The Impact of Material Fatigue on Aircraft Maintenance and Safety
4 min readAircraft maintenance and safety are critical aspects of the aviation industry. Ensuring that all components of an aircraft are in top condition is essential for safe flights. Among the various factors influencing aircraft maintenance, material fatigue stands out as a significant concern. Material fatigue refers to the weakening of a material caused by repeatedly applied loads. This phenomenon can lead to the failure of aircraft components, posing serious risks to safety. Let’s explore the impact of material fatigue on aircraft maintenance and safety. We will delve into the concept of low cycle fatigue vs high cycle fatigue, examining how these types of fatigue affect aircraft components differently. By understanding these aspects, we can better appreciate the importance of effective maintenance practices in ensuring the longevity and safety of aircraft.
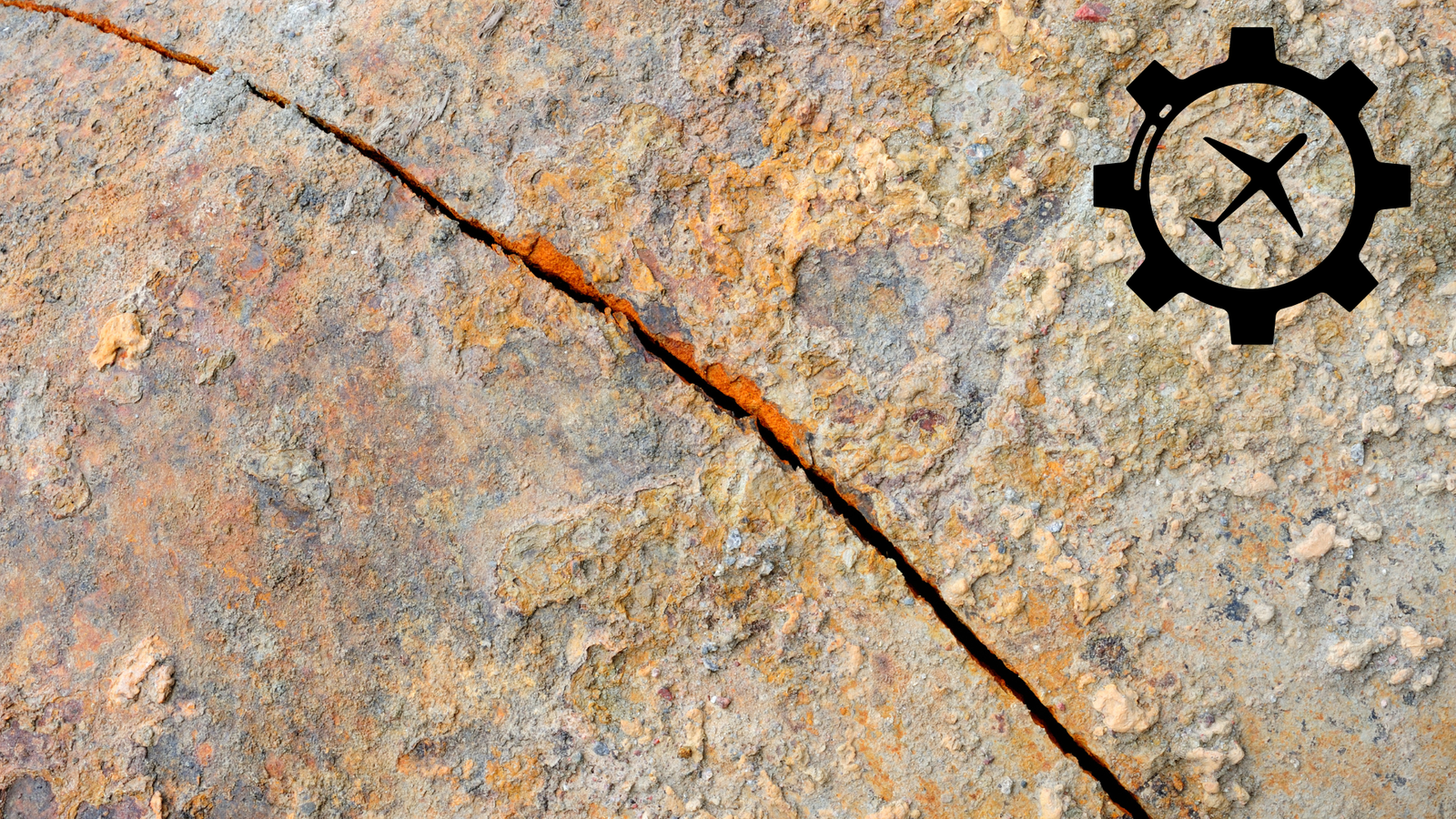
Understanding Material Fatigue
Material fatigue is a process that occurs when a material is subjected to cyclic loading, leading to the progressive and localized structural damage. In the context of aviation, this means that aircraft components can experience significant wear and tear over time due to the stresses of repeated flights. The process begins with the initiation of tiny cracks within the material, which can then propagate and eventually cause failure.
Several factors contribute to material fatigue in aircraft. One of the primary factors is the magnitude of the stress applied to the material. Higher stress levels can accelerate the fatigue process, making it crucial to monitor and manage the loads experienced by aircraft components. Additionally, environmental conditions, such as temperature and humidity, can influence the rate of fatigue. For instance, extreme temperatures can cause materials to expand and contract, exacerbating the stress on the components.
Read: fatigue-quick-guide-and-checklist/
The Role of Aircraft Maintenance
Effective aircraft maintenance plays a vital role in mitigating the risks associated with material fatigue. Regular inspections and maintenance schedules are designed to identify and address signs of fatigue before they lead to component failure. This includes non-destructive testing methods, such as ultrasonic testing and radiography, which can detect internal cracks and weaknesses in materials.
Moreover, maintenance practices must account for the specific usage patterns of each aircraft. Different types of aircraft and their respective missions can result in varying levels of stress and fatigue. For example, commercial airliners may experience different fatigue patterns compared to military aircraft due to differences in flight profiles and operational demands. Tailoring maintenance strategies to these unique conditions is essential for maintaining safety and performance.
Low Cycle Fatigue vs. High Cycle Fatigue
Material fatigue can be classified into two main categories: low cycle fatigue (LCF) and high cycle fatigue (HCF). Understanding the distinction between low cycle fatigue vs high cycle fatigue is crucial for effective maintenance and safety management.
Low Cycle Fatigue (LCF): This type of fatigue occurs under conditions of high stress and a low number of cycles. It is typically associated with significant plastic deformation, meaning the material undergoes permanent changes in shape. LCF is common in aircraft components that experience high loads during takeoff, landing, and turbulent conditions. For example, landing gear and engine mounts are often subjected to LCF due to the intense stresses they encounter during these critical phases of flight.
High Cycle Fatigue (HCF): In contrast, HCF occurs under conditions of lower stress and a high number of cycles. This type of fatigue is characterized by minimal plastic deformation, with the material remaining mostly elastic. HCF is prevalent in components that experience repetitive loads over long periods, such as wings and fuselage structures. The constant vibrations and aerodynamic forces during flight contribute to HCF, making it a critical consideration for long-term aircraft safety.
Implications for Aircraft Components
The implications of material fatigue for aircraft components are significant. Failure to address fatigue issues can lead to catastrophic outcomes, including in-flight component failures. As such, understanding the different types of fatigue and their effects on various components is essential for effective maintenance practices.
For instance, components subjected to LCF require frequent inspections and possibly more robust materials to withstand the high stresses. On the other hand, components affected by HCF may benefit from design modifications that reduce stress concentrations, such as smooth transitions between different parts of the structure. Additionally, the use of advanced materials and manufacturing techniques can enhance the fatigue resistance of aircraft components, contributing to overall safety.
Material fatigue is a critical factor in aircraft maintenance and safety. The repeated stresses experienced by aircraft components can lead to the initiation and propagation of cracks, ultimately resulting in component failure. Understanding the factors contributing to material fatigue, such as stress levels, environmental conditions, and usage patterns, is essential for effective maintenance practices. Ultimately, ongoing research and technological advancements will continue to play a pivotal role in enhancing our understanding and management of material fatigue in aviation.