Warehousing and storage-Manual handling
10 min readMusculoskeletal disorders (MSDs) are the most common occupational illness in many workplaces. They affect many people a year and account for more than 40% of RIDDOR-reported ‘over-3-day’ injuries in warehouses. They include problems such as lower back pain, neck pain, and upper-limb disorders due to improper manual handling. Many work activities can lead to MSDs, from heavy lifting to repetitive order picking. Injuries can occur as the result of a single incident or they can develop over time. A wide range of common work tasks can cause MSDs, and many will be caused by one or a combination of the following risk factors:
- repetitive and heavy lifting;
- bending and twisting;
- repeating an action too frequently;
- uncomfortable working position;
- exerting too much force;
- exerting a force in a static position for extended periods of time;
- working too long without breaks;
- adverse working environment (eg hot, cold); and
- psychosocial factors (eg high workloads, tight deadlines, and lack of control over the work).
this article will explain the safe Manual handling technics at warehousing and storage activities to avoid MSDs commonly caused, or made worse, by activities at work. The effects of MSDs can be reduced and new cases caused by workplace activities are prevented by using a common-sense approach and controlling the risks.
Also Read: Musculoskeletal Disorders (MSDs) in the Prep Kitchen
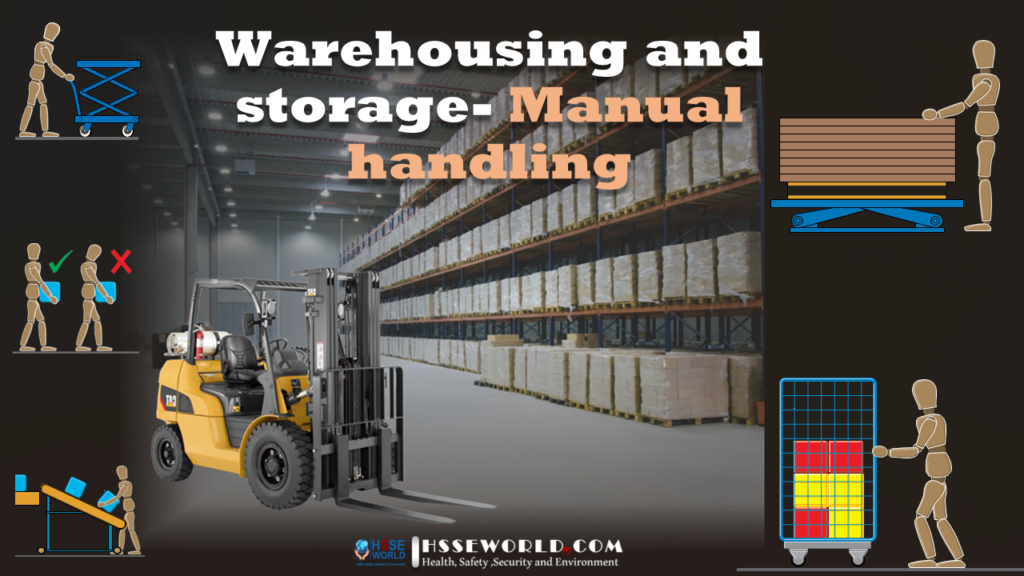
Manual handling risks
If there is a risk from a manual handling task, where reasonably practicable the task should be avoided. If this task cannot be avoided, the risk of injury occurring should be minimized as far as is ‘reasonably practicable’. Consider all systems of work in the warehouse involving manual handling operations and, where appropriate, redesign tasks to:
- avoid the need to move loads manually; or
- fully utilize mechanical handling devices, eg lift trucks, pallet trucks, trolleys, conveyors, chutes, scissor lifts, etc. Where necessary, introduce additional mechanical handling devices to avoid or reduce manual handling
also Read: Keeping Warehouse Personnel Safe 6 Key Tips -Safety Moment#20
Manual handling assessment
You must carry out a manual handling assessment for all manual handling operations and tasks that present a risk of injury and that cannot be avoided.
The assessment should identify where improvements or other measures are necessary to reduce the risk of injury from manual handling operations. Consider the following factors when making such an assessment:
Also Read: Photo of the day: Preventing Common Kitchen Hazards
- The task: Are there any tasks that involve foreseeable risks? Consider unsatisfactory bodily movements or posture (eg twisting), excessive lifting or lowering distances (eg from floor level to above waist height), excessive pushing or pulling distances, situations where the load is required to be held or manipulated at a distance from the trunk of the body, or repetitive handling.
- The load: Are there any loads unsuitable for manual handling? For example, too heavy, bulky, unwieldy, slippery, wet, sharp, unpredictable, or unstable.
- The working environment: Are there conditions in the warehouse that increase the risk of injury from manual handling operations? For example, constricted work areas, narrow aisles, areas of extreme temperature (hot or cold), over-steep slopes, or changes in floor level.
- Individual capability: Are there any employees who require specific assessment before undertaking manual handling operations? For example, pregnant women or new mothers, people with known medical conditions, people with previous manual handling injuries, or young workers.
- Other factors: Is movement or posture hindered by personal protective equipment or clothing? Also consider organizational factors that have an impact on the risk, eg order-picking software.
Where the assessment identifies manual handling operations that involve a risk of injury, you should take appropriate measures to reduce those risks as far as is reasonably practicable. These measures could include redesigning the task or system of work, altering shelving heights or the warehouse layout, or introducing mechanical handling devices.
Work-related upper-limb disorders
Upper-limb disorders (ULDs) are problems with the shoulder and arm, including the forearm, elbow, wrist, hand, and fingers, and can include neck pain.
In warehouses, ULDs can be caused by a variety of work tasks involving forceful or repetitive activity, or poor posture. The way that the work is organized and managed can cause ULDs as well as make them worse.
ULDs fall into two broad categories: those conditions that have a specific medical diagnosis (eg carpal tunnel syndrome, frozen shoulder) and non-specific pain syndromes where it is not possible to define the cause of the pain. The term ‘repetitive strain injury’ (RSI) is often used, but is not a medical term and is not accurate in describing many ULDs.
There is a wide range of ULD symptoms, some examples are tenderness, aches, pain, stiffness, weakness, tingling, cramp, or swelling. Symptoms should never be ignored, even if they appear slight.
If there is a risk of ULDs from the work undertaken within your warehouse, you should carry out a risk assessment. The risk of ULDs should be reduced to as low a level as reasonably practicable, eg by changing the way work is organized
Also Read: Industrial Ergonomics: Preventing Musculoskeletal Disorders
Managing and controlling the risk of musculoskeletal disorders
The risk of all MSDs can be easily managed by following the simple steps:
Figure 1 Good handling technique for lifting equipment
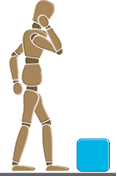

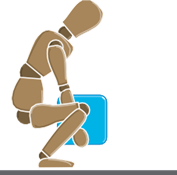

Identification
Identify which activities are causing a significant risk of MSDs in the workplace. Observe the work being done, discuss with employees, and look at injury history. Particular attention should be paid to moving heavy objects, awkward load shapes, strenuous pushing and pulling, stacking above shoulder height, uncomfortable working positions, repetitive work (eg packing), and use of excessive force.
Elimination
Tasks identified as presenting a significant risk of causing MSDs should be assessed in more detail to see if they can be avoided altogether, or if the task can be changed to reduce the risk. For example, can the task be automated or significantly assisted by mechanical means?
Preventative measures
Where tasks cannot be eliminated or automated, you will need to implement suitable preventive and protective measures to reduce the risk of injury.
Reporting symptoms
Encourage your employees to report any symptoms of injury as soon as they notice them. Early reporting of symptoms enables early diagnosis, proper treatment, and rehabilitation. In general, back pain can best be tackled by keeping gently active rather than resting. Specialist occupational health advice may be helpful in managing severe episodes of MSDs.
Information and training
Employees should be given information about the weight and properties of any load if manually handling the load involves a risk of injury. This is to protect employees, so the information provided should be of practical use in preventing injury. In some cases, it may be reasonably practicable to give precise information about the weight, eg by marking this on a load. Where it is not reasonably practicable to do this, general indications about the weight can be provided. If a load has a center of gravity that is not centrally positioned, then the heaviest side could be marked. This should be done if the load is sufficiently out of balance to take handlers by surprise.

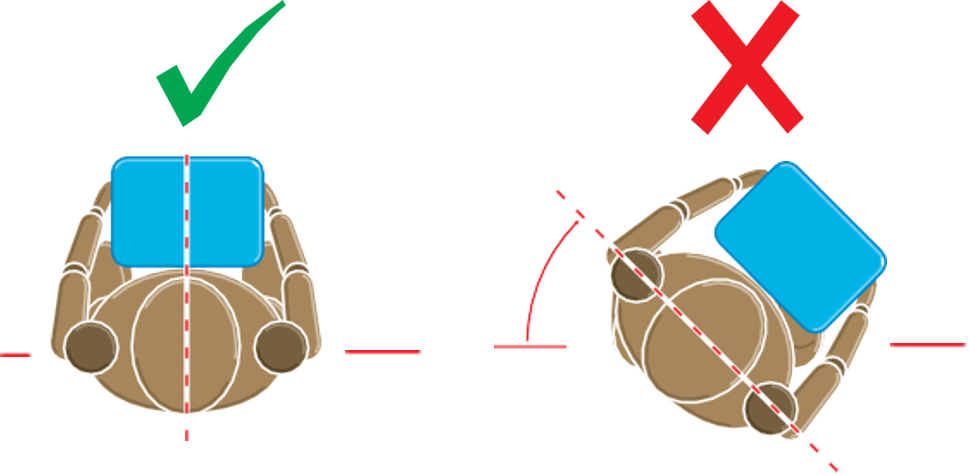
especially while the back is bent.
Ensure that your employees clearly understand how a manual handling operation has been designed to safeguard their health and safety. Training should complement a safe system of work and not be a substitute for it. A training program should be specific to the tasks being undertaken and should provide a clear understanding of:
- good handling techniques, including posture, lifting techniques, and methods of carrying;
- the proper use of handling aids;
- actors affecting individual capability;
- the importance of good housekeeping;
- how potentially hazardous loads may be recognized;
- how to deal with unfamiliar loads;
- the proper use of personal protective equipment; and
- features of the working environment that contribute to safety.
Also Read: Forklift Operator’s Daily Checklist and safety Tips
Monitoring
Finally, it is important to check that preventative and protective measures have made improvements. You can do this by monitoring sickness absence records and ill health, ensuring there is adequate supervision, monitoring the use of mechanical aids, etc.
The supply chain
Handling risks are often inherited through the supply chain, eg by the receipt of goods that have not been palletized. If your suppliers and customers can agree on acceptable product weights and maximum pallet heights etc, and how products should be handled, purpose-made handling solutions can be used at each stage.
It is also important to ensure that you consider manual handling problems for distribution staff, delivery workers, and customers. Each supplier in the chain should cooperate with the others in identifying problems and agreeing solutions.
Roll cages
Roll cages (also known as roll containers or roll pallets) are commonly used in warehousing, storage, and distribution.
When fully loaded, roll cages can generally carry up to 500 kg of goods, but some manufacturers rate the capacity of their containers as high as 700 kg. Roll cages are supplied in a variety of heights, ranging from 1550 mm up to 1830 mm.
Musculoskeletal and other injuries arising from:
- pushing/pulling loaded roll cages, especially up slopes, over steps, or on uneven floor surfaces;
- trying to prevent roll cage overbalancing (and crush injuries where this was not successful);
- repetitive loading and unloading of roll cages;
- trapping hands while assembling/dismantling cages;
- trapping hands and other parts of the body between the roll cage and a wall, side of the vehicle, etc;
- feet being trapped under the castors; and
- roll cages falling off lorries (eg from the tail lift) during loading and unloading, often causing the most serious injuries.
Designs to reduce injuries
The most important design features that will help reduce roll cage incidents are:
- the use of large-diameter wheels, to reduce pushing/pulling forces and to make these less sensitive to surface imperfections (eg the forces required to overcome a small step are typically 12–24% greater if using a 100 mm diameter wheel, as opposed to a 125 mm diameter wheel);
- the careful selection of wheel material – hard materials such as nylon will lower rolling resistance and, unlike cast iron, should not damage floors or make too much noise, although polyurethane wheels are quieter and produce less vibration on rough surfaces;
- good quality castors, each with a well-maintained wheel bearing (ball bearings offer the least rolling resistance, followed by roller bearings and then plain bearings, as used on nylon wheels, although the latter require less maintenance);
- castors close to corners to improve stability;
- incorporating handles (at a height of approximately 1000 mm) to move fingers away from the corners of containers where they are vulnerable to impact and, when cages are pulled, to keep feet further from the castors;
- marked load height limits, to enable the operator to have a clear view when pushing the load.
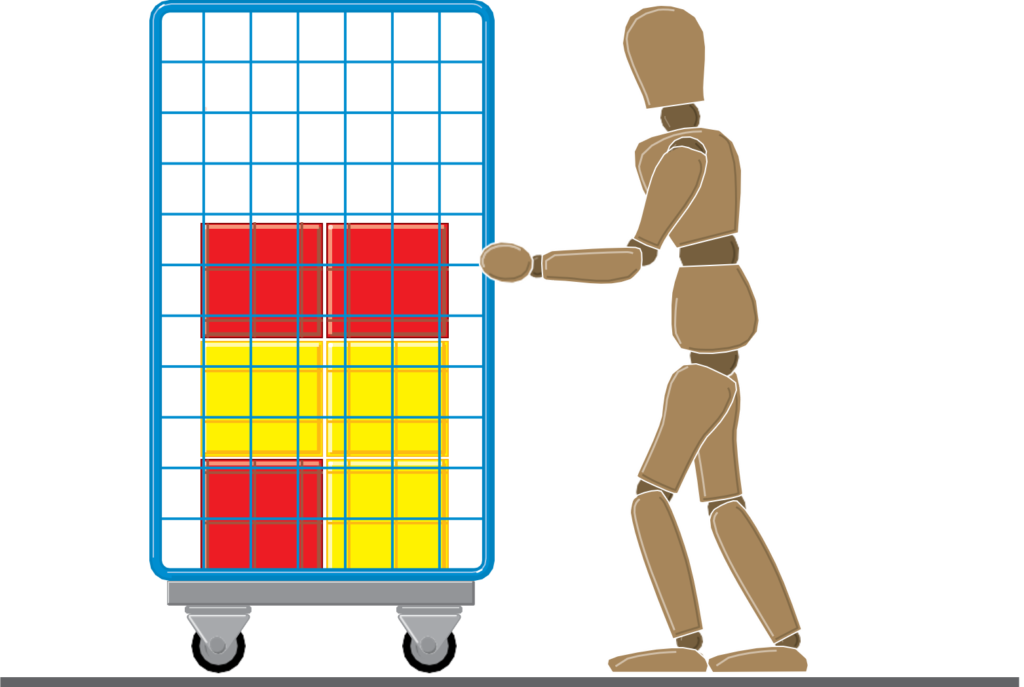
Risk assessment for roll cages
Carry out a risk assessment for each roll cage application, covering both on-site and off-site risks including:
- pushing/pulling options;
- forces required to move the roll cage;
- the effect of slopes and terrain/floor surface problems;
- availability of safe handles;
- visibility for the operator;
- hand/body/foot trapping risks;
- slips and trips;
- correct lifting methods for loading and unloading the roll cage; and
- risks associated with loading/unloading roll cages onto lorries (eg with tail lifts).
Pushing roll cages (rather than pulling) is the preferred option, although in practice, both pushing and pulling are necessary in most situations. Pushing has ergonomic advantages (two hands can be used and there is less twisting). There is also less risk of foot trapping or impact injury if the cage overruns or the operator slips.
When considering pushing/pulling forces, the risk assessment should take into account the sex and weight of the person pushing the roll cage. Female workers can typically exert only 60% of the force of male workers. Older and very young workers (male and female) may also have reduced capabilities.
For pushing/pulling on slopes, your risk assessment should be particularly cautious. For example, a roll container with a load of 400 kg and a slope of 1 in 12 (4.8°) would require a force of 33 kg (330 N), well above the force a man might be expected to handle and double the force a woman might be expected to handle. Slips are also more likely on slopes, especially with the extra pushing forces required.
With uneven surfaces, the maximum starting force could rise to 10% of the load. Moving heavily loaded roll containers is therefore likely to place lone operators at risk of injury, even on level surfaces.
Safe working with roll cages
Your employees should be trained in the use of roll cages and the safe system of work. The following precautions have been shown to reduce injuries. Operators should:
- only move one roll cage at a time;
- use the handles provided;
- move the roll cage no faster than walking speed;
- wherever possible, push the cage rather than pull, as this is ergonomically better and will reduce the risk of foot trapping;
- seek help from another person when moving a roll cage up or down a ramp or on an uneven surface or when a cage is heavily loaded;
- not ride in or on roll cages, as they can easily overturn or trap the operator;
- wear gloves and safety shoes when moving roll cages – softer sole shoes will reduce slips;
- wear gloves to protect hands and fingers when assembling cages;
- stack heavier items at the bottom of the roll cage to keep the center of gravity as low as possible (the correct lifting technique is particularly important at this low level);
- not overload the trolley;
- not load the cage above the load line or above the level where the operator can see over the load;
- move no more than three to five empty, nested roll cages at one time (see manufacturer’s recommendations).
Also Read: Photo of the day: Conveyors Safety Tips
Inspection and maintenance of roll cages
Poor maintenance can be a factor in accidents involving roll cages, for example, jammed or faulty wheels or protruding sharp edges.
You should have systems in place for the inspection and maintenance of roll cages.
Trolleys
Where your workers use trolleys, select a suitable design. Trolleys are designed to be used on level, even surfaces. If used on a gradient there may be a risk of trolleys freewheeling out of control and causing injury to people. Trolleys should not be used on gradients unless a safe system of work is adopted to prevent such risks from occurring.
Carry out a manual handling assessment for the use of trolleys.
Make sure you have systems in place for the inspection and maintenance of trolleys.
Figure 3 Lifting and handling aids

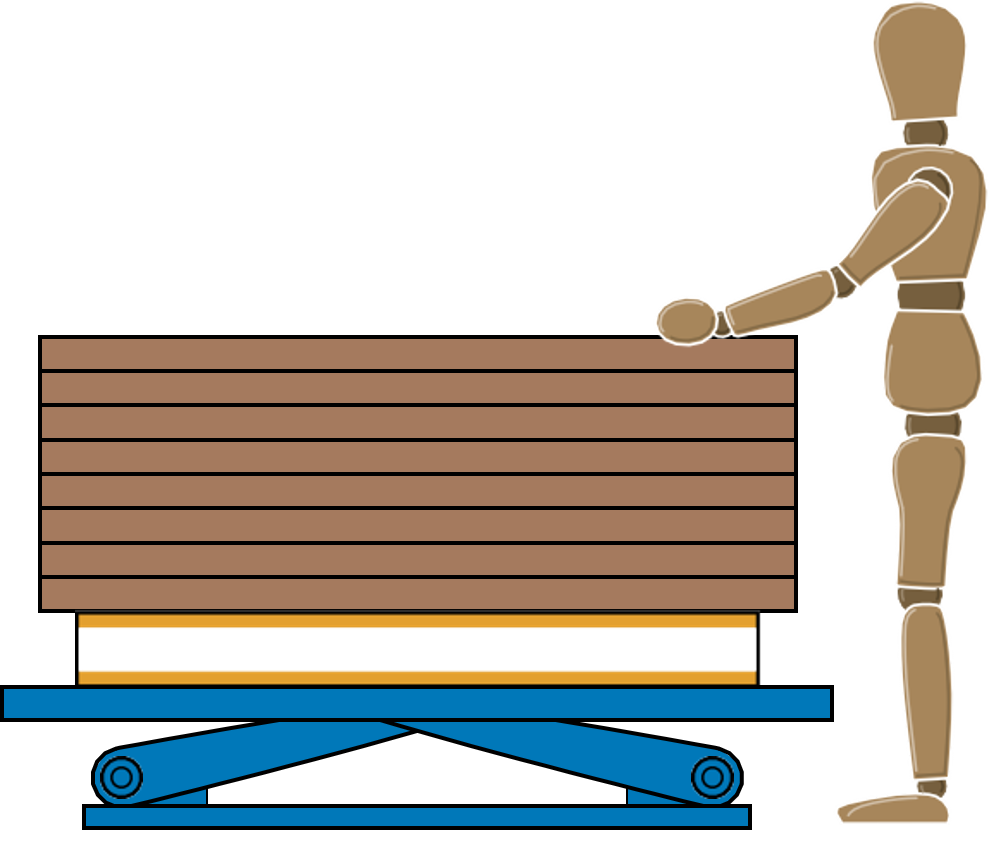
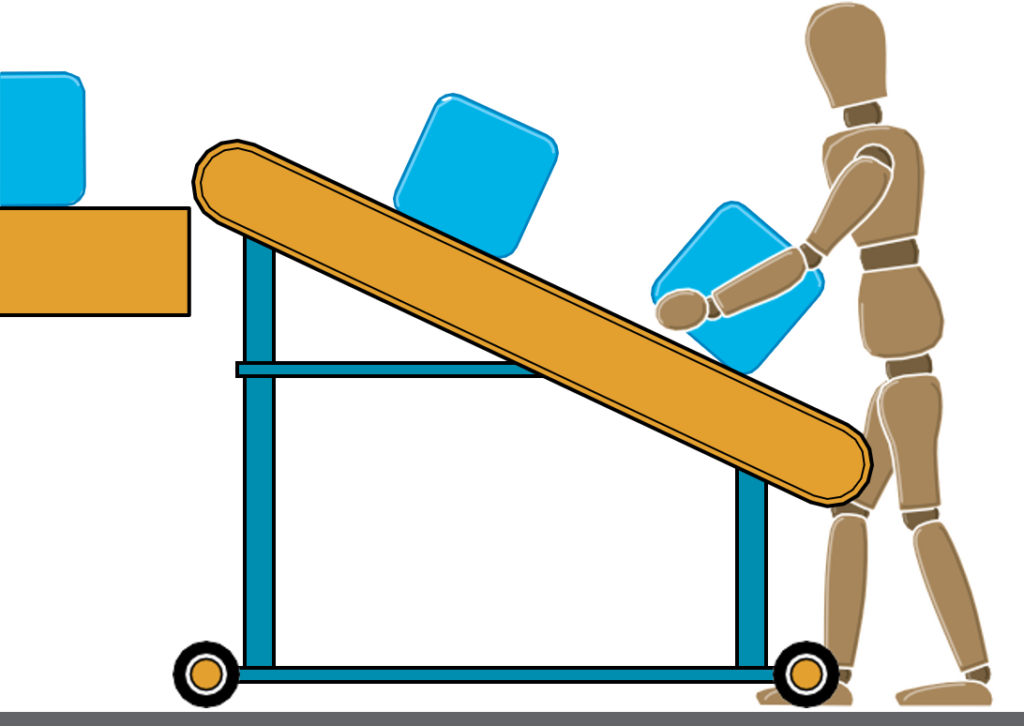
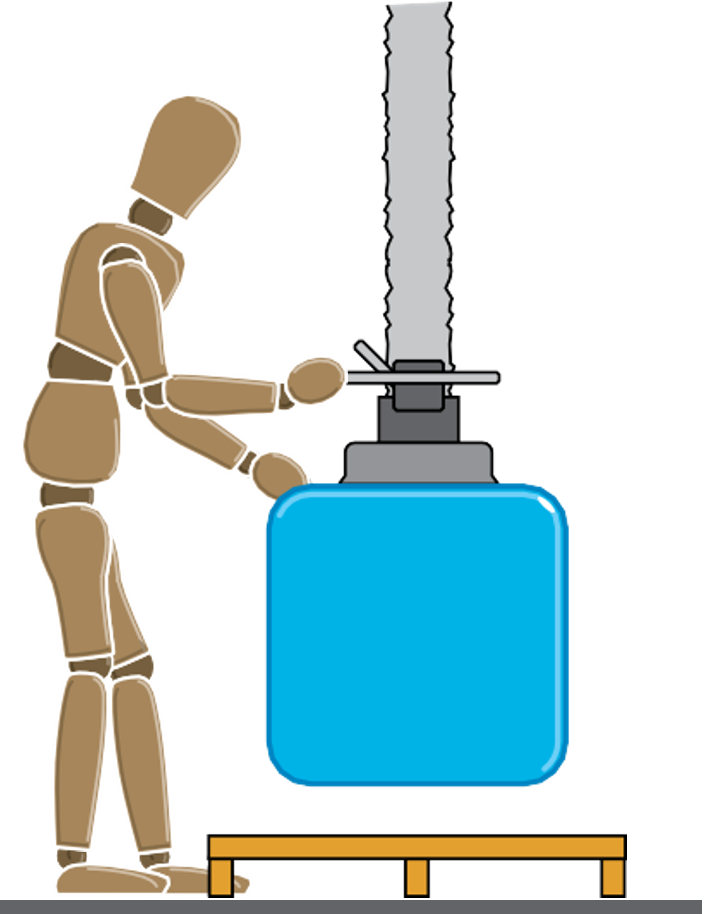
Also Read Q & A: Do Manual Hoists and Trolleys Require a Load Test after Installation?(
For more safety Resources Please Visit Safetybagresources