Best Practices for Effective Contractor Safety Orientation Programs
As companies strive to maintain a safe and productive work environment, implementing effective contractor safety orientation has become a crucial element of their risk management strategy. By providing contractors with the necessary knowledge and tools to navigate the unique hazards and regulations associated with a particular worksite, these programs serve as a vital bridge between the company’s safety standards and the day-to-day operations of its external workforce. This article delves into the significance of contractor safety orientation, exploring the key elements that contribute to its effectiveness and the far-reaching impact it can have on workplace safety, productivity, and profitability. Through a comprehensive understanding of the benefits and best practices, companies can empower their contractors to work safely and efficiently, ultimately enhancing the overall success and sustainability of their operations.
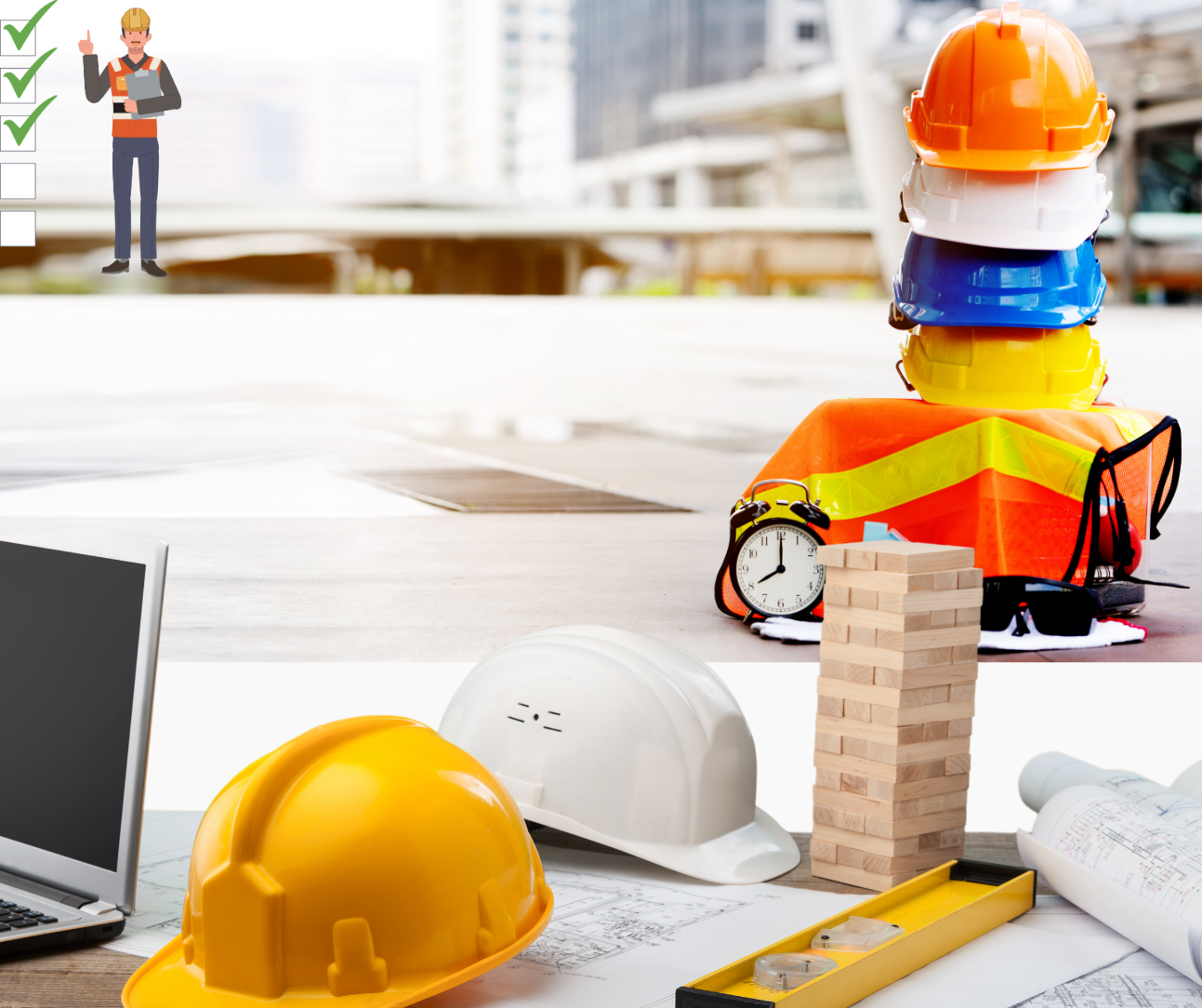
Introduction to Contractor Safety Orientations
Contractor safety orientations aim to educate contractors on the safety protocols relevant to a particular job site. These orientations are critical for ensuring all personnel understand company-specific safety guidelines and procedures.
Key components include:
- Company Policies: Overview of safety regulations and expectations.
- Site-Specific Hazards: Identification of potential dangers unique to the job site.
- Emergency Procedures: Steps to follow in case of an emergency, such as evacuation routes and contact information.
By emphasizing these areas, firms can significantly reduce the risk of accidents and ensure a safer working environment for all.
Downlaod: ample-of-accident-prevention-program-app-template-for-general-industry-free-download
The Importance of Contractor Safety in the Workplace

Ensuring contractor safety is crucial in maintaining a secure and productive work environment. Unsafe practices can lead to:
- Increased Accident Rates: Contractors unfamiliar with safety protocols are more prone to accidents.
- Legal Liabilities: Organizations may face fines and legal action if contractors are injured.
- Operational Disruptions: Accidents can halt work, causing delays and financial losses.
- Reputation Damage: Poor safety records can tarnish a company’s reputation.
Focusing on contractor safety prevents incidents and promotes a culture of health and safety, benefiting both contractors and the company.
Key Elements of a Successful Safety Orientation Program
A successful safety orientation program should encompass the following elements:
- Clear Objectives: Establish specific safety goals.
- Comprehensive Training: Cover all potential hazards, safety procedures, and emergency protocols.
- Accurate Documentation: Maintain detailed records of training sessions, attendance, and performance.
- Qualified Instructors: Ensure trainers are certified and experienced.
- Engaging Content: Utilize multimedia and interactive components.
- Regular Updates: Refresh program content based on new regulations or incidents.
- Employee Involvement: Encourage feedback and questions from participants.
- Assessment and Evaluation: Implement quizzes or practical tests to gauge understanding.
- Continuous Improvement: Review and improve the program periodically.
Also Read: photo-of-the-day-new-worker-orientation-safety-orientation-checklist
Identifying and Assessing Potential Hazards
A comprehensive approach to identifying and assessing hazards is critical. Contractors should be oriented on:
- Site-Specific Hazards: Understanding unique risks associated with the particular work environment.
- Daily Hazard Assessments: Conduct regular inspections to uncover new or evolving risks.
- Emergency Procedures: Familiarizing with emergency exits, medical facilities, and communication protocols.
- Personal Protective Equipment (PPE): Knowing mandatory PPE for various tasks.
- Witnessing and Reporting: Encouraging immediate reporting of unsafe conditions to supervisors.
- Work Permits: Ensuring the acquisition of appropriate permits for high-risk activities, like hot work.
Legal and Regulatory Requirements
Effective contractor safety orientation programs must comply with various legal and regulatory standards to ensure safety and avoid liability.
- OSHA Standards: Contractors need orientation based on specific Occupational Safety and Health Administration (OSHA) standards relevant to their tasks.
- Documentation: Maintain records of all training sessions, including attendance and materials covered, to demonstrate compliance.
- Hazard Communication: Ensure contractors are informed about workplace chemical hazards per OSHA’s Hazard Communication Standard.
- Site-Specific Regulations: Tailor orientation programs to address any additional site-specific safety regulations.
- Legislation Updates: Regularly update training materials to reflect changes in laws and safety protocols.
Effective Communication Strategies
Clear communication is critical to a contractor safety orientation program.
- Use Plain Language: Avoid technical jargon that may confuse contractors.
- Multimedia Presentations: Utilize videos, infographics, and slides to make information accessible.
- Interactive Sessions: Encourage questions and discussions to ensure understanding.
- Written Material: Provide handouts or digital copies of safety protocols for future reference.
- Regular Updates: Keep communication channels open for ongoing updates and feedback.
- Language Considerations: Offer materials in multiple languages if the workforce is diverse.
- Feedback Mechanisms: Implement surveys or suggestion boxes to gather contractor input.
Training and Education Programs
To ensure contractor safety orientation programs are effective, detailed training and education must be provided.
- Needs Assessment: Conduct thorough assessments to identify training requirements specific to each contractor’s role.
- Customized Training Modules: Develop role-specific modules, covering essential safety protocols and practices for various job functions.
- Hands-On Training: Incorporate practical, hands-on training sessions to demonstrate safety equipment usage and emergency procedures.
- Documentation: Provide instructional materials, including manuals, videos, and online resources, accessible anytime.
- Regular Updates: Schedule regular training updates to address new safety regulations and emerging risks.
- Feedback Mechanism: Implement feedback systems to evaluate training efficacy and incorporate improvements based on contractor input.
Creating a Culture of Safety
A culture of safety ensures ongoing commitment and compliance. Leadership must demonstrate commitment. Steps to create this culture include:
- Leadership Involvement: Leaders should visibly engage in safety programs.
- Regular Training: Conduct periodic safety training sessions.
- Open Communication: Encourage feedback and reporting of hazards.
- Recognition Programs: Acknowledge compliance and safe behavior.
- Clear Policies: Establish clear and accessible safety policies.
A collaborative approach and commitment to these actions can elevate safety standards across the organization. Each member’s role is vital to sustain an effective safety culture.
photo-of-the-day-5-essential-outcomes-of-an-effective-leadership-survey-process
Monitoring and Measuring Success
Regular analysis of safety metrics ensures program effectiveness. Collect data from incident reports, near-misses, and safety audits. Utilize these metrics:
- Accident Rates: Evaluate the frequency and severity of workplace accidents.
- Training Completion: Track completion rates for orientation programs.
- Behavioral Observations: Conduct periodic checks to observe compliance with safety protocols.
- Feedback Mechanisms: Implement anonymous surveys for contractor feedback.
- Compliance Audits: Regularly audit safety practices in the field.
- Follow-Up Training: Offer additional training sessions based on identified deficiencies.
By closely monitoring these parameters, organizations can identify areas for improvement and verify that safety goals are being met consistently.
Continuous Improvement and Feedback Loops
Incorporating continuous improvement and feedback loops into contractor safety orientation programs ensures they remain effective and relevant. Key elements include:
- Regular Reviews: Conduct periodic evaluations of the program to identify improvement areas.
- Surveys and Feedback: Gather input from contractors through surveys and feedback forms.
- Data Analysis: Analyze incident reports and safety data to track program success.
- Stakeholder Meetings: Hold regular meetings with key stakeholders to discuss findings and implement changes.
- Training Updates: Update training materials regularly based on the latest safety standards and regulations.
Continuous feedback fosters a proactive safety culture and aids in mitigating risks.
Case Studies of Successful Implementations
Company A: Reduced Incidents
- Initial Challenge: High rate of safety incidents.
- Approach: Comprehensive digital learning modules.
- Results: 40% reduction in incidents within six months.
Company B: Enhanced Engagement
- Initial Challenge: Low engagement during orientation.
- Approach: Interactive workshops and hands-on training.
- Results: 30% increase in participation and feedback.
Company C: Improved Compliance
- Initial Challenge: Inconsistent adherence to safety protocols.
- Approach: Regular refresher courses and quick assessments.
- Results: 25% improvement in safety compliance rates.
These cases demonstrate the positive impact of tailored safety orientation programs.
Common Challenges and How to Overcome Them
Lack of Engagement
- Solution: Use interactive training modules.
- Solution: Incorporate real-life scenarios.
Language Barriers
- Solution: Provide multilingual materials.
- Solution: Use visual aids.
Insufficient Time Allocation
- Solution: Schedule dedicated sessions.
- Solution: Offer flexible training hours.
Varied Skill Levels
- Solution: Assess skill levels beforehand.
- Solution: Offer customized training paths.
Technology Limitations
- Solution: Ensure access to necessary tools.
- Solution: Provide technical support.
Retention of Information
- Solution: Use frequent refreshers.
- Solution: Implement a mentor system.
Compliance Issues
- Solution: Regularly update protocols.
- Solution: Conduct periodic audits.
Leveraging Technology for Safety Orientations
Incorporating technology enhances the effectiveness and engagement of safety orientations. Implementing digital tools can streamline processes and ensure consistency. Key technological tools include:
- Online Training Modules
- Accessible anytime, allowing flexible learning.
- Interactive content to maintain engagement.
- Virtual Reality (VR) Simulations
- Realistic scenarios for hands-on experience.
- Safe environment for practicing skills.
- Mobile Applications
- On-the-go access to safety resources.
- Easy tracking of progress and certifications.
- Learning Management Systems (LMS)
- Centralized platform for course management.
- Automated reminders and assessments.
These technological solutions provide a modern approach to ensure contractors are well-prepared for safe working environments.
Conclusion
Implementing robust contractor safety orientation programs is critical to ensuring a safe and productive work environment. By adhering to best practices, companies can mitigate risks and promote safety.
- Consistent Communication: Maintain open channels for questions and updates.
- Interactive Training Modules: Use engaging formats to enhance comprehension and retention.
- Regular Assessments: Frequent evaluations ensure compliance and address gaps.
- Continued Education: Keep contractors updated on new safety protocols.
- Documentation: Meticulously record all training activities for accountability.
Effective safety orientation programs foster a culture of safety, ensuring that all contractors are equipped with the necessary knowledge and skills for their tasks.
general-elements-of-ohs-program
have more safety resources at safetybagresources