees in the baggage sorting area move bags from conveyors to carts for transport to the plane for departure, and from carts to conveyors upon arrival.
BAGGAGE CART
Potential Hazards:
- Extended reaching into the cart to pull bags from the far side of the cart (Fig. 9).
- Elevated and extended reaching with arms above the shoulder while lifting bags to elevated locations inside the cart (Fig. 10). These same postures and motions are necessary when unloading.
Possible Solutions:
- Load heavy bags close to the cart opening to minimize heavy lifts with the arms extended.
- Establish work practices (or redesign baggage carts) to prevent stacking bags above shoulder height.
- For example, limit the stacking of baggage in the cart to two bags high. This may necessitate adding more carts to the string.
- Consider redesigning new baggage carts to be narrower to reduce the reach with extended arms.
- Educate employees in proper lifting techniques to keep the load close to and in front of the body. Employees should grasp the bottom of the bag when loading to elevated areas rather than using the handle.
- Use a rotation scheme to rotate employees out of tasks that are particularly stressful. Rotating will distribute the stressful tasks equally.




BAGGAGE CONVEYOR
Potential Hazards
- Lifting from and to the conveyor while bent over with arms fully extended (Fig. 11).
- Repeated lifting of heavy objects from a low conveyor or from the floor.
- Repeated twisting of the torso while lifting the baggage between the cart and the conveyor (Fig. 12).
- Possible Solutions:
- Raise the height of the conveyor to reduce bending and lifting.
- Park the cart at an angle to minimize twisting when transferring baggage to the loading conveyor (Fig. 13).
- All baggage tagged “heavy” should be handled by two or more people and/or lifted with a lifting aid (e.g. hand truck or dolly).
- Educate employees in proper lifting techniques to keep the weight close to the body and near its center.
- Use a rotation scheme to rotate employees out of tasks that are particularly stressful. Rotating will distribute the stressful tasks equally.
TO/FROM LOADING CONVEYOR
In loading operations, a string of filled baggage carts is pulled by a tractor to a mobile loading conveyor parked near the airplane. The baggage handlers load the baggage from the carts onto the conveyor. The conveyor then carries the load to the door of the airplane baggage compartment. The operation is reversed for unloading. Variable weather conditions add to the potential hazards.
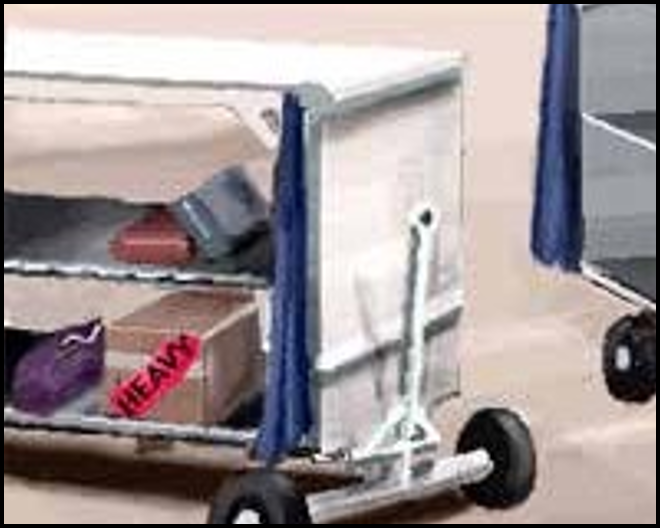
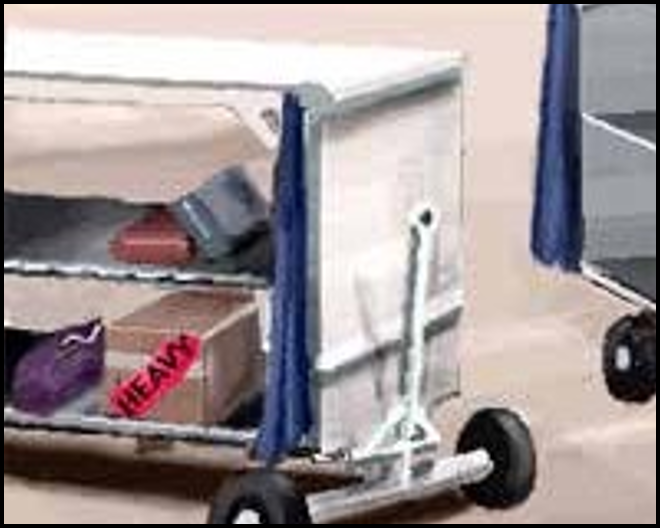


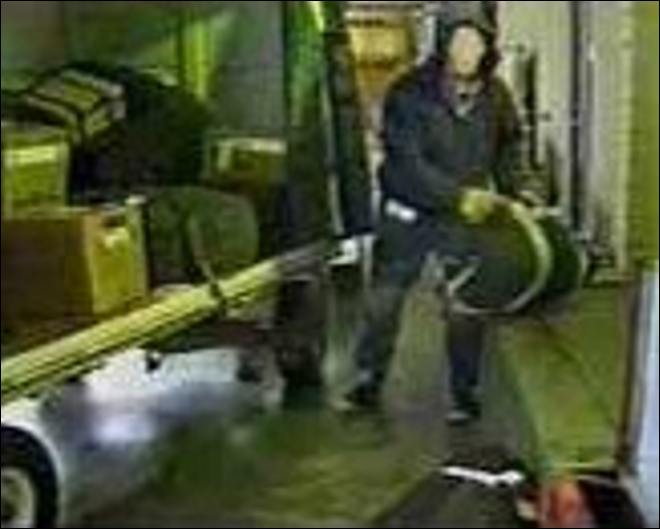
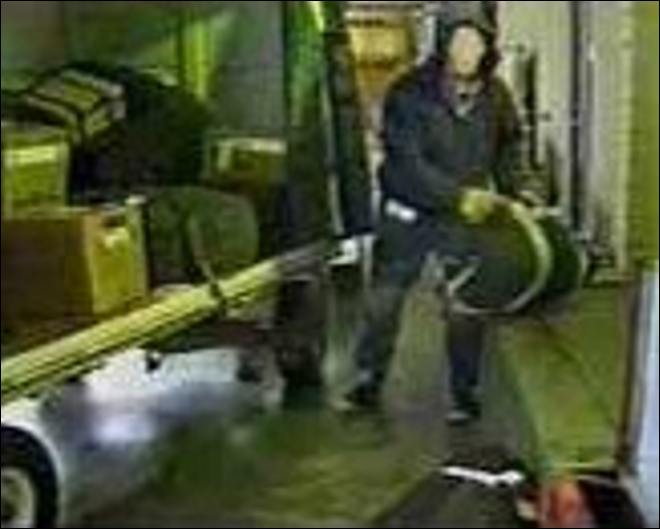
TO/FROM LOADING CONVEYOR
Potential Hazards:
- Repeated lifting of heavy objects from or to the loading conveyor. The baggage will be more difficult to grasp securely when wet from rain or snow.
- Repeated twisting of the torso while lifting the baggage between the cart and the conveyor (Fig. 14).
- Slipping on wet and icy pavement, particularly while handling heavy baggage.
Possible Solutions:
- Park the cart at an angle to minimize twisting when transferring baggage to the loading conveyor (Fig. 15).
- All baggage tagged “heavy” should be handled by two or more people and/or lifted with a lifting aid (e.g. hand truck or dolly).
- Ensure the use of proper lifting techniques, with emphasis on lifting problems associated with unsure footing.
- Use a rotation scheme to rotate employees out of tasks that are particularly stressful. Rotating will distribute the stressful tasks equally.
- Keep walking surfaces free of ice and snow.
- Workers should use footwear that maximizes traction for the conditions present.
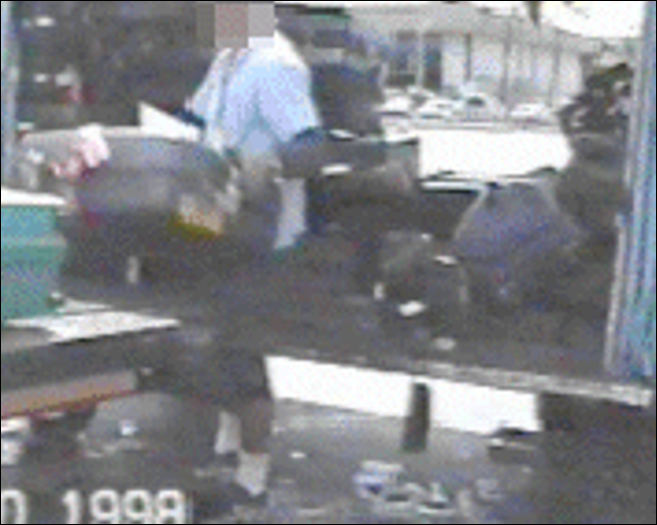
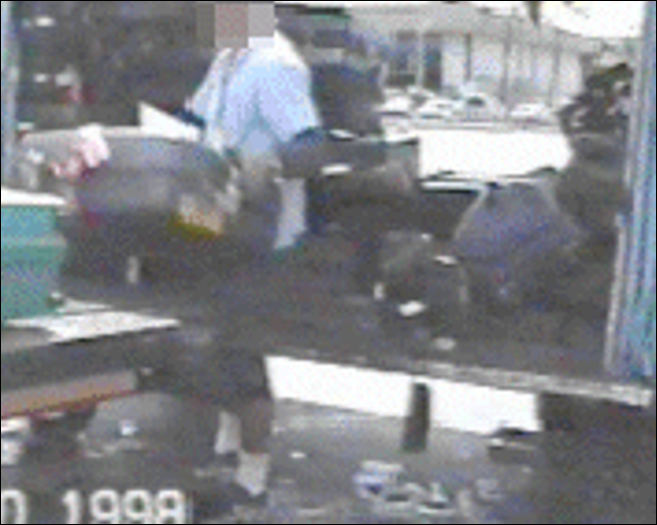


TO/FROM BAGGAGE COMPARTMENT
On all but the largest airplanes baggage is brought to the door of the baggage compartment by a mobile loading conveyor. Workers lift the bags from the conveyor and stack them within the compartment. The tasks are reversed for unloading. Employees must work on their hands and knees because of cramped conditions. Larger airplanes utilize mechanical baggage systems that do not require work in cramped spaces and can be highly automated.
BAGGAGE COMPARTMENT
Potential Hazards:
- Lifting baggage while bent over, and lifting with arms fully extended, because handlers must stoop, sit, or kneel to fit inside the baggage compartment (Fig. 16).
- Repeated twisting of the torso while lifting due to the cramped conditions.
Possible Solutions:
- Consider modifying the conveyor or its placement, to bring the end of the conveyor deeper inside the compartment. Often, the end of the conveyor is located on the outside edge of the door opening. This forces the handlers to reach and pull the baggage into the compartment.
- Segregate bags by weight on the baggage carts, so heavier bags can be placed on the bottom of stacks where lifting is minimized.
- Minimize the height to which heavy bags are stacked to minimize lifts with the arms above shoulder height. Heavy bags should be placed on the bottom.
- Consider a “buddy” system to reduce lifting while twisting. One handler retrieves the bags from the conveyor and slides it to a second handler who stacks the bags in place.
- All baggage tagged “heavy” should be handled by two or more people and/or lifted with a lifting aid (e.g. hand truck or dolly).
- Ensure the use of proper lifting techniques, particularly as adapted for the cramped conditions inside the baggage compartment.
- Use a rotation scheme to rotate employees out of tasks that are particularly stressful. Rotating will distribute the stressful tasks equally.
- Wear knee pads to reduce contact trauma and abrasive injuries while kneeling on hard surfaces.
- When in a cramped space, kneeling is preferable to stooping for lifting tasks, while stooping is preferable for pulling tasks.
AUTOMATED SOLUTION: MECHANICAL BAGGAGE SYSTEM
Consider the installation of a mechanical “containerized” baggage system to minimize lifting.
- Rather than using standard carts, baggage for larger airplanes is often loaded directly into containers or bins specifically designed for the airplane (Fig. 17). The bins are mechanically lifted and placed inside the baggage compartment (Fig. 18), thus eliminating the common lifting hazards associated with these tasks.
- Consider a similar system for smaller aircraft (obviously using smaller bins or “tubs”) or other ways to include mechanical lift devices. For example, a roller conveyor and/or overhead trolley system may be used for moving baggage inside the baggage compartment.






Also Read: Free Ergonomics Checklist for General Industry
For more safety Resources Please Visit Safetybagresources